Continuous Improvement and Your QMS
Last month I discussed the notion that, properly implemented, the requirements of a management system standard such as ISO 9001 can provide not only a baseline for improvement but also the tools to hold the gains made through improvement activities. That begs the question: What do we mean by "properly implemented?" There are some obvious answers, such as using the audit program required by ISO 9001 to monitor adherence to the process changes needed to achieve improvements. But using a quality management system (QMS) as a basis for improvement requires a bit more than that.
First, let's review what continual improvement is and what it's not. Continual improvement isn't necessarily improving everything in the organization. However, it does entail identifying and planning changes to those products, processes or systems that will improve the organization's performance. Such continual improvement requires:
• Setting objectives
• Planning for improvement and change
• Achieving both incremental and breakthrough improvements, which are different in both outcome and process
• Achieving project-by-project changes
• Involving people and teamwork
• Learning and innovation
• Refusing to lose the gains you make
The notion of continual improvement is one of eight quality management principles in ISO 9000:2000. Why is continual improvement so important? It's important because many businesses must improve performance just to keep up with their competitors. But it's also important because processes, equipment and even the QMS itself can deteriorate over time unless they receive ongoing attention focused on improvement.
Annex B of ISO 9000:2004--"Process for continual improvement," briefly describes the distinction between breakthrough and incremental improvement. Maintaining a clear understanding of this distinction is important for an organization committed to improvement because it's easy to use inappropriate improvement tactics. The distinction between both kinds of improvements is shown in the figure below. There are potential traps in the continual improvement concept when organizations expend large sums of capital to achieve small gains or expect great gains from employees with no improvement budget. Recognizing the distinctions and applying them to each opportunity is key to achieving planned improvement.
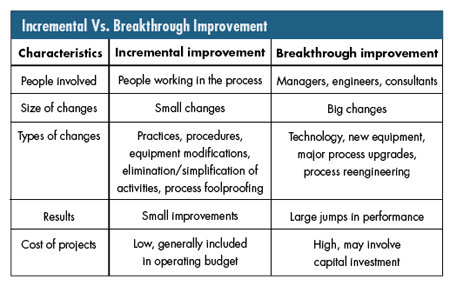
Making lasting improvements generally necessitates improving organizational processes. For example, it's obvious that improving part conformity with requirements often requires better process capability. However, it's less obvious that an apparent need for a better product design requires a better design process. Often, continual improvement requires eliminating the real causes of problems. To the purist, there are two basic types of causes. To the pragmatist, there are three:
•Special causes, which aren't part of the planned process
•Common causes, which are inherent in the process
•Phantom causes, which are situations or conditions that appear to be causes and are often "corrected" but actually have no effect on the process
Sometimes sustained improvement isn't achievable unless several processes are changed. In the case of improving a product design, it might be necessary to change not only the design and development process but also the process for hiring designers, the capital allocation process and the process for understanding customer requirements. In such a case, overall system changes are needed; just starting a new product design project may be the organization's worst approach.
Note: This article is based in part on chapter six of Unlocking the Power of Your Quality Management System: Keys to Performance Improvement by John E. (Jack) West and Charles A. Cianfrani (ASQ Press, 2004).
John E. (Jack) West is a consultant, business advisor and author with more than 30 years of experience in a wide variety of industries. From 1997 through 2005 he was chair of the U.S. TAG to ISO TC 176 and lead delegate for the United States to the International Organization for Standardization committee responsible for the ISO 9000 series of quality management standards. He remains active in TC 176 and is chair of the ASQ Standards Group.
|