Job
Satisfaction at Record Low
According to a recent survey
from The Conference Board, less than half of all Americans
are satisfied with their jobs--the highest level of discontent
since the survey was first conducted in 1995. The decline
in job satisfaction is found among workers of all ages across
all income brackets and regions.
“The level of job satisfaction has been steadily
on the decline since reaching nearly 59 percent in 1995,”
says Lynn Franco, director of The Conference Board’s
Consumer Research Center. “As technology transforms
the workplace--accel-
erating the pace of activities, increasing expectations
and productivity demands, and blurring the lines between
work and play--workers are steadily growing more unhappy
with their jobs.”
The survey found that Americans are most satisfied with
their commutes, a finding that mirrors last year’s
survey results. Only one in five workers is satisfied with
promotions and bonus plans, and only about one in three
is content with wages. Educational and training programs
are also near the bottom of the list.
Those aged 45 to 54 express the least amount of satisfaction.
Only 46 percent say they’re satisfied with their employment.
Those 65 and older claim the greatest level of satisfaction,
54 percent.
The survey shows that satisfaction levels tend to rise
with earnings. Households earning less than $15,000 are
less satisfied with their employment than those earning
in excess of $50,000. Among high-end earners, the overall
level of satisfaction has fallen over time.
In 1995, 66.5 percent of households earning more than $50,000
claim to be satisfied with their jobs compared to 53.4 percent
today.
Regionally, the differences are very pronounced. Workers
expressing the least amount of satisfaction (about 43 percent
claiming to be satisfied with their jobs) reside in New
England and the West South Central states. Residents of
the West North Central states are the most satisfied; nearly
55 percent responded that they are satisfied.
Key findings include:
The largest decline in overall job satisfaction--from 60.9
percent in 1995 to 47.2 percent this year--occurred among
workers aged 35 to 44. This group was once the most satisfied.
The second largest decline took place among workers aged
45 to 54, with the satisfaction level dropping from 57.3
percent to 46.1 percent. This group recorded the lowest
level of satisfaction.
The overall level of satisfaction among households earning
in excess of $50,000 has declined from 66.5 percent o 53.4
percent, yet they still remain the most satisfied.
Among households earning less than $15,000, there was no
change in the level of satisfaction. Currently, 45.4 percent
claim they are satisfied, the same proportion as eight years
ago.
With 43.2 percent of households claiming to be satisfied
with their current job vs. 59.7 percent in 1995, residents
of West South Central region are among the least satisfied
in the nation.
New England residents are among the least satisfied in the
nation. Only 43.5 percent claim they are satisfied with
their jobs, down significantly from 65.4 percent eight years
ago.
Promotion policies were the least satisfactory benefit of
employment. Only 20 percent claim they are satisfied, down
from 23.4 percent in 1995.
Bonus plans received poor ratings. Only 20.1 percent claim
to be satisfied with their company’s policies.
Only 29.3 percent claim to be satisfied with educational
and job training programs.
The commute to work was rated as the most favorable aspect
of one’s job, with 57.9 percent satisfied with their
travels. However, there was a decline in the level of satisfaction
from the 1995 levels.
Co-workers were given a favorable rating despite a decline
of 56 percent from 64 percent eight years ago.
Quality Digest’s Web portal, InsideQuality.com,
recently conducted an informal job satisfaction survey among
recipients of its weekly QualityInsider e-newsletter. The
results show that 36.2 percent of respondents are satisfied
with their jobs, and 20.1 percent are dissatisfied. The
percentage of those neither satisfied nor dissatisfied was
18.8.
The Conference Board survey, conduced in July 2003, is
based on a representative sample of 5,000 U.S. households.
NFO WorldGroup conducted the survey. To learn more about
the “Special Consumer Survey Report: Job Satisfaction,”
visit The Conference Board at www.conference-board.org.
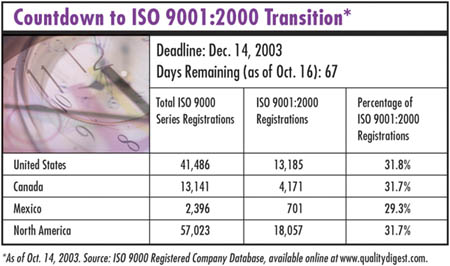
Poor Health Quality Translates to Lost
Dollars, Work Force
A new report from the National
Committee for Quality Assurance shows that the nation’s
health care system is riddled with quality gaps that prevent
millions of Americans from receiving best-practice care.
These gaps, the results of factors such as poor use of technology
and irrational payment systems, lead to more than 57,000
avoidable deaths each year and $11 billion in lost productivity.
NCQA’s
annual “State of Health Care Quality” report
also documents the enormous financial toll of commonplace
failures to deliver appropriate care. Nearly 41 million
sick days could be avoided annually if well-known best practices
were more widely adopted. The observed quality gaps were
not equally prevalent throughout the system--among health
plans that measure and report on their performance, clinical
quality was higher and showed strong gains.
“It’s not a question of knowing how to treat
heart disease, diabetes or mental illness,” says Margaret
E. O’Kane, NCQA president. “We know how. We’re
just not doing it. We’re literally dying, waiting
for the practice of medicine to catch up with medical knowledge.”
Nationwide, about 40 percent of the 31 million Americans
diagnosed with high blood pressure have their conditions
adequately controlled. An increase to 68 percent (a level
already reached by some of the nation’s top health
plans) would save an estimated 28,000 lives next year.
The loss of life is compounded by the financial costs
the nation pays for gaps in health care. U.S. hospitalizations
due to avoidable heart attacks cost more than $1.6 billion
a year, according to the report.
The economy also suffers through lost days of labor each
year. According to NCQA, the system’s failure to treat
five health care conditions--asthma, depression, diabetes,
heart disease and high blood pressure--is responsible for
nearly 41 million sick days. This translates to the equivalent
productivity of more than 173,000 workers and annual costs
to U.S. companies of more than $11.5 billion.
The NCQA notes that one reason for the failure to apply
best practice care is that payment systems may discourage
it. Physicians and hospitals are compensated based on the
amount of care they provide, thus discouraging the use of
new treatments and therapies that may send patients home
sooner, the report contests.
“We’re throwing up roadblocks to quality when
we should be giving out rewards,” says David F. Durenberger,
former U.S. senator and chairman and CEO of the National
Institute of Health Policy. “We have to start asking,
‘What are we buying?’”
Peter V. Lee, president and CEO of Pacific Business Group
on Health, agrees. “This report underscores that employers
and consumers are not getting the quality of health care
they’re paying for,” he argues. “The path
to saving lives and money lies not in finger-pointing but
in finding out who’s doing it right and sharing that
information with those who want to do it better.”
The report did find some encouraging statistics. NCQA
reports that the quality of clinical care improved for health
plans serving the commercial, Medicare and Medicaid sectors.
It’s the fourth consecutive year that screening and
control of heart disease has improved. Additionally, health
plans serving Medicaid and Medicare beneficiaries demonstrated
gains in cholesterol management.
“The State of Health Care Quality: 2003” is
available at NCQA’s Web site, www.ncqa.org.
An expanded version of the report will be added to the Web
site by the end of the year.
Synchronization Issues Dimming Electrical
Industry Profits
Data exchanged between manufacturers
and distributors in the electrical industry contain significant
errors, according to a report released by the Industry Data
Exchange Association. The report was the result of a study
to determine the level of synchronization of item data exchanged
between manufacturers and distributors in the industry.
Its findings are similar to those of an earlier study by
the Automotive Aftermarket Industry Association that concluded
the automotive industry was losing $1.7 billion due to item
data errors.
The data synchronization study demonstrates that there’s
variance between the trading partners’ item data,
causing significant financial supply chain problems. According
to the study, 60 percent of the items submitted by manufacturers
don’t accurately match those in their trading partners’
files, costing companies hundreds of millions of dollars
in increased transaction costs and lost sales.
The study focused on identifying specific data issues
between pairs of trading partners (i.e., a manufacturer
and one of its distributors). Ten leading manufacturers
and eight distributors participated in the study. The trading
partners’ data were matched on UPC code, part number,
order quantity, unit of measure, distributor pricing and
trade pricing.
“We’re glad that we participated in the pilot
program because the results have enabled us to take immediate
action and create a program to clean up our business data
errors,” notes Ron Schlader, vice president of operations
and quality for Crescent Electric Supply. “We’re
creating processes to ensure that we continuously exchange
good quality data with our trading partners, thus saving
costs for the whole supply chain.”
Results from data synchronization studies in multiple
industries support the electrical industry findings. An
earlier report by IDEA and the National Electrical Manufacturers
Association revealed that product and pricing inaccuracies
cost manufacturers and distributors 1 percent and 0.75 percent
of sales respectively. In a study for the grocery industry
released last year, AT Kearney announced that 30 percent
of items in retailer item files were in error and that the
consumer packaged goods industry alone is losing $40 billion
in sales every year due to poor product information.
As a result of the study findings, IDEA has implemented
a data audit certification program. “The study reveals
that the electrical industry faces a significant challenge
in achieving and maintaining data synchronization,”
says Mike Rioux, president of IDEA. “Recognizing the
high cost of this critical business issue, the IDEA board
of directors approved the implementation of an audit program.
Profile Systems was selected to provide the data audit services
for IDEA with the objective of ensuring that accurate, valid
data is exchanged between trading partners in the industry.”
Profile Systems, an IDEA technology partner, was authorized
to perform the data synchronization analysis to help illustrate
the effect of data synchronization on the industry.
To learn more about the study, visit www.idea-inc.org
or www.profilesystems.com.
Report Reveals Pharmaceutical Best Practices
The most efficient way to avoid
Food and Drug Administration scrutiny in the pharmaceutical
manufacturing quality control process is to create well-trained
and knowledgeable staffs, according to a study from pharmaceutical
research firm Best Practices LLC.
“The Quality Function: Structures, Staffing and
Execution” illustrates quality training techniques
used by pharmaceutical leaders. Additionally, it reveals
benchmark trends in quality organizations, staffing and
execution at some of the world’s preeminent pharmaceutical
and biotech firms.
For example, one benchmark firm ensures it has a well-trained
staff by requiring potential quality auditors to follow
a three-month training period with certified auditors to
gain experience. Following training, auditors also undergo
annual compulsory refresher courses. Additionally, 40 percent
of this company’s employees have 11 to 20 years of
quality experience.
“Savvy companies recognize that properly trained
quality auditors can prevent internal issues from becoming
external problems,” says Keith Symmers, vice president
of Best Practices. “Trained manufacturing staff can
proactively identify potential problems long before a regulatory
action or patent safety issue emerges.”
The study also describes ways manufacturers can determine
appropriate budgets and resource allocations; implement
process improvements; increase productivity and performance
measurements; and design a plan of action for quality management
systems.
To download a summary of “The Quality Function:
Structures, Staffing and Execution,” visit www3.best-in-class.com/rr214.htm.
NIST Aims to Improve Metal Stamping for
Manufacturing
The National Institute of Standards
and Technology has set out to cut manufacturing costs through
improved sheet-metal cutting.
According to NIST, each year millions of dollars are lost
on delay-causing errors in the design of dies used to make
sheet-metal parts, ranging from car hoods to airplane wings.
The U.S. automotive industry spends $700 million on designing,
testing and correcting new dies for its latest models, each
containing about 300 stamped parts shaped by dies and presses.
About half the total cost goes to remedying unanticipated
errors--manifested as wrinkles, splits, excessive thinning
or other defects.
By fitting NIST’s metal-stamping test station with
an X-ray stress measurement system, the Institute’s
materials scientists are able to make detailed maps of stresses
and strains as sheets of steel and other metals are punched,
stretched or otherwise shaped to achieve the desired part
geometry.
According to the project leader, Tim Foecke, the system
can measure stress and strain behavior in different directions
while the sheet is being stretched in two directions simultaneously,
a condition most commonly seen in forming operations. Current
methods extrapolate from strain measurements taken from
tests that stretch the sheet only in one direction. As a
consequence, newly designed dies must often undergo successive
rounds of refinement to correct simplifications in computer
models.
U.S. automakers and producers of steel, aluminum and other
metals, including developmental ones, are supplying Foecke’s
team with samples for testing and evaluation. The project
will result in a database of materials’ properties
that designers can feed into computer models for predicting
whether would-be dies can form particular metals into specified
shapes. Project findings might point the way to new metal-forming
methods.
To learn more, visit www.nist.gov.
APQC Conducting Three Best Practice Surveys
The American Productivity and Quality Center, on behalf
of the Information Work Productivity Council, is conducting
a series of surveys to identify best practices and measurements
for three work areas.
Upon completion of the surveys, APQC will analyze the
results and develop a set of best practices. The final results
will be published in a research report and distributed to
IWPC members and organizations that complete one of the
surveys. All research data is confidential, and participating
company names will not be published.
The three studies are:
Global collaboration within product and service management
teams study. APQC will identify key drivers for and
challenges to successful global collaboration among geographically
dispersed management teams. The study will also provide
a model and measures for assessing an organization’s
effectiveness in using virtual product or service management
teams based on the best practices and benchmarks identified.
Furthermore, it will serve to establish thought leadership
on the nature of information work for global collaborators
and identify enablers and inhibitors to productivity.
Customer feedback study. This study will enable
rapid implementation of improvement recommendations by applying
best practices and lessons learned. It will also establish
thought leadership on the nature of information work for
new product developers and identify enablers and inhibitors
to productivity. In addition, the survey will help develop
a model and measures for assessing a company’s effectiveness
in using customer feedback on best practices and benchmarks
identified.
Personal knowledge management study. Participants
of this survey will help identify the tools and processes
that individual information workers use to effectively manage
work-related personal information and knowledge. The study
will discuss how tools and processes affect how productively
workers manage work-related personal information and knowledge,
as well as define measures to gauge how information workers
manage work-related personal information and knowledge.
To participate in any of the surveys, visit www.apqc.org
or call (713) 685-4717.
INDUSTRY NEWS
Stranaska Calibrations LLC has changed its name to Refmacal
Labs LLC. The company still provides the Stranaska series
of UV/VIS absorption spectrophotometer calibration measurement
standards, which are patterned after and traceable to standards
of the National Institute of Standards and Technology. Refmacal
Labs will continue operations at the same location in Fort
Collins, Colorado. To learn more, visit www.refmacal.com.
Sigma Breakthrough Technologies has hired three new executive
directors: Michael Brennan, Richard R. Scott and Ian Wedgwood.
Brennan has been a senior consultant and project manager
with SBTI since 2002, specializing in strategic planning,
training in Six Sigma and design for Six Sigma. Scott has
been with SBTI since 1999 as a senior consultant and program
manager. He assumed the role of program manager for SBTI’s
Master Black Belt Program in August 2003.
Wedgwood has been with the company since March 2001 as
a product manager and master consultant.
The executive directors will work with clients, consultants
and staff to ensure smooth operations, excellent communications
and business development. For more information, visit www.sbti-hq.com.
Many financial services organizations have begun using
Six Sigma to improve customer satisfaction, achieve high
levels of process performance and identify cost savings.
As a result, many of these companies’ peer organizations
are looking toward them as examples. To help explain the
process of Six Sigma in a financial services setting, a
forum will be held Dec. 1 and 2 at the Marriott Marquis
in New York.
Six Sigma Strategy in Financial Services Forum will provide
insight into Six Sigma implementation; ways to quantify
and reduce defects in the financial services value-chain;
strategies to increase productivity; determining whether
the organization is ready for Six Sigma; and other topics.
To register, visit www.srinstitute.com/cg102.
PQ
Systems will provide immediately accessible quality expertise
through an expanded online advisor service. The site offers
responses to questions and articles on capability, statistical
process control, measurement systems analysis, Six Sigma
and design of experiments, among other topics. The quality
advisor also offers forums for users with specific questions
and an article library.
Visitors to the online advisory service will be able to
secure assistance and advice from quality experts such as
Michael J. Cleary, Gordon P. Constable, Sally J. Duncan,
Jackie Graham and Matt Savage. All experts are PQ Systems
consultants with a wide scope of knowledge and experience.
To access the service, visit www.qualityadvisor.com.
The
National Institute of Standards and Technology and International
SEMATECH, a consortium of global semiconductor companies,
have released the NIST/SEMATECH e-handbook of Statistical
Methods. The handbook, available for free on CD-ROM, complements
the NIST/SEMATECH Web-based guide released in July 2002.
The new CD allows users to view the guide on their own computers
without accessing the Web site. The new CD version includes
files in printer-friendly format, complementing a comprehensive
overview of statistical methods, including experiment design,
data analysis and quality control. The problem-oriented
approach includes cases studies from the semiconductor industry
and NIST laboratories. It illustrates statistical solutions
to engineering and scientific problems.
To request the free CD version of the e-Handbook of Statistical
Methods, e-mail handbook@nist.gov
and include a mailing address. The Web version of the publication
is available at www.nist.gov/stat.handbook.
Entela Inc. has announced the expansion of its vibration
testing capabilities. Entela now offers additional vibration
capacity as a result of its new 6,600 lbf shaker with 2
in. stroke. Entela’s shock testing capability has
increased accordingly to 50G, 11 ms pulses with an estimated
200 lb payload in vertical axis. An environmental chamber
is being added to the system to allow for rapid-transition
thermal cycling during vibration in all three axes.
The shaker is appropriate for industries including automotive,
consumer products, furniture, industrial, medical and aerospace.
Entela Inc. provides full product, systems and material/component
testing, failure analysis, multistandard global conformity
assessment, management system registration, engineering
services, accelerated testing and failure mode verification
testing. Visit www.entela.com
for details.
|