by Judy Delude
During the last half of the 20th century, the global economy grew to the point where it required consistency and compatibility between management systems. As a result, the ISO 9001 standard began to gain international acceptance in the manufacturing world. Buzzwords such as "total quality management," "total productive maintenance," "quality circles," "zero defects," "just-in-time," and "lean manufacturing" shifted organizations’ focuses away from inspecting quality into products and toward developing processes that would ensure quality.
In recent years, many of the world’s businesses have focused on preserving and improving the environment while continuing to develop new technologies. Like many organizations today, yours might be facing the challenges of meeting these concerns while expanding your international market presence. As an example, the decisions you make on managing hazardous substances in the workplace could affect the future success of your business. These decisions may be in response to industry demands, legislation, or customer requirements, or they may have become important because they’re the right things to do.
Whether you sell your products locally or internationally, meeting your customers’ demands for cleaner, more environmentally friendly products, as well as the many regulatory and statutory requirements, is no longer optional. The new hazardous-substance-free (HSF) requirements affect not only where you can sell your products, but also how you package them and identify the components. As with the quality management initiatives of the last century, taking a holistic approach to implementing a comprehensive hazardous substance process management (HSPM) system is the most effective way to meet HSF requirements. However, the time and cost required to implement a standalone HSPM system can be difficult to justify.
Understanding the effect of noncompliance will determine your return on investment. Noncompliance with the new HSF requirements may result in big fines, as much as 15 million euros and, in Ireland, up to 10 years imprisonment. In the People’s Republic of China, you could face the removal of your products from the market by the Ministry of Information Industry. Even if none of these drastic measures occur, your organization’s growth could still be limited, and your market share could dwindle because unmet regulations prevent you from shipping your product to Europe or China.
As more companies establish their own HSPM policies for their supply chains, a strong business case can be made for implementing an internationally recognized HSPM system that complies with the International Electrotechnical Commission’s QC 080000 IECQ HSPM certification system. Implementing such a system allows you to leverage the existing quality management system infrastructure that you’ve established through the ISO 9001 (or equivalent) registration process.
In May 2006, the European Union issued an enforcement guideline on how the restrictions of hazardous substances (RoHS) directive should be implemented and would be enforced. Although it discussed product testing, the guideline emphasized the compliance assurance system -- in other words, process control. In much the same way that manufacturers during the 1980s couldn’t "inspect quality in," today, we can’t "test hazardous substances out."
Based on the need to meet the technical aspects associated with reducing hazardous substances in electrical and electronic products and related materials, an accredited certification program was developed by the International Electrotechnical Commission Quality Assessments System. The QC 080000 certification program is a structured approach to managing hazardous substances. It is an international specification to which organizations can register to demonstrate, through objective verification of their manufacturing systems, control of hazardous substances and HSF process-management activities. This allows organizations to manage, minimize, or eliminate their hazardous substances. QC 080000 certification is a technical management system that’s implemented along with an established and maintained QMS such as ISO 9001, ISO 13485, or TL 9000.
QC 080000 assessment provides an internationally recognized certificate to indicate that an organization has demonstrated that its control of the hazardous substances used in its products and processes are compliant with international statutory and regulatory requirements, as well as any specific customer requirements as identified in its purchase orders.
The IEC supplies the global market with multilateral standards and conformity assessment programs that are key to international trade in the electrical and electronics fields. The International Electrotechnical Commission Quality Assessment System for Electronic Components is the IEC’s conformity-assessment and product-certification program focused on the quality assessment of electronic components and associated processes and materials.
IECQ conformity assessments are global in concept and practice. They can reduce trade barriers caused by different certification criteria in various countries. By helping to remove significant delays and costs of multiple testing and approvals, IECQ conformity assessments enable industry to reach the market with greater speed and less expense.
QC 080000 is an internationally approved technical specification intended for certification by third-party assessors. As with many industry-specific standards or specifications, QC 080000 assumes a compliant ISO 9001 QMS has been established, and then provides the necessary additional requirements to establish a compliant HSPM system. The most significant differences between ISO 9001 and QC 080000 are in the following areas:
• Policy
• Design
• Supply chain, or bill of material (BOM)
• Process validation
• Traceability
An assessment verifies that a company’s processes to manage, minimize, or eliminate hazardous substances meet the highest standards. The assessment includes, as applicable, RoHS; the Waste Electrical and Electronic Equipment directive; California’s state bill 50 (SB 50); Green Process; registration, evaluation, authorization, and restriction of chemicals (REACH); and QMS principles.
Incorporating QC 080000 into an existing QMS will help establish a compliant system to reduce the risk of rejected product or penalties from customers and governmental bodies. It also will establish the means to control suppliers, reduce testing requirements, provide a competitive advantage, and, perhaps most important, reduce customer audits.
An organization can easily incorporate the elements for RoHS, WEEE, SB 50, Green Process, or REACH into its HSPM compliance-assurance system. Following are some examples of what you must address to ensure that your system will comply with European and Chinese RoHS directives:
• Policy. Understand the effect of legislative and/or regulatory requirements established in the jurisdictions in which your organization wants to manufacture or sell its products, for example, the RoHS-restricted substances for the electronic industry in Europe.
Establish corporate policies and objectives to meet the customer and market demands. It’s important for a company to understand what requirements pertain to it and to establish a policy that ensures compliance in a way that demonstrates due diligence. Establishing a certified QC 080000 system provides a flexible and adaptable framework for the future as more substances are designated as hazardous and more laws and regulations emerge globally. Having the flexible and scaleable framework for QC 080000 in place allows organizations to respond to ever-changing legislation and requirements, which in turn will reduce the cost of compliance over time.
• Design. For organizations that design original equipment, establishing a process that addresses HSPM at the design stage is critical. At the design stage, every part of the product, from your BOM and component selection to your build-to-print documentation for external suppliers, must be validated and documented. The safest evidence from a supplier is its material declaration sheet.
• Supply chain. Identify the hazardous substances that must be managed. This includes all hazardous substances in use in your organization as well as the hazardous substances supplied to you as part of the BOM in your final product. You’re responsible for your entire supply chain. Every piece of raw material is subject to analysis, as well as any process reagents that could leave detectable trace amounts above allowable limits. You must be able to produce evidence of material compliance either by maintaining a database independently or requiring evidence as part of the procurement process. The organization must ensure that procured product conforms to HSPM requirements and that supply-chain assessments are performed.
• Process validation. Implement the system through appropriate processes and procedures that are developed and documented to meet QC 080000 requirements. The system must be supported by appropriate resources, which means that all personnel must be trained and requirements communicated to suppliers and subcontractors. Management also must periodically conduct internal assessments to determine if the HSF processes conform to the requirements of the standard and to customer specifications, are effectively implemented, and if the HSPM system ensures continued compliance and improvement.
• Traceability. A manufacturer must establish traceability for its final product and have a process for producing records to identify where product has shipped to, should a nonconformity be discovered or reported.
Manufacturers that design and manufacture both compliant and noncompliant (or exempt) products can implement a compliance-assurance system to QC 080000 to manage both conforming and nonconforming products. The following considerations apply to nonconforming product:
• The organization must ensure that products not conforming to HSF requirements are identified and controlled to prevent their unintended use or delivery.
• The organization must deal with nonconforming product in one or more of the following ways:
-- There shall be a clear procedure to handle situations when nonconforming products that contain restricted substances are detected, and to prevent products that contain restricted substances from being shipped unless otherwise allowed.
-- Records of the nature of nonconformities and subsequent actions taken shall be maintained and clearly identified as to what restricted substance was detected.
-- When nonconforming HSF product is detected after delivery or use has started, the organization shall take action to notify customers according to contract agreements or the company’s process-management policy.
Seeking an independent verification and/or certification of the compliance of an implemented system is an established and economic approach to demonstrating to customers and potential customers that the company can meet requirements. A strategic approach to incorporating QC 080000 will establish a compliant system that can reduce the risk of rejected product or penalties from customers, countries, and numerous states. It will also help to control suppliers, reduce testing requirements, and provide a competitive advantage.
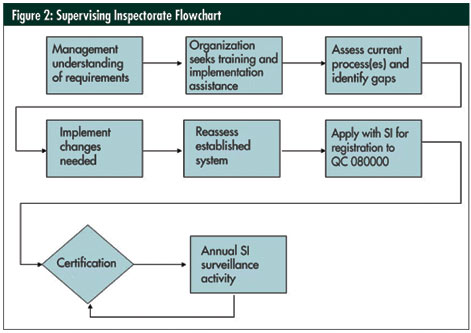
All of this adds up to the need for a process-based solution to manage existing global hazardous-substance restrictions. QC 080000 is that solution. The initial steps for an organization begin with senior management’s awareness of the applicable laws and how the QC 080000 specification can address these requirements. The steps to certification are outlined in figure 2, above, and must be executed by a supervising inspectorate (SI) authorized by the IECQ. For example, as the SI, a registrar such as NSAI would perform the assessments for ISO 9001 and QC 080000 simultaneously.
That said, not all registrars are approved SIs to the IECQ, so ISO 9001 and QC 080000 assessments can be done by separate third parties. Although there are obvious savings when these assessments are combined, this is the choice of the client. The IECQ has specific guidelines that outline the number of audit days allowed for the initial registration and surveillance. Much like ISO/IEC Guide 62, audit days are based on the number of employees in the organization. Audit days for the initial assessment range from one and one-half days for an organization with up to 50 employees, to up to seven assessment days for organizations with up to 4,000 employees. Once an organization has obtained certification, an annual surveillance assessment that ranges from one to five audit days is required to maintain compliance. Unlike with ISO 9001, organizations aren’t currently required to seek a three-year reassessment for QC 080000.
In summary, RoHS, WEEE, REACH, SB 50, Green Process, etc., are not passing fads in manufacturing. Increased demand of global environmental legislations and customer-driven requirements have created the need for a solid foundation in which to manage hazardous materials and processes. QC 080000 was developed to provide a structured approach to address the complex requirements for HSPM and can help your organization establish a customized compliance-assurance system that is certified to an international standard.
Judy Delude is a marketing specialist with the National Standards Authority of Ireland, based in Nashua, New Hampshire. NSAI is a leading global certification authority and a supervising inspectorate with the IECQ. NSAI also provides assessment and certification services to QC 080000. Delude has held a variety of engineering and marketing positions in leading high-tech electronics and software companies for more than 20 years. For more information visit online at www.nsaiinc.com.
|