Averting 100-Percent Inspection
Simsack revisits sampling
Michael J. Cleary, Ph.D.
mcleary@qualitydigest.com
Greer
Grate & Gate has secured a major National Park Service
contract that involves making iron gates to replace deteriorating
older models and installing them in all of the national
parks in the United States.
Because this is the largest order in the company’s
history, its president, Rock deBote, is determined to ensure
that the gates will be produced at the highest quality levels.
(Rock deBote is Hartford Simsack’s brother-in-law,
who hired Simsack as a family favor after he’d been
released from the state penitentiary.)
After consulting with Simsack, deBote decides to hire
four new quality inspectors, who will be responsible for
charting 10 characteristics of the Park Service’s
gates. By turning the project over to the quality department,
deBote can return to more important matters. He will, for
example, be working seriously on his putting, now that he’s
found a carpeted conference room and a sign that reads,
“Keep Out: Meeting in Progress” to hang on the
closed door.
Left to his own devices, Simsack experiences a moment
of panic. “Let’s see: 10 characteristics for
thousands of gates.” Stumped by the project’s
sheer mathematics, he decides to brush up on X-bar and R
charts by taking yet another statistics course from his
mentor, Dr. Stan Deviation, at the local community college.
Distracted by his preoccupation with the monumental task
that lies ahead, Simsack doesn’t pay attention to
Deviation’s lecture on the lower control limit for
the range section of a control chart. When he hears the
question, “Do you all understand why D3 is equal to
zero from a sample size of two to six?” Simsack nods
along with the rest of the class because he doesn’t
want Deviation to know that he hasn’t been paying
attention. He believes he’ll never need to know this,
anyway.
In fact, the explanation for the fact that D3 is equal
to zero (0) for a sample size of two to six is one of the
following:
a) A small sample size will lead to higher R values.
b) As all Black Belts understand, the standard error is
equal to the standard deviation of the population, divided
by the square root of the same size.

c) Unless at least seven people show up for your next dinner
party, nothing (0) will be served.
d) A sample size of seven or more will generate a distribution
of range values that looks normal.
(Answer to “Averting 100-Percent Inspection”
)
The correct answer is d.
Intuitively, this is logical because with a sample size
of two, the probability of having a range of zero is high,
but with a sample size of three, the probability decreases.
As the sample size increases, the probability of a range
equal to zero continues to decrease. Thus, with a small
sample size, the distribution of range values will be skewed
to the right.
As the sample size increases, the chance of getting zero
decreases and the probability of getting both very small
and very large values in the same sample increases, making
the range values larger and more consistent.
With a small sample size (i.e., n less than seven), there
will always be an upper control limit for R, but the lower
control limit will be zero.
Increasing the sample size will make the distribution
of R’s approach a normal distribution.
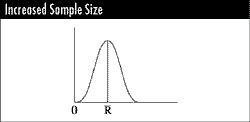
Thus, the range section will have a lower control limit
that’s greater than zero.
Michael J. Cleary, Ph.D. is a professor emeritus at Wright
State University and founder of PQ Systems Inc. He has published
articles on quality management and statistical process control
in a variety of academic and professional journals. Letters
to the editor regarding this column can be e-mailed to letters@qualitydigest.com.
|