Mapping for Business Improvement
In last month’s column, "Applying Six Sigma to Leadership," I described the leadership process at the highest level, the L1 level. I mentioned that the "improve" phase of leadership requires mapping core processes to an actionable level, one where the process excellence leadership team (PELT) can identify the critical-to-quality drivers in the process. In this column I’ll describe an approach for actually doing this that’s known as "L-mapping." L-maps are simple process maps used to obtain an understanding of key business processes at a high level.
The traditional way that businesses are organized is by a functional hierarchy. Tasks are divided among specialists who have, more or less, monopolies on certain sets of activities. Within a given function, decision-making authority is delegated from a single person at the top downward to subordinates. In larger organizations this functional or hierarchical arrangement may exist in several different business units, each focusing on a particular market. This view of the business is often called a "silo" structure because a chart depicting the hierarchy resembles a grain silo seen in farm country.
Despite the tremendous success of the silo organizational form, it’s not without problems. A common one is that customer value isn’t created within any given silo. Instead, value streams flow across several silos, drawing a bit of value from each. These are called "core processes" in process-excellence work. In a traditional organization, core processes aren’t managed, per se. In other words, they’re not specifically designed; key process outcomes and indicators aren’t defined or measured, and no one is held accountable for process performance. As you might guess, this results in inconsistent performance at best, and it sometimes leads to disastrous results.
Let’s look at an example of how L-maps can help remedy this situation. Figure 1 shows an L1-map for a software company. Despite its simplicity, such a map requires a considerable amount of discussion and thinking on the part of the senior leadership team. Because it’s from the process perspective and is an entirely new way of looking at their organization, functional leaders are often puzzled and confused by it and require training to understand it.
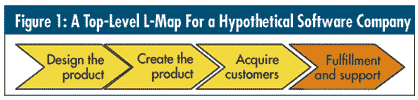
Organizations that take process excellence seriously will identify owners for each process on the L1-map. Although the process owners’ duties and authority vary from one organization to the next, there are some common features. Process owners are responsible for defining their process in detail, establishing performance measures, and working with functional managers to achieve process excellence. This can be accomplished utilizing fulfillment and support L-maps, as seen in figure 2.
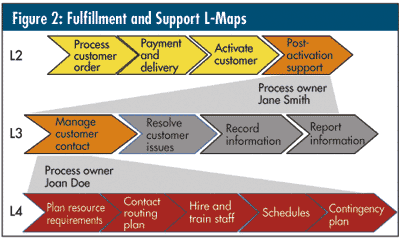
At some level the L-mapped process will become "actionable." This simply means that at this level a process owner will be able to determine how to improve the process. Improvement might involve Six Sigma projects or some other method of improvement, such as a traditional project, continuous improvement, or local work-group activities. For Joan Doe, her process map provided the guidance she needed to identify her process- improvement strategies.
Note that figures 1 and 2 drill down only along a single path for each level. The entire set of L-maps that define all of the top-level processes can be quite large at the L4 level. Consequently, a company’s top leaders will need to develop reporting systems that focus their attention on the vital improvement projects and activities that deploy their strategies and implement their goals.
Don’t let the simplicity of L-maps fool you. This tool provides an anchor that employees and team members can use to determine how their work affects the company’s performance. Creating L-maps helps the entire management team develop a shared vision of what the organization really is. It links projects and local plans to higher-level goals and results. Once you’ve incorporated this simple tool into your routine, you’ll wonder how you got along without it.
Thomas Pyzdek, author of The Six Sigma Handbook (McGraw-Hill, 2003), provides consulting and training to clients worldwide. He holds more than 50 copyrights and has written hundreds of papers on process improvement. Visit him at www.pyzdek.com .
|