newsdigest
by Dirk Dusharme
Supplier Audit Confirmation is the latest twist to ISO 9000 registration.
Proposed by David Ling, an ISO 9000 program manager with Hewlett-Packard,
SAC seeks to limit the scope of ISO 9000 third-party audits at eligible
companies.
Since its introduction last November, SAC has gained the endorsement of
more than 50 companies worldwide, including Hewlett-Packard, Motorola, Xerox,
National Semiconductor, Varian Associates and Sun Microsystems. Several
registrars have also agreed to try SAC on a pilot basis.
In practice, SAC proposes that registrars issue an ISO 9000 certificate
based on a third-party audit of a company's management review system, internal
audit processes and corrective action processes (three of ISO 9000's 20
elements that Ling refers to as ISO 9000's engine) and by acceptance of
the company's internal audit of the remaining ISO 9000 elements.
Acceptance of internal audits should cut back on the amount of money and
manpower companies spend on registration. More important, companies gain
greater flexibility in tailoring processes to meet customer requirements,
says Ling. He stresses that there is nothing groundbreaking about any of
this.
"The International Accreditation Forum's position is that this methodology
is allowed under the EN45012 guidance document and that the registrar has
the discretion to allow this methodology based on the supplier's maturity
and the internal audit process," Ling points out.
Perhaps the central issue driving SAC and one of Ling's biggest complaints
is that for companies with multiple sites, registrars require a complete
audit of each site seeking a certificate if those sites do not have a common
quality system in place.
"They are turning a blind eye to the internal audits," says Ling.
"They should leverage off the internal audits. They can verify that
we are doing competent audits, even conduct a few themselves to make sure
that we are competent. But to not even look at the data that already exists
and say that we have to do it independently, all over again, site by site,
is ridiculous."
Not so, says John Souter, divisional director of quality and information
systems for registrar BSI Quality Assurance, which doesn't, as yet, accept
the SAC route to certification.
"A company's internal auditors are rarely full-time, rarely professional
capacity and rarely have the experience, authority and initiative to do
the kind of things that external auditors do," argues Souter. "If
they did, then why would external auditors write up so many nonconformities?
There is something somehow not right in thinking that a process is useful
that simply inspects what the internal auditor has done."
But where is the added value in a registrar redoing what internal auditors
have already done, asks Ling. Souter responds that registrars add value
by identifying genuine areas for improvement in the client's quality and
business systems, helping the client understand solutions to identified
problems and helping the client take ownership of problems. This can't take
place if the registrar simply rubber-stamps a company's internal audit,
claims Souter.
For companies like Motorola, SAC's value is obvious. The electronics and
telecommunications giant plans to register about 30 more sites, says Dale
Misczynski, corporate vice president and director of quality and standards
at Motorola. The company is currently involved in a pilot with KEMA Registered
Quality and Lloyds Register Quality Assurance that could keep the company
from having to undergo a complete third-party audit at each site.
Beginning October 1, Motorola will give a copy of the results of every Quality
System Review and all corrective actions to the registrars. Registrars may
choose to witness or participate in site QSRs on a sample basis-30 percent
of the sites per year. The registrars will use the QSRs, sample audits and
audits of a site's management review system, internal audit processes and
corrective action processes to determine whether a site can be registered.
SAC Supplier Eligibility Requirements
The supplier is recognized among the leaders for customer satisfaction.
The supplier has an operational, formal documented quality system that encompasses
the ISO 9000 standard and an effective internal audit system where competent
internal lead auditors and internal auditors assess the quality system.
The supplier has a culture of senior- and middle-management participation
in the quality system, where management establishes policies and procedures
for continuous improvement.
The above must be demonstrated to the registrar for approval by objective
evidence:
Third-party ISO 9000 certificate achieved and maintained within the quality
system.
"Preferred Supplier Status" or winner of industry-recognized quality
awards.
Long-term continuous improvement in its quality measures.
Source: Condensed from "(DRAFT) The Supplier Audit Confirmation (SAC)
Route," Rev. 0.3, July 1995, David Ling, Hewlett-Packard Co.
Oregon Offers Quality Training Statewide
A new, ambitious program will allow all Oregon businesses to avail themselves
of a standardized set of quality courses offered through the state's 16
community colleges. The program is particularly important to a state where
90 percent of the businesses have fewer than 100 employees, says Ron Hulett,
director of the Training and Economic Development Center at Chemeketa College
in Salem, Oregon.
"A lot of these companies can't afford a comprehensive quality program,"
explains Hulett.
The program began two-and-half years ago with a $390,000 grant from the
Oregon Economic Development department, matched by funds from business partners.
Working with representatives from organizations such as the American Electronics
Association, Society for Manufacturing Engineers, Motorola and Saturn, organizers
developed a comprehensive quality curriculum called P4Q.
P4Q is comprised of 17 course modules, ranging from a four-hour quality
overview course to a 32-hour statistical process control course. Other courses
include ISO 9000, teams, just-in-time, strategic planning and cycle-time
reduction. Courses can be delivered on-site and cost about $100 per course
hour. Only 12 of the 17 modules are finished, but Hulett expects the entire
curriculum to be finished and available to all 16 Oregon community colleges
by October 1.
The beauty of the program, says Hulett, is that it is a statewide program
with certified instructors all trained in the same curriculum.
"This will benefit Oregon companies that have multiple outlets like
Fred Meyer or Payless Drug stores," explains Hulett. "Their managers
or employees will get the same type of teamwork training no matter where
they live."
The program was developed through the Oregon Advanced Technology Consortium,
which hopes to market the curriculum nationwide.
For more information, contact Ron Hulett at Chemeketa Community College,
(503) 399-5181.
Feds Cut Red Tape
Has Vice President Al Gore's National Performance Review lived up to its
promise to cut red tape and streamline the federal government? Maybe, at
least some of it.
In reports submitted on June 1, federal agencies told President Clinton
that they propose to get rid of 16,000 pages of outdated or unnecessary
rules on U.S. businesses and the public, according to the National Performance
Review's newsletter "Reinvention Roundtable."
Federal workers from 35 agencies reviewed 86,000 pages of government regulations
and held more than 250 meetings across the country to create grassroots
partnerships with those affected by regulations. The result was the elimination
of thousands of pages of unnecessary "bureaucratese," including
the following:
All agencies-except the Internal Revenue Service-will cut regularly scheduled
reports in half and allow regulators to waive fines where small businesses
have unwittingly violated rules.
The Social Security Administration will stagger payments for new beneficiaries
throughout the month instead of the third day of each month, thus eliminating
workload spikes.
Veterans Affairs will simplify the eligibility criteria for veteran's medical
care, including cutting the eligibility form from 93 questions to four.
The IRS, Labor Department and Social Security will streamline tax reporting
by allowing taxpayers to file just one report. The agencies will share the
information with each other.
Maintenance Tips From Mack Trucks
At Mack Trucks in Hagerstown, Maryland, total productive maintenance training
has turned every machine operator into a maintenance technician. The Hagerstown
facility, which manufactures diesel engines and transmissions for Mack vehicles,
recently won Maryland's U.S. Senate Productivity Award.
"We teach that TPM makes every operator a partner with maintenance
15 to 20 minutes a day," says Clancy Pugh, manager of facilities at
the 1,200-employee site.
Since September 1993, more than 240 operators have received 40-hour TPM
training. In the same time, operators have identified 1,792 equipment abnormalities
and corrected 1,642.
Here's a few TPM tricks used at Hagerstown:
Next to each piece of equipment is a bulletin board with a photograph of
the equipment. Arrows from each machine maintenance point lead to close-up
photos showing that point being serviced and a written description of what
service is required (lubrication, for instance).
To track maintenance, each board also contains a peg area with holes for
each day of the week and each shift. After every scheduled maintenance,
operators put a peg in the appropriate hole, notifying others that maintenance
has been performed. Pegs are cleared weekly.
Operators submit suggestions on how to improve machine operation or environment.
By June 30, Hagerstown had implemented 237 of 296 improvement bulletins.
Hagerstown routinely performs random equipment maintenance audits. The number
of machine demerits is based on how well a maintenance item checks out multiplied
by the importance of the item. TPM training and operator feedback have reduced
demerits from an average of 1,500 to an average of 460 per machine.
JAB Pulls Proposed Standard
During a meeting with the American National Standards Institute held late
last August, the Japanese Accreditation Board agreed to kill their proposal
for an ISO-9000-type standard tailored specifically for software products.
The proposed standard raised tremendous furor among U.S. software manufacturers
who viewed it as a Japanese trade barrier.
The agreement, signed by ANSI President Sergio Mazza and JAB Executive Director
Takashi Ohtsubo, calls for adherence to the principles and guidelines established
by the International Organization for Standardization, the International
Electrotechnical Commission, the World Trade Organization and others. ANSI
and JAB also developed a joint interpretative document laying out their
common understanding of the role of the ISO 9000 system standards and the
need to avoid unique standards and national accreditation systems that inhibit
international trade, says Dale Misczynski, corporate vice president and
director of quality and standards for Motorola, who headed the ANSI delegation.
"Starting in October, you will be able to get an ISO 9001 certificate
in Japan if you are a software company," asserts Misczynski. "You
couldn't do that until this time. And it will be based on ISO 9001 by itself
without any special steps."
U.S. Ambassador to Japan Walter Mondale recognized the U.S.-Japan private-sector
efforts and called the agreement a "major step forward."
"I am confident that with JAB and ANSI working together, the implementation
of new conformity assessment programs that meet the terms of the agreement
will enhance relations between the two organizations," says Mondale.
Feds' First ISO 9001 Certification
In August, the U.S. Coast Guard Yard in Baltimore, Maryland, became the
first U.S. government organization to achieve ISO 9001 certification.
As with many private organizations, the Yard's move to earn ISO 9001 certification
was driven by the need to maintain existing customers-97 percent of which
are Coast Guard-and to attract new customers. Getting better control over
the Yard's more than 200 processes was key to that effort, and ISO 9001
provided the framework, says Paul O'Donnell, the Yard's quality officer.
"We wanted to assure our customer, the Coast Guard fleet, that we could
give them the best service," says O'Donnell. "We want to ensure
that they don't go to a private East Coast shipyard."
The Yard isn't stopping the improvement process now that they have achieved
certification, says O'Donnell. They are now looking for ways to streamline
and improve each of their 200 processes. In addition, the yard plans to
apply for the Malcolm Baldrige National Quality Award in 1998-assuming the
award includes a government category at that time. Otherwise, they will
apply for the Presidential Award for Quality.
Wanted: Baldrige Examiners
The U.S. Commerce Department's National Institute of Standards and Technology
is seeking quality experts from all sectors of U.S. business, as well as
from nonprofit health-care and education organizations, to serve on the
1996 board of examiners for the Malcolm Baldrige National Quality Award.
Applicants for the board must be experts in quality and business management,
and be able to evaluate large and small manufacturing and service businesses.
In addition, quality experts from the health-care and education communities
are needed to participate in ongoing pilot programs to determine whether
the Baldrige Award should be expanded into those two sectors.
Applications for both boards are available from the Malcolm Baldrige National
Quality Award Office, A537 Administration Building, NIST, Gaithersburg,
MD 20899-0001. Telephone (301) 975-2036, fax (301) 948-3716 or e-mail oqp@micf.nist.gov.
Applications are due Nov. 1
Managers Want Strong Work Ethic
A willingness to work hard is more important than education, according to
OfficeTeam, a Menlo Park, California-based staffing service. Nearly 60 percent
of managers in the national survey ranked "work ethic" as the
most important factor when hiring an administrative employee, assuming the
candidate has the basic skills required for the job.
"Aside from the basic skills needed to do the job, which of the following
factors is most important when hiring an administrative employee?"
Work Ethic 59%
Intelligence 23%
Enthusiasm 12%
Education 4%
Other/Don't know 2%
How do You Define Communication?
Communication is the most desired, yet least acquired tool by which we can
share with and understand one another. Benefits to quality include increased
productivity, improved customer relations and better morale among co-workers.
Communication can also serve to identify an impasse, for which an alternative
approach must be found.
-Christine M. Gibney
Manager, Quality Control
Anamet Laboratories Inc.
Hayward, CA
Communication is when both the sender's information and effect are accurately
received by the receiver as evidenced by the receiver's subsequent action.
-Dennis J. Barry
Department of Social Services
State of Connecticut
Hartford, CT
Communication is the exchange of information, ideas and thoughts between
individuals, groups and identities. Good and honest communication leaves
no gray areas for misunderstandings.
-Richard Carr
Quality Manager
Hacker Industries
Henderson, TX
Communication is the effective transfer of information between individuals
that results in a commonly shared understanding of the issues at hand.
-Kellen Wilkes
ISO 9000 Manager
Wavetek Communications
Indianapolis, IN
Each month, Quality Digest features a quality-related term as defined by
our readers. "Responsibility" is our next quality term. Fax your
definition of responsibility to us before November 1, 1995, at (916) 527-6983.
(Please make sure the definition is your own.)
Calling all news
Send us your news tips.
Is there something important happening in the quality arena? Has your company
achieved outstanding results by implementing a quality program? Let us report
it in "News Digest." Send news tips or story ideas to News Editor,
Quality Digest, 40 Declaration Drive, Suite 100C, P.O. Box 1769, Chico,
CA 95927-1769, or phone (916) 893-4095, fax (916) 893-0395 or e-mail qdnews@aol.com.
Be sure to include contact information.
Surveys Predict Boon in ISO 14000 Registration
Another registrar feeding frenzy may be on its way, this time on those seeking
ISO 14000 certification. Two-thirds of responding registrars say they believe
that nearly half of their registered clients are presently interested in
ISO 14001 registration, reveals a recent survey of ISO 9000 registration
in North America. All of those registrars plan to seek accreditation to
offer ISO 14001 registration. Both are signs that potential business abounds
for registrars, according to Irwin Professional Publishing, publishers of
newsletter "Quality Systems Update," which conducted the study.
Another survey, conducted by Lloyd's Register Quality Assurance, supports
QSU's results. Eighty-seven percent of LRQA clients' responding to their
survey said they will implement an environmental management system. Of those,
96 percent said they plan to go for ISO 14000 certification, with 58 percent
planning on doing so within the next three years, says Dave Hadlet, director
of business development with LRQA.
"Certainly the view of the registrars is that they are gearing up to
offer ISO 14000 registration," says Hadlet. "They see it as being
a significant amount of business for them. In addition, there already exists
a large, mature environmental consulting business, and I think they will
expand into environmental management systems as well."
The QSU survey also reports that 77 percent of responding registrars plan
to conduct ISO 9000 and ISO 14001 audits simultaneously, if their clients
agree to it. Sixty-three percent say they intend to use existing quality
auditors to perform ISO 14001 registrations, if possible, and 97 percent
say that any regulatory violations that turn up during an ISO 14001 audit
should be brought to the attention of the client's management.
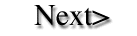