by James Clark
Manufacturers want to measure more features and parts in less time. For a growing number of companies, the features they want to check are complex surfaces, and the form and fit of assemblies. As good as contact measurement techniques are, they're simply too slow and cumbersome to satisfy this demand. So these inspection jobs are beginning to migrate to laser measurement devices, the noncontact optical-inspection technology that's poised to accommodate a surge in applications during the next few years.
People are often surprised to hear this claim because of laser scanning's slow start. They remember the old laser scanners of the 1980s, such as the Hymarc scanner. Designed mostly for use on coordinate measuring machines (CMMs), these relics required operators to manually adjust the pitch, yaw and roll in order to put the laser in the correct position and orientation for each pass over the features being measured.
Moreover, scanning only multiplied data and the headaches that went along with interpreting them. Quality control engineers still had to pour over the measurements in the same way they looked at data collected by touch probes: They read pages of X, Y and Z coordinates. With scanned data, the chief difference was that operators were now looking at thousands of points instead of only scores.
Those days are long gone, thanks to innovations in the mid-1990s that made laser scanning desirable for hand-held applications. The first of these innovations was a new generation of scanners that are much lighter and more reliable than their predecessors. Exploiting the electronics and materials revolutions, scanner manufacturers not only simplified their designs to use fewer parts but also built them from smaller components and lighter materials, such as magnesium.
The availability of reasonably priced computing power played a big role, too. Collecting one to five million points and comparing them to computer-aided design (CAD) files within a minute or two takes a lot of horsepower. Five to eight years ago, that processing speed simply wasn't available. Given the processing power and memory capacity available now at reasonable prices, today's high-end personal computers are more than sufficient for working with the massive point clouds that laser scanners generate.
Perhaps the most overlooked advances in computing technology have been made in the software for operating the equipment and interpreting data. During the mid-1980s, software developers began using object-oriented programming, which organizes code by function rather than sequentially. Object-oriented programs are much shorter and simpler because they refer to the same section of code each time a particular function occurs, instead of repeating the code each time in the sequence. As a result, it's easier and cheaper to develop sophisticated programs that run quickly, contain more features and have simple, intuitive user interfaces.
Hand-held laser scanners, such as this Metris K-Scan MMZ, are useful in a variety of applications within the automotive and aerospace industries.
|
About the time that the new generation of lightweight laser scanners appeared on the scene, manual coordinate measurement arms had just co
me into their own. They could do a job without special programming. The operator simply defined a coordinate system and either touched the appropriate points with a probe at the end of the arm or moved a laser scanner on the arm over the features to be scanned.
The manufacturers of these arms, FARO Technologies Inc. and ROMER Inc., had adopted an open architecture to encourage the development of tools that would expand the range of applications for their products. They viewed laser scanners as one of these tools and were eager to promote them. Largely because of their marketing strategy, laser scanning found its first significant set of successful applications.
Admittedly, most of these applications were restricted to reverse engineering, design and troubleshooting. Equipment portability was a boon for these applications, but its manual nature made it impractical for in-process inspection, which is where most potential applications are found. Establishing laser scanning in the heart of the inspection market would require one or more platforms that could automate the measurements to speed the process and remove human error.
CMM builders provided the first of these platforms around 2000. Wanting to replicate the success that laser scanning had in widening the range of applications for portable measurement arms, builders adopted a new strategy for their machines--they transformed them into multisensor measurement centers. Like a machining center, these CMMs have access to touch probes, analog scanning probes and laser scanners. Operators can program their CMMs to make basic prismatic measurements with probes and to measure complex free-form surfaces with the scanner.
CMM builders demonstrated their commitment to the new strategy by giving scanner manufacturers access to their native control codes, software interfaces and error maps. Thus, today's scanning software can adjust qualifications automatically on most CMMs that use Renishaw's PH10 indexing head. Scanning is much faster, and its accuracy no longer depends on the operator's skill and diligence.
The productivity gains from this technology can be tremendous. An Ohio- based manufacturer of blow molds, trim dies and associated tooling reports that the automation enables one of the CMMs in its quality laboratory to complete a typical scan of its tools in about an hour. With the old technology, getting good results on the same surfaces would have taken six to eight hours. Along with a growing number of moldmakers, this company's engineering staff is learning to incorporate laser scanning into its quality-control regimen and is finding more ways to keep its CMMs busy.
Laser radar is another platform for automating noncontact inspection with laser scanners. Although the technology has been available for a decade, it really hadn't found much practical use until recent advancements made automation more appealing. Because of the automation available now, a number of manufacturers of large assemblies, such as aircraft, have replaced their laser trackers and theodolites with laser radar.
Originally, manufacturers of laser trackers designed the devices f
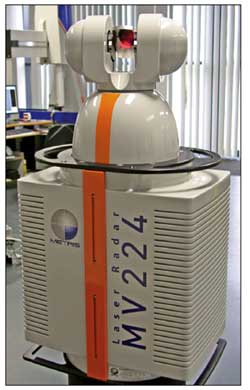
Laser radar is a large-volume tracking system enabling high-accuracy, factorywide localization of multiple objects.
|
or laying out large components and putting equipment into position. Over time, they adapted the technology for inspection by developing a hand-held tracking ball. To use it, one operator climbs on or under the aircraft and holds the target on the point to be measured while another operator on the ground makes the measurement. During the process, the operator holding the ball must not interrupt the laser beam hitting the tracker ball. If this happens, he or she must recapture the beam before measurement can continue. Some newer tracker technologies, such as FARO's XtremeADM, have mitigated this problem.
Laser radar works on a different principle. Rather than following a tracker ball, it points its beam directly at the hole, slot, surface or other feature being measured. Consequently, laser radar isn't limited to measuring point by point. It can scan complex surfaces, collecting millions of points and forming point clouds just as a laser scanner on a CMM would do.
Because no one needs to climb on the aircraft to hold the tracking ball in place to attract the laser beam to the points to be measured, laser radar's movement can be automated to run an unattended, preprogrammed inspection routine. Radar technology can bring the benefits of automation to inspecting large parts and assemblies much as CMMs do for smaller ones. Not only does inspection occur much faster, but removing the operator from the measuring process also eliminates the major source of error and variability in trackers.
This technology appeals greatly to manufacturers in the aerospace industry, where it has found a number of applications. Laser radar units are already measuring the large solar sails that unfold once a satellite achieves a geocentric orbit around the Earth. Because these sails are made of a thin metal foil, checking them before deployment is a challenge. The slightest breeze, even one caused by a person moving about the room, can cause the sail to move enough to introduce significant error into the measurements. Laser radar solves this problem by allowing the operator to set up the inspection during the day, leave, and let the inspection proceed overnight.
Besides its affinity for automation, laser radar can easily measure composite materials, which pose refraction problems for most other optical systems. Now that composite materials are figuring more prominently in new designs, such as Lockheed's Joint Strike Fighter and Boeing's 787, aircraft manufacturers and their suppliers have been taking notice of the technology.
Indeed, some are already using it to inspect fuselage subassemblies. Using laser radar for this purpose allowed one aircraft manufacturer to chop two weeks from its inspection cycle.
Perhaps the most impressive development in optical noncontact measurement is the ability to mount laser scanners on robots. When a robot completes its work in an automated production cell, it can swing to a tool rack, release the tool at the end of its arm, grab a scanner as it would any other tool, and return to the part or assembly to inspect it. Because the scanner is a flexible measurement device, the robot can retrieve the appropriate inspection program for checking a particular workpiece in the mix of products flowing through the cell.
Enabling a robot to wield a laser scanner seems a logical ex--tension of the technology that human operators use when they wave a manually operated coordinate measurement arm over a part. Getting to this point, however, required more than developing a laser scanner for manual jobs. Robots might be capable of flexible automation, but in the past they've been too inaccurate for inspection. A robot's controller normally predicts where the end-effector is in space based on position feedback from the rotary encoders in the arm. The inaccuracy of this technique makes robots unsuitable for direct inspection.
The situation has changed radically during the past year with the introduction of optical dynamic motion measurement (DMM) technology, such as the Krypton product from Metris. An optical DMM tracks a hand-held laser scanner held by a robot arm, triangulating its location and orientation based on the position of nine light- emitting diodes (LEDs) built into the probe's handle. A bank of three linear CCD cameras external to the robot and scanner reads the signals coming from each of the LEDs as the robot scans the workpiece. The DMM bypasses the robot's encoders and measures the scanner's position and orientation directly and accurately, thereby removing the previous constraint on robotic inspection.
Of course, another constraint remains. Despite their flexibility, robots are anchored to the floor. The next step in the evolution of robotic laser inspection will be to overcome that limitation by coming full circle and automating manual coordinate measurement arms. Companies are already ironing out the details in that technology. The plan is for these arms to be portable like their manual predecessors and also able to execute a program and inspect parts automatically, without the operator manipulating the scanner.
Robotic measurement arms will fill a niche for automating the inspection of products made in volumes too small to justify other forms of automation, yet large enough for manual inspection to be a burden. Examples might be products made in small batches or made as a one-off every so often. Not only will robots that can carry out inspections currently done with the manual arms boost repeatability, but they also will open laser scanning to an even larger range of applications. They, like other automated platforms already at work in factories, are the reason that laser scanning is poised to take noncontact inspection by storm.
James Clark is a physicist and vice president of business development for Metris USA Inc. in Rochester Hills, Michigan. He began his career in 1992 as a researcher for the department of computing and electrical engineering at Heriot-Watt University in Edinburgh, Scotland. Clark holds degrees in physics from Dundee Institute of Technology (Scotland) and Heriot-Watt University of Edinburgh. He has authored more than 25 journal, conference and trade journal articles on topics ranging from 3-D measurement, polarization vision, reverse-engineering inspection and 3-D scanning of ancient works of art.
|