by Douglas S. Kindred, Ph.D.
When it comes to defects, out of sight can be out of mind. Many industries--including aerospace and automotive manufacturing--machine, weld, and cast parts with complex internal structures and surfaces that aren't visible to the naked eye. The parts are often vital to performance and safety. Borescopes are optical instruments that give you the inside view. They are first cousins to the medical endoscopes now used widely to view inside the human body for minimally invasive surgical or diagnostic procedures. Surgeons work while watching video images from an endoscope inserted in the patient's abdomen or knee, just as inspectors examine cross holes in a machined part for burrs caused by drilling or cutting. Borescopes frequently form the front end of complete inspection systems, with powerful light sources, digital and video cameras, and laptop computers to store, print and e-mail images.
Advances in the optics and illumination of modern borescopes give bright, clear, crisp images that allow definitive decisions. Every borescope has an objective lens to form an image of the subject, relay optics to carry the image from end to end and an eyepiece lens to magnify the image for the viewer. Relay optics are most important to borescope image quality. Rigid borescopes use one of three technologies to relay images:
• Achromatic doublets, which are cost effective in large-diameter borescopes.
• Hopkins design relays, which give excellent quality for medium diameters but require precise grinding, polishing and centering of many tiny lenses and optical glass rods. (See figure 1.)
• Gradient index lenses, which afford the best combination of quality and price for medium and small-diameter borescopes, because the relay optics are simple, chemically treated glass rods. One gradient index rod, for example, can replace 24 optical elements in a Hopkins design scope. (See figure 1.)
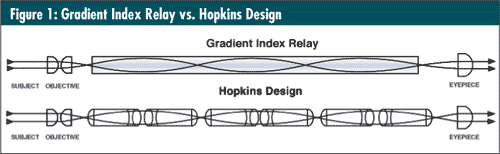
In choosing a borescope, start by considering access to the area to be inspected. If the path is straight, use a rigid borescope; if it's indirect or curved, choose a flexible borescope, which uses flexible optical glass fibers to relay the image. Videoscopes offer similar flexibility but house a very small CCD camera chip near the tip of the scope and relay the image electronically to a monitor rather than an eyepiece.
Both rigid and flexible borescopes use optical glass fibers, in a separate illumination channel, to bring light to the subject. A lightpost at the eyepiece end provides a standard plug-and-play interface for a wide variety of possible light sources, ranging from compact, battery-powered lights to powerful, line-powered metal halide arc lights.
For the best results, use the largest borescope that will fit the hole. Larger borescopes are sturdier and give brighter, sharper images. More illumination fibers carry more light, and the larger imaging optics also transmit more light and give crisper, better-quality images.
Direction of view is the next decision in buying a borescope. The most common direction is straight ahead (i.e., 0° to the borescope axis). Some rigid borescopes come with mirror tubes that slide over the borescope tube, placing a 45° mirror at the end of the scope to give a view perpendicular (90°) to the scope axis. This makes them essentially two borescopes in one.
Control of the direction of view is the most important issue, after diameter, when choosing a flexible borescope. The simplest flexible borescopes have a gooseneck sheath that allows you to set the shape before insertion. More expensive flexible borescopes have articulated tips, allowing you to control the direction of the tip back and forth in a single plane (two-way) or in two perpendicular planes (four-way), using levers on the borescope body. You can use the articulation to steer the scope to its destination, then look around. Flexible borescopes allow the inspection of complex castings like engine blocks and turbochargers, tubes, pipes and turbine engines. The best flexible borescopes relay images through bundles of up to 25,000 optical glass fibers. The fibers are acid-leached to separate each fiber from its neighbors, reducing crosstalk between them and increasing contrast for whiter whites and blacker blacks. An impermeable plastic sheath prevents entry of fluids, such as fuel or oil. A tough, durable, woven tungsten wire sheath that reduces friction and protects the scope from damage by burrs and sharp edges surrounds and protects the plastic sheath.
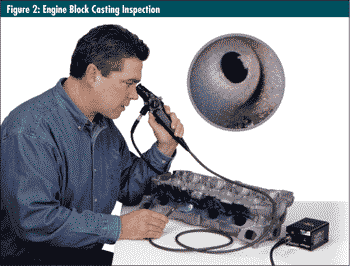
Foundries that cast automotive engine blocks, turbochargers and exhaust manifolds find it very difficult to check for residual sand, blockages, flash or voids because the castings often have complex, inaccessible cavities and winding pathways. They use flexible borescopes that range in diameter from 0.100 in. (2.5 mm) up to 0.5 in. (12 mm). By controlling the articulated tip, they steer the borescope as it snakes through the part.
Hartzell Propeller, of Piqua, Ohio, has been manufacturing airplane propellers since 1917, when Orville Wright encouraged young Robert Hartzell to make propellers at his father's sawmill. Today, Hartzell makes more than 300 different two- to six-blade propellers for everything from piston engines to large turboprops. The company even makes propellers for the Goodyear blimps. On airplane takeoff, propeller tips approach the speed of sound. Centrifugal forces of up to 20 tons try to pull each blade out of the hub. They must twist and flex, absorbing both the punishing vibrations of the engine's power pulses and the oncoming air stream. It is imperative that propellers are balanced.
Each metal blade has a small-diameter axial bore of varying length to contain static balance weights. Hartzell "shot peens" the interior of this bore by spraying it with metal beads at high velocity, creating a compressive surface layer that improves fatigue strength. Hartzell then examines this bore with a 12 in. borescope, a 90° mirror tube and a video camera. A metal halide arc light provides intense illumination. The operator compares the part to an inspection standard, using an LCD display, to ensure that each bore receives proper coverage.
Some rigid borescopes have prisms built into their working ends. Prisms allow alternate directions of view, such as 30°, 70° and 90°, like a mirror tube. Because illumination and imaging are completely independent, prism borescopes are particularly well suited for maximum image clarity and contrast in inspecting large, dark cavities such as those found in diesel cylinders or tanks. Prism borescopes also give "right reading" images, making them easier and more intuitive to control. The prism can even pivot, in the aptly named swing prism borescopes, allowing the user to change the direction of view.

A major defense contractor makes transmissions for armored vehicles. Machinists use gun drills to drill 16 in. long, 5/16 in. diameter holes in the aluminum housing for hydraulic fluid circulation. When a drill crosses an existing hole, it often forms a burr. Burrs can restrict or even block fluid flow or break loose and move to another part of the system, causing damage there. The company uses 0.157 in. (4.0 mm) diameter, 17 in. long borescopes with a prism to obtain a 90° direction of view. Video cameras attached to the scopes give clear, definitive views of the cross-holes on an LCD video monitor so inspectors spot burrs every time. Aluminum is highly reflective but the prism design minimizes glare, despite the use of the intense metal halide arc light. The company's technicians have found that plastic bushings on the tube help center it in the hole, providing consistent, focused images.
Tell Tool Inc., of Westfield, Massachusetts, is a world-class manufacturer of precision machining for components in the aerospace industry, including fuel-control housings for helicopters, and military and commercial aircraft. Tell Tool drills more than 500 holes in the large, complex fuel-control housing, all of which cross other holes. Many holes are as small as 0.10 in. and may be 4 in., 6 in. or even 9 in. deep. Burrs can form where the holes intersect, and it's critical to remove every one of them before assembly. Even a single loose burr could potentially shut down the engine, with disastrous consequences.
Five Tell Tool technicians take three to four days to deburr 30 units by hand. Using 0.095 in. (2.4 mm) diameter precision borescopes, they examine every hole in every part. The video system provides comfortable viewing of highly magnified images from some borescopes, using the metal halide arc light for illumination. The technicians also use the borescopes for direct viewing, using a compact, portable light. After inspection, the technicians ultrasonically wash the part, flush it, dry it and then inspect it again. There is zero tolerance for burrs in this critical application.
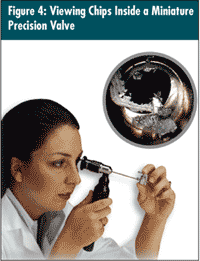
Andrew Feist, an officer of the police department in Albuquerque, New Mexico, was shooting an urban rifle qualification with his LAR-15 rifle when a serious malfunction occurred. Feist, who is left-handed, was lucky to escape injury as hot gases blew out of the ejection port toward his face at high pressure and velocity.
Feist took the rifle to Michael Haag, a forensic scientist and firearm and tool mark examiner at the department's crime lab. Haag used a 0.165 in. (4.2 mm), 17 in. borescope to examine the casing while it was still in place. Excessive pressure during extraction had caused the casing brass and primer to give way in the extractor area, where it was least supported. Inserted from the muzzle end, the borescope and 0.188 in. (4.8 mm) diameter, 90° mirror tube allowed Haag to see that the mouth of the casing had moved rearward slightly and begun to extract. This viewpoint and the critical information it showed, especially prior to movement of the bolt, could only be achieved with the 90° mirror tube. Looking straight ahead (0°) into the casing showed that brass had melted and molded to the breech face. Taking the path of least resistance, escaping gases blew out the receiver, dust cover and magazine, bent the extractor outward and even split the bolt carrier.
The Albuquerque police department was understandably concerned that there might have been a flaw in the ubiquitous and highly reliable LAR-15. Haag was quickly able to show that the problem originated in the casing. The ammunition company took full responsibility, replacing the weapon as well as the ammunition.
Modern borescopes give clear, unambiguous images that enable you to make confident quality decisions. By using borescopes with video or digital cameras, an image can be comfortably viewed at high magnification, shared with others and stored. Borescopes are powerful, and indeed essential, in many quality assurance procedures, yet are simple and intuitive to apply.
Douglas S. Kindred, Ph.D., is president of Gradient Lens Corp., manufacturer of the market-leading H awkeye precision borescope. He developed the patented endoGrins gradient index lens technology used in the Hawkeye borescope, as well as endoscopes for medical and veterinary applications. Kindred graduated summa cum laude with a bachelor's degree in physics and mathematics from East Tennessee State University. He was a naval research fellow at the University of Rochester's Institute of Optics, graduating with a Ph.D. in optical engineering in 1991.
|