by Mike Dusharme
More on RFID
Manufacturers
News
|
Manufacturing automation continues its decisive march with one of the hottest innovations in the field: inventory control and supply chain management using radio frequency identification (RFID) technologies. RFID implementation promises to simplify and expedite inventory control and supply chain management across a broad spectrum of enterprises. Retail, defense, transportation and health care have begun requiring their suppliers to implement this technology. The magnitude of some of these enterprises--such as the well-known "big box" chains or the Department of Defense--means that this requirement affects thousands of smaller suppliers.
RFID is a technology for automating the identification and tracking of commodities and collecting information on their whereabouts, their contents and their physical state. An RFID system has several components, including chips, tags, readers and antennas. One of the reasons that RFID is so efficient is that it's designed so that individual items can have an individual identi fier.
This identifier is a small, programmable, silicon RFID memory chip capable of recording and storing information. The chip is attached to a small, flat, flexible antenna, and this assembly makes up a tag that's attached to an item. To read a tag, a radio frequency (RF) reader, also equipped with an antenna, sends the tag an encoded radio signal. The tag receives some of the RF energy from the reader signal and transmits it back as a return signal that delivers information from the tag's memory.
RFID tags are designed and manufactured in a variety of shapes and sizes depending upon the application's requirements. RFID has a large enough read range to use extremely small tags for such applications as near-field item-level tracking, where tags might reside under bottles caps or behind product labels. But it works just as well with applications such as pallet- or case-level tracking of products on conveyors. Items that pass through portals, where they can be read from a distance, typically require larger tags.
RFID readers generally comprise a computer and a radio. The computer manages communication with the network, allowing tag data to be sent to enterprise software applications such as enterprise resource planning (ERP) systems. The radio controls communication with the tag, typically using a language dictated by a published protocol such as the electronic product code (EPC) Class 1 specification. This particular protocol, one of several in use, is the most common language used by tags in supply chain applications. The reader can receive multiple signals and identify many items at once. RFID can collect large volumes of data each second from many RFID-tagged items as they move across assembly lines, through dock doors and even off of store shelves. Integrated with an enterprise-level network, RFID systems can serve as the first step in identifying and tracking information to be analyzed and used to prompt decisions and actions.
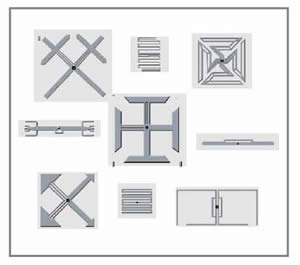
|
More advanced RFID readers also accommodate remote management and coordination of readers via the company network when many units are used in the same environment. These mechanisms reduce interference and allow coordinated operations. Finally, some readers have state-of-the-art receiver designs that provide for the best possible read range.
RFID antennas can vary in their technologies but are typically attached to the reader at any one of four to eight ports for an equal number of send and/or receive points. The antennas, placed in their own housing, are usually mounted remotely from the reader to obtain the best possible vector to the tags.
Fully realizing the benefits of RFID also requires host computer platforms to manage the reader-to-tag communications for encoding and decoding algorithms, reader-to-reader communications for managing blocks of readers in close proximity without degrading read rates, reader-to-enterprise communications for implementing a control and management link between readers and the enterprise, and a platform integration of the reader with existing management structures such as network security and other business applications.
An RFID assembly might consist of two light-metal framework panels in opposing positions on each side of a waist-high conveyor located at the rollup door of an indoor unloading dock. Antennas, in their housings, would be mounted on the framework above the conveyor and opposite each other at a height best suited to the application. Readers would also be mounted on the framework, and the antennas attached to the readers. Optional hardware could include an RFID printer encoder for generating tags.
As incoming items are offloaded from the transport and sent down the conveyor to pass between the antennas, the reader begins transmitting an encoded RF signal via the antennas. The tag antennas sense the signal and pass it on to the chip, which generates a responding signal back through the tag antenna. This signal is then sensed by the reader antenna and passed to the reader, which communicates the item information to the host system.
RFID systems have a read range of approximately 30 ft under ideal conditions. Systems can also be modified for lower-range requirements by reducing the output power at the reader, thereby reducing the size of the reader antenna or the tag antenna.
In the retail sector, applications include supplying pallet-to-case-to-item-level visibility with versatile RFID readers and tags. To increase supply chain visibility and reduce labor and shrinkage, retail markets are a good fit for RFID (Wal-Mart, Best Buy, Target and Albertson's have all reportedly implemented the technology). At receiving, RFID reduces labor, enabling the quick scanning of pallets and eliminating the need to open cases to get inventory down to the item level. Benefits include reducing out-of-stocks through item-level visibility of storeroom and shelf inventories, reducing the reconciliation of misshipments by promoting more accurate shipping, and preventing product counterfeiting, diversions and theft through mass, reliable, item-level identification.
According to the U.S. Government Accountability Office, 13 federal agencies are already using or plan to deploy RFID technology. The U.S. Department of Defense has mandated the use of RFID by its suppliers for increased supply chain visibility and improved forecasting. Other governments, meanwhile, are evaluating similar initiatives.
Implementing RFID to deliver the right materials in the right condition at the right time is a critical part of support. The military and its suppliers gain a more accurate picture of consumption and are better able to reduce stock-outs of critical materials. Logisticians and forces on the ground are able to make better-informed decisions on which supplies to move first and where to move them. Duplicate orders are minimized, and logisticians can be more responsive. RFID tags and readers meet a variety of defense requirements, including longer-range asset tracking and monitoring of environmentally sensitive materials, such as rations and medical supplies.
In the area of health care, including pharmaceuticals and clinical environments, RFID applications are particularly promising. Mallinckrodt Pharmaceuticals, a division of Tyco Healthcare, one of the fastest-growing generic pharmaceutical companies in the United States, has been using RFID for the past two years. The initial RFID solution provided by ADT/Tyco Fire and Security for Mallinckrodt involves tagging bottles of selected strengths of Mallinckrodt Pharmaceuticals Generics' oxycodone and acetaminophen family of products. RFID tags are placed on bottles of the analgesic drug as they leave Mallinckrodt's distribution center in Hobart, New York. The RFID tags can then be used by retailers to continue tracking the product throughout their supply chain .
Pharmaceutical manufacturers, hospitals and clinics, regulators charged with public safety, retailers and consumers benefit from RFID-enabled applications for patient safety. These include product-pedigree traceability and medication-administration validation, asset tracking, threat protection, recall management and general supply chain visibility. For manufacturers and hospitals, using low-cost RFID technology to tag and track high-profit margin assets such as medical equipment is an effective use of the technology. Health care providers, meanwhile, hope to lower insurance premiums due to RFID-driven reductions in liability.
RFID can also ease compliance with regulatory and reporting mandates, such as pedigree laws for traceability and rules for hospital accreditation. The practical requirements for deploying RFID in health care applications are broad due to the range of potential tag sizes and form factors, as well as a broad spectrum of read ranges to support rapid, accurate reading off of pallets on conveyors as well as near-field item-level tracking.
For the transportation industry, everything in the global supply chain eventually moves by air, truck, train or ship. RFID can bring visibility and enhanced security to the handling and transportation of materials, baggage and other cargo. Such applications as freight tracking, baggage handling, airport- and freight-terminal security, and cold chain management can all benefit from the technology. RFID tags and readers meet a variety of transportation requirements, including tracking over extended ranges and real-time monitoring of cargos for temperature, humidity and tampering during shipment.
Another practical application for RFID is brand authentication. Counterfeit brands have become a serious problem for many industries. The apparel and entertainment industries have been particularly hard-hit as counterfeit brands bleed off substantial sales and damage carefully crafted brand images. In such industries as pharmaceuticals, counterfeits also threaten consumer safety. For unsuspecting retailers, they can pose serious liability issues. RFID is a potentially powerful brand-protection solution that's capable of identifying product pedigree and ensuring brand legitimacy down to the individual item level. Because it's a cost-effective solution for automating brand authentication, RFID can also contribute to lowering overall product and operational costs.
Cold chain management involves monitoring produce, packaged foods, meat and poultry products, seafood, flowers, chemicals and sensitive pharmaceuticals--anything that's frozen or must stay within strict temperature parameters. Producers, carriers and retailers are implementing RFID to ensure the quality and safety of perishables by providing visibility into environmental conditions during shipment and storage. Rather than allowing spoiled product to reach the customer, RFID provides real-time data that can be analyzed throughout the cold chain. This is achieved through tagging shipments on a pallet and case level rather than the traditional truck or container level. The tag travels with the pallet from the manufacturer or grower, through the distribution center to the store. A single temperature record is maintained that can be used to pinpoint problems, assign liability and take preventive measures.
For automated asset tracking via RFID to be effective, the technology platform must provide for extended range, sensor capabilities and memory. Often, access to the objects being tracked is limited, and frequently the ability to monitor for shock, vibration and tampering is key. Tag memory is important for storing sensor data, as well as individual asset information.
Automotive and other large-item manufacturers can implement RFID to track manufacturing progress. For example, a tag is applied to an automobile or truck chassis on the assembly line, and as new components are added, the tag is updated to eventually reflect a finished product or subassembly.
Reducing inefficiencies caused by human error and driving down overall labor costs will undoubtedly improve the return on investment for those able to invest in RFID. However, with the cost of RFID systems for an average supplier running well into six figures, according to one RFID equipment supplier, large enterprises that require their vendors to implement RFID might well unintentionally exclude smaller suppliers, or put such a financial burden on them as to make deployment impracticable. Such was the situation Wal-Mart ran into after mandating that all its suppliers be RFID-capable by January 1, 2005. Many Wal-Mart suppliers have yet to comply, due largely to technical or logistical issues.
Along with the basic costs of the hardware, for RFID to fulfill its promise, investments in a number of outside RFID integration services must be made. An installation begins with a site evaluation by experts trained in the behavior of RF technology in various environments. The evaluation results will determine the system requirements. Mechanical work that often accompanies an RFID installation must be performed, and then the services of those skilled in RFID implementations have to be engaged.
Only some of the RFID suppliers offer software that does more than collect data from tags that have been read. For the data to be meaningful and useful, the software that interfaces RFID data with enterprise software must be purchased, or designed and implemented. Much of this will be determined by how many RFID-specific business processes are involved. Following that, integration with the existing enterprise system software might require modifications performed by a consultant.
Additionally, RFID tags must be developed that are appropriate in dimension and material for the items to be tagged, and the tags must be cost-effective. In large quantities, a 96-bit EPC tag costs from 20 to 40 cents. According to one expert, that puts RFID tagging out of the picture for high-volume, low-margin products such as grocery products, where the break-even point is in the 5-cent-per-tag range ("Finding RFID's Break-Even Point," Jorge Santana, RFID Journal , Dec. 6, 2004).
The system and implementation costs of RFID may constitute another barrier that further excludes small businesses from participating in a resurgent economy. However, as the technology gains ground in multiple industries, it's expected that costs will be within the reach of other enterprises beyond the global giants.
Mike Dusharme has held positions in research and development, and sales management of industrial automation throughout a 20-year career. He is currently a freelance technical writer based in Southern California.
|