newsdigest
by Dirk Dusharme and Alexander Karolyi
TEAM Act Stalls Senate
DNV Acquires AT&T Quality Registrar
Survey Highlights Quality Companies
Let's Do Lunch
Secretaries Cut Computer Clutter
Downsizing Myths
Variance Analysis Improves Health Care
ASQC Celebrates 50 Years of Quality
ISO 9000: When Your Product Is People
Partnerships Improve Quality
TEAM Act Stalls Senate
It's election year. And one of the little-known pawns in this year's politicking
is the Teamwork for Employees and Management Act (see "News Digest,"
February 1996). The TEAM Act will amend Section 8(a)(2) of the National
Labor Relations Act, allowing nonunion employees and their managers to form
teams that address workplace issues involving terms and conditions of employment.
Currently, it is illegal within a nonunion setting for such teams to exist.
The act recently became a political hockey puck used by presidential rivals
President Bill Clinton and Bob Dole. Clinton had offered to sign a Senate
bill temporarily repealing the 4.3-cents per gallon federal gas tax if the
Republicans were to sign a minimum wage increase. Dole countered with a
package that included the gas tax repeal, the minimum wage increase and
the TEAM Act. Staunchly against the act, Clinton rejected the package, stalemating
all three bills. The president has promised to veto the act, should the
bill get that far.
Why did this little-known bill hold up the Senate?
According to Sen. Edward Kennedy (D­p;Mass.), one of the bill's most
outspoken opponents, the bill is "anti-workplace democracy." Kennedy
accuses supporters of only being interested in "protecting anti-union
companies." He claims the bill is unnecessary because the current law
doesn't prohibit labor-management teams. Kennedy refers to several NLRB
cases that upheld the lawfulness of labor-management teams.
"They [TEAM act supporters] cannot point to a single National Labor
Relations Board case that has forced the disestablishment of a legitimate
employee team dealing with quality, productivity or efficiency," says
Kennedy. "This is a bill in search of a question."
Sen. John Ashcroft (R­p;Mo.), a supporter of the bill, calls Kennedy's
arguments "half-truths" and bristles at Kennedy's accusation that
the bill is anti-union.
"A labor union attempts to organize a company, and if the organizing
drive fails, the union files unfair labor practice charges against the company,"
says Ashcroft. "That's what Senator Kennedy refers to as 'anti-union
animus.' "
Regardless, it doesn't matter if there is union­p;organizing activity,
adds Ashcroft. Under the law, even if there is no anti-union animus occurring,
a company can violate the provisions of Section 8(a)(2).
Ashcroft also refutes Kennedy's assertion that the current law allows nonunion
teams that deal with quality, productivity and efficiency by producing his
own list of court cases. In several instances, federal circuit courts have
ruled that specific team topics related to the above issues are illegal.
These include: new production equipment, bonuses, merit increases, profit
sharing, absenteeism, improving air conditioning, safety labeling of electrical
breakers, hiring part-time help, removing unsanitary recycling materials,
purchasing larger smocks for pregnant employees and providing safety goggles.
Each item was ruled as falling under the definition of "conditions
of employment" as defined by the NLRA-an area that is illegal for employee-management
teams to address.
Kennedy maintains that it is still legal, even regarding these issues, for
management to deal directly with individual employees, groups they form
themselves or the work force as a whole.
"This is true," states Ashcroft. "However, what he does not
say is that when employees form a group, the employer has to be completely
independent from the group. In other words, the employer cannot allow the
group to meet on company time, provide the space for them to meet or give
them financial information about the company. That would be considered 'dominating'
the 'labor organization' according to Section 8(a)(2)."
This restriction makes the formation of employee-management teams that deal
with conditions of employment untenable, according to Ashcroft.
A Senate vote on the TEAM Act is expected soon.
Back to Directory
DNV Acquires AT&T Quality Registrar
Det Norske Veritas has agreed to acquire the quality system registration
business of AT&T Quality Registrar for an undisclosed amount.
Through this agreement, AT&T will transfer to DNV 267 quality system
certificates of customers that achieved ISO 9000 compliance. AT&T Quality
Registrar has provided those services since 1990. According to AT&T,
its quality registrar is not strategic to AT&T's restructured business.
"The newly acquired AT&T Quality Registrar will complement our
strength in the electronic, freight-forwarding and machinery industries,
as well as enhance our position with the pulp and paper industry,"
says Yehuda Dror, general manager for DNV Certification Inc.
AT&T and DNV have formed a team to assure a smooth transition for AT&T
accounts into the DNV system.
Back to Directory
Survey Highlights Quality Companies
What do Kodak Photographic Film, Disney World and National Geographic have
in common? It's not a photo essay on the world's largest mouse.
They all recently received top honors as quality companies in the 1996 EquiTrend
brand equity survey, placing first, second and third, respectively; the
Discovery Channel captured fourth and Mercedes-Benz Automobiles rolled into
fifth.
The survey, conducted by Total Research Corp., an international marketing
research firm, reached more than 6,000 consumers nationwide. Consumers were
asked to rate the quality of more than 500 brands in the United States.
Using seven nonquality criteria, such as industry dominance, function and
value, and service/responsibility, the survey recorded participants' perceptions
of the quality of the companies.
"Brand quality perceptions of consumers are excellent indicators of
a brand's sales and profitability," says James Alleborn, senior vice
president and managing director of TRC's Consumer Research Division. "And
research shows a very high association between the brand quality perceptions
of consumers and the stock performance of the company that manufactures
the product."
Back to Directory
Let's Do Lunch
Say it's not so. Has downsizing and an increased pressure to perform killed
off our lunch hour? It could be. Fourteen percent of U.S. office workers
don't take lunch, according to the Steelcase Workplace Index.
While a few office workers actually eat, 44 percent run errands, 38 percent
take working lunches, 37 percent read, 27 percent go shopping, 14 percent
exercise (go figure), 9 percent go to the doctor, 6 percent check on their
kids and 1 percent go on job interviews (probably looking for a job where
they can eat in peace). The average lunch hour for the survey's 298 respondents
was 36 minutes.
Northeast and West Coast workers still got it right. Forty percent of those
workers take a full lunch hour five days a week. Which reminds me it's 11:59
and this is California.
Back to Directory
Secretaries Cut Computer Clutter
When it comes to computers, secretaries have the savvy. In a survey developed
by OfficeTeam, a national staffing service, 88 percent of executives said
they consider their administrative assistants' recommendations about corporate
computer needs important.
"Administrative assistants are becoming increasingly familiar with
a wide range of software applications, from word processing, spreadsheet
and desktop publishing packages to database and presentation software,"
says Andrew Denka, executive director of OfficeTeam. Denka noted that many
administrative assistants have become so adept at using computers that they
are able to help others in the company.
Back to Directory
Downsizing Myths
Contrary to traditional beliefs regarding the benefits of downsizing, many
companies are finding that reducing their number of employees may lead to
a reduction in profits. Some common myths and myth busters are provided
here and on the following pages.
Myth: Downsizing boosts profits.
Fact: Profitability does not necessarily follow downsizing. Between
1989 and 1994, operating profits increased in only 51 percent of companies
reporting work-force reductions; 20 percent said operating profits declined
(The Wyatt Co., 1993).
Myth: Downsizing boosts productivity.
Fact: A study of more than 250,000 manufacturing plants by the National
Bureau of Economic Research found that while some plants did downsize and
post healthy gains in productivity, even more (including many of the largest
facilities) managed to raise output per worker while expanding employment
(Business Week, July 1994).
Myth: Since companies are just "cutting fat" by downsizing,
there are no adverse effects.
Fact: For the majority of companies, downsizing has had adverse effects
on workload, morale and commitment. Among 531 companies surveyed, six out
of 10 reported increased workloads among survivors, and more than half reported
decreased morale and commitment (The Wyatt Co., 1993).
Back to Directory
Variance Analysis
Improves Health Care
At St. Mary's Health Center, a continuous improvement technique called variance
analysis allows hospital staff to increase its quality of care. The St.
Louis hospital uses Care Pathways to plan treatments, diagnostics, education
and discharge planning. Nursing staff chart any patient care that varies
from the pathway and, after analyzing variances, determine if the variance
is an implementation problem or whether the pathway itself needs to be adjusted.
For example, in 1994, when St. Mary's began variance analysis on Care Pathways
for pneumonia patients, two key items surfaced. Patients were not receiving
antibiotics within four hours, as specified by the American Thoracic Society,
and often didn't receive the antibiotics called for by the pathway or the
ATS, explains Beth Clamp, Care Pathways coordinator at St. Mary's.
"We wanted to know to make these patients feel better quicker,"
says Clamp. "The answer was, give them the appropriate antibiotic and
get it to them sooner."
Based on the variance analysis, St. Mary's educated its physicians, pharmacists
and nursing staff on ATS guidelines. They also changed the pathway, specifying
drugs to be used and adding boxes to record the time a patient is admitted
and when the patient first receives antibiotics.
From July 1994 to December 1995, the mortality rate for pneumonia patients
dropped from 10.4 percent to 3.4 percent, average length of stay decreased
from 7.6 days to 6.3 days, and average length of time between admittance
of a patient onto the hospital floor and the administration of antibiotics
decreased from 5.3 hours to 3.5 hours.
Back to Directory
ASQC Celebrates 50 Years of Quality
This year, the United States' largest quality organization, the American
Society for Quality Control, marks its 50th anniversary. Most of the quality
methods now used throughout the world-including statistical process control,
quality cost measurement and control, TQM, failure analysis and zero defects-have
come from the ASQC and its members.
The organization, which boasts a membership of more than 130,000 members
worldwide, was founded on Feb. 16, 1946, in a meeting between the Society
for Quality Control and the Federation of Quality Control Societies. It
became a national organization when 17 separate societies merged, forming
a society of 1,000 members. Annual dues were $3.
The ASQC's birth can be indirectly traced to the Japanese attack on Pearl
Harbor in 1941, according to On Q, the ASQC's journal of record. U.S. involvement
in World War II called for large-scale production of wartime materials,
which led to an increased need for statistical methods to improve product
inspection and quality. To train factory workers in these methods, courses
were developed by quality pioneers W. Edwards Deming, Eugene Grant, Ralph
Wareham and Holbrook Working.
Following the courses, which were eventually taught throughout the United
States, participants met to share their knowledge. These meetings led to
the formation of local quality control societies. It was out of these societies
that the ASQC was formed.
ASQC's mission statement hasn't changed much in the 50 years since it was
first published in the March 1946 issue of Industrial Quality Control, ASQC's
first publication:
"The purpose of this society shall be the advancement of and diffusion
of knowledge of the science of quality control and its applications to industrial
progress; to serve the public by making available journals, newspapers and
other channels of public information; to promote unity and effectiveness
of effort among all those who are devoting themselves to quality control
of industrial processes, by research, by application of its principles,
by teaching or studying."
In a recent interview, when asked to comment on the ASQC's most important
contributions to quality, ASQC President Deborah Hopen echoed key aspects
of the 50-year-old mission statement.
"I think that one of the greatest contributions made by the ASQC is
that we pulled together people from so many fields and so many independent
organizations in order to exchange ideas," explains Hopen. "We
started a chain of networking, debate and growth for continuous improvement
of the knowledge base. This is very important. As soon as a new idea came
out, we got very, very good at sharing it back with our members."
ASQC Timeline
1946-ASQC founded on February 16.
1947-Walter Shewhart: ASQC's first honorary member. Shewhart Medal established.
1948-ASQC's Code of Ethics established.
1965-ASQC co-sponsors the first International Congress in Quality Control
in Tokyo.
1968-First certification examinations for quality engineers.
1984-Congress designates October as National Quality Month.
1987-Malcolm Baldrige National Quality Award established with ASQC as co-administrator.
1990-ASQC starts the RAB.
1994-American Customer Satisfaction Index released. Eleven elementary schools
participate in Koalaty Kid training initiative.
1995-Deborah L. Hopen becomes ASQC's first woman president. ASQC launches
Internet home page.
Back to Directory
ISO 9000: When Your Product Is People
Documenting for ISO 9000 is difficult enough when your product is an easily
definable product or service. But what about when your product is employees?
Recently, the procedures used by 294 Adia Personnel Services branches to
select and place temporary employees were registered to ISO 9002.
Unlike documenting products that can be tracked easily, Adia faced documenting
products that can be much more difficult to account for-people.
Wanting to establish consistent quality among its branches, Adia's corporate
staff compiled a quality management system manual outlining every procedure
involved in placing clerical and light-industrial workers at local companies.
Each branch reviewed job orders to ensure there were detailed notes on all
transactions with current and prospective employees. Employees of Adia's
branch offices also had to have confirmed references on file, completed
application forms and results from tests identical to those given to other
individuals applying for the same positions.
The process resulted in more consistent employee/client matching, says Liz
Vaughn, quality manager at Adia Personnel Services.
"Our staff doesn't have to think twice about what has to be done,"
explains Vaughn. Instead, they can focus on working more closely with employees
and companies to ensure a better fit between the two,"
Back to Directory
Partnerships Improve Quality
In the 1950s, it wasn't uncommon for large corporations to fund colleges
and universities. International Paper Co., however, was one of the first
companies to enter into business-education partnerships to improve the quality
of education at primary and secondary schools.
Through its Education and Community Resources program, IPC awards grants
for schoolwide redesign, teacher fellowships for theme-related activities
and technology grants that benefit students and teachers.
"We have local partnerships between school districts and the company,"
says Sandra Wilson, vice president of the International Paper Co. Foundation.
"We spend $700,000 a year in grants to schools. But it's a comprehensive
program, not just a 'write a check and come back next year' thing."
The program focuses on teacher recognition, professional development and
serving rural schools often overlooked by funding organizations, says Wilson.
It also requires that the local IPC facility commit to allocating staff
time and other resources.
Each school's needs differ, but the results speak for themselves, says Wilson.
In Camden, Arkansas, for instance, the district leveraged a $9,000 EDCORE
grant into an additional $35,000 in donated community services and materials
to develop a school-based farm. All students, not just agricultural students,
use the farm to learn science, math, team-building and decision-making skills.
The International Paper Company was one of five recipients of the Conference
Board's Best in Class Award, which honors corporations for their innovative
education-improvement programs.
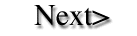