by Jeff Wilkinson
Wireless in Action
This following wireless application takes place at a milling operation on a 360,000 square foot shop floor. Each of the shop's 12 milling stations requires four digital micrometers during the inspection process. The plant currently has 12 wireless micrometers, enough for three stations to perform inspections concurrently. Micrometers are moved between stations as required. Each micrometer is outfitted with a radio that sends data to the manufacturing office at the other end of the building. The previous approach used a PC on a cart rolled around to each station, where the operator took 30 data points manually. The operator stopped measuring after every five points and entered data from memory by typing it into a spreadsheet. With a wireless system, the operator takes all 30 measurements without stopping and doesn't have to hand-type any data. Because the data are sent to the manufacturing office wirelessly, there is no need to roll a PC on a cart to each station hourly. All stations can now send data simultaneously.
|
Lord Kelvin's quote, "If you cannot measure it, you cannot improve it" holds true in quality circles and drives data-collection processes throughout all aspects of a modern production operation. With Six Sigma and customer-specific quality audits, SPC professionals are increasingly faced with initiatives and measured goals that require continuously improving quality. At the same time, manufacturing is under intense competitive pressure to increase throughput and reduce cost.
These factors create an inherent conflict between quality and manufacturing goals: quality assurance's time-intensive data collection vs. manufacturing's need to increase throughput. For many applications, automated data collection is the answer.
Automated data collection isn't new. It has evolved to include a wide variety of portable and fixed-data collectors with tools and sensors wired to a collector or a host computer. Fifty tools or more can be wired to a single collector, allowing for a centralized data-collection point.
However, centralization has substantial costs. Collector and peripheral expansion units require a significant investment. Then there 's the mass of wires tethering each measuring device. This article will explain the advantages as well as the unique challenges of implementing a wireless data-collection system in the shop floor environment.
Whenever wires are attached to measuring tools, there are safety factors to be considered. For instance, one application involves a large cylindrical casting requiring frequent measurements. The casting is four feet in diameter and requires several machinists taking measurements. In the wired application, cables of 50 feet are used. The cables are often damaged or snagged by forklifts and/or personnel walking through the area. Aside from the tripping hazard, a snag could pull the tool into a lathe chuck or drag other bench tools to the floor, causing damage to tools or, worse, an injury.
Efficiency and convenience are also considerations for eliminating the wired data-collection systems. A typical quality assurance bench in a lab can have four to six tools wired for data. During a measuring sequence, the tools can easily become tangled. This is even more likely with an online inspection application where managing data cables slows the ability to measure a critical parameter.
The solution to the wired mess is to get rid of the wires. After all, most of us are already unplugged. We talk on our cell phone while we access our e-mail with our laptop through a wireless local area network, so why not use the same technology to let our gages take measurements and wirelessly communicate the data back to a centralized data collector?
In a manufacturing environment where inspectors may use gages from several different vendors and interface with a variety of different software packages, the solution isn't as simple.
All radio transmissions are prone to disruption due to radiated electro motive force (EMF). Radiated interfering frequencies, competing frequencies within the operating frequency band and fade are the most common disturbing effects. With this physical limitation of radio waves, wireless data-collection systems must effectively deal with radiated noise without corrupting the data to be sent.
In addition, when multiple radio systems are operated in close proximity, the data may be transmitted successfully but can be received by the wrong recipient collector, thus corrupting the data set of the wrong collection system while "losing" data for the intended collection system.
A wireless system design that anticipates the limitations of the RF (radio frequency) world can achieve very high reliability and extraordinary data integrity, and can equal the reliability of wired data collectors.
If all atmospheric and factory operation conditions were ideal, a point-to-point radio system would work well as long as the transmitter and receiver were within an adequate fade range. However, these conditions exist infrequently. In reality, manufacturing environments include induction hardeners, magnetizing fields, rotating spindles and high-power motors, all of which generate significant EMF fields that can disrupt normal radio transmissions. Most quality inspection labs are not adequately shielded from EMF and other noise components, so robust and reliable data-collection networks are paramount.
There are a number of techniques that can be implemented to ensure robust data transmission and data-collection performance in an otherwise RF-hostile environment. Unfortunately, most radio systems are insufficient for industrial applications, especially statistically significant data-
collection applications.
The wireless system should be easy to install, set up and operate. It should have built-in diagnostics and performance monitoring so that the operator and/or administrator can determine if there are offending disturbances in the environment causing diminished system function. Useful parameters would include battery voltage of the radios attached to the tools or sensors (i.e., endpoints), aggregate functioning of the radio network, tracking and recording lost or dropped measurements, an indication of the number of "retries" the system must make to ensure safe arrival of the data and warning messages of marginal operating conditions. These factors would provide the information required to tune the system in advance, before invalid data would be collected. The pairing of the host data collector and endpoints for measurement should be configured so that they can be flexible, robust and adapted to the varied shop floor layouts. Overall reliability of the system shouldn't be compromised when long distances are involved.
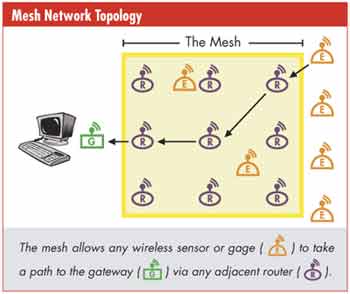
The mesh network topology (see figure above) stands out as a robust approach to covering large areas with radio connectivity. This type of network is similar to a cell phone network, with multiple transmitter/receivers (i.e., routers) relaying data throughout the shop floor. The robustness offered by the mesh network topology can't be equaled by any of the other common network topologies. In the world of "wired" networks, the mesh topology proves more expensive because of the large number of cables and connections required. However, when employing wireless communications with radio devices equipped with the right antenna at each network node, the network topology inherently becomes a low-cost mesh network.
In a mesh network, the reach or range can be extended, redundancy added and the general reliability of the network enhanced by simply adding more routers. This may be needed to provide a best route for the radio signal, thereby increasing throughput and reducing congestion. All routers in a mesh network can communicate with two or more other routers. If one radio/network node can no longer operate, all the rest can still communicate with each other, directly or through one or more intermediate nodes. This precludes the practicality of point-to-point or daisy-chain network approaches (see figure below). The latter has a single point of failure. If one router in a daisy-chain configuration ceases to function, there is no capability for the network to recover. Therefore, the data to be sent will never reach their destination. Mesh networks "self-heal" in that if interference enters the environment, such as a large EMF plume from an induction hardener, the network has alternate paths for the data to traverse. In this way, data can reach their intended destination.
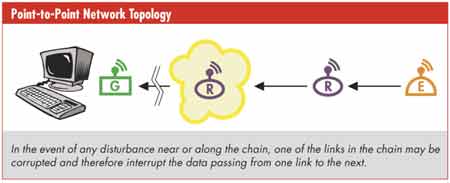
The transmitters (i.e., radios) that attach to the measurement tool (i.e., caliper, micrometer, height gage, etc.) should be built to withstand the hazards of industrial shop environments. Coolant and crush resistance are two critical criteria. The radios should be very low power to keep the battery and the radio small, and have long battery life. Ideally, these radios should also have some capability to indicate to the operator that the data have not only been sent to the SPC collection point, but also that they were received by the collection point. Other useful indications include an audible or visual indication when something is wrong with the system (e.g., an entire production shift of data-taking is not lost if the host SPC collection point has had its power turned off). Without this kind of enunciation, a remote operator would have no idea that the collection system is down.
The radios must be able to connect to gages from a variety of manufacturers (e.g., Starrett, Mitutoyo, Brown & Sharpe, Bowers, Sylvac, etc.). The common data- collection platform must adapt to various connector styles and electrical signaling for successful integration.
Other useful features are the ability to record data from other sensors, with that data bound to the measurement taken. For instance, ambient temperature often has a pronounced effect on the accuracy of linear and volumetric measurement, so it would be highly desirable to have the endpoint collect a measured parameter and the ambient temperature at the same time.
From the host or receiver end of the system, a flexible interface to legacy or installed SPC software is paramount. Simply adding a wireless collection system should not cause the user to re-invest in SPC software. Further, the wireless data-collection system should be able to communicate with a company's database directly or export data sets via flat file in a universal file format (e.g., TSV, CSV, XML or XLS). Hardware connectivity should also be flexible and compatible with existing SPC infrastructure, so that re-tooling or an engineered system approach is unnecessary. Examples of this would be USB, Ethernet or RS-232 interfaces.
The whole system of transmitters and receivers should have capabilities that avoid or compensate for the known types of interference typical to radio systems. Some of these are RF modulation schemes, the RF frequency, network topology, and error-detection and correction schemes. The system must be adaptable to existing infrastructure, from both the hardware and software perspectives. It must be mechanically robust to survive harsh production environments. The system must provide useful information about data-transmission status and the general health of the system. It must also be unobtrusive to the user both from a user-interface perspective and ergonomically.
One issue that hasn't been resolved is the compatibility of wireless systems from various manufacturers. Most are proprietary in some ways. Although there is some push for standardization, work still needs to be done in this area. Simply speaking, if you choose to go wireless, make sure the system meets all your needs because it may not be easy to integrate a wireless system from a different manufacturer should yours fall short of expectations.
Obviously, some design approaches are better than others, but with a careful review of these capabilities, needs and options, a quality-conscious organization will select a robust and predictable wireless data-collection system.
Jeff Wilkinson is the general manager of The L.S. Starrett Co.'s Advanced Technology Division, where he is responsible for the oversight of operations and is a key developer of many of the company's newest products. During his career, Wilkinson has successfully delivered more than 200 products to market, is a published author and holds three patents. He is the former director of research and development for Nokia Inc. QD |