by Russell T. Westcott
The U.S. Technical Advisory Group to ISO Technical
Committee 176 established a Product Support Initiative
task group as a means of obtaining feedback from users
of the ISO 9000 series standards. This initiative
provides guidance for future revisions of ISO 9001
and also factual information to assist organizations
implementing the ISO 9001:2000 and ISO 9004:2000 standards.
The PSI ISO-9004 subteam No. 6 is responsible for
establishing communication channels and products for
feedback and awareness of the ANSI/ISO/ASQ Q9004-2000.
The purpose of the committee is to ensure that standard
users and potential users are aware of the advantages
and uses of ISO 9004 and to solicit input for continual
improvement. This subcommittee consists of Jarvis
Alka, Karen Hitchcock, Sandford Liebesman, Robert
Peach, Art Ramos, Rob Ruel, J.P. Russell, Russ Westcott
and Larry Wilson.
|
As they make their transition
to ISO 9001:2000, many organizations are doing it the hard
way. They purchased the initial ISO documents, concentrated
on deciphering ISO 9001:2000 and relegated the ISO 9004
guideline to obscurity. Meanwhile, they struggle to understand
that value lies in maintaining registration.
The ISO 9004 guideline is a compendium of suggested actions
for improving the potential value of a quality management
system. ISO 9004 answers many of the questions that arise
when an organization implements an initial transition QMS,
and it offers the potential for subsequent improvements.
Solid reasons exist for establishing a value-adding QMS.
The ISO 9001:2000 series allows almost any organization,
regardless of type, size, product, industry or location,
to implement the standard. It allows organizations flexibility
in structuring, documenting, monitoring and continually
improving their QMSs. However, the fact that registering
to ISO 9001 represents the minimum requirements is frequently
unrecognized. The ISO 9000 series doesn’t focus on
maintaining a minimum-level QMS but rather on taking actions
that will continually improve the QMS. And that’s
where ISO 9004 comes into play.
ISO 9004’s strength is its ability to help companies
achieve higher levels of performance. For example, the assessment
tools in the standard’s Appendices A.1 through A.4
can help an organization determine its hot spots for improvement.
Appendix A.3 translates the guidelines into “how”
questions, the answers to which can be most revealing to
those who participate in the assessment process.
ISO 9001:2000 emphasizes management’s involvement.
To convey a continual and consistent message throughout
the organization, management must actively participate in
quality-related decisions and actions. Top management is
usually evaluated on its performance in satisfying the organization’s
stakeholders, especially the owners/investors. An effective
and efficient QMS will directly enhance profitability, cost
containment or budgeting and thus reflect favorably on top
management. This is a key selling point for moving the organization’s
QMS to a value-added system. Also key is assigning the responsibility
for maintaining and improving the QMS to the highest organizational
levels. This is no longer a job for the quality control
department. It requires a recognized and respected positional
authority to manage the QMS over the long term. Implementing
and sustaining a strategic QMS is the business of higher
management.
When an organization adopts a value-added philosophy for
evaluating its QMS’s effectiveness and efficiency,
it should also carefully monitor its resources. This means
setting measurements and monitoring results. Teaching the
entire organization how to apply simple return-on-investment
measures to all improvements will highlight the QMS’s
value-added contribution to performance. All these measured
ROIs enable management, and those who evaluate management,
to understand the importance of the QMS.
A good way to monitor ROIs is to establish a “log
of quality system improvements” as a feature of the
QMS. The LOQSI directs all improvements to a central manager,
who documents the nature of the improvement and its estimated
first-year, or partial year, ROI. A summary of these ROIs
is presented at each management review. Appropriate recognition
is directed to those who contributed to the ROIs, and all
improvements are scanned for lessons that might be implemented
elsewhere within the organization.
ISO 9004 emphasizes customer satisfaction. It focuses
on how the quality policy embraces customer needs and expectations
and how an organization can interpret their relevance. The
guideline also addresses the resources and processes that
will satisfy customer needs and expectations, and outlines
how to collect and analyze the data. Thus, the guideline
addresses factors that lead to customer retention and refer
your organization to potential customers. Consider the five
scenarios:
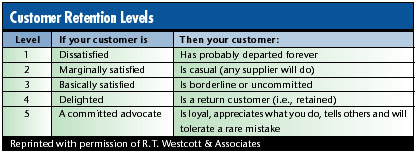
The outcome of a strategic planning process is to deploy
goals and objectives throughout the organization. Operational
(i.e., tactical) objectives and plans support actions to
achieve strategic goals. An organization closely monitors
action plans, makes informed course corrections, and measures
and analyzes the results. Inherent in a well-planned strategic
process is attention not only to the customers but also
to the marketplace.
Marketplace competition is intensifying. Use ISO 9004
for guidance in maintaining and improving your position.
Begin by assessing your organization. An effective and efficient
QMS can help:
Decrease variation in its processes
Continually improve, organize and deliver customer needs
and expectations
Do it faster and at less cost than its competitors
ISO 9004’s Appendix A.5 lists 27 benefits that might
apply to your organization. If your company is going to
stay in the game, it must continually strive to improve
the potential of ISO 9001. The smartest way to do this is
by using ISO 9004.
Should an organization first implement an ISO 9001-based
QMS or undergo the process of applying for a quality award?
Each approach has its own purpose. There are some similarities,
but look at some of the differences:
An ISO 9000-based QMS focuses entirely on establishing an
effective and efficient QMS. Quality award criteria such
as the Baldrige National Quality Program focus on the whole
organization and the environment in which it functions,
the effectiveness of its approaches (e.g., breadth and depth),
and--for a relative few--qualifying for an award.
ISO 9001:9004 concerns itself with organizational reliability
and compliance (i.e., avoiding failure), whereas the Baldrige
criteria focus on organizational excellence and strategy.
ISO 9001:9004 is more detailed and prescriptive than the
Baldrige criteria.
ISO 9001:9004 addresses eight management principles that
are also in the Baldrige criteria; however, the Baldrige
criteria add additional core values including:
- Visionary leadership
- Organizational and personal learning
- Agility
- Managing for innovation
- Creating value
The assessment process for ISO 9001 certification and subsequent
surveillance focuses on compliance with the standard, conforming
to practices documented in the QMS and finding deficiencies
that need correcting. The registrars that conduct assessments
are paid by the client. The Baldrige examination process
is more extensive and is conducted entirely by trained,
nonpaid volunteers.
The ISO 9001-registered QMS remains in effect as long as
surveillance audits indicate the system is in compliance
and working effectively--and the registrar is paid. A Baldrige
Award is basically a one-time event. Unlike the certified
QMS, the Baldrige Award has no built-in leverage to keep
the process functioning effectively.
Neither ISO 9000 nor the Baldrige criteria ensure that the
product or service is of acceptable quality or meets customer
requirements. It’s implied that if the certified QMS
or the Baldrige winner has followed its processes and approaches,
the product or service should be good.
There’s also no guarantee that ISO 9001 registration
or the Baldrige Award will ensure that an organization will
live long and prosper. Neither process addresses everything
needed for an organization to remain viable, although the
Baldrige criteria do offer more guidance in overall management.
Which should an organization attempt first? Absent any
hard and fast rule, implementing an ISO 9001-based QMS and
getting certified would appear a logical first choice for
the following reasons:
Depending on what quality measures are already in place,
a QMS could be implemented within a range of six to 18 months.
Typically, Baldrige winners take three to five years or
more to reach a winner’s qualification--and then there’s
the limitation on how many awards may be given each year.
An organization must develop and follow its QMS according
to ISO 9001’s documentation. It also instills the
quality policy, principles and continual improvement practices
among employees. It institutes organization and standardization.
It firmly inculcates management in the need for data-based
decision making and measurable results. And it helps employees
to be aware of customers’ needs and the organization’s
desired outcomes.
ISO 9001-based and ISO 9004-enhanced QMSs create a solid
foundation upon which building toward the Baldrige criteria
is less threatening and potentially less costly.
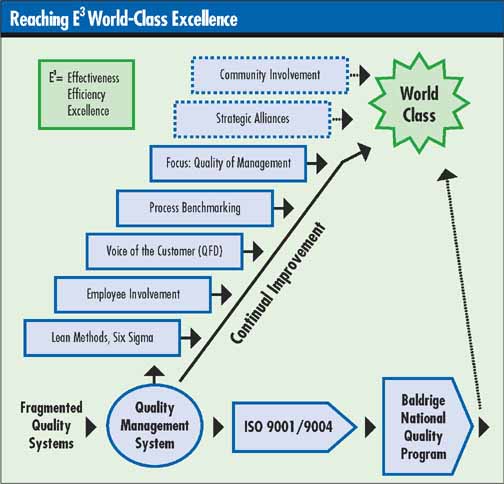
A value-adding QMS is a necessity for survival for all
types of organizations. The most efficient way of establishing
one is by using the guidelines outlined in ISO 9004. Companies
should build an ISO 9001-based QMS and then expand to broader
Baldrige-type criteria to achieve E3 status (as illustrated
above):
ISO 9001 for effectiveness
ISO 9001:9004 for efficiency
ISO 9001:9004 plus applicable Baldrige criteria for excellence
Russell T. Westcott is president of R.T. Westcott
& Associates, a consulting firm that assists clients
with strategic planning, QMS implementation and registration
process applying management concepts such as lean manufacturing
and benchmarking as well as applying for Baldrige-type awards.
He’s a fellow of the American Society for Quality,
an ASQ Certified Quality Auditor and Certified Quality Manager,
and serves on several committees of ASQ’s Quality
Management Division. He’s the author of Stepping
Up To ISO 9004:2000 (Paton Press, 2003). Letters to
editor regarding this article can be sent to letters@qualitydigest.com.
|