by Thom Linehan
Two electronics directives implemented by the European Union--Restriction of Hazardous Substances (RoHS) and Waste Electrical and Electronic Equipment (WEEE)--have drastically changed the way manufacturers produce products, and how those manufacturers work with one another and their suppliers. RoHS prohibits or restricts the use in electronics equipment of six potentially harmful materials: mercury, hexavalent chromium, cadmium, lead, polybrominated biphenyl, and polybrominated diphenyl ether. WEEE requires manufacturers to reacquire and recycle certain electrical and electronic equipment made after August 2005 instead of just throwing those parts away.
Confounding the issue, many countries outside the European Union, and even some states in the United States, have started implementing their own versions of RoHS and WEEE, making it difficult for global companies to consistently interpret the regulations and ensure compliance.
South Korea, Taiwan, Australia, and other countries are also planning to implement their own versions of RoHS. The biggest concern rising from this is that each country will have a different marking requirement, which will complicate the scenario for manufacturers looking to comply and for regulators looking to inspect products for compliance.
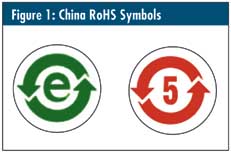
China’s RoHS labeling system is comprised of two symbols. Compliant products get a green “e,” and noncompliant products are orange with a number corresponding to the number of years it is expected to last before it begins leaking contaminants.
|
China, too, is taking its own approach to RoHS. Despite discussions with the European Union about implementing RoHS, China developed its own version, which has fewer exemptions and doesn’t require all products to be compliant. For example, if a product is compliant, it’s marked with a green “e.” If it isn’t, it’s marked with an orange number signifying the number of years that the product is expected to last before it begins leaking contaminants, as seen in figure 1 at right.
The National Electrical Manufacturers Association is advocating that the United States implement its own version of RoHS by mid-2010, which would supersede individual states’ legislation and create a consistent directive for the country.
Although reasonable in theory, complying to all of these directives would be a challenge for any company. However, most organizations see the process as an essential business decision that will serve customers best in the end. D-M-E Co., a global mold technologies leader in the plastics and die-casting industries, quickly made the decision to achieve compliance to avoid losing sales and ensure that its customers receive the compliant parts they need.
Dealing with these new regulations required D-M-E to look not just at its own products, but also at its processes and suppliers to ensure that every aspect of the manufacturing process was compliant.
Interpretation issues pose one of the greatest challenges with these new rules. RoHS restricts the content of the six items by weight but is unclear whether the restriction is at the component level, subassembly level, or for the whole product. WEEE leaves it up to the manufacturing companies to determine what proper disposal means for products made prior to 2005.
D-M-E resolved this conflict by using an all-encompassing interpretation of RoHS and WEEE rather than risk losing sales because of noncompliant products. The company’s solution, and one that many manufacturers should consider, is to alter all part designs--from circuit boards to small components such as fasteners--to comply with the most stringent interpretations of RoHS and WEEE. This ensures that products are compliant and accepted no matter where customers are in the world.
D-M-E circuit board using a surface-mount design rather than the more traditional through-hole configuration, which is not WEEE-compliant.
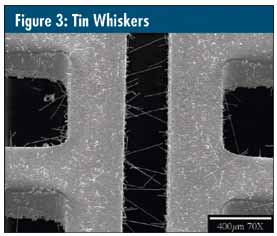
Magnified view of tin whiskers found on some electronics
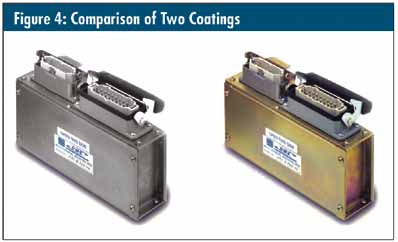
When shown side by side, the color difference is very clear between trivalent chromium (right) and hexavalent chromium materials.
This symbol is on all products requiring proper disposal as named in the WEEE legislation.
|
The first step in RoHS compliance is removing the six potentially harmful materials from products. To determine which materials you can substitute for the harmful ones, contact research institutes, contract-manufacturing companies, or even in-house experts. For instance, D-M-E relied on the IPC - Association Connecting Electronics Industries, an electronics industry group in Bannockburn, Illinois, for help with new solder formulas.
Also, you will need to work closely with suppliers and outsourcing partners on each alteration to ensure complete supply-chain compliance and quality assurance.
D-M-E started by reengineering its entire line of temperature-control equipment to eliminate all traces of lead. This solved the problem of determining what percentage of restricted materials is allowed in each country.
For electrical-board layouts, D-M-E had to change from a through-hole to a surface-mount design. With the former configuration, lead components were actually stuck through the circuit board to hold them in place, causing contamination to the solder pot over time. With the surface-mount design solution, lead components sit on top of the circuit board rather than penetrating it, eliminating contamination. As another benefit, surface-mount boards are easier to recycle, facilitating WEEE compliance, as seen in figure 2, right.
The configuration change didn’t completely solve the problem. To create a surface-mount circuit board, components are attached using a solder paste screened onto the face of the board. The board is then moved through an oven to melt the solder paste. However, the high-process temperatures required to melt the paste can cause problems with the components and boards, potentially affecting product longevity.
D-M-E designed a new oven-heating process for adhering components to the electrical boards. Using precise timing and a single pass through the oven rather than multiple exposures to the intense heat, D-M-E ensured proper connection with minimal heat stress to the components.
Another issue the company faced was tin whiskers on its edge-card connectors. On lead-free tin surfaces, tin whiskers may grow long enough to short one electronic circuit to another, causing the product to malfunction. This issue was solved by using hot-dipped plating with a matte finish wherever possible instead of electroplating, because a shiny electroplated finish is most likely to cause whisker growth, as seen in figure 3 at right.
The lead ban also affects solder appearance. IPC has recommended a new solder made of 97 percent tin, 0.5 percent copper, and 2.5 percent silver to comply with RoHS. Manufacturers are concerned because the solder joints don’t look as clean and shiny with this new mixture as they did when using a tin and lead mixture.
Manufacturers should focus on reevaluating old standards rather than trying to comply with them. For instance, IPC has created new levels of acceptability for visual inspection of lead-free circuit boards. The new, not-as-pretty appearance is acceptable until something better is developed.
With electrical enclosures, D-M-E needed to eliminate hexavalent chromium, a restricted material often identified by its yellowish color. The challenge was finding a cost-effective equivalent that offers the same corrosion resistance. D-M-E switched to trivalent chromium, a silvery, compliant material that offers the same level of corrosion resistance and the same cost of plating, as seen in figure 4, at right.
As D-M-E reengineers its products, the barcodes are changed to indicate which parts are compliant. Not all manufacturers have chosen to do this, which may make proving compliance difficult later on.
Also, D-M-E makes thousands of parts for its customers. The process of testing and changing each product so quickly is impossible to do without a small percentage of errors. Therefore, D-M-E remains in close contact with its customers to remedy noncompliances immediately.
Supplier compliance may be the most important aspect of the entire RoHS and WEEE challenge. One bad component can cost sales.
Although product reengineering requires working closely with suppliers and outsourcing partners, it may not cover all of them. You may be a compliant manufacturer, but if your suppliers or your suppliers’ suppliers aren’t compliant, you’ll have trouble.
D-M-E works with its suppliers and outsourcing partners to ensure complete compliance to supply chain and quality standards. Sometimes this means testing suppliers’ components to make sure that they truly are compliant. When working with suppliers, ask them to show compliance in their product literature. On the supplier side of the conversation, your customers may ask you to test your products for compliance. Third-party tests of your product line can be expensive, and you should carefully weigh these requests in project proposals.
Unfortunately, upgrading products for compliance doesn’t come without a cost. In one case, the new requirements increased production cost for one of D-M-E’s domestic suppliers, resulting in a $10 per unit price hike. Although D-M-E worked with the supplier for almost five years, it had to take its business elsewhere. In the end, the product was outsourced to China, where the cost fell $30 and quality and compliance levels remained the same.
WEEE’s aim is to eliminate air, soil, and water contamination from the hazardous disposal of manufacturing materials and chemicals. Problems such as the one discovered by Erin Brockovich, where water contaminated with hexavalent chromium sickened California residents, would be prevented by this directive.
For manufacturers, WEEE’s compliance challenge is deciding what to do with all the component pieces returned to them. It will probably mean longer-lasting parts as manufacturers do more repairing and less disposing.
Consumer electronics don’t tend to have long life spans. When a $35 CD player dies, few consumers will spend $50 to fix it. Even if manufacturers bear the cost of returning the items for disposal, will consumers actually return them? In Belgium, consumers pay recycling fees up front when they purchase items, and some U.S. computer manufacturers are beginning to do that as well.
Addressing the RoHS side of compliance will help make the WEEE side easier to tackle. As you work to eliminate banned materials from your products, make sure you also consider the WEEE effects.
Although this article has focused on the challenges of complying with RoHS and WEEE, the endeavor offers some benefits as well. Eliminating lead-based processes from manufacturing saves time and money on complex environmental-compliance issues. Manufacturers will worry less about tracking and reporting use of lead solders and managing hazardous-waste disposal. They will also save time by no longer keeping detailed records regarding lead consumption.
Reevaluating products for RoHS can also help improve reliability and quality. When D-M-E eliminated hexavalent chromium from its electrical enclosures, it led to an environmentally friendlier alternative that was cost-effective and offered the same corrosion resistance that the product needed.
Finally, RoHS and WEEE are probably just the beginning of a plethora of environmental changes manufacturers will face. Being able to respond quickly to these changes gives companies a competitive advantage because they will have established a record of accomplishment and a reputation for being compliant. Having that flexibility could provide companies with new customers that they might otherwise have missed.
Companies will face some obstacles during the compliance process, but there are ways to overcome them. It’s important to remember that no matter what the regulation, you must still deliver quality products to your customers.
Manufacturers can’t afford to take a passive approach to these issues. They must take the lead in making these changes if they want to compete globally and maintain a diverse customer base. Really, they only have two choices: Embrace early and lead the way, or resist and get left behind.
Many companies have yet to make the transition. By starting now, you’ll gain a definite competitive advantage.
Thom Linehan is the global business manager of temperature and process control at D-M-E Co. Linehan is responsible for engineering and product management, product sourcing, and training at D-M-E. He has led D-M-E’s engineering and marketing through the ISO 9001 process and has also served as an internal auditor in the 28 years that he’s worked there. Linehan has written numerous white papers for the plastics industry’s ANTEC and RETEC conferences, participated in creating the guideline AN148 of the Society of Plastics Industry, and created WC73, a standard for conductor usage at elevated temperatures, via the National Electrical Manufacturers Association.
|