by Greg Brue
Is the health care industry in denial when it comes to practicing Six Sigma? The answer, unfortunately, is yes. Although the industry is slowly adopting the methodology, the majority of these initiatives aren't designed to improve the quality of the medical treatment offered to patients. Instead, most health organizations focus on improving care from the administrative side. As a result, patients aren't getting the quality improvements to which they're entitled. The real issues facing health care are ignored due to medical practitioners who are afraid to admit that the lack of quality care is a result of their own errors and inefficiencies.
Why is everyone so afraid to speak about the "pink elephant in the room," i.e., the root cause of the most pressing defect in health care: the failure to correctly diagnose patients at the outset, leading to improper and ineffective treatment? The purpose of health care is to deliver proper treatment to patients. Yet with so many health care organizations concentrating on improving quality, why is medical treatment not improving overall? Because, in this industry, Six Sigma initiatives focus on everything but core issues.
My five years of extensive research with a major player in Six Sigma for health care indicates that most improvement initiatives in this field have consisted of nonessential projects. Some of these are listed below:
Reduce wait time for call-ins
MRI scheduling
Increase capacity in X-ray
Report turnaround time
Discharge delays
Improve patient satisfaction at ER
Improve medical capacity
Increase surgical capacity
Improve the revenue cycle
Employee safety
Patient waiting time
Call center defects
Health care billing defects
Reduce in-patient waiting time
Defective patient records
Internal billing and insurance
Rescheduling
Operating room utilization
Doctor utilization and wait time
The sad reality is that the elephant is getting bigger because medical practitioners behave as though they're above using Six Sigma problem-solving tools. But problem solving is what medicine--and Six Sigma--are all about. Case in point: I took the Medical College Admissions Test to gain a better understanding of the medical thought process. I also use the test as part of a test model for Master Black Belt training. Despite having no medical training whatsoever, I scored 87 percent on the test. How is that possible? Because 90 percent of the test consisted of problem-solving questions. Six Sigma provided the perfect tool set to pass the MCAT.
Obviously, Six Sigma can help doctors provide better care to their patients. But if those of us in the Six Sigma industry continue to partner with the medical community and focus solely on noncore health care problems, we're actually doing patients a major disservice. We're enabling doctors to provide the wrong treatments more quickly.
The other defect plaguing this industry is insurance regulations, which force medical practitioners to suboptimize care to align with schedules of benefits. Typically, these are out of date months before they're printed. We must let doctors do their jobs to ensure the correct treatment the first time, not waste time and money trying to work around the system. This is a separate topic with an entirely different approach and scope that needs to be addressed as well.
"Six Sigma is based on the principle that quality ends up costing less, the better you do it," says Six Sigma Consultants' partner, medical advisor and Chief Medical Officer David J. Shulkin, M.D, a major advocate of Six Sigma and quality in the medical field. "It's hard to get someone to understand something when his salary depends on him not understanding it." His point is that doctors get paid the same regardless of whether they embark on Six Sigma or not. If there's no monetary motivation for doing so, why make the effort?
Everyone knows that major defects exist in core areas of health care, and that these defects cost not only dollars but human life. For example, medication errors are the second most expensive type of malpractice lawsuit, averaging $163,090 per claim, according to Shulkin's 2002 presentation titled, "Developing the Role of the Patient Safety Officer." It's easy to understand why this is the case: just look at the way many prescriptions are communicated between medical professionals (e.g., doctor to nurse, doctor to pharmacist). In the table at right, the left column lists a common and more error-prone method of presenting prescription instructions; the right column shows the unambiguous, less error-prone method.
More evidence that medical practitioners are turning a blind eye to root causes based on error can be found in statistics on avoidable deaths per type of procedure, as seen in the table below.
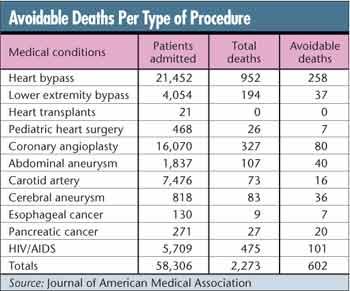
"There are real life-and-death differences between hospitals, and that shouldn't be ignored," Dr. R. Adams Dudley told the San Jose Mercury News in 2000. Dudley is an associate professor of medicine and health policy at the University of California, San Francisco, and the author of "Study: Choosing the Right Hospital Can Be a Life Saver" (Journal of the American Medical Association, 2000).
But don't just take his word for it; you can perform a simple ANOVA test to statistically prove the validity of that statement. Even that may not be necessary. The data in the table below, a sampling from several hospitals for the same procedure, indicate that perhaps there are obvious, even blatant, differences.
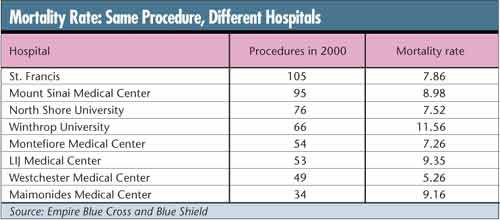
Working with doctors, we used Six Sigma tools to analyze the data from each of the fatalities and determined that the rate of avoidable deaths could have been reduced by more than 50 percent.
You're probably thinking, "Yeah, this sounds great in theory, but does it really work for medical diagnostics?"
A real-life health care problem will demonstrate how Six Sigma was used to solve a treatment issue. Call this project "Anemia Case 101." This project actually arose out of a side discussion with four doctors and five nurses regarding anemia. I was asked by one of the doctors to join in the side discussion to see if there was an application for Six Sigma. In fact, this was a perfect problem that Six Sigma could solve rather quickly, given participation from the medical side.
Anemia is defined as any condition in which the number of red blood cells, the amount of hemoglobin and the volume of packed red blood cells in the blood are lower than normal levels. The disc-shaped cells contain hemoglobin, a unique molecule that carries oxygen to the body's tissues. One of the more common blood disorders, anemia occurs when the number of healthy red blood cells decreases in the body. The effect to the patient is debilitating and sad. Loss of blood will cause blackouts, low energy levels and poor quality of life. In fact, some of the patients in our study suffering from this mysterious blood loss caused major auto accidents due to their frequent blackouts.
If we use the "Y is equal to the function of X" formula as we do in Six Sigma, we can identify causes. However, before we could go into the X's, the measurement system was validated using a measurement systems analysis that looked for repeatability and reproducibility in the measurement of red blood cell count. Now we knew the data were valid and we were ready to identify the high-level factors for anemia.
Anemia X's included:
Increased destruction (i.e., breakdown) of red blood cells
Increased blood loss from the body
Inadequate production of red blood cells by the bone marrow
We next pulled a sample data set based on a combination of past patient data, accounting for 1,373 patients over a one-year period. We used a multivariate, passive Six Sigma tool on the past patient data to sort through the many reasons, codes and diagnosis conditions. In addition to the past data set, there were 286 active patients.
Of the active patients, 23 percent (65 patients) suffered from the type of anemia that is caused by blood loss. Therefore, blood loss was the "Y" we needed to solve for those patients. Incidentally, the doctors included in this study hadn't even attempted to address the cause. Instead, they treated the patients' symptoms. The treatment was to take major doses of iron along with monthly blood transfusions. Insurance companies paid for this treatment in full for years without knowing the root cause of the problem. Where was the blood going? No one cared to find out. Why not? Because treatment was ordered, which constituted effective management of these patients according to and approved by the insurance provider. This is an excellent example of suboptimizing to insurance companies.
Using Six Sigma tools, we looked for possible X factors driving the blood loss in those 65 active patients and discovered that for 17 percent of them (12 patients) the root cause was literally going down the toilet. Blood was being passed through the stool of the patients due to massive hemorrhoids.
This project took one month from beginning to end, at which point we shared our project results with the doctors. A basic surgical procedure was the solution, and after many years of poor quality of life, these patients are living full lives again. The solution had a one-time average cost of $7,000, compared to an average cost of $78,000 over a two-year span of unnecessary treatments, additional ER and other nonrelated visits, all the result of treating the symptom rather than finding the cause. Of course, this didn't include related costs incurred by the patients as a result of poor quality of life, missed workdays, auto accidents, etc., which are impossible to estimate.
The once skeptical doctors were convinced of the viability of applying Six Sigma to core medical issues and have since begun studies on other core issues. This study focused on one treatment solution; keep in mind that there are literally thousands of treatments being undertaken right now, involving millions of patients. How many of these patients are receiving incorrect treatments, and how much money is being wasted across the entire health care industry? Think about the true effect that Six Sigma could have if we focus on the core issues of health care and improving the lives of these patients.
Health care can approach the near perfection of Six Sigma. Human systems aren't so different from others in which
Six Sigma has successfully reached high levels of reliability. The health care industry must begin applying the same Six Sigma methods that worked to improve manufacturing processes.
All it takes is just a couple of brave leaders willing to take the right course and confront resistance to core issues once and for all.
Greg Brue is a leading practitioner of Six Sigma and an original Six Sigma pioneer. He worked in concert with Jack Welch and Larry Bossidy to bring about the unprecedented success of General Electric's and AlliedSignal's initiatives. The success model and training content he designed for these initiatives have been regarded as the standard in the industry for more than a decade and have been adopted by several academic institutions, including Wake Forest University, for their Six Sigma curricula. He's the best-selling author of Six Sigma for Managers (McGraw-Hill, 2002) and Design for Six Sigma (McGraw-Hill, 2003). The Six Sigma 36-Hour Course, Six Sigma for Small Business and Radical Thinking are scheduled for release later this year.
|