Manufacturers continue to find new ways to apply machine vision -- commonly called automated inspection -- to improve productivity and quality in the manufacturing process. With its advanced color-processing capabilities, color machine vision solves problems and performs tasks that once required human vision.
On a typical production line, for instance, a sensor detects a part and signals a video camera positioned above or to the side of the inspection point to capture an image and send it to a machine vision processor. Using a combination of hardware and machine vision software, the vision system analyzes the image and provides a mathematical answer to questions such as "Where is the part located?" "How long is the part?" and "Are any defects present?"
However, what happens when the questions turn to "Is this part the correct color?" or "Which parts are orange and which red?" Because traditional grayscale machine vision technology makes decisions based on 0-256 shades of gray, inspecting colored parts automatically is unreliable in many cases and impossible in others. For this reason, manufacturers use color machine vision technology to inspect parts in ways that could not be done using traditional grayscale machine vision systems.
Specifically, manufacturers use color vision to solve three primary vision applications:
Color verification -- Verifying that a certain part's color matches what the vision system is programmed to find.
Color sorting -- Sorting parts based on color.
Color inspection -- Inspecting colored parts for defects that grayscale image processing tools can't detect.
What types of color parts do color vision systems verify, sort and inspect? Before discussing specific ways in which this technology works on the factory floor, it might be helpful to gain a better understanding of color itself and how machine vision systems interpret it.
Color spaces
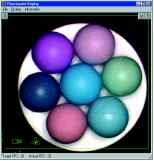 |
The vision task is to sort the center blue ball form the others |
|
|
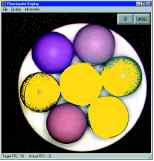 |
Because many balls contain a blue hue, sorting by hue alone is not enough. |
|
|
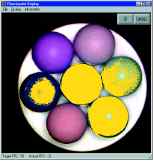 |
Looking at hue and intensity is better, but still not enough. |
|
|
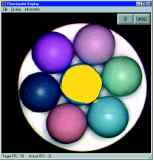 |
Using hue, intensity and saturation, the color vision system can sort the center blue ball from the others. |
|
|
|
Defined as the perceptual result of visible light reflected from an object to our eyes, color represents an interpretive concept. This means that, depending on how light is reflected, we all see colors a bit differently. Because a great deal of both variation and interpretation influence what we know as color, the Intersociety Color Council has created a Universal Color Language, which is accepted all over the world. The council's color standards make it possible to quantify and measure color, thus maintaining consistency in manufacturing.
The Universal Color Language classifies colors into color spaces. These three-dimensional coordinate systems quantitatively define colors. Although dozens of defined color spaces exist, color machine vision primarily uses two, known as RGB and HSI. The RGB color space represents all colors as a mixture of red, green and blue, which constitute the primary colors used by video cameras, televisions and PC monitors. When combined, these colors can create any color on the spectrum.
The HSI color space is broken down into hue, saturation and intensity. Hue refers to pure color, saturation refers to the degree or color contrast, and intensity refers to color brightness. Modeled on how human beings perceive color, this color space is considered more intuitive than RGB. It can be compared to the dials on an old television set that help viewers adjust the set's color.
To analyze and process images in color, machine vision systems typically use data from either the RGB or HSI color spaces, depending on a given task's complexity. For example, in simple applications such as verifying that a red LED on a mobile phone is indeed red and not green, a vision system can use data from R, G and B signals to perform the operation. With more complex applications, however, such as sorting pharmaceutical tablets of subtly different colors, a vision system may require hue, saturation and intensity information to perform the operation. The series of images in Figure 1 illustrate how a machine vision system might use hue, saturation and intensity to sort pastel-colored balls.
Advanced color vision systems can mix RGB and HSI color planes, giving users more flexibility and a wider range of inspection options.
Before color machine vision technology emerged, color image analysis, though possible, remained highly impractical for use on the factory floor. Programmers had to spend a great deal of time developing specialized software algorithms, and because RGB data couldn't be converted to HSI in real time, color processing occurred very slowly. As an alternative, standard grayscale vision tools performed the task, which involved assigning a value based on a 0-256 grayscale to a colored part.
Unfortunately, this method failed in applications where parts under inspection were similar in color. For instance, when a grayscale vision system inspects a dark blue and a pale yellow object, the two colors appear quite differently to the system, which most likely will assign them grayscale values at opposite ends of the spectrum. However, if the first object is dark blue and the other a medium blue, the vision system will have trouble differentiating between the two and might assign very similar grayscale values. This would prevent the system from reliably verifying, sorting or inspecting these parts based on color, which means the parts must be inspected manually.
Today, advancements in machine vision technology and faster, more powerful PC processors have made color machine vision feasible for real-world manufacturing. Vision companies have developed specialized chips for converting standard RGB images from a color camera into the HSI color space, and color processing is now fast enough for high-speed production lines. Additionally, easy-to-use, intuitive software tools have been developed that enable users to program vision systems using Windows-based dialogue boxes and point-and-click dials. Such tools work for a variety of tasks, including measuring an image's color, distinguishing between a single color's multiple hues or segmenting an image on any color plane.
New applications
The Eyes Have It: A Three-In-One Solution with Color Machine Vision
A leading manufacturer of color eyeliner pencils needed to perform a variety of inspection tasks to ensure the quality and safety of its pencils. First, it needed to inspect the color material around the pencils' tips. Second, it needed to verify that the pencils were sharpened at the correct end because a pencil sharpened at the wrong end would expose a wooden point -- a potential hazard to consumers. Finally, it needed to measure the sharpened tips' shapes to ensure that the cone was produced to the specified size and roundness. The manufacturer could not perform these tasks using grayscale vision tools and required a vision system that would allow it to develop and modify its own application.
Using a Cognex Checkpoint 900C color machine vision system, the manufacturer now can perform all three inspection tasks with a high degree of accuracy and reliability. Because the inspections all involve the pencils' tips, each pencil is rotated a full 360 degrees in the camera's field of view. Using a combination of front and back lighting, the vision system inspects the entire circumference of four pencils per second and checks for excess makeup on the tip, verifies that the correct side is sharpened and measures for specific shape. Plant engineers can develop and modify inspection applications easily by using the system's Windows-based graphical user interface.
This solution has enabled the manufacturer to produce eyeliner pencils at a higher standard of quality and safety, while giving it greater control over its production environment. |
|
Color machine vision technology has opened doors to a wide range of applications that could not be performed previously. As a result, manufacturers around the world in virtually every type of industry have embraced the technology.
One of the most promising areas for color vision is the pharmaceuticals industry, where various products are color-coded to indicate their formulation, strength or brand. Pharmaceuticals manufacturers have used color vision technology successfully to perform safety inspections, such as checking blister packs containing tablets to ensure they contain the correct color tablets.
Color machine vision also has proved useful for solving applications that aren't obvious candidates for color inspection. For instance, the technology is now used to inspect electrical leads -- which have tips coated with gold -- to make sure that the correct area of the lead is coated. Because of the way light reflects off metal, grayscale vision systems can't distinguish between the lead and the gold coating. Advanced color machine vision systems, however, can tell the difference between the metals, changing this application from impossible to easy.
Automotive quality engineers -- who already use machine vision technology to inspect brake pads, radios, airbags and many other products -- have found that color vision tools can solve problems that previously required human inspectors, such as verifying that color side-view mirrors are assembled on the correct car body. In the white color family, for example, shades might include white, off-white, champagne, pearl and cream. Human operators often mismatch these colors, while color vision tools can distinguish more reliably between them.
As the above examples attest, color vision systems improve on grayscale machine vision technology, bringing the full spectrum to bear on color verification, sorting and inspection. Advances in both machine vision technology and related software tools have enabled manufacturers to apply color machine vision on the factory floor in real time. This technology also can solve problems formerly restricted to manual inspections. Once a futuristic concept, color vision systems have evolved into practical and cost-effective additions to current manufacturing.
About the author
Susan J. Keirouz is product manager at Cognex Corp., a leading supplier of machine vision systems. She can be contacted by fax at (508) 650-3344 or via e-mail at skeirouz@qualitydigest.com . |