by Sidney Vianna
Few people pay attention to
the forewords of international standards. If they did, they
might be surprised by what they learn. For example, the
foreword of AS9100 Revision B states, “The establishment
of common requirements, for use at all levels of the supply
chain, by organizations around the world, should result
in improved quality and safety and decreased costs, due
to the elimination or reduction of organization-unique requirements
and the resultant variation inherent in these multiple expectations.”
Who would have thought that an international quality standard
would promote cost reduction? For many, this seems an oxymoron.
Yet, for organizations that have implemented AS9100 and
related standards, the statement represents the simple truth.
Quality improvement and cost reduction in the aerospace
industry is a unique concept. It started with the vision
of a few quality leaders who recognized the benefits of
developing internationally accepted quality management system
standards.
Fortunately for us, they realized the potentially huge
benefit of harmonizing system requirements for aerospace
suppliers.
For example, AS9100 reduces costs and improves quality
by eliminating multiple variations of the same requirements.
For decades, aerospace suppliers were inundated with customer-specific
requirements that often demanded slightly different ways
of accomplishing the same task. Because AS9100 harmonized
these requirements worldwide, suppliers can now focus on
developing a single quality management system acceptable
to all their customers--and thereby reduce waste and redundant
effort.
Another potential cost-saving benefit bestowed by AS9100
is the industry’s increased reliance on accredited
certificates issued by specifically approved registrars.
Redundant and inconsistent customer audits have always been
a source of complaints for aerospace suppliers. Some undergo
more than 50 customer audits a year--basically one audit
per week. Suppliers have employees who do nothing but coordinate
and facilitate customer audits. Any company that’s
experienced such a heavy auditing schedule knows that repeated
QMS audits disrupt day-to-day activity and hamper efficiency.
Imagine, for example, your supplier quality assurance engineers
spending four hours per week answering auditors’ questions
about supplier performance monitoring. This alone represents
10 percent of a weekly workload.
However, if customers can rely on certificates issued
by independent, accredited and competent registration bodies
attesting to the supplier’s AS9100-compliant system,
they can focus their time and resources on product- and
process-specific assessments instead.
These improvements to the cumbersome supplier-OEM relationship
presented a cost in terms of a change in thinking. In order
for aerospace OEMs, primes and regulatory authorities to
have confidence in the certificates and accept them as a
component of the supplier oversight process, the industry
had to enhance existing mechanisms of registrar and auditor
competence and performance monitoring. Instead of relying
on a typical third-party process, an Industry Controlled
Other Party process was developed.
Under the ICOP process, registrars still apply for accreditation
through organizations such as ANSI-RAB NAP, INMETRO, SCC,
COFRAC, UKAS and others. However, the accreditation bodies
themselves are subject to approval and monitoring by aerospace
representatives. Further, the registrars are subject to
joint (i.e., accreditation body/OEM) oversight; office visits
and audit witnessing are two common mechanisms used to verify
the registration process’s integrity.
Due to the particular requirements for auditor competence
and registrar qualifications, a sector-specific document--SAE
AIR 5359, presently in Revision B--was created to outline
the additional requirements. Registrars and auditors are
measured against the requirements contained therein before
being granted approval to issue AS9100 certificates. Subscribers
at all levels of this process also agree to provide right-of-access
to regulatory agencies such as the FAA and JAA for their
oversight.
Presently, nine accreditation bodies are approved for
AS9100:
ANSI-RAB NAP (United States)
INMETRO (Brazil)
SCC (Canada)
UKAS (United Kingdom)
COFRAC (France)
ENAC (Spain)
SINCERT (Italy)
TGA (Germany)
JAB (Japan)
In the Americas, 32 registrars are approved for AS9100.
They are listed in the table below.
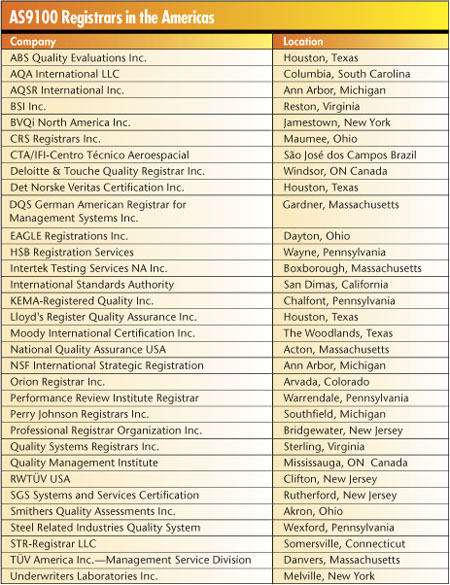
As proof that these oversight efforts aren’t simply
an exercise in rubber-stamping, some registrars have had
their AS9100 accreditation temporarily suspended. The aerospace
industry is serious about ensuring that integrity is maintained
in the registration process, which in turn should provide
much-needed confidence to all stakeholders, especially in
regulated sectors.
In addition to the process described above, some OEMs
are going further.
The Boeing Co., for example, performs certificate validation
audits during which Boeing auditors visit AS9100-registered
suppliers to ensure that their systems deserve registration.
Much effort has been made to ensure that AS9100 requirements
are accepted and adopted not only by U.S. aerospace OEMs
and primes but also by their counterparts in Europe, South
America and Asia.
In order to accomplish this, three aerospace sectors were
created around the world to allow the industry to speak
with a single voice to its global supplier base: the Americas
Aerospace Quality Group, the European Aerospace Quality
Group and the Asia Pacific Aerospace Quality Group. Together,
these sector schemes compose the International Aerospace
Quality Group. Each group determines the standards bodies
responsible for controlling their respective documents.
In the Americas, SAE performs this task; in Europe, it’s
the AECMA; and in Asia Pacific, SJAC maintains the documents.
For more information about the IAQG and AAQG, visit the
organizations’ respective Web sites at www.iaqg.org
and www.sae.org/aaqg.
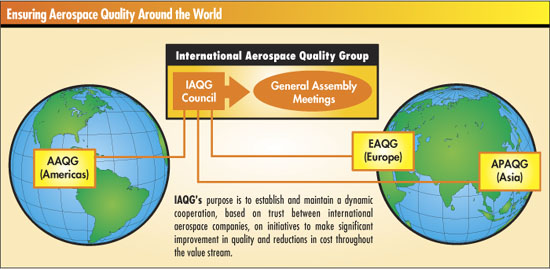
During the process of developing AS9100, quality professionals
realized that the sectors would benefit from a number of
additional documents. Many of these have been harmonized,
meaning all three sectors have agreed to make their standards
identical. A few documents pertain to a single sector; to
differentiate these, documents designated as “91xx”
represent those that are harmonized, whereas standards designated
as “90xx” aren’t adopted universally.
For example, SAE AS9100 contains exactly the same requirements
as AECMA EN9100 and SJAC 9100. On the other hand, AS9003
doesn’t have an equivalent document in Europe or Asia
Pacific.
Noteworthy documents in the AS family of standards include:
AS9101--An assessment checklist and reporting template to
capture the results of the assessments performed to the
AS9100 standard
AS9003--A system for noncomplex aerospace suppliers that
focuses on inspection and test systems
AS9102--An industry-harmonized document about performing
and reporting on first-article inspections
AS9103--Assists organizations interested in variation management
of key characteristics
AS9110--Details the quality system requirements for organizations
involved in repairing and overhauling aerospace parts
AS9111--An assessment checklist and reporting template to
capture the results of the assessments performed to the
AS9110 standard
AS9120--Quality Management Systems--Lists aerospace requirements
for stocklist distributors
AS9121--An assessment checklist and reporting template to
capture the results of the assessments performed to the
AS9120 standard
Other documents have either just been released or remain
in the deliberation process. These include AS9006 and AS9108,
which deal with deliverable software and statistical product
acceptance requirements, respectively.
AS9100 continues to inspire cost-reducing quality improvements,
not only to organizations registered to the standard but
also to aerospace regulations in general. To keep abreast
of developments, industry players can access the Online
Aerospace Supplier Information System, the official database
of up-to-date information. Among other information, it lists
approved accreditation bodies, registration bodies, aerospace-experienced
auditors and, finally, the registered suppliers that have
already attained accredited registration. As of early May,
more than 1,000 suppliers were listed in the OASIS database,
as seen online at www.iaqg.org/oasis.
Sidney Vianna is the western district manager for
DNV Certification, one of the world’s leading registrars.
He’s responsible for business development and customer
interface as well as supervising a team of 19 lead assessors
in the Western United States. Vianna is an IRCA QMS 2000-certified
lead assessor and has been involved with management system
registration since 1988. Vianna represents DNV in AAQG meetings.
A longstanding member of ASQ, he’s been a past programs
chair for the Orange Empire Section. He recently reinstated
the Los Angeles ISO Users Group.
|