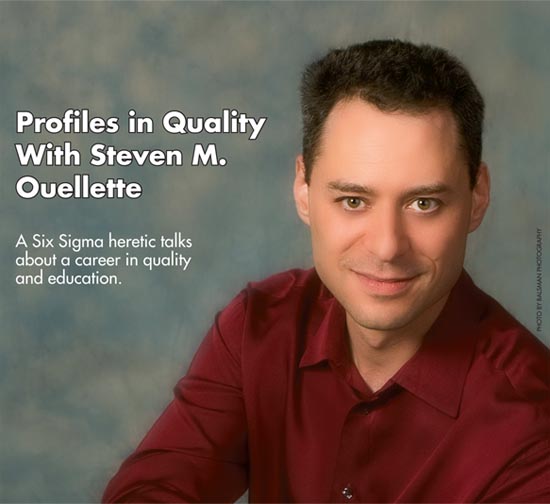
by Carey Wilson
Steven Ouellette earned his undergraduate degree in metallurgical and materials science engineering at the Colorado School of Mines, and a master’s degree in engineering management from the University of Colorado. As a Thomas J. Watson Fellow in 1991, he studied for a year in Western Europe. While working at Alcoa, he achieved the rank of senior metallurgical engineer and was trained in the quality sciences by Luftig & Warren International (LWI). Eventually, Ouellette joined LWI and worked there for six years in a variety of industries, during which time he became principal in developing LWI’s materials for teaching Six Sigma. He has been an ASQ-certified Quality Engineer and Certified Quality Auditor. He received a Black Belt from Motorola University and a Master Black Belt from LWI. He is the director of the Center for Business Performance Improvement (CBPI), which was created in 2007 through the Engineering Management Program (EMP) at the University of Colorado, and also acts as an advisory board member to Orion Registrar. Ouellette writes a monthly column titled “The Six Sigma Heretic” for Quality Digest ’s monthly e-newsletter, Inside Six Sigma . Ouellette lives in Colorado with his wife and two daughters.
Quality Digest : When you began your university studies in metallurgical and materials science at the Colorado School of Mines, were you already planning on becoming a quality engineer?
Steven Ouellette: Not at all--in fact, I went into a presentation about business performance excellence actively hostile to the idea. I thought, “Hey, I’m an engineer--give me a process and a product, and I will make them work. Don’t talk to me about that statistics or business stuff; I don’t want to know.” What I learned was that every decision I made about the processes or products that I was responsible for were marketing and sales decisions, but I was making them without any knowledge of the business requirements and with no understanding of the concept of variation. I left that presentation with the knowledge that I was ignorant--but I was willing to learn.
QD : The Thomas J. Watson Fellowship that you received in 1991 allows exceptional students to design their own curriculum and study overseas for a year with a degree of financial security; how did you decide on a destination and course of study?
SO: My topic for the fellowship was, “The Evolution, Fabrication, and Social Impact of the European Sword.” Ever since hearing an archaeological metallurgist describe his investigations of ancient metal smelting and sword making, I had been fascinated with the topic. The hard part was choosing between studying in Japan or in Europe. I only had one year, though, and it seemed likely to me that I would be able to communicate and learn more in Europe than I would in Japan.
QD : What experiences gained in that year influenced the course of your career?
SO: There were two fundamental effects of the fellowship. The first was to realize that everywhere I went, I wanted to show things to my best friend, so I proposed to her while I was still living in Europe! We’ve been married now for 14 years, and without her help I wouldn’t have taken the chance to switch from the relatively safe world of being an engineer to the much less certain (but ultimately more rewarding, for me) world of being an external consultant. Second, while traveling through most of Western Europe, I met many people who were from backgrounds that were quite different from mine, and I found myself in some unaccustomed situations. This helped me learn how to put things in perspective and to recognize that, shocking as it may seem, reality does not always conform to my notions. In fact, this is part of the reason that I end most of my “Six Sigma Heretic” articles the way I do--by saying, “But I could be wrong.”
QD : You were trained in the quality sciences by Luftig & Warren International, and eventually went to work for that company and helped it develop its Six Sigma training materials. When did you become aware of Six Sigma, and what drew you to it as an area in which you wanted to develop expertise?
SO : LWI was at Motorola when Six Sigma was being born, so they were always peripherally aware of it. I began to get inquires from clients as to whether we could do this “Six Sigma stuff” in the late 1990s. I looked into what that “stuff” was and found out that we had been doing it since 1985, and even before that, if you count Jeffrey T. Luftig’s work with W. Edwards Deming in the early 1980s. Unlike many newcomers to the field, our Six Sigma development consisted of just repackaging a number of courses that LWI had been teaching for ages, adding some business context and fitting them into the “traditional” four-week training for Black Belts. That is why I am a “heretic” about Six Sigma--as an engineer, I look at all these tools and ask myself, “What is the best tool to help me get the job done?” and “What do I need to know about this to avoid making a mistake and looking like an idiot?” Because our training existed before Six Sigma, I sometimes find that my answers differ from Six Sigma orthodoxy.
QD : You are currently the director of the University of Colorado’s Center for Business Performance Improvement (www.csscu.com ). How did your relationship with the university develop?
SO : My mentor, Jeffrey T. Luftig, Ph.D., retired from LWI in 1998 and went back to academia. His primary criteria were a top-tier university and a place where he could ride his motorcycles year-round, so he chose the University of Colorado. His classes about the quality sciences at the Leeds School of Business were so popular that he contacted me to teach some sections. In 2005, he moved into the Lockheed-Martin Engineering Management Program as the W. Edwards Deming Professor of Management and began agitating for me to join the faculty there. He had this crazy idea to start a center through Engineering Management that would link up graduate students and businesses to implement the tools and strategies we had used so successfully for our clients at LWI. I ended up getting a master’s degree in the program, joining the faculty, and was asked to lead the creation and development of the center.
QD : How did you come up with the idea for the CBPI web site?
SO : What I wanted was a site that integrated some design elements from the EMP and University of Colorado web sites, so that our ties with both would be visually clear. At the same time, I wanted a web site that would be really easy to build and maintain--I didn’t want to spend a lot of time messing with code or trying to explain to someone what I wanted. I ended up choosing an open-source content management system called “Joomla!” that lets me concentrate on getting the content in while the computer figures out how to make it compatible with different browsers.
QD : What are the goals of the site?
SO: Primarily, I want to get the word out about the benefits that our center can bring to businesses and students while providing some useful information to people working to improve their businesses’ profitability through the use of data.
QD : Who will benefit from visiting the site?
SO : I’m hoping that a number of people will benefit from the information I have there. Someone looking to increase the profitability of his or her business will find articles describing some tools to do that and learn more about how the center can help. Another person might be looking for on-site basic and advanced training in the quality tools. Finally, students considering joining the EMP, or who are currently enrolled, will find ways in which they can leverage their degree into very valuable work experience.
QD : Are visitors to the site able to give as well as take information about their quality improvement processes?
SO: We have plans in the future for a discussion board that would become a “go to” site for discussions in our areas of expertise, but we are holding off implementing that until next year. Visitors can submit “ask the expert” questions, which should be a lot of fun.
QD : CBPI offers formal training (and, through the “ask the expert” function of the site, practical advice) in statistical process control, business performance excellence (BPE), and data analysis; what areas of interest have attracted the most attention?
SO: Most people who contact us are interested in the BPE implementation, and for good reason. This is a structured approach to deploy the strategic plan to the entire company. In our experience, throwing a bunch of highly trained Black Belts at problems without this system means that a) you fix a lot of problems that b) have nothing to do with the direction of the company, and c) are never reflected in the bottom line, resulting in d) a lot of wasted time, money, and effort, and the failure of Six Sigma. Further, the things that might maximize the profit of a company might very well have nothing to do with reducing the costs of poor quality (what a Black Belt works on). These are the things that come out during a BPE implementation.
QD : With CBPI being part of the EMP at the University of Colorado, what is the role of student participation in its programs?
SO : This really is one of the differentiating things about our center. Some of our EMP graduate students are on a track to achieve Green, Black, or Master Black Belt certification through the center but are looking for class projects. The center hooks them up with a company in need of their expertise. The company gets a technical resource to capture the savings, and the student gets to use the advanced tools in a real situation--everyone wins. Of course, some projects are too critical or complex to give to a student, or the timing doesn’t fit in with the academic schedule, and that is why the center offers on-demand professional-level services as well.
QD : Can you give an example of how educational opportunities for students can lead or have led to mutually beneficial community and business improvement projects?
SO : We have a very exciting project right now with the city of Golden, Colorado. Recently, their city council passed a resolution that will improve the sustainable practices of local government as well as the citizens, resulting in cost savings due to a decrease in energy consumption. As is normal with efforts like this, there are lots of ideas, but the trick is in prioritizing and aligning the organization to achieve those goals. Our students have been trained in the BPE process and are contributing both that knowledge and, in some cases, their analytical abilities to help Golden achieve its objectives. The city manager, Mike Bestor, is a big believer in Deming, and our BPE process is a descendent of Deming’s philosophy. With our help, the department heads will be able to choose metrics for their areas to achieve as well as the projects that will best achieve them. Bestor’s stated intention is to make “meaningful, measureable improvement, not just a bunch of activity with no results,” and that is an area in which we are perfectly positioned to help.
QD : What do you see as the future of Six Sigma training in the educational system?
SO : I dropped my crystal ball the other day so I’ll have to guess, but I think we’re seeing two trends in Six Sigma. First is the commodification of training--everybody and their dog is hanging a shingle up saying that they “do” Six Sigma. Going hand-in-hand with this is a horrifying variability in the training that people are receiving. So I think that there will be a strong driving force to push this type of education back to institutions of higher education. However, there is a real risk in this if the training ends up coming out of math or psychology departments. The types of problems that businesses encounter, and thus the most efficient tools to deal with them, are entirely different than what is taught out of these departments. In my opinion, Six Sigma training needs to be strongly anchored by business experience and technical depth. Look to see Six Sigma ending up in business-savvy engineering schools or data-driven business schools.
QD : How has, or how should , business/quality education evolve to meet the globalized economy?
SO: I really think that Deming’s and Juran’s idea about quality being defined as the reduction of variability around customer-defined targets is very important for people in business to understand. In addition I think that what the Japanese call hoshin, or deploying the company’s strategic intents, will be the differentiating characteristic of globally successful companies. In my experience, most people in business do not have a good understanding of either concept, and those who do are desperately needed by companies that want to successfully compete in the global market.
QD : What are you currently most excited about in the future of the center?
SO : That is a tough one--we have a process that greatly improves a company’s profitability by aligning metrics and objectives, and that’s tough to beat. But I have to admit that I am most looking forward to offering a working seminar with Luftig on “Ethical Decision Making in Business.” That topic is so timely and important, and Luftig is such a gifted speaker, that we could really have a fundamental effect on how people think about ethics.
Carey Wilson is Quality Digest’s news editor.
|