by Roderick A. Munro, Ph.D., and Ronald
J. Bowen
Have you noticed the recent
news about the automotive industry? Industry gossips hint
that U.S. automakers aren’t happy with supplier performance
under the QS-9000 requirement and consider ISO/TS 16949:2002
a last chance for the international community to prove its
ability to ensure “perfect parts.” Consider:
Toyota has enough cash to buy both Ford Motor Co. and General
Motors Corp. if it wanted--but why would it?
Toyota is developing a new vehicle line--Scion--aimed at
young buyers. (People laughed when it developed Lexus, too.)
GM and Ford have made tremendous quality improvements during
the last 20 years, but in some key areas they haven’t
kept pace with Japanese automakers.
During the 1980s, U.S. OEMs were concerned about supply-base
reductions for a number of reasons, notably eliminating
poor performance. Now OEMs want to raise the bar even higher.
Who will be left? Only “excellent” suppliers?
What will it take to become an excellent supplier in the
automotive community? How will suppliers deliver only perfect
parts?
Both Ford and GM are closing the gap between them and
Toyota and are working with suppliers to ensure that parts
delivered to automakers’ assembly plants are the best
they can be. This article takes a look at a few efforts
that are currently underway.
The industry uses something called automotive core tools
to establish processes that meet customer requirements.
The five basic tools include:
Advanced product quality planning and control plans. These
are developed by product engineers rather than quality engineers.
The process monitors planning procedures during the design
and development of assembly plant products and establishes
controls to ensure perfect parts.
Production part approval process. This is carried out by
the supplier before production to ensure that everything
is ready. Thus, the run-at rate must be achieved before
the OEM assembly plant is ready to launch.
Failure mode and effects analysis. This is conducted in
both design and potential production failure modes to anticipate
problems and ascertain their risks prior to any occurrences.
Preventive action is carried out to eliminate the problems.
Statistical process control. This reduces variation in the
process and monitors process behavior characteristics. Under
the international standard, all employees are required to
know how to analyze statistical data. Using all the basic
statistical tools--not just control charts--is key.
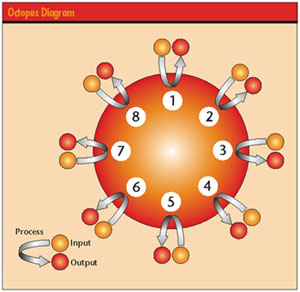
Measurement systems analysis. It’s more important
than ever for a supplier to be aware of a measurement system’s
uncertainties in order to establish benchmark data about
ongoing improvements. A single gage repeatability and reproducibility
study will no longer suffice. At least for families of gages,
suppliers must conduct stability, bias, linearity and graphical
analysis studies in conjunction with the gage R&R analysis.
Along with these five basic tools, additional methods
are now in use. ISO/TS 16949:2002’s new process approach
emphasizes process auditing, and internal auditors are expected
to identify turtle and octopus diagrams that lead to preventive
action reports, as illustrated on pages 60 and 62. This
approach should produce many more PARs than the traditional
corrective action report method. If all process activities
are correct and flawlessly executed, outputs will likewise
be flawless.
Six Sigma initiatives have been established. Specially
trained individuals and teams identify variation reduction
opportunities and process improvements. Both Ford and GM
now require suppliers not only to use problem-solving tools
but anticipate quality improvements of both parts and services
that are delivered to OEMs.
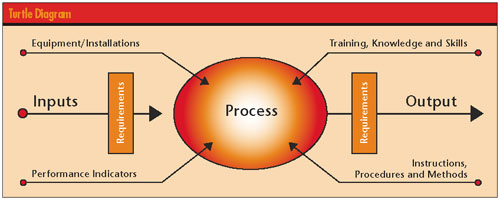
Is GM returning to the days of the conglomerates, fully
supported by Wall Street? The stage was set even before
the “bubble,” those stock market excesses created
by momentum players and traders.
GM’s pilot programs, Yellowstone and Blue Macaw,
might give us a glimpse into the future. Blue Macaw is GM’s
small-car program in Brazil, where it builds the Chevrolet
Celta. Lear is only one of its just-in-time suppliers. In
2000, Lear built a 63,000 ft2 facility adjacent to GM’s
Gravatai Automotive Complex so that car seats could be installed
immediately into the Celta.
Yellowstone is the code name for GM’s North American
Car Group’s plan to achieve profitability. “Yellowstone
builds on Blue Macaw and tailors the concepts to North America,”
explains GM’s Bill Hogan. The Yellowstone concept
includes codesigning with suppliers as well as modularity,
the latter being defined as combining subsystem components
into a single assembly-part number for delivery to the plant.
With codesigning, GM and its supply base work together to
define module requirements. Suppliers are far more involved
in product development than ever before.
Since 1999, GM has replicated these two pilots and the
lessons learned. In a September 2000 article in Automotive
Industries, John McCormick wrote: “GM’s new
plant in Thailand is cranking out Opel Zafires--and setting
the stage for other ‘common footprint’ plants
to come. In the pipeline for the next two to five years
are new Delta Township and Lansing Grand River plants in
Michigan, as well as a massive investment in a fresh facility
at Opel’s mammoth Russelsheim, Germany, complex. All
of these and more to follow will benefit from the lessons
learned in Rayong, Thailand, and its three sister plants
in Poland (Gliwice), China (Shanghai) and Argentina (Rosarlo).”
For more information, read the following articles regarding
Yellowstone and Blue Macaw:
“Yellowstone Provides Basis for Profitability in Small
Cars, GM’s Hogan Tells World Congress,” PR Newswire,
Jan., 1999 (www.findarticles.com/cf_0/m4PRN/1999_Jan_11/53545441/print.jhtml)
“Another Piece of the Puzzle (General Motors’
new Thailand plant),” Automotive Industries, Sept.,
2000 (www.findarticles.com/cf_0/m3012/9_180/65352732/print.jhtml)
“Lear Corporation Inaugurates New Brazilian Plant
to Supply General Motors Corp.’s Gravatai Automotive
Complex,” PR Newswire, July, 2000 (www.findarticles.com/cf_0/m4PRN/2000_July_20/63573448/p1/article.jhtml)
GM’s strategy appears to be right on track. Lansing
Grand River is in place, and suppliers now build and install
the front-end module right on line. Given this, it’s
easy to imagine suppliers staffing future assembly centers.
Each step of the process, from the body shop through car
track and shipping, would be the supplier’s and its
organization’s responsibility--consequently requiring
that suppliers be registered to ISO/TS 16949:2002 and
comply with the GM site’s ISO 14001 EMS processes
and procedures. Also, the seven quality strategies--which
include PFMEAs, PPAP, APQP, MSA, SPC and Six Sigma--must
be executed flawlessly.
GM has worked hard to fine-tune its vehicle development
process, and one need only look at J.D. Power and Associates
and Harbour reports to see the results of its labor. In
2003 J.D. Power awarded GM’s new Lansing Grand River
plant the Silver Plant Quality Award; the GM Oshawa, Ontario,
plant received the Gold Plant Quality Award. But Toyota
and other manufacturers continue to improve as well. For
example, in 2003, J. D. Power recognized Korean manufacturers
as the most improved in quality. Global competition is unrelenting.
GM registered all its sites to ISO 9001, QS-9000 and ISO
14001. They’ve championed certification of top management,
engineers, quality personnel, manufacturing personnel and
technicians as ASQ-certified quality engineers, quality
auditors, reliability engineers, and Six Sigma practitioners.
GM’s mission is to be the manufacturing best-in-class
at understanding, managing and controlling variation. Variation
must be reduced in all areas of production around the stated
target, specification or requirement. The same intensity
will be expected of suppliers that plan to do business with
the automaker.
GM has benefited immensely from its registration initiatives.
If today’s challenges happened a decade ago, the company
wouldn’t have survived the competitive requirements,
marketing incentives and economic variation it’s now
experiencing. But that’s exactly what ISO 9001:2000,
ISO/TS 16949:2002, ISO 14001 and their predecessors were
designed to help companies do--provided they comply with
the standards. If not suboptimized, each of the elements
can reduce process variation even in the simplest functions.
Ford’s assembly plants still use a concept called
“incoming quality” with suppliers. This involves
a monthly meeting during which the five to 10 worst suppliers
explain to plant management and senior Ford executives what
they’ll do to improve products. If a supplier stays
on this list for more than six consecutive months, the Ford
plant can withdraw its Q1 customer endorsement.
Ford’s Q1 endorsement was originally developed during
the early 1980s. The current version includes five categories.
(Note: Most of Ford’s listed documents are accessible
only to its suppliers via a confidential Web site. Other
items are available through the Automotive Industry Action
Group at www.aiag.org.):
Capable systems. Suppliers are required to maintain third-party
registrations to both ISO/TS 16949:2002 (or QS-9000:1998
through December 2006) and ISO 14001. Also, suppliers must
pass an MS 9000 materials management operations guideline
or materials management system assessment. Ford required
suppliers to register to ISO 14001 by July 1, 2003. For
those that didn’t meet the deadline, a special letter
published earlier this year through the AIAG outlined the
steps they must take. Basically, if a supplier has yet to
comply with ISO 14001, it’s subject to losing its
Q1 status.
Ongoing performance. With the ongoing performance requirement,
suppliers are monitored for five key performance metrics:
field service actions, stop shipments, part per million
performance, delivery performance and violation of trust.
A monthly report called “Supplier Improvement Metrics”
is issued with a six-month rolling status. Suppliers start
with 1,000 points, which diminish following various requirements
violations. If a supplier falls below 850 points, it must
create action plans for Ford’s supplier technical
assistant. If these fail to resolve the issue, then Q1 probation
is initiated.
Manufacturing site assessment. This is an evaluation of
whether a supplier is performing to Ford’s various
operating units’ expectations. The assessment includes
planning and demonstrating manufacturing process capability,
variability improvement (i.e., Six Sigma project results),
manufacturing efficiencies (i.e., new programs improved
through surrogate data, first-time-through initiatives and
overall equipment effectiveness) and customer satisfaction
(i.e., a robust and effective quality operating system).
Customer endorsements. These state that Ford operation units
are satisfied with the service and quality they receive
from a specific supplier. In addition to the assembly plants,
suppliers must seek endorsements from other Ford groups
they might deal with, including material planning and logistics,
customer service, and supplier technical assistants.
Continuous improvement. CI is a yearly assessment to ensure
that suppliers are actually improving. Suppliers must show
objective evidence both to their registrars and Ford indicating
improvement--not just change--in the way they satisfy the
automaker. This is monitored primarily through the SIM reports.
As one supplier technical assistant stated: “All STAs
are watching the continual improvement thresholds, which
suppliers must establish in 2003, with manufacturing efficiency,
variability reduction and customer satisfaction as the lead
indicators. The lean game, Six Sigma, FTT and OEE improvement,
and other quality tools are required.”
Ford has been credited with one of the best quality system
concepts in the industry, despite the fact that, during
the 1990s, the company didn’t seem to practice what
it preached. Today, it’s working toward a full partnership
with its suppliers to ensure that customers are truly delighted
about the product.
OEMs expect flawless execution in every process their
suppliers undertake. This begins with the advanced product
quality planning process and continues through service of
vehicle parts with no warranty claims. However, the purchasing
public also expects vehicles that are exciting and perform
as promised in advertising. In this regard, U.S. OEMs would
do well to heed Einstein’s definition of insanity:
doing the same thing over and over and expecting different
results.
As U.S. manufacturers continue their quest for the elusive
“silver bullet,” Japanese automakers found help
from people like W. Edwards Deming and Joseph M. Juran.
Toyota, Honda and others even opened their operations to
U.S. competitors and formed joint ventures such as NUMMI,
knowing that U.S. organizations would miss the opportunity
to improve, as Japanese manufacturers did, too, early in
their benchmarking.
W. Edwards Deming summarized his life mission in what
he called “profound knowledge” into four key
attributes: appreciation for a system, knowledge of variation,
theory of knowledge and psychology. Japanese organizations
listened to Deming and implemented and improved upon what
they learned. U.S. OEMs used Deming’s ideas for a
while, but it’s not always evident that they consistently
apply what they’ve learned. They still have an opportunity
to demonstrate continual improvement, but time is growing
short.
The silver bullet is nothing more than understanding,
managing and controlling variation. It must be reduced around
targets, specifications and requirements in every process
step, from concept through product sale.
Roderick A. Munro, Ph.D., is a business improvement
coach with RAM Q Universe Inc. (www.ramquniverse.com)
and has more than 30 years of experience in manufacturing,
automotive, service and education. He has served, trained
and consulted for many industries in the United States,
Canada and Europe, and trained or consulted with production,
nonproduction and transportation tier-one suppliers in quality
systems. Munro is an ASQ Fellow, Certified Quality Engineer,
Certified Quality Auditor, Certified Quality Manager and
a Fellow of the Quality Society for Australasia.
Ronald J. Bowen spent 46 years with General Motors,
focusing on variation reduction. He developed the internal
audit process and managed QS-9000 registration and ISO 14001
implementation and registration at one of GM’s plants.
He now serves as president of Quality Station Inc., which
provides consulting services in quality and environmental
management systems implementation and internal audits. Bowen
is a past chair of ASQ Greater Detroit Section, served as
the ASQ deputy chair for four years, is a member of ASQ’s
American Quality Congress Board, examining chair for the
ASQ Automotive Division and deputy regional director for
ASQ Region 10. He’s an ASQ senior member, and CQE,
CQA and IRCA QMS provisional auditor. Letters to the editor
regarding this article can be sent to
letters@qualitydigest.com.
|