by Charles Rastle and Julie Fraser
Using Six Sigma initiatives
to focus on improving the performance of business and manufacturing
processes isn’t a new concept. But a growing number
of manufacturers seeking to stay competitive and improve
profitability are, instead, turning to Six Sigma to provide
stronger value to customers. As a structured and fact-based
means of achieving continuous improvement, Six Sigma programs
need accurate data to analyze current performance issues
and their root causes. Measuring improvement--in terms of
defects per million, for example--requires accurate data.
Unfortunately, some Six Sigma programs get bogged down
in the area of data collection, particularly when collecting
information related to production, fulfillment and service
operations. Sometimes, Six Sigma teams--whether comprising
trained Black Belts, Green Belts or other employees--spend
significant time manually gathering data that they aren’t
confident is correct, which can cause justifiable frustration.
If the gathered data has built-in bias at the source or
is subject to interpretation, the results of analysis will
be suspect. At the very least, progress will be slow, which
can blunt support and momentum. Furthermore, manual data
collection is inherently error-prone, so an analysis may
be skewed by the Six Sigma team itself.
Preventing Six Sigma programs from withering due to a
lack of rich and accurate data requires sound information
systems. Ideally, these information systems should gather
data automatically at the source of an activity, which would
avoid data-source inaccuracies as well as errors potentially
resulting from human interpretation or filtering.
Six Sigma teams can benefit even more from data available
in a form that already correlates processes to products
and customer orders. In a production plant setting, a manufacturing
execution system is designed to provide just such data.
As an MES guides the execution of production processes,
it can also gather detailed data about the process, materials
and production. The information can be correlated to show
all materials that go into a product--and the conditions
during all of the process steps the materials underwent.
Many of these systems are tamper-proof to help companies
meet regulatory requirements, so there’s little room
to question the data. An MES is a rich source of detailed
yet contextualized information that allows Six Sigma programs
to take root and flourish.
Research findings from a newly released report, “MES
Performance Advantage: Best of the Best Plants Use MES,”
illustrate the benefits of MESs to plants undertaking Six
Sigma programs. Written by Industry Directions and sponsored
by Rockwell Automation, the report uses an existing database
of survey responses to questions about performance and business
practices and compares companies that are and are not using
an MES.
In a database of 106 plants judged to be the highest-performing
in North America during a period of five years, 24 responded
that they use Six Sigma methods extensively. Within that
group, 58 percent of respondents with Six Sigma initiatives
also use an MES. Despite the relatively small number of
Six Sigma users, the differences within the group are striking.
(All percentages listed here are the mean response of the
group mentioned--those using Six Sigma and either using
or not using an MES.) Here are some results:
Companies using an MES together with Six Sigma improved
their profitability 151 percent over three years, whereas
those using Six Sigma without an MES improved profitability
by 22 percent, as illustrated on this page. Improving profitability
by even 20 percent is impressive, but organizations with
an MES improved 678 percent more, on average. Some of this
profitability came from improved productivity for plants
using an MES and some came from cost savings.
Process capability is a cornerstone of Six Sigma strategy.
The goal is to create business processes that generate 3.4
defects per million or fewer (Six Sigma including a 1.5
sigma drift). Again, the MES fostered much greater success
for the group of companies undertaking Six Sigma in this
study. Companies using an MES together with Six Sigma had
a process capability (Cpk) of 2.4, compared to 1.5 for those
not using an MES to support their Six Sigma initiatives.
Some specific process results were greater cycle-time reductions
over three years--more than 54 percent greater in order-to-ship
cycle time, the primary target for customer satisfaction.
And, among plants using an MES with Six Sigma, the manufacturing
cycle time component shrank by more than 82 percent compared
to plants using Six Sigma alone (60.6% vs. 33.2% over three
years). In a previous study by Industry Directions, “Becoming
Demand Driven,” the key indicator of demand-driven
performance was revealed to be achieving cycle times shorter
than the customer order lead time.
Companies using an MES with Six Sigma also decreased lot
sizes more dramatically and were better able to build to
order. For just-in-time orders, the plants using an MES
built entirely to order 85 percent of the time; those using
Six Sigma without the MES data source built-to-order for
JIT 40 percent of the time, as illustrated in the chart.
Customers who ordered on a JIT basis and got exactly what
they wanted built for each specific order were likely to
be more satisfied.
The study reports other benefits of MESs, both to companies
with Six Sigma programs and overall. What is clear from
this data subset is that having accurate, reliable and comprehensive
operational data from an MES helps companies fully leverage
Six Sigma initiatives. Those using MESs realize significantly
more dramatic gains in performance.
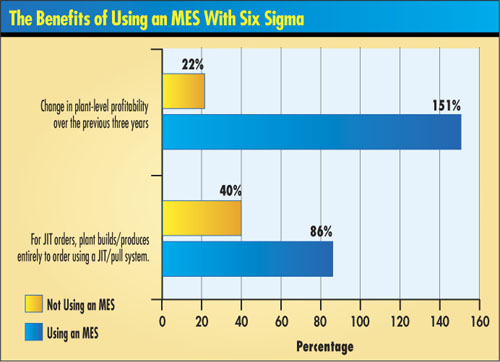
The five critical processes used in a Six Sigma program
are define, measure, analyze, improve and control. An MES
provides a foundation of data and ongoing support for all
of those except define--which it assists.
Define--Identifies business issues that affect
the customer, defines project goals and boundaries, and
distinguishes issues that must be addressed for improvement.
Here, existing MESs can be used to help identify problems
that must be addressed, whether in the process, materials
or output.
Measure--Gathers information about the current
situation as baseline process performance data and identifies
problem areas. MESs provide data about plantwide process
performance, usually with both current and historical data
available.
Analyze--Identifies root causes of problems and
confirms those causes with data-analysis tools. Again, an
MES has the foundational data, including all production
processes correlated to each other and the materials that
flowed through the manufacturing process, the personnel
that worked on them, the conditions in the plant and the
customer order that was filled. An MES can also feed its
data into analytical tools, and some MESs now have internal
operational analysis capabilities in the off-the-shelf software
product or can be built-in during integration.
Improve--Implements solutions or changes to the
business processes to address the root causes identified
during analysis. The MES can be reconfigured to change process
parameters or flows, indicate conditions outside control
limits and provide operators with the necessary data to
avoid or correct problems early.
Control--Ensures day-to-day business processes
stay in the improved state and become standard and integrated
into the daily routine. The MES can enforce business processes--disallowing
operations when certain conditions are not met, for example.
It also measures performance on an ongoing basis to evaluate
the success of an improvement.
The July 2003 issue of Quality Digest featured an article,
“Six Sigma for the Rest of Us,” which discussed
ways smaller companies can succeed using Six Sigma without
making major investments in Black Belt training or major
process redesign. In keeping with this philosophy, MES technology
is becoming more available to companies of all sizes. A
variety of MES solutions are available today to meet the
unique requirements of companies large and small. Both MES
and Six Sigma solutions can be focused on a specific piece
of equipment or plant area, or they can provide a comprehensive
solution that manages the operation of an entire production
plant.
MES applications utilized in itemized situations are modular
solutions designed to collect and provide visibility into
equipment operating data. An MES solution provides information
needed by Six Sigma Black Belts to measure current performance,
analyze operations and identify opportunities for improvement.
MES applications can also provide feedback to operators,
enabling them to ensure that equipment or a line is operated
within defined control conditions.
The advantage of such modular solutions is that they’re
focused on requirements of a specific production area or
process. They’re configurable and have been designed
to meet the requirements of a specific area of the manufacturing
plant. The plant does not need to change its operations
to fit the MES. Rather, the MES can be configured to meet
the needs of the plant.
MES applications now being deployed are also scaleable.
In many cases, a Six Sigma project will be focused on a
single piece of equipment or line. At the completion of
the project, if value is demonstrated, the manufacturing
company will want to deploy the MES throughout its operating
plant. The current generation of MES applications has the
capability to be rapidly scaled-up from a single line to
an entire plant.
Many companies are deploying MES applications that enable
the collection and analysis of multiple types of data. Data
on machine downtime are no longer the sole information needed
to improve the throughput of a production line. New MES
applications allow Six Sigma teams to look at more complex
relationships and analyze downtime data, quality data, operating
conditions, product type and labor resources. In the past,
this required Six Sigma teams to generate separate reports
and then compare data across reports. Current MES applications
allow Six Sigma teams to view data in a single application
for review and analysis. This has been facilitated by the
capability of MESs to exchange data among various enterprise
systems (e.g., enterprise resource planning, material requirements
planning and laboratory information management system) and
their improved analytical capabilities.
In their book, Six Sigma: The Breakthrough Management
Strategy Revolutionizing the World’s Top Corporations
(Currency, 1998), Mikel Harry and Richard Schroeder discuss
the fact that companies improving 1 sigma each year, from
3 sigma to 4.8 sigma, will experience a 20 percent margin
improvement. Recent research shows that adding an MES to
support the Six Sigma program can further boost margin improvement.
At 151 percent over three years, the companies in Rockwell’s
newest study average about 50 percent margin improvement
each year. The reason for this success is twofold. First,
the Six Sigma process is enhanced when its analysis can
be based on critical production data present in an MES.
This data enables Six Sigma teams to make their analysis
and develop production improvement recommendations based
on solid and consistent data. Second, an MES also provides
data necessary to define current operations and establish
a baseline to measure improvement and value delivered to
the company.
Manufactures need to keep in mind that analysis of the
existing situation and recommendations for improvement are
just part of the Six Sigma process. MESs help provide the
capability to monitor the production process and implement
business process control to improve production execution.
Many Six Sigma projects and MES implementations have failed
in the past because MESs have not been utilized to help
drive the continuous improvement process. Manufacturers
must view MES technology as a vehicle for business change
and improvement in the manufacturing process.
By properly incorporating an MES with Six Sigma initiatives,
manufacturers can effectively boost profitability, productivity
and process across their operations.
Charles Rastle is an industry strategic marketing
manager for Rockwell Automation’s Global Manufacturing
Solutions group. Rastle earned his bachelor’s and
master’s degrees from the Colorado School of Mines,
and he earned his MBA from the University of Colorado.
Julie Fraser is a principal and analyst with Industry
Directions, a manufacturing and supply-chain analysis and
consulting firm.
|