by Peter Dickin
On-machine verification allows initial checking of machined parts to be carried out in situ on any computer numeric controlled machine tool, rather than having to transfer them to coordinate measuring machines (CMM) for inspection. The main advantage is that any mistakes are discovered where they can be corrected--on the machine tool. Repeated cycles of machining and inspection, interspersed with long setup times on the respective pieces of equipment, are avoided, meaning that overall manufacturing times can be reduced.
The most obvious benefit of on-machine verification is for those companies that do not have existing inspection capabilities. Most modern machine tools either come with, or can be retrofitted with, probing capabilities to assist in the setup of the job. With the right software, this same equipment can now be used for verification at little extra cost.
On-machine verification can provide huge time savings by enabling the quality of the component being machined to be monitored at all stages in the manufacturing process. This allows any errors to be detected earlier, and thus corrected more quickly and at lower cost. For example, it is possible to check that the correct amount of stock has been left on the component after a roughing operation, rather than having to wait until all machining operations have been completed before discovering that an error has been made.
Similarly, the extent of any damage caused, for example by a tool breakage, can be assessed accurately and a decision made immediately to determine whether the part can still be completed within tolerance or whether it will have to be scrapped.
Of course, there are already a variety of manual methods for undertaking such checks between machining operations. However, like all manual operations, these are time-consuming and prone to human errors and inconsistencies. Furthermore, they are based on inspection against drawings, when most design data are now issued as computer-aided design (CAD) files. On-machine verification is a more automated and more consistent process than manual measurement, and also allows checking against CAD data.
Companies that already have suitable inspection equipment might think that on-machine verification is an unnecessary operation that can cost machining time. However, if the whole process is considered, there is considerable potential to reduce delivery times. After all, machining time is only valuable if the operation is producing good parts.
If a part has to be transferred to a dedicated CMM and the inspection shows any errors, the component must be returned to the machine tool and reclamped in position before being machined again. This is time-consuming for any component and can take many hours for a large, heavy item, such as a press tool for an automotive body panel. In addition, any mistakes during the setup back onto the machine tool could result in a new series of errors in the component, and so lead to a further cycle of inspection and remachining.
With on-machine verification, the part can be checked at each stage without being moved. The inspection on specialty-measuring equipment only needs to be undertaken once at the end of the manufacturing process. This more regular in-process verification provides greater confidence that the component will be produced within specification.
There are also concerns about the reliability of using a machine tool to check its own work. Of course, measurements made with a machine tool on the shop floor cannot duplicate the accuracy that is possible on a dedicated CMM in a climate-controlled environment. That level of precision may be very impressive, but it is rarely needed in most manufacturing operations. In addition, the quality of the results from machine tools can be checked against known artifacts in exactly the same way that the inspection accuracy of a CMM can be confirmed. Trials undertaken by Gloucestershire, United Kingdom-based metrology specialists, Renishaw Plc, have shown the results from machine tool measurements to be both more accurate and more consistent than expected.
The latest advance in on-machine verification has been the introduction of multi-axis operation. This development allows companies with four-, five-, or six-axis equipment to undertake verification of their parts on these more complex machine tools, both during and after machining. The benefits of this approach are similar to those that are gained by using five-axis machining. First, more features are able to be inspected in a single operation in the same way that more of the component can be machined. For example, users will have the ability to check undercut regions or to check a series of deep holes with different orientations without any need to refixture the work piece. Similarly, the ability to use shorter probes can increase verification accuracy, just as using shorter cutting tools can improve machining accuracy.
The move of the checking process from the CMM room to the factory floor means that the results need to be both quick and easy to produce and understand. Because there will no longer be specialty metrologists to interpret the data produced, making the best use of on-machine verification requires software that is not only simple enough for machine tool operators to use but that gives a quick and easy comparison of tooling or sample components against CAD data. The output must be clear, comprehensive reports that can be understood by everyone involved in the product development process, not just inspection specialists.
For this reason, PowerINSPECT software, created by Delcam, located in Birmingham, United Kingdom, has proven particularly successful for on-machine verification. The system offers a wizard-based approach to developing the inspection sequence, making it easy to generate the required probe path. An extra level of security is provided by the process simulations that can be carried out on the computer, allowing any potential collisions to be detected before the routine is run on the shop floor. The software is also very flexible, allowing extra measurements to be taken in any areas that may cause concern during the verification process.
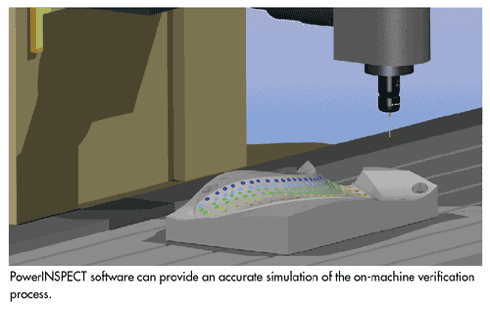
Most important, the results are easy to understand. All measurements are initially displayed as green, red, or blue dots, depending on whether the point taken is within, above, or below tolerance. At the end of the process, reports can be generated quickly in a clear, customizable format that shows whether the part has been made accurately and highlights the areas that might cause concern.
Two examples from different industries show how significant the benefits of on-machine verification can be. The first is at Taiwan’s leading press tool manufacturer, COC Tooling & Stamping, where the introduction of on-machine verification has allowed the company to halve the time need to manufacture its tools. The new technology has helped the company gain the maximum benefit from its recent investment in high-accuracy, high-speed machining equipment.
Established in 1990, COC now employs approximately 450 people at its 50,000-square-meter site in Taoyuan County, Taiwan, where it specializes in tooling for large automotive body panels. These tools are supplied to major manufacturers, including Ford Motor Co., Nissan Motor Co. Ltd., Toyota Motor Corp., General Motors Corp., and Mitsubishi Motors. COC is justifiably proud of the many awards it has received from these customers, in particular its 2003 Ford Global Suppliers World Excellence Award, which is only given to 10 suppliers each year.
Y.K. Tseng, president of COC, explains that the introduction of on-machine verification produced enormous increases in productivity, even though, at the time, it had only been in use for six months. “With on-machine verification, we can measure the press tools on the machine and find out immediately if there are any problems,” he explains. “We can obtain a direct comparison with the CAD model, which is much more reliable than using inspection methods based on drawings.”
Most of the machine tools at COC are between four and five meters in length, and many of the press tools being manufactured are of a similar size. “Moving parts of that weight and size to the CMM for inspection used to be extremely difficult and slowed down the whole production process,” says Tseng.
The main problem with these large tools is that the longer cutters needed to machine to their full depth can be pushed out of alignment, especially near the bottom of the part. This gives an oversize surface on the punch, while the cavity will be undersize.
“Previously, because of the problems in setting up the tool back on the machine, we would use hand-finishing to correct any errors,” remembers Tseng. “This wasn’t very accurate and was also very time-consuming. Now, we can remachine the surface on the machine tool, which is both faster and more reliable.” This higher quality can be seen in the much reduced tryout times needed for new tools. “We can now be confident that the tool will work as soon as it comes off the machine,” says Tseng.
The second example is Crosby Composites, a leading composites manufacturer based in Northhamptonshire in the United Kingdom. The addition of on-machine verification has helped the company to produce composite components to levels of accuracy rarely seen in the industry. Owner Paul Crosby now uses the ability to finish-machine every part to tolerances between 0.1 mm and 0.25 mm as the key differentiator for his business.
Crosby founded his company 25 years ago and has spent all his working life in the autosport industry. He began his career as an engineer with the Mach F1 team, when the use of composites in racing cars was first introduced. “It was obvious that this was an opportunity that would get bigger and bigger, so I started my own company,” he recalls. “We began with very basic wet lay-up methods, and moved to using pre-preg and autoclave curing as the company developed.”
With composites, machined holes and pockets tend to be undersize because the material relaxes when it is cut. This effect is difficult to predict because it is impossible to cut all the fibers in the same orientation. To overcome this problem at Crosby, the initial machining operation is now followed by an inspection on the machine tool. This shows how much more material needs to be removed and enables the required extra tool paths to be generated in the company’s computer-aided manufacturing software.
For a typical component, with between 20 and 30 holes, a further cycle of inspection and machining may be needed to produce all the dimensions to the required tolerance. However, for subsequent parts, the complete machining sequence can be repeated and the results checked with a final inspection.
The first set of 17 components produced with this method was supplied to one of the F1 teams and fitted onto the car with no clashes or rework. It was the first time in the team’s history that this had happened with any set of composite parts from any supplier.
“Since then we have used on-machine verification as much as we possibly can,” says Crosby. “It ensures that we can catch any mistakes before they reach our customers. In the six months since we started with this approach, we have only had one part rejected, and that was because of just one undersized hole.”
With productivity a key issue for all manufacturing companies, anything that can reduce waste or improve efficiency must be worthy of further investigation. On-machine verification has the potential to achieve both these goals, making it something that progressive manufacturers cannot afford to ignore.
Peter Dickin has worked for Delcam for more than 15 years, initially as public relations officer; then as country manager responsible for Australasia, Southern Africa, India, and Pakistan; and currently as marketing manager. Prior to his arrival at Delcam, Peter spent 16 years at the plastics and rubber consultancy, Rapra Technology, located in Shropshire, United Kingdom.
|