Easy Auditing
Michael J. Cleary, Ph.D.
mcleary@qualitydigest.com
Rock DeBote, CEO of Greer Grate
& Gate, calls it good news. Hartford Simsack, quality
manager, calls it rotten luck. The company is about to undergo
an ISO 9001 audit, and DeBote anticipates that with the
preparation the company has given to the audit, it will
all go swimmingly. Simsack, wondering how he’ll ever
be able to respond to any serious questions relating to
SPC, just wishes it would all go away.
Unfortunately, Les Ismore, who’s been responsible
for all gage calibrations and inventories, has recently
left the company for a position with another organization.
DeBote has suggested that Simsack temporarily take over
Ismore’s responsibilities, at least until after the
audit. “We don’t have time to train someone
new,” DeBote points out, not realizing that Simsack
himself knows nothing about gage management and precious
little about SPC. So far, he’s managed to disguise
the paucity of his statistical understanding with language
garnered from his mentor, Dr. Stan Deviation. Simsack is
in trouble.
Hastily leafing through a catalog of workshops offered
by the local community college, Simsack is relieved to see
that a seminar on gage management, taught by
Professor Cal Ebbrate, is scheduled for an evening session.
“Perfect,” Simsack says. He arrives at the seminar
ready to take notes so he can at least use the terminology
to impress his colleagues and win over the auditors. His
concentration, however, is somewhat flawed, compounded by
the fact that the class takes place in the evening—and
by his propensity not to pay attention to lectures.
Professor Ebbrate, discussing the uses of R&R, points
out that systems which correctly utilize the power of R&R
are far more likely to pass their audits. Simsack is suddenly
alert. “I knew I’d get something out of this,”
he mutters to himself.
The next day, Simsack returns to GG&G and schedules
a meeting with DeBote to review the requirements for the
upcoming audit and the strategies his company will pursue
to ensure success. “We need to have the entire quality
department experience R&R” (which he assumes means
rest and relaxation), Simsack asserts. “Professor
Ebbrate says it’s the most useful thing we can do,
and I know that the best advice to someone preparing for
a test is to get enough rest, so I’m sure this will
help.” DeBote is somewhat dubious but nonetheless
listens and reluctantly agrees when Simsack suggests a day
at the beach for all employees.
Where does Simsack’s suggested strategy fall?
a) Into the catcher’s glove
b) Near the left field bleachers
c) Out of the ballpark: It’s such a good idea that
it will be a home run for the company.
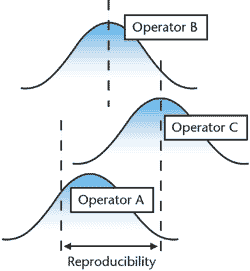
The answer is b. Simsack has hit a foul ball. His habit
of depending only on terminology without understanding its
meaning has created a monster.
R&R studies, of course, refer to “repeatability
and reproducibility,” not “rest and relaxation,”
and they play a key role in any gage management system.
Repeatability is the “variation in measurement obtained
with one measurement instrument when used several times
by an appraiser while measuring the identical characteristic
on the same part” (Measurement System Analysis, AIAG,
1995, p. 17).
“Reproducibility,” according to the AIAG source
cited, “is the variation in the averages of the measurements
made by the different appraisers using the same measuring
instrument when measuring the identical characteristic on
the same part.”
A typical test for repeatability includes having two operators
measure five identical parts three times each and then creating
a range chart for all 10 trials. If the range chart is in
control, the gage’s repeatability can be calculated.
The estimate for the standard deviation for repeatability
is:
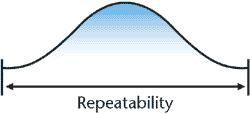 
Where R is the average range from the study, d 2* is the
weighting factor derived by the number of trials taken,
the number of parts and the number of appraisers. The larger
the se, the less the repeatability of the instrument. For
a more complete explanation of repeatability and reproducibility,
see the AIAG manual referred to above.
Michael J. Cleary, Ph.D., is a professor emeritus at Wright
State University and founder of PQ Systems Inc. He has published
articles on quality management and statistical process control
in a variety of academic and professional journals. Letters
to the editor regarding this column can be e-mailed to letters@qualitydigest.com.
|