by Chad Kymal and Praveen Patiyasevi
Semiconductor devices are the core of all electronic products we use today, be they phones, radios, computers, toys or cars. For the most part, this industry and its products are hidden from view. As each year goes by, semiconductor devices are becoming smaller and thinner, using less energy and offering increased computing power. These strides in technology have fueled a boom in new products that capture the consumer's imagination: 60-in. televisions, razor-thin cell phones and computers that double in power every six months. This industry is characterized by very high-quality standards paired with rapid new technology introductions. A missed design cycle often means no growth and loss of market share.
These are turbulent times in the semiconductor industry, as many new technologies make their appearance through venture capital-funded, fabless semiconductor organizations. At the same time, new assembly houses and fabs are appearing in China and India. High-growth opportunities in these nations are forecasted to replace traditional markets.
During these times of change, quality initiatives and improvements continue to be important. The most demanding customers and the highest expectations for quality are found in the semiconductor sector. Let's look at the current challenges and pressures within this industry.
For the most part, the semiconductor industry has completed its ISO/TS 16949 and ISO 9001 implementations. Many large semiconductor organizations, contract fabs and assembly subcontractors that were registered to QS-9000 have successfully transitioned to ISO/TS 16949 despite the scope restrictions of this technical specification.
Because the scope of ISO/TS 16949 meant it only applied to automotive products, many semiconductor organizations couldn't make the transition from QS-9000 to ISO/TS 16949. These organizations, including many assembly houses, chemical suppliers or mask-set suppliers, were forced to adopt ISO 9001 instead. This mandatory movement from QS-9000 to ISO 9001, rather than ISO/TS 16949, will have severe repercussions for semiconductor organizations in the years to come.
Since the early 1980s, the semiconductor industry has seen a hundredfold improvement in product quality. Organizations such as Motorola epitomized this change. In 1995, when Omnex helped Motorola's AIEG division became QS-9000-registered, Motorola was led by Bob Galvin, a charismatic chairman who was the icon for the resurgence in the U.S. electronic and semiconductor industry. Following that model, most semiconductor organizations followed a quality management systems road map similar to the one shown in figure 1.
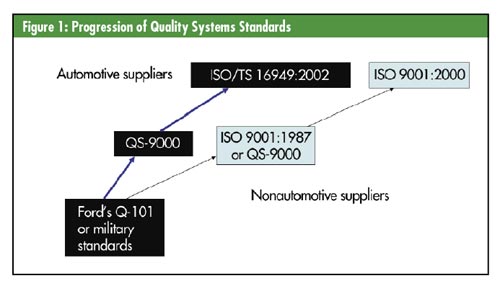
In this example, some semiconductor manufacturers, previously following military standards or Ford's Q-101 standard, transitioned to QS-9000 and then to ISO/TS 16949.
This road map resulted in semiconductor organizations sequentially applying gage repeatability and reproducibility; statistical process control; initial sample inspection reports, a predecessor to production part approval process (PPAP); failure modes and effects analysis (FMEA); control plans; 8-D; and others. These systems fueled the quality improvements prevalent in semiconductor organizations.
Others (i.e., those that weren't making automotive parts) backtracked into ISO 9001.
The problem is that, historically, semiconductor companies viewed quality management standards as a necessary evil to keep a customer happy. That mindset led companies to simply "meet the spec." As the standards got more rigorous, such as with ISO/TS 16949, the companies kept up and quality improved.
By backtracking into ISO 9001, with the same mindset in place, some semiconductor companies are only going to meet the spec rather than apply the more rigorous, but not required, process dictated by ISO/TS 16949. As a result, we anticipate a decrease in quality.
There are two reasons for product quality and design lead times to backslide. One is the failure to adopt ISO/TS 16949 and the stringent quality systems it has come to represent. The second is the advent of fabs and assembly houses in China and India. For the most part, the systems and workforces are very new in these factories. In our opinion, there will be a reversal in the hard-won quality improvements envisioned in the 1980s.
Culture and knowledge don't come with new technologies or new processes in the fab or assembly house. Furthermore, this evolution doesn't just happen by using common procedures. Most of our customers have great processes to transfer product from one fab to another, or from one assembly house to another. However, they need to work on systematic processes for new factory start-up. These knowledge and company-culture transfers happen in both systems and people.
There is a third factor that may lead to the deterioration of quality improvements. This is the emergence of fabless semiconductor organizations. These are organizations that are design-centered, performing no manufacturing. All manufacturing is subcontracted to contract fabs and assembly houses. For the most part, technology leaders who don't really understand the legacy of semiconductor quality systems lead these companies.
These organizations are also ISO 9001-based. Their systems may lack the rigor of those typically found in the larger and more mature semiconductor organizations.
While quality-system rigor is trending downward, customer expectations for product quality are increasing. Rather than expect a certain number of defective parts per million (PPM), customers expect zero defects per shipment. Modern semiconductor organizations generally have external PPM levels of between 30 PPM to fewer than 10 PPM. When working with these organizations, it's apparent that outgoing PPM levels are low, but that customer dissatisfaction is high. The semiconductor industry customer's product quality threshold is not really based on PPMs, but on the absence of issues that interrupt the manufacturing and/or assembly processes.
In other words, most electronic manufacturing and assembly operations have implemented "dock-to-stock" policies. When a semiconductor supplier ships bad products--even a few bad devices--it can result in costly repercussions. The line stops, which leads to a call to the quality department, which leads to a call to purchasing, which leads to a call to the supplier. A customer complaint is issued, and the devices are shipped back to the supplier. This incident subsequently sets off another set of chain reactions within the supplier. These interruptions and incidents are costly and numerous.
One top-10 semiconductor organization has more than 500 customer incidents a month in its Asian market alone. A small U.S.-based fabless semiconductor has close to 100 customer incidents a month. Even though their PPMs are low, they're too high for their customers. The semiconductor industry is in a state where PPMs may no longer be the right metric for measuring quality. The new metric may be percentage of shipments with no problems. Viewed that way, the same organizations with low PPMs may find that they have defects that measure close to a few percentage points. The second metric may be to add the internal and external PPMs together. When internal PPMs are high, there is a good chance that a few of the rejects get shipped. In fact, David Garvin established this fact in his study of the air-conditioner industry, published in a 1983 article in the Harvard Business Review. He found empirical evidence of a strong correlation between internal and external rejects.
Mature semiconductor organizations are adopting zero defect methodologies for quality improvement. These methodologies vary; however, all programs include a mistake- and error-proofing program.
The zero defects movement within the semiconductor industry is being championed by Delphi and Visteon, respectively. These organizations are pushing semiconductor organizations to ship error-free product. The methodology focuses the organization on adopting the following:
• Focus on the highest-known risks (i.e., mistakes and errors that have taken place in the last six months, both internally and externally).
• Update the FMEA and mistake-/error-proof the failure mode.
• Drive this control to the shop floor with effective process control.
• Create a layered process audit for manufacturing and support personnel to ensure control is followed, as seen in figure 2.
Zero defects programs are yielding significant improvements within semiconductor organizations.
The second important movement within semiconductor organizations is the adoption of define, measure, analyze, improve and control (DMAIC) Six Sigma methodologies. As part of the business, these organizations have, through balanced scorecards or policy deployment, identified a large list of money-saving projects each year. Although a fair number of these projects are implemented, the problem is that they're not being executed fast enough.
Semiconductor organizations need a methodology that can focus resources for large money-saving and strategic projects.
The DMAIC methodology combined with the Six Sigma infrastructure is yielding large dividends for semiconductor organizations. A recent launch of Six Sigma projects within an organization operating in the United States, Asia and Europe showed the following savings in each location: $7.5 million in the United States, $9.6 million in Europe and $10.2 million in Asia. There were more than $800,000 in savings on each individual project.
The semiconductor industry and the overall electronics markets are growing. The emergence of assembly and fabs in China, and a recent move to develop fabs in India, will create strategic tension. Will prices go up or down? Will there be an oversupply in the market? Which will carry more weight--design houses, or fabs and assembly houses?
With Motorola and Philips spinning off their semiconductor organizations, top management is preoccupied with many
issues. Semiconductor customers, meanwhile, remain
very quality-conscious.
Top management will have to take decisive action to improve quality and reduce costs close to home and also in emerging markets such as China and India. Implementing strategies that maintain customer satisfaction and improve profitability is recommended.
The opportunities for improvement in mature organizations are as follows:
• Implement ISO/TS 16949 and its Semiconductor Supplement. Focus on the processes that are preventive in nature, including measured system analysis (MSA), SPC, disciplined new-product design, design FMEA, process FMEA and control plans.
• Change the method of calculating PPMs because this metric doesn't capture the customer's real goal of shipments without problems.
• Understand that the overall throughput yield may be a dismal 70 percent to 80 percent. Implement Six Sigma DMAIC processes to save hundreds of millions of dollars in the first three years.
Several other important priorities beyond the scope of this article include reducing design turns and lead time, enterprise process management and supplier improvement strategies
Chad Kymal is an international trainer and consultant, and is chief technical officer and founder of Omnex Inc. He was the president of the Semiconductor Assembly Council in 2004 and helped write the ISO/TS 16949:2002 Customer-Specific Semiconductor Supplement. He has recently written two books, The ISO/TS 16949:2002 Implementation Guide, available through Paton Press, and the forthcoming Auditor Handbook to ISO/TS 16949:2002--A Guide to the Automotive Process Approach to Audits.
Praveen Patiyasevi (Pat) is currently the country manager of Omnex Co. Ltd., Thailand. He has more than 18 years of experience in supplier quality and development. He specializes in ISO 9001, ISO/TS 16949, QS-9000, advanced product quality planning (APQP), FMEA, control plans, MSA and SPC for suppliers. He is currently working with many semiconductor organizations worldwide.
|