10 Rules for successful
ISO 9000 Registration
by C.W. Russ Russo
Working toward ISO 9000 registration can feel like wading through a morass.
Participants can feel like the fellow up to his posterior in alligators
in a swamp. Through my experience of helping several companies transform
their quality assurance processes to meet ISO 9000 requirements, I have
learned the following 10 simple tenets for successful registration.
1 - Forget the ISO 9000 standard.
Forget the standard and concentrate on your internal processes and your
customers' needs. Your quality assurance system is supposed to satisfy your
organization's needs. Think about what you need to do to effectively and
efficiently produce your product or service and meet your customers' needs.
Each of the 20 sections of the standard is designed to challenge your thinking
about how you conduct your business and how you satisfy your customers.
Some people will do the most amazing things to themselves in the name of
ISO 9000. When someone tells me they must do something because ISO 9000
requires it, I know they are focused on the standard rather than on their
own processes and customers. While there are certain requirements in the
standard, many of the challenging tasks people create for themselves have
no justification in reality. If something doesn't pass the crucial "process/customer
need" test, don't do it.
2 - Know the standard.
The standard is short-less than 10 pages. The problem for many organizations
is that the standard is generic and doesn't provide specific implementation
guidelines. No one external to your company can tell you the "right
way" to implement ISO 9000 because it's about your product and your
customers. The answers must come from people who own the processes. The
more you work with the standard and think about applying it to your own
situation, the more you become an expert. One good tactic is to have several
people working on an ISO 9000 implementation team to bounce ideas and interpretations
off each other.
3 - You are smarter than any auditor.
Yes, auditors are certified. Most have experience in quality control or
quality assurance. Few have experience as operations or line personnel.
So even if the auditor has worked in your industry, this doesn't mean that
he or she has worked in a company the same size as yours or has used the
technology you use. Also, there is no guarantee that the auditor has kept
current with the industry-specific knowledge.
A subrule here is never take any requirement claim in the standard at face
value. Respect the auditors, but do not believe them blindly. While auditors
know the standard, they don't know your system, your specific processes
or your customers. It is always useful to ask auditors to show you the specific
sentence in the standard being referred to and to explain the thinking behind
their interpretation.
Another important subrule revolves around the fact that auditors are only
at your company for a few days and don't have an opportunity to thoroughly
learn your business in detail. One of the best things you can do for yourself
and your company is to make sure your employees understand what ISO 9000
is all about and how their jobs support the company's quality policy. This
requires a planned and concerted effort to get the word out and run a good
communications program as the registration project develops.
4 - Keep it simple.
This rule sounds like an old saw, but it is true. There is specific guidance
in both the standard and the guidelines that encourages you to achieve simplicity.
You should attempt to develop and implement the simplest quality assurance
system that works well. For example, always try to work with the lowest
level of documentation possible. If a work instruction will serve, do not
write a procedure. Use flowcharts, pictures and diagrams instead of words
in both procedures and work instructions.
Also, use work instructions as training records. You don't need to develop
separate training documentation. Simply have the supervisor observe an employee
perform the work instruction, sign off with a standard statement at the
bottom of the form, and file the work instruction as the employee's training
record.
Good organizational communication is simple and focused. Write simple sentences,
aimed at the eighth-grade reading level-even if you have a company full
of Ph.D.s. This raises the likelihood that people will read and act on the
material.
Use standard forms whenever possible. For example, develop a fill-in-the-blank
form for your internal audit report and assemble relevant documents as attachments.
Use the back of internal audit forms as your corrective action form. One
major complaint against ISO 9000 is that it is documentation-intensive.
That is a fallacy. Smart quality personnel know how to avoid too much detail
and minimize paper.
5 - Salvation is in the details.
An alternative way to say this is "plan your work and work your plan."
A computer-based project-management software program can be a blessing and
will help you identify and track the myriad of tasks and activities that
need to be accomplished. Further, it will help you stay on track and on
schedule.
Most ISO 9000 transformation projects involve hundreds of steps and tasks.
While they are not complex individually, following up on them can be. Most
delays in an implementation timetable are due to small breakdowns in schedules.
These can snowball until the project goes into crisis overload. Getting
control of the details on the front end saves much time and frustration.
6 - Set milestones and enforce them.
Identify milestones that will show participants both how much has been accomplished
and what remains to be done. Dividing the project into manageable sections
also can reassure participants that the project is achievable. To do this
organizing work, use computer project software, distribute GANTT charts
showing milestones and publish milestones and tasks in meeting minutes.
Make sure to spread the work around and let everyone know that they are
an important contributor and that failure to deliver on time lets down everyone
on the team. Do quarterly progress updates to management, and don't hesitate
to identify missed deadlines. It's not politically wise to identify individuals
who aren't performing. It will only take a couple of missed deadlines reports
before offenders start taking their responsibilities to the project more
seriously.
7 - Get help.
Frequently, the organization's quality manager is selected to be the ISO
9000 management representative. This seems logical because management sees
ISO 9000 registration as a quality department issue. This is a false perception.
Quality is a line management issue.
To avoid shunting the responsibility to the quality manager, form an ISO
9000 oversight group or executive support group. These "champions,"
who represent the highest level of functional management, should be responsible
for knocking down barriers and encouraging participation. They need to promote
and support the ISO 9000 project by ensuring their people contribute as
needed. Members of this group should meet at least quarterly and receive
brief reports of the project's progress. Some companies put ISO 9000 as
an agenda item on the executive steering committee's quarterly agenda.
The second group should be the implementation team. The quality manager
might chair this group, but outsiders should do the "committee work."
For example, one person should be responsible for running the internal audit
program, and a different person should run the corrective and preventive
action program. Yet a third individual should be responsible for the documentation
development program to satisfy ISO 9000 requirements.
Fill this group out with one or two interested wizards-people enthusiastic
about their work. They enjoy being in the forefront of change efforts and
manage to get things done. They can come from anywhere within the organization
and are a marvelous addition to the registration project. Start searching
for wizards in the accounting department and from among mid-level supervision
in the operations department.
8 - Keep the project visible.
A closely related issue is the need to promote the project in order to secure
resources and help. Use milestone charts and graphs to show progress, report
activities in the company newsletter, post progress reports on employee
bulletin boards and talk up the project next to the water cooler and as
an agenda item in department meetings. Given a choice between a one-hour
briefing for a department and several short, 10-minute progress updates
in department meetings, go for short updates.
Find ways to keep the project alive and visible so that people see that
it is ongoing and an integral part of the organization. Effectively publicizing
an ISO 9000 transformation project takes frequent and varying types of
small exposures rather than a few big events. The point is to help people
adapt to and accept the program as part of their daily lives.
9 - Celebrate small victories.
Find any excuse to party or to help people feel good about their progress
and be recognized for their efforts. Sometimes just a kind word or two is
sufficient, but you should also try to organize specific celebrations around
milestones. They need not be elaborate. A group breakfast for the team takes
is easy and inexpensive to organize.
10 - Remember the political issues.
Certainly, ISO 9000 is a wonderful concept. It is reasonable, and everyone
should appreciate its value to the organization. But the reality is that
we are all creatures of our corporate cultures. Further, we have substantial
ego involvement in our work and our vision of our positions in the organization.
Two fundamental phenomena underlying these political realities are the need
for self-preservation and the territorial imperative. These drives make
changes in our roles and responsibilities feel very risky.
Another political reality an implementation team must reckon with is the
human tendency to form and voice opinions based on unspoken assumptions
and insufficient information. While people are often prepared to act despite
a lack of information, not knowing what is expected or the likely outcome
feels dangerous. One solution is an active public relations campaign that
recognizes these fears and helps people understand how the ISO 9000 transformation
will directly affect their jobs. Individual and group feedback to ISO 9000
participants is another powerful way to reduce individuals' uncertainty
and discomfort.
11­p;ISO 9000 registration looks great on your résumé.
Every quality expert knows you are supposed to give your customers more
than they anticipated. This article was supposed to have 10 rules; however,
here is an "extra" for good measure. It is probably the most useful
of all.
ISO 9000 is neither a miracle nor a panacea. Organizations experience disheartening
and frustrating times during such a large project. But the process clearly
works, and the outcomes for organizations are powerful in both external,
customer-oriented and internal, employee-oriented ways. This is evident
in the number of companies pursuing and obtaining ISO 9000 registration.
The total is increasing logarithmically, and it is predicted that at least
100,000 companies in the United States will register or seek registration
by the turn of the century. Talented and experienced ISO 9000 management
representatives will be in demand. On the darkest days, think about the
bright shining spot on your résumé that your experience with
ISO 9000 registration represents.
About the author
C.W. Russ Russo is managing partner of The Trainers Workshop, a consulting
firm in Lawrence, Kansas, that provides consulting, training and support
in quality management, continuous improvement and ISO 9000
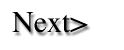