gageguide
by Drew Koppelmann
Microinch Measurement
Gaging microinch production tolerances is
not for the shop floor-it requires extraordinary
attention to detail.
The trend toward tighter and tighter manufacturing tolerances is unstoppable.
Some manufacturing engineers and quality control managers are finding, to
their dismay, that design engineers are now calling for tolerances in the
range of 20p;50 microinches (i.e., millionths of an inch, or µ).
While such high levels of precision do, in fact, improve the functionality
of some designs, they present a real challenge to inspection. Here's why:
All of the components in a gaging setup-the gage itself, the master and
the workpiece-are subject to thermal influences. One inch of steel will
expand by 6 microinches for every 1° F increase in temperature. If
the workpiece is at a different temperature than the gage or the master,
or if temperatures vary unpredictably in the gaging environment, reliable
measurements become impossible.
Airborne dust and other contamination can also throw off measurements.
Just by sitting exposed for a few hours in a typical production environment,
as much as 0.0005" of dirt may accumulate on a gage's contacts. Furthermore,
humidity in the atmosphere can corrode metal surfaces. Even at levels invisible
to the naked eye, such corrosion will quickly impair the accuracy of gage
blocks or other standards.
Many electronic gage amplifiers boast digital displays that read to microinches;
however, display resolution may be misleading, because the mechanism may
not repeat to that level of accuracy. In other words, the same part measured
twice may generate different readings. To combat this, holding fixtures
must be rock-solid, machined to tight dimensional and geometric tolerances,
and capable of positioning the workpiece repeatedly, while gage mechanisms
must demonstrate absolutely regular response and minimal friction and lost
motion.
Gages must be more accurate than the tolerance being measured; a gage that
repeats to 50 microinches is not accurate enough to inspect part tolerances
of 50 microinches. Although gaging practice typically calls for a 10:1 ratio
between gage accuracy and part tolerance, this is rarely achievable at the
microinch level, where it may be necessary to accept ratios as low as 5:1.
The standard (a master or gage block) must, in addition, be about five times
more accurate than the gage it is used to set. Thus, to reliably inspect
parts to a 50-microinch tolerance, the gage should repeat to about 10 microinches,
and the standard should be calibrated to within 2 microinches.
Because of their sensitivity to environmental variables, microinch gages
must be mastered frequently, and standards must be calibrated frequently.
Many shops must, therefore, maintain a capability to calibrate their own
standards, to avoid the long turnaround associated with using an outside
calibration service. Calibration instruments with accuracy of 1p;2
microinches are available, but they require special care to generate reliable
results.
First, a controlled gaging environment must be established. This usually
means designing and installing a gaging lab, in which temperature can be
maintained at a steady 68° F, with variation of no more than 2°
F per hour. Humidity should be kept below 50 percent, and the room should
be isolated from sources of vibration (e.g., machine tools, HVAC systems,
automotive and forklift travel). It must also be kept free of contamination.
The entry should be an air lock, and low-lint materials should be chosen
for operators' clothing, furniture upholstery and even computer paper.
Parts should be cleaned before being brought into the lab, then staged
on a steel plate that acts as a heat sink to bring them into thermal equilibrium
with the rest of the room. Parts and masters should be handled with gloves
or insulated tweezers. A clear plastic shield may be required to deflect
the operator's body heat and breath from parts, standards and the gage itself.
There are many more specific measures to observe, but the foregoing indicates
the level of care required.
Surface finish and part geometry, or form variation, must also be considered.
Failure to account for and control minute variations in surface roughness,
flatness, waviness, etc., can negate all efforts at high-precision dimensional
control. We will look at these subjects in some detail in a later column.
Microinch production tolerances are here now, and they will continue to
infiltrate additional industries as product designs become more sophisticated
and production technology improves. Gaging these tolerances requires extraordinary
attention to detail, but with proper preparation, it can be done accurately
and reliably.
About the author
As applications manager, gaging products, at Federal Products Co. in Providence,
Rhode Island, Drew Koppelmann provides dimensional gaging applications assistance
to companies in a wide range of industries, including automotive, aerospace,
packaging and electronics. He can be reached by fax at (401) 784-3246 or
by e-mail at dkoppelmann@qualitydigest.com.
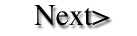