Creating Organizational Excellence--Part One
H. James Harrington
jharrington@qualitydigest.com
For the last 50 years, quality
professionals have tried to impose quality systems on businesses,
governments and academia. And our track record, hasn't been
stellar, especially when you consider that quality control,
total quality control, zero defects and total quality management
have all failed, and Six Sigma is failing.
Why is it that new quality methods inspire an initial
spurt of success before slinking into oblivion like their
predecessors? Their fate is similar to old toys that get
stuffed in a dark corner of the closet when a new toy is
found under the Christmas tree.
This exercise in futility stems from applying quality
initiatives like bandages to an organization when what's
really needed is fundamental organizational change. Treating
symptoms usually doesn't affect a cure.
Organizational excellence is designed to permanently change
a company by focusing on five important elements. Each of
these isn't new by itself, but learning to manage them together
is the key to success in the endless pursuit of quality.
In this column I'll discuss the first key element: process
management.
As a concept, process management certainly isn't new to
quality professionals; it's the basis of most improvement
methodologies. A process is a series of interconnected activities
that take input, add value to it and produce output. It's
how organizations do their day-to-day routines. Your organization's
processes define how it operates. Consider the simple process
model below.
In order to manage a process, the following must be defined
and agreed upon:
An output requirement statement between process owners and
customers
An input requirement statement between process owners and
suppliers
A process that's capable of transforming the suppliers'
input into output that meets the customers' performance
and quality requirements
Feedback measurement systems between process and customers,
and between process and suppliers
A measurement system within the process
These five key factors should be addressed when designing
a process. However, the problem facing most organizations
is that many of their support processes were never designed
in the first place. They were created in response to a need
without really understanding what a process is.
The best methodology I know to overcome this problem is
area activity analysis. AAA methodology is a simple approach
used by natural work teams to define the key processes they're
using. AAA defines:
The natural work team's mission
The natural work team's major processes
The customers for each major process and agreed-upon output
specifications
The suppliers for each major process and agreed-upon input
specifications
The internal process that converts input into output
Efficiency measurements for the process
The measurement system
Dividing these elements among the natural work teams reduces
the effort required by any one group and puts the process
understanding in the hands of those who work with it.
So, what's required to manage a process? You must:
Prevent errors. A process must be designed to make it difficult,
if not impossible, to create mistakes.
Understand the capabilities of each activity within the
process to produce acceptable output on schedule. This can
be accomplished through process capability studies.
Identify negative changes in the process so they can be
corrected before the process goes out of control. Control
charts do this well.
Ensure that new people are trained before they become involved
in the process
Detect errors resulting from activities that are incapable
of producing acceptable quality levels
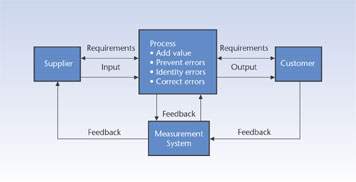
Report detected errors
Define the root cause of errors and initiate a process to
eliminate them
Obtain customer feedback that defines process errors so
that the process can be improved
Develop ongoing feedback to your suppliers about their output’s
acceptability and obtain their plan for eliminating unacceptable
input to the process
As you can see, when it comes to managing it, a process
is almost like a small business. All processes should be
designed, documented, measured and controlled. This is as
true of a chip-manufacturing process as it is of hiring
or accounts payable processes. Most of the work that quality
professionals do is related to continuously improving our
processes. Some of the tools we use include design of experiments,
process capability studies, root cause analysis, document
control, quality circles, suggestions, Six Sigma, Shewhart’s
circles, ISO 9000, just-in-time manufacturing and supplier
qualification, among many others.
Next month I’ll discuss project management, the
key to real improvement. Basically, processes are the way
we do business; projects are the way we improve our processes.
H. James Harrington has more than 45 years of experience
as a quality professional and is the author of 20 books.
Visit his Web site at www.hjharrington.com
. Letters to the editor regarding this column can be sent
to letters@qualitydigest.com.
|