Call Me Old Fashioned--Part 1
I notice the issue of capability indexes still hasn’t gone away and agree with what Donald Wheeler wrote several years ago in this column: I don’t have any use for them or the accompanying obsession with normal distribution theory.
Static summaries say nothing about the process producing the data. Give me a time plot any day, accompanied by the answers to two important questions:
“How were these data collected?”
“How does this plot affect one’s degree of belief in predicting the next batch from this process?”
Here’s an example. Say you’re considering four vendors for a big contract. You’ve requested that each make a run of product that will supply you with 50 random samples for SPC calculations, as well as the lot’s production control chart and its Rbar/d2 estimate of standard deviation. Your specification range for this quality characteristic is 5,700 to 6,300. Regarding costs: vendor two < vendor one < vendor four < vendor three.
Your quality assurance lab comes up with a summary of the four lots based on the samples provided and produces the following comparative histogram:
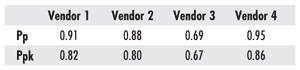
From the Rbar/d2 calculation of the process standard deviation supplied by the vendors, you calculate their Cp and Cpk:
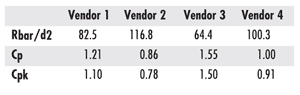
Your company’s statistical guru cautions that the data for vendors three and four aren’t normally distributed: “Vendors one and two both pass the normality test with p > 0.05,” he says, “although vendor four doesn’t quite fail the null hypothesis at the p < 0.01 level.”
His analysis of variance proves no statistical difference among the four vendors with a p-value of 0.307 and confirmed by the overlapping 95-percent confidence intervals:
Given this, should you base your decision solely on price?
Then again, vendor three wasn’t normally distributed, had the highest overall standard deviation and was the most expensive. Obviously, its estimate of standard deviation is incorrect. So, the analysis is redone with vendor three omitted:
Looks like vendors one, two and four are virtually identical; it all comes down to price.
How many of you do this every day and must make decisions based on such calculations? What do you generally do--and what would you do in this situation?
Then you discover the control chart sent by each vendor with its shipment….
To be continued next month.
Davis Balestracci is a member of the American Society for Quality and the Association for Quality and Participation. He previously served as chair of the statistics division of ASQ. His book, Quality Improvement: Practical Applications for Medical Group Practice (Center for Research in Ambulatory Health Care Administration, 1994), is in its second edition. Visit his Web site at www.dbharmony.com.
|