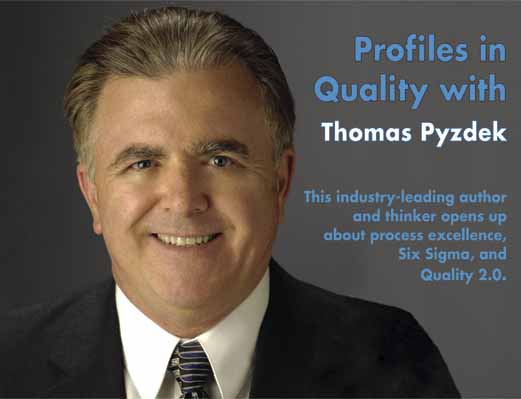
by Carey Wilson
Thomas Pyzdek is the author of The Six Sigma Handbook (McGraw-Hill, 2003), The Handbook of Quality Management (Quality Publishing, 2000), Quality Engineering Handbook (Marcel Dekker, 2003), and more than 50 other copyrighted works. He has also written hundreds of papers on quality and process improvement. Pyzdek worked on committees that created such journals as Quality Engineering , Quality Management Journal , and the International Journal of Six Sigma and Competitive Advantage, and he writes the monthly column “Quality 2.0” for this magazine.
Pyzdek serves on the editorial boards of several journals and provides consulting and training in process excellence to clients around the world in the fields of manufacturing, health care, and services and transactions businesses. He was an examiner for the first Malcolm Baldrige National Quality Award and a judge for the first Arizona Governor’s Award for Quality.
He is an ASQ Fellow and is ASQ-certified in both quality and reliability engineering and a recipient of ASQ’s Edwards and E.L. Grant Medals and the Simon Collier Quality Award from the Los Angeles section of ASQ. He is listed as an outstanding author in The International Who’s Who in Quality (Industrial Engineering & Management Press, U.S., 1994). During his 41 years as a quality professional, Pyzdek has trained thousands in process excellence principles and techniques. His podcast on process excellence draws more than 1,000 listeners per episode.
For more information, visit www.pyzdek.com.
Quality Digest: When you began studying quality processes, what were your goals and ambitions?
Thomas Pyzdek: I started my career in quality in 1967. At the time I was working as a press operator in a can-manufacturing plant, and I applied for an opening as a quality technician. I was immediately fascinated by the fact that we could take measurements from a sample of five units every 15 minutes from a process producing up to 1,500 units per minute, plot a few key metrics on control charts, and control the quality of the process. I wanted to learn as much as possible about this magic crystal ball called statistical quality control.
QD: What would you say has been the greatest achievement in the process excellence movement in its history, and in the past 10 years?
TP: In its history? Wow! That’s a big question. I guess I’d say that modern quality began when Walter A. Shewhart invented statistical process control in 1919. This was a revolution that moved the focus from inspection of product to control of the process. It was a revolution because it changed quality from looking at outcomes to looking for root causes, using statistical methods to help guide them. We still use this approach today.
In the past 10 years quality has moved from manufacturing into many other types of businesses and other organizations. Quality has also moved from being the exclusive domain of the quality department to being practiced by a large number of people in other parts of the organization. When I visit with clients and attend meetings, I see senior leaders using the tools originally created by the quality profession to help them run the organization. I hear questions such as, “What are we solving for with this plan?” and “What data do you have that support that hypothesis?” These folks are applying t he quality tools, techniques, and principles to metrics that have nothing to do with product quality to deliver results for investors and employees as well as for customers.
QD: As a writer, educator, and consultant in matters of quality management, you must deal with people at all levels of management; what sort of assessment process do you use to evaluate a client’s needs and goals, and how do you go about reaching those goals?
TP: I begin by asking the senior leaders to simultaneously look at balancing goals for all major stakeholder groups, and balancing their short-term and long-term goals. This is usually something new for them, and it’s difficult, but quality is all about discovering the harmony of stakeholder interests and creating a game where all stakeholders win.
To accomplish the goals, I have the leadership develop strategies and then operationalize their strategies via metrics. The metrics are then classified as either key requirements that must be competitive or differentiators that must be world-class, and they are displayed using balanced scorecards. Differentiators and key requirements with critical gaps are placed on dashboards and used to identify plans that are of strategic importance. Some plans are implemented as a normal part of the work; others are implemented via projects. For projects, I have leaders develop problem statements, business cases, and burning platforms. Projects are pursued as “just do” projects, or using an improvement methodology such as lean, lean Six Sigma, kaizen , etc. The dashboards are used to monitor the progress of plans and projects, and the balanced scorecards are monitored to confirm that all of the activity is actually having the desired strategic effect.
QD: You have written that Six Sigma must be implemented from the top down. What are some of the biggest challenges of teaching Six Sigma to CEOs and managers who were previously unfamiliar with the procedures necessary for implementing successful Six Sigma programs?
TP: One of the big challenges is simply awareness that Six Sigma can be useful to them as C-level leaders. Many CEOs think that Six Sigma is only for their technical people. The best way I’ve found to overcome this is to expose CEOs to other CEOs who have had success with Six Sigma. I’m looking for excitement and faith at the beginning. Once the CEO gets excited about process excellence, the rest is mere detail. The quality profession has developed a powerful, proven approach to achieving total business excellence that isn’t hard to teach and practice, if we have the CEO’s commitment to lead the program. I’m also always impressed by how much a committed CEO can add to my basic approach. These folks are really smart, they know their organization, and they’re inspired leaders. Remember, it was CEOs who turned the quality profession’s tool kit into a powerful approach for achieving a competitive advantage.
QD: What are the hallmarks of a successful implementation of Six Sigma? Can you talk about a particular company (or type of company) that has benefited specifically because of its implementation of Six Sigma?
TP: There are two hallmarks that I recognize in all successful process excellence deployments: the simultaneous focus on all stakeholders and short-/long-term [objectives], and the use of evidence to guide decisions. Companies that I’ve personally seen benefit from implementing process excellence include Boeing Satellite Systems, Intuit, Seagate, H&R Block, and many others. As a Baldrige examiner and a judge for the Arizona Governor’s Award for Quality, I’ve seen hundreds of other examples. The funny thing is that each one is unique, yet the hallmarks of excellence are the same.
QD: How does your concept of Quality 2.0 tie into the training of Six Sigma practitioners?
TP: Quality 2.0 is my attempt to incorporate the lessons that I’ve learned from my experience and the knowledge I’ve gleaned by studying successful and not-so- successful attempts to improve organizations. Certainly, Six Sigma has made valuable contributions, but Six Sigma and quality practitioners have much more to offer other than their ability to improve operational processes. For example, I’d like to see the Six Sigma approach applied to deploying strategies. Strategic planning has historically failed to produce the kind of change leaders hope for because there hasn’t been a rigorous way to program the strategies into real change. Creating real change is one of Six Sigma’s strong suits. By marrying Six Sigma deployment know-how to strategic planning’s vision, we can help our organizations quickly move toward their vision. Six Sigma training needs to help practitioners learn how to do this. In many cases this will involve moving away from a project-by-project approach and using Six Sigma tools and principles in an operational way.
QD: How has the blossoming of global enterprises affected the education, training, and working conditions of quality professionals?
TP: Well, it certainly means a lot more time on airplanes! Quality professionals must understand different cultures and different attitudes toward quality. Quality trainers must adapt to different styles of learning, language barriers, and so on. Third-world manufacturing facilities and test equipment vary from ancient to ultramodern, and the professional needs to be able to look beyond the surface conditions to determine if the overseas supplier can meet the requirements. In the global economy the quality professional will need to be flexible in terms of time, attitude, and tolerance.
QD: What has been the greatest change in quality management since you began your career?
TP: I graduated from college and began my career in quality in earnest in the mid-1970s. I was taken aside by a friend who explained that quality was the “backwater” of the company. It was the department where those who couldn’t cut it elsewhere went to watch their careers die. He implored me to look elsewhere in the company. I thought about what he said for quite some time. He was certainly correct about some of the personnel, and the quality department was always underfunded. However, it seemed to me that quality was undeniably important and that the situation inevitably had to change.
Of course, it did. By the mid-1970s U.S. businesses began to notice that they were losing customers to overseas competitors because of quality problems. By the 1980s American management could no longer hide from the fact that it was largely to blame for the inferior quality of its own products. The NBC documentary “If Japan Can… Why Can’t We?” introduced America’s senior leaders to W. Edwards Deming, TQM was rediscovered, and we haven’t looked back. During my career, quality management moved from a backwater to the board room.
QD: How long have you been affiliated with the American Society for Quality, and what brought you into contact with the organization?
TP: I graduated from the University of Nebraska at Omaha in 1974 with a degree in economics, and seven years of work experience as a quality technician and quality engineering technician. The main value of the economics degree was that the American Society for Quality Control [ASQC, as it was then called] would allow me to sit for the certified quality engineer [CQE] exam. Back then the CQE was ASQC’s only certification and the exam took all day. I took a refresher course, passed the exam in 1975, and immediately got a job as a quality engineer. I joined ASQC in April of 1975 and have belonged to the organization ever since. I am now a Fellow.
QD: What are the benefits of ASQ membership for a quality management professional?
TP: ASQ [The organization dropped “control” from its name in 1997] is the quality industry’s primary professional society. Membership has become complicated, and I’m still somewhat confused by it, so I just maintain my section membership and membership in a couple of divisions. I find that membership in the ASQ is a way to meet other quality professionals, locally and from all over the world. Through ASQ I’m able to give back to the profession that has been my life’s work. I’ve worked on numerous committees, helped establish two major peer-reviewed journals, spoken at many events, and done what I can to help promote quality. In the process I have met fellow professionals and established many lifelong friendships. I highly recommend ASQ to my fellow professionals in the quality field.
QD: Quality Digest is read by thousands of quality assurance and control professionals in every field of human enterprise, and every segment of the manufacturing supply chain--how can they best work together to make their jobs complementary of each other?
TP: One way is through membership in ASQ. Another is to make use of Quality Digest’s many fine online forums. The internet provides a way to meet with others without the need to travel. Read the articles and columns in Quality Digest and write to the authors or to the editor to share your views. ASQ Region 7 sponsors discussion groups of people with similar interests; find out if your section or region has something similar. If it does, participate. If it doesn’t, volunteer to set something up. Most important, as the Nike ad says, “Just do it!”
Carey Wilson is Quality Digest’s news editor.
|