Quality Management
by A. Blanton Godfrey
To be effective, strategic quality planning must be used as a tool,
a means to an end, and not as the goal itself.
Integrating Quality and Strategic Planning
A few years ago, an organization I was working with gave me a wonderful
visual image that has stuck clearly in my mind. It is dogs on bungee cords.
The creator of this image is Paul Plsek, a colleague from my Bell Labs days.
This organization used the image to accurately portray their quality management
activities: happy dogs bouncing up and down. Almost half of their employees
were involved in quality teams. But they achieved almost no results: no
real changes in cost structure, no increase in customer satisfaction, no
increase in market share.
It didn't take long to discover the cause. They had no real strategic or
quality plan. People throughout the organization guessed at what was important,
what the priorities were, what was urgent. Activities were not aligned with
key strategies. Improvements were not linked to provide meaningful results
across critical processes. Even at senior levels, they had no clear agreement
on important priorities.
The past few years has seen an increasing emphasis on strategic quality
management. Companies recognize that the true key to business excellence
is integrating quality goals and actions into the organization's strategic
and operational plans.
This process of defining a customer-focused vision, stating the objectives
and integrating quality goals into the company's strategic and annual business
plans is often called strategic quality planning. For many years, it was
one of the Malcolm Baldrige National Quality Award criteria. Last year
it was changed to just strategic planning to recognize the emphasis of the
award criteria as a model of business excellence, not just quality management.
In some companies, this process is called hoshin kanri, or translated (poorly)
as policy deployment, policy management or even hoshin planning.
In the United States, this process is known as strategic quality management.
The elements of strategic quality management are not too difficult to understand.
At the 30th Anniversary Congress of the Asian Productivity Organization,
Hideo Sugiura, former chairman of Honda Motor Co., explained the roles of
senior management and strategic quality management clearly. Sugiura described
four "sacred obligations" of management:
n Have a clear vision of where the company is going. This must be clearly
stated and communicated to every member of the organization in language
he or she understands.
n Define clearly the small number of key objectives that must be achieved
for the company to realize its vision.
n Translate these key objectives throughout the entire organization so
that each person knows how performing his or her job helps the company achieve
objectives.
n Provide a fair and honest appraisal so that each and every employee knows
how his or her performance has contributed to the organization's efforts
to achieve the key objectives, accompanied by guidance on how the individual
can improve this performance.
One of my colleagues, Joe DeFeo, has collected information on more
than 20 leading companies' strategic plans and worked with several in integrating
quality goals into their strategic plans. In a recent paper, "TQM and
the Bottom Line," Joe describes several commonalities of these plans.
Most companies have redefined their long-term plan, or vision, to focus
on being the best at what they do, not just the traditional goal of being
market leaders. Each has strategic goals in a few key areas: customer focus,
operational efficiency (costs), new-product development, financial success,
personnel development and environmental responsibility.
DeFeo has found some other important characteristics leading companies
share. They have developed specific measures for the goals, subgoals, annual
goals and supporting projects. Executive management reviews these regularly.
Responsibilities, accountabilities and resources have been clearly identified.
The company communicates the plans throughout the organization.
To be effective, strategic quality planning must be used as a tool, a means
to an end, and not as the goal itself. It must be an endeavor that involves
people throughout the organization. It must capture existing activities,
not just add more activities to already overflowing plates. Finally, it
must help senior managers face difficult decisions, set priorities and eliminate
many current activities, not just start new ones.
For many companies, it is the first time in the history of the organization
that everyone has formed a clear picture of where the organization is going,
why it is going there and what activities are necessary to get there. For
others, it is the first time people have felt that their views were important.
About the author . . .
A. Blanton Godfrey, Ph.D., is chairman and CEO of Juran Institute
Inc. Send comments, suggestions or questions about this column either to
the editor or directly to Godfrey at Juran Institute, 11 River Road, Wilton,
CT 06897, by fax (203) 834-9891 or preferably by e-mail to godfrey@netaxis.com.
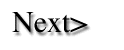