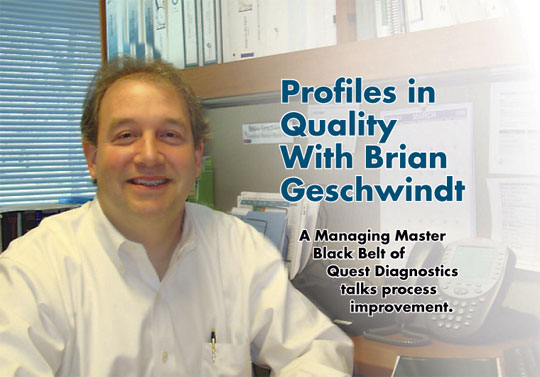
by Mike Richman
Brian Geschwindt is a man who lives and breathes process improvement. As a Managing Master Black Belt for Quest Diagnostics Inc., headquartered in Madison, New Jersey, he’s responsible for Six Sigma implementation in the customer touch functions at one of the largest medical test and information organizations in the United States. He’s practiced quality improvement at various organizations for more than 20 years.
Geschwindt is a judge for the Lean Six Sigma CEO of the Year Award 2008, being presented at WCBF’s Lean Six Sigma Summit in Chicago, April 29-May 2. He’s also speaking at this year’s summit. For more information on this event, including registration information, visit online at www.wcbf.com/quality/5082.
Quality Digest : What separates exceptional leaders from their peers in managing the necessary culture change that comes with lean and Six Sigma implementations?
Brian Geschwindt: What separates exceptional leaders from their peers is that they don’t treat quality as something extra on top of everything else that needs to be accomplished. Exceptional leaders understand that quality principles should be ingrained in the day-to-day running of the business. It’s embedded in there because making sure that you have the highest-quality services and products is going to get you more revenue growth, greater profit, and better customer satisfaction. These leaders are not reactive about quality improvement. They are less likely to say, “We have a problem and now we need to fix it. Let’s put a program in place, and then once we fix the problem, the program can probably go away.” Exceptional leaders ensure that the program remains for ongoing improvement
QD : Your company, Quest Diagnostics, is a leader in medical testing services. What are the special challenges and opportunities for quality improvement within the health care industry?
BG : Quality improvement methodologies such as Six Sigma and lean are relatively new to the health care industry, so our industry is just beginning this journey. In health care, the key stakeholders are physicians or highly trained technical people who have a very strong ownership of their processes. The special challenge is gaining buy-in with these particular stakeholders to allow quality improvement initiatives to move forward.
For example, we do lean Six Sigma at Quest Diagnostics. We know how to find and eliminate waste, and we’re teaching our people these processes. Our company led the industry forward by bringing Six Sigma to health care in 2000, and we’ve had more than 2,000 people go through Green Belt training. We’ve trained more than 400 Black Belts. We’ve executed more than 2,000 projects. Quest Diagnostics has embedded Six Sigma everywhere. We want to get the message out there so when you discuss Six Sigma, or talk about the DMAIC methodology for example, our people can say, “Oh, I know what that is… define, measure, analyze, improve, and control!”
QD : So you’re all speaking the same language.
BG: Right.
QD : Do a number of those Green Belts eventually develop into Black Belts?
BG : Yes, one of the requirements that we have, when we’re posting for Black Belt positions, is to give a strong preference for certified Green Belts who have been through our training program. When someone calls me from operations, sales, or marketing, and they want to be a Black Belt, I ask them, “Have you been through Green Belt training? Are you certified? Have you done your two projects?” If they say, “Yes,” then I go a bit deeper and ask, “Why do you want to become a Black Belt?” Being a Green Belt is a part-time role. That person has a full-time job and then, while doing their job, they own a few Green Belt projects. It may actually be more challenging for those in the Green Belt stage because they own Six Sigma projects in addition to their full-time professional responsibilities, whereas Black Belts are focused on their Six Sigma projects as their full-time job.
QD : What’s your background and training? How did you find your way to Six Sigma and Quest Diagnostics?
BG : I received my degree in industrial engineering from Lehigh University in the mid-1980s, where I was taught the concepts of the just-in-time methodology and statistical process control, which eventually morphed into lean and Six Sigma. I worked for General Electric for two years in their manufacturing management program (before Six Sigma), where I learned a great deal about operations. I then took a position with Corning Inc., where we were applying the just-in-time system (lean) in one of our manufacturing plants. I was involved in converting the plant from the classic functional department orientation to manufacturing cells. I then had an opportunity to apply lean principles to Corning’s clinical lab business and essentially did many of the same things in the laboratory environment that I did in manufacturing. When Corning spun off their lab division as Quest Diagnostics, I stayed on and held various operations roles. When our CEO said that we were going to begin a Six Sigma program at Quest Diagnostics, I wanted to participate because it was really an extension of all of the things that I had already learned.
QD : People tend to get wrapped up in the statistical elements of Six Sigma, but isn’t the methodology less about just measuring, per se, and more about simply doing better work?
BG : What it’s about is innovation and improvement. How you get there can be simple or complex, depending upon the challenge at hand. You may need the deepest tool in the world; you may need to do a multivariable analysis because, say, you’re mixing 17 chemicals together. However, if I’m looking at customer service call-in rates and I see that I have 14 people who are experiencing challenges, and that’s what’s driving a particular root cause situation, I can say, “OK, here’s the issue. I may be able to just run a Pareto chart because I know that the problem is occurring within this segment of the operation over here.”
QD : It doesn’t have to be that complex.
BG : Six Sigma is not about complex measurements. Six Sigma is about making improvement and measuring the right things to understand whether you made the improvement or not.
QD : That’s an excellent, clear statement. Many times, however, people get lost in the language, the tools, and the statistics of Six Sigma.
BG : Very true. If I get a Black Belt that I want to hire and he or she says, “I’m great at statistics,” I think, “ Well, that’s a good skill to have, but can you execute? Can you get things done? Can you make a change?” Strong Black Belts will not allow themselves to become so caught up in analysis that they can’t make the necessary changes to improve the process. They present an innovative improvement, and they make sure the necessary changes happen so that it gets done .
QD : Your company is a far-flung enterprise with a large number of locations. How do you ensure quality and standardization in such a highly diffuse environment?
BG : We have a central or corporate group consisting of Six Sigma and subject matter experts that develop standards with the participation of many of our units. Once the standard is agreed upon, it’s rolled out to the entire organization for implementation. In many cases, the implementation of the standard is accomplished through a Green Belt initiative at that location.
QD : What is the role of the Black Belts in this process? Are they primarily mentors for the Green Belts?
BG: Yes, exactly. If the Green Belt has done several projects, the Black Belt may be very hands-off. However, if it’s a first-time project for a Green Belt, that Green Belt may go to the Black Belt and ask questions such as, “Can you help me with the define stage?” or “What should I measure to make sure that when we put this program in place, it will actually work correctly?” In some cases, the Green Belt may need clarification on the DMAIC steps; in others, a Black Belt may teach them how to do project management.
QD : In your experience, what element of the Quest Diagnostics’ culture has been most positively affected by Six Sigma? Where do you still have work to do?
BG: I think that all elements of the culture have been positively affected. I’m not aware of any part of our organization that is not using Six Sigma in one way or another. We have a great amount of work still to do because there’s so much opportunity in health care. We can get a process into the Six Sigma methodology today, but tomorrow the requirements might change, so it’s always a moving target. There are always new processes, and we never stop; we always improve. Our vice president of operations states that process improvement is a way of life. It is not something we turn on or off. Haven’t we all had experiences where we go into an area where we’ve worked hard to improve the process and then we say, “But….”
QD : You can see there’s more work to be done.
BG : Yes, that’s right. And at Quest Diagnostics we believe it’s important work to be done because we know that our patients and their doctors are counting on us.
Mike Richman is Quality Digest’s publisher.
|