Let the System Drive Your ISO 9000 Effort
by John M. Murphy
Quality management software can help you reach
ISO 9000 certification and much more.
The pressure is on-you've been told that you have to become ISO 9000 certified
because your customers demand it, your competitors do it, and you're likely
to lose business if you don't do something about it. But what changes will
ISO 9000 demand of your business? And where do you start? More importantly,
is there a way to get something back for all the effort? Can you meet the
ISO 9000 standard and actually make money from this accomplishment? Many
manufacturers are finding that they can, by implementing software systems
that automate and integrate critical quality and business functions.
How to view ISO 9000
ISO 9000 provides a set of criteria against which to measure the management
principles and procedures employed by a company to assure quality performance.
However, unlike other quality standards, ISO 9000 is broader. In addition
to quality control and record keeping, ISO 9000 also incorporates quality
planning, contract review, design, purchasing, training and servicing.
The ISO 9000 standards don't tell you how to run your company. They only
provide a framework for evaluating what a company does or should do. For
example, a raw material producer faced with formulating a compound to meet
an automotive specification would choose a mix of ingredients to meet the
specification and allow the company to earn a reasonable profit. Meeting
the ISO 9000 standard should be approached from the same perspective.
ISO 9000 should be used as a framework against which to evaluate your present
business systems. The standards present a unique guide for managers to learn
what the marketplace is demanding and what sets of quality criteria customers
and suppliers are using. With this guide, management teams can pinpoint
the strengths, gaps and weaknesses in the existing systems and develop plans
to make improvements.
Some jump right in and start filling in the present gaps, adding manual
systems to meet specific needs or a standalone PC software package to cover
different areas of the standard. After all these gaps have been filled,
they spend countless hours documenting in detail what each component does.
The end result is a set of complex systems and procedures that are devoid
of any integration, leaving islands of operational procedures that become
difficult to manage and control. This approach fails to recognize the companywide
desire to integrate the various requirements and systems into one workable
solution that satisfies ISO 9000 and the operational business objectives
as well.
Traditional manufacturing software
Most manufacturers today use a traditional materials requirements planning
system to manage and streamline the business functions associated with inventory
control, purchasing, production scheduling and materials planning. Many
of these systems also include financial and shipping functions. These systems
can be used to satisfy ISO 9000 requirements for procedures that cover contract
review and acceptance, capacity planning and purchasing. They can also be
used to show that the customer requirements are adequately defined and that
the company can deliver what is required. In order to satisfy ISO 9000,
it would be necessary to document how this system is used every day to coordinate
these various ISO 9000 required activities.
Managers must remember that companies evaluate and purchase an MRP system
because it meets their unique requirements. Once they implement the system,
few companies would consider operating without it. These systems are justified
because they automate tasks, reduce paperwork and, more importantly, communicate
information throughout the entire company. These systems recognize that
the company has unique departments and users who each have different needs
for the information.
For example, the purchasing department needs to ensure that sufficient raw
materials are on hand to produce an order, scheduling needs to know when
the order is due, accounting needs to know the correct selling price at
which to invoice and whether credit has been extended, shipping needs to
know what truck carrier to use, etc. These systems are critical for the
tasks and processes that they control and necessary for the efficiency and
productivity of the company.
Quality management software
While an MRP system can provide some of the functions required by ISO 9000,
you must bear in mind that it is primarily a quality standard. In addition
to the administrative functions handled by MRP systems, ISO 9000 requires
many of the elements normally associated with traditional quality management
methods. For example, you must be able to:
Verify the processes used to manufacture products.
Inspect and test incoming supplies and outgoing product.
Retain necessary quality records and documentation.
Control inspection and measuring test equipment.
Document corrective actions.
Perform statistical techniques in order to verify process capability.
A quality system is strategic. And while ISO 9000 may be used as the catalyst
to implement more effective quality systems and controls, these systems
can bring enormous benefit. Today, for example, statistical process control
is used to reduce process variation and anticipate out-of-control trends
before they occur. SPC helps to analyze the relationships between key process
variables. And it contributes to a better understanding of the manufacturing
process-providing process engineers and quality personnel with the feedback
required to make effective and timely decisions.
The fact is, you have to perform various quality tasks. They may include
data collection, record keeping, SPC, Pareto analysis, receiving inspection,
gage calibration, test certificates and more. When you examine the building
blocks of an effective quality system, you are left with three components:
product specifications, process data (measurements or notes) and reports.
These components form the heart of any quality system. The functions associated
with manually maintaining the specifications, recording the data and summarizing
the information in a variety of reporting formats can be time-consuming.
Software is ideally suited to automating these tasks. It is faster, more
accurate and more cost-effective than manual systems, which are difficult
to manage and prone to mistakes.
Today, most companies would not dream of drawing a complicated part design
by hand. Rather, they employ computer-aided design software to accurately
define each component and, in many cases, transfer this information directly
to machining centers that will produce the part. The same argument applies
to your quality functions. Why record measurements manually on log sheets
that are filed and later retrieved and typed into a word processor to produce
a certificate of analysis that must accompany a shipment?
Computer automation of these tasks will save enormous amounts of time collecting
and processing data. It allows companies to automate the repetitive tasks,
electronically file records, eliminate miscalculations and typos of critical
customer paperwork, and enable people to satisfy customer requests for reports
and data. Furthermore, it should provide companywide access to the data
in real-time for process engineers, quality personnel, lab technicians,
production operators, sales personnel and others. The increased productivity
associated with software automation will produce substantial cost savings.
Companywide integrated quality systems
Like all software, the fundamental criteria for selecting and evaluating
a quality system should be, "Does it fit our business objectives?"
However, an often overlooked criteria is the level of integration that the
quality software package offers. Remember that the ISO 9000 standards require
documentation of procedures for a wide range of quality activities, including
inspection data on incoming and outgoing product, gage calibration, statistical
analysis and corrective actions. The true measure of a software product's
value is its ability to integrate the various business-required functions
into one multiuser system.
Alternatively, some companies purchase many individual and independent
standalone software packages, each representing a distinct task that was
needed. While improved system efficiency and meeting ISO 9000 requirements
may have been the goal, this approach yields islands of automation that
control individual tasks but don't tie the elements together into an integrated,
companywide system. Let's examine a fictitious company, The ABC Co., to
demonstrate the value of software functionality and integration as it relates
to quality requirements and the ISO 9000 standards.
When The ABC Co. produces a particular lot of material, various quality
audits are performed. Their integrated quality management system allows
lab or production operators to input the results of testing into the computer,
which stores the information by lot number. Some of these test parameters
are taken from lab instruments that are directly cabled into the computer,
which controls the uploading and filing of the result. The operator need
not key in these values.
When ABC's shipping department prepares to fill an order for customer XYZ,
they realize that this customer requires a pH value that is higher than
many of ABC's other customers who purchase the same product. The shipping
department uses the quality software to hook into the MRP warehouse inventory
and list the lot numbers currently held in inventory. The quality software
retrieves the quality audits for each lot and compares them to the specifications
it stores for customer XYZ. The software informs them that three lots meet
customer XYZ's requirements.
Customer XYZ also requires a certificate of analysis to be sent that documents
ABC's compliance to the specifications. This data must be specific to the
lot number to be shipped. From the quality software, ABC's shipping department
types in the lot number and the software prints a certificate of analysis
that shows the requirement for each attribute as well as the results obtained
through testing on this lot of material. It even incorporates the proper
pH value. The acceptable lot is then shipped to customer XYZ.
Whenever quality data has been entered into the system, ABC's engineers
are able to produce statistical reports that examine trends over time or
comply with customer XYZ's quarterly reporting requirement. The software
also keeps track of the number of hours the lab instrument has been in service
and will notify the operator when a gage must be calibrated. ABC can even
enter the results of incoming materials inspection into the software and
generate statistical reports on vendor performance. For traceability, they
can track which lots of vendor material go into producing the finished ABC
lot of material shipped to customer XYZ.
The true value of ABC's quality management system is that it integrates
their various quality requirements into one system. Other companies may
have different requirements. For example, a company may want to use bar
code readers for accurate and consistent data entry. The user may need to
link into their MRP system to print the customer's order number and shipping
address on the certificate of analysis. The company may want to be able
to add corrective actions or notes directly into the software and associate
them with a particular lot number or point in time.
The objective of a companywide quality system is to integrate all these
tasks-SPC, data collection, reporting, gaging, receiving inspection, etc.-into
a cohesive system, where departments and individual users can quickly access
the information they need to be effective. An integrated system streamlines
all your data processing so that duplication is eliminated and repetition
is automated. This means that data can be collected faster and more efficiently,
with less chance of error. And it automates the time spent collecting, filing,
distributing and analyzing the data. In addition, integrated systems will
decrease training and implementation time by providing common interfaces,
terminology and training tools.
A word about software validation
While nothing in the ISO 9001 standard specifically refers to software programs,
most auditors investigate the control and validation of software used to
validate process capability or verify design. The auditor will be concerned
with control of versions and revisions, master software copies, documentation
and validation. While most auditors may not expect in-house validation,
it should be noted that a software product will produce the proper results.
Some vendors may furnish a validation certificate or include a validation
statement in their manual.
If a validation report or a user manual is not available, the auditor will
issue a noncompliance. This should especially be kept in mind for in-house-developed
software. The validation report can simply list the types of tests that
were performed, the expected results and the actual results. Some companies
have found that a written certification can substitute for a validation
report if the software has been in use for some period of time prior to
ISO 9000 implementation. The certification would state that the program
had performed satisfactorily in the past and was considered proven for use.
However, this grandfathering approach will not eliminate the need for a
procedure to validate new software and future revisions to older software.
For reference, see ISO 9000-3 Part 3: Guidelines for the application of
ISO 9001 to the development, supply and maintenance of software.
Satisfied customers and
empowered workers
ISO 9000, then, can be used to accomplish strategic business objectives,
provided that it is used as a guide to improvement. The objective is to
create a quality system that fits each business, integrates companywide
operations and makes money. A specialized quality software system can help
do just that.
The benefits of implementing such a system are clear. They go beyond ISO
9000 certification and extend throughout the entire company. They come in
the form of improved worker productivity, increased process efficiency,
reduced manual errors, time saved, access to real-time information for decision
making, positive customer surveys and empowered workers.
The worker empowerment comes from the ability of employees to make a difference
in the processes they manage. An integrated quality system provides workers
with the tools to analyze, organize, understand and use large amounts of
data to make important decisions that impact the bottom line. Because the
software collects and maintains a centralized database, users always have
access to the most up-to-date information, and they can share it in real-time.
When there's a problem, they have immediate feedback so they can begin troubleshooting
on the line, before the situation goes out of control. That's the power
of information.
A business system
Business success is based on the degree to which managers know their business.
Similarly, quality starts with knowledge about the product. And this knowledge
comes from the data collected from processes. Data is a fundamental aspect
of any business. Management should build a quality system that collects
and protects that data, making it available to the organization's biggest
asset, its employees.
Look for software that best fits your needs. Use ISO 9000 as a roadmap to
guide you. Select the software that integrates the tools you need to reach
those goals. Good software will enable you to build accuracy, efficiency
and productivity into your quality system from the start. And it will have
the flexibility and features to serve your needs in the future. In the end,
you'll have an integrated, companywide quality system that not only provides
the marketing effects of ISO 9000 certification but fits your vision of
what your business should be.
About the author
John M. Murphy is vice president of sales and marketing for Murphy
Software. Since 1987, Murphy Software has helped many Fortune 500 manufacturers
implement companywide SPC and quality management software systems. These
manufacturers have used Murphy Software's integrated quality system to help
them achieve ISO 9000 certification.
© 1995 Murphy Software. All rights reserved.
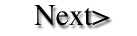