Navy Requires Quality, Lean Training
U.S. Navy leaders got an early Christmas present from the government recently: a requirement that they take a course on process improvement, lean and Six Sigma.
They had until November 30 to complete the new Fleet Business Course, an eight-hour training session in advanced leadership, lean principles, Six Sigma and theory of constraints.
“We’re providing our leaders with some inspiration and understanding, and a few tools they can use to maintain our warfighting culture, with the added dimension of business discipline,” says Rear Adm. James Winnefeld, director, Warfare Programs and Transformational Concepts, U.S. Fleet Forces Command.
Realizing the importance of educating leaders as part of the cultural change toward quality and efficiency, the Naval Education and Training Command and Center for Naval Leadership produced a computer-based training course that provides practical instruction to command-level leadership in the methodologies.
“Although the demands of our wartime footing and the need to recapitalize have spurred efforts to be more efficient, the American taxpayer rightfully expects we do so as a matter of routine,” says U.S. Fleet Forces Command Adm. William J. Fallon. “We can and will continue to exercise fiscal discipline in achieving combat readiness by undertaking a fundamental change in culture, one that incorporates a continual, rigorous evaluation of the costs in preparing for combat, and the assumptions that drive those costs.”
Commanding officers, executive officers, department heads, command master chiefs, chiefs of the boat and senior enlisted advisors are currently required to take the course. However, Winnefeld reports that the Navy may extend the course requirement to other personnel.
As part of the effort to improve processes, the Fleet Forces Command also established a business practices Web site, which serves as a central repository of information on fleet business strategies and policies, recommended reading, links to other valuable sites, and a Web-based system to collect and disseminate best practices from the fleet and reward personnel for innovative strategies.
“This is not just… another new leadership technique or applying the latest business trend,” Winnefeld says. “This is about sailors getting fired up to learn about being smart businesspeople and applying best business practices and ideas to improve the way we use the resources entrusted to us for our nation’s defense.”
For more information, visit www.news.navy.mil.
Does Cheap Registration Cheapen Registration?
A low-cost, controversial new method of renewing registrations to ISO standards--one that avoids on-site audits, and issued by a registrar accredited by an accreditation body under the same management as the registrar--is now available, but not everyone in the quality industry is convinced it’s a quality operation.
In question is American Global Standards, a Boston-based registrar that offers a registration renewal program called Virtual Cert. It’s easy and costs a flat fee of $500 per year.
But while Virtual Cert may be easy, it’s not without critics. While companies that renew their registrations this way received an on-site audit from their current registrar at some point, without another outside audit at renewal time, there’s no guarantee that the efficiency of their processes hasn’t eroded since the initial registration was granted.
Allowing registered companies to avoid on-site audits is a “slippery slope” that could threaten the quality auditing industry, says one major registrar who asked not to be named.
“There are enough fly-by-night registrars out there that one more isn’t the end of the world,” he says. “But it certainly doesn’t help the perception that auditing isn’t really necessary.”
AGS owner Stephen Keneally advertises that his service saves ISO reps time, with “no on-site audit to prepare for [and] no stupid NCRs to respond to, just send in management review and internal audit summary at your convenience.”
Keneally, who founded Scott Quality Registrars in 1992, says that he developed the Virtual Cert program at the behest of his customers, many of whom doubted the value of registration to ISO standards as its related costs increased. “The last straw for all of our customers was the requirement to ‘upgrade’ to ISO 9001:2000 or lose their certifications,” Keneally says. “Almost every customer I talk to feels the revision was a huge waste of time and money, and most importantly, manpower.”
Instead of on-site auditing, AGS clients are required to provide internal auditing reports and scheduling, proof of previous registration and proof of corrective actions. Clients also have to permit surveillance of their processes, which is done on short notice at a minimum of once every three years.
But that isn’t convincing enough for some companies that require their suppliers to register to ISO 9001.
“No way would I endorse anything like that,” says Mary Moore, Autoliv Inc. North America quality systems manager. “If all someone has to do is just send in paperwork detailing how things are supposed to be, that doesn’t tell you anything about the way they probably really are.”
The “nitpicking” nature of the auditing process isn’t the only beef Keneally has with the industry. AGS was accredited by the ANSI-RAB NAP until January 2003, when it lost its accreditation over a dispute about its registration renewal. The RAB reports that it subsequently sued AGS for allegedly “misrepresenting its authority to issue ANSI-RAB NAP-accredited certificates.”
Keneally’s company is now accredited by the American International Accreditation Organization-Bureau of Accredited Registrars, a nonprofit agency that shares the same phone number as Keneally.
The dual management of American Global Standards and its accreditation body gives the perception that the registrar cuts quality corners, says John E. (Jack) West, chair of the U.S. TAG to ISO TC 176, the technical committee responsible for developing and revising the ISO 9000 standard series. However, it doesn’t necessarily mean that all the registrations AGS has issued are suspect, says West.
“I wouldn’t want a registrar to even be in the reach of an accreditation body,” says West. “It just doesn’t look right. There has to be an impartial observer to verify that both the registrar and the accreditation body are doing what they’re supposed to be doing.”
The RAB contends that because AGS and AIAO-BAR share management, the value of the registrations AGS issues is suspect. The global conformity assessment scheme depends on consistent adherence to requirements and cooperation among certification/registration bodies, and while operating outside that sphere isn’t illegal, it has the ability to upend long-standing rules in the industry, says the RAB.
“An organization that provides certification or recertification services without regard for, or contrary to, internationally accepted requirements offers no value to potential customers in the global marketplace,” reports the RAB. “The requirements for certification/registration bodies provide clear guidance on what is required for a legitimate certification, and issuing a certificate without having conducted an (on-site) audit clearly doesn’t meet the requirements.”
The value of this new registration method is dependent upon the customer’s reasons for pursuing it. If more companies choose virtual registration renewal like the service offered by AGS, the trend could affect the weight of traditional compliance audits, as more companies perceive that the certificate itself is more important than the process improvement auditing requires.
Quality News From China
The Chinese government encourages China’s thriving business sector to strive for better quality in a recently issued standard.
The new standard is based on foreign models and is geared toward China’s unique business environment--especially in improving business credibility, brand-building strategy and sustainable development. The Chinese government issued its “Law on Product Quality” in 1993, and the new standard is touted as a significant expansion of the government’s commitment to quality.
Liu Yuanzhang, director of the national standard auditing committee, says that the standard will help raise the profile of quality among Chinese manufacturers. “The American quality award focuses on competition, the Japanese quality award focuses on innovation and the Chinese quality award focuses on reform,” Liu says.
The Chinese government used components of the Malcolm Baldrige National Quality Award to form the Chinese National Quality Award criteria. Representatives of the Shanghai Academy of Quality Management, who helped write the country’s new quality standard, invited Baldrige Award winners to Shanghai to report on their processes. At the same time, they held many seminars to study Baldrige criteria, learning to adapt those concepts to Chinese quality policy.
Seventeen businesses have been awarded the Chinese National Quality Award during the last three years. Among them, Baosteel and Shanghai Dazhong Taxi won the World Class Organization Award and the Asia-Pacific Quality Award, in 2002 and 2004, respectively.
The new quality standards become effective on Jan. 1, 2005.
Kudos to a Nutty Team
Yazaki North America recently awarded an employee team with a Quality Control Circle Award for its innovative quality and cost avoidance plan.
The seven-member team, which calls itself “The Nut Finders,” is from the machine maintenance, quality and tooling departments at the company’s plant in El Paso, Texas. The team received the award at the conclusion of Yazaki North America’s Quality Control Circle Presentation Run-Off at the company’s Canton, Michigan, headquarters. The award gives the team the opportunity to represent the Texas plant--which manufactures vehicle components--at the corporation’s global quality competition in Japan.
Team members Rodney Robles, Frank Nieto, Mike Otto, Jose Hernandez, Gabriela Suarez, Ferol Vernon and Renee Bullitt earned the award for modifying an underperforming mold that made it difficult for a sensor to detect the presence of a nut inside. Additionally, the team modified a metal detector to allow it to move in reverse when defects are detected. The method was adapted for other processes and will result in a $70,000 savings for the company.
Yazaki North America has deployed the quality message to all its employees. The corporation supports more than 140 QC Circle teams in its four U.S. plants. The teams compete against each other to find the most innovative ways to save the company time and money. All viable ideas are implemented to improve performance, and the winning teams are able to compete against teams from abroad.
“Events such as this really show how employees contribute to our company’s ability to remain competitive,” says Fred Randall, manager, Yazaki North America ComBU-QAD.
For more information, visit www.yazaki-na.com.
Bush Approves Baldrige Expansion
President Bush signed into law a bill to create a nonprofit category for the Malcolm Baldrige National Quality Award on Oct. 5.
Both houses of Congress passed the legislation unanimously. The American Society for Quality, which lobbied for the bill, hailed it as a big step toward expanding the Baldrige Award to the nonprofit sector.
“[The signing is] a significant accomplishment for all of us who worked so hard to ensure that the many benefits of the Baldrige Award process extend to every segment of the economy,” says ASQ president Danny Duhan.
The legislation took the form of an amendment to the Stevenson-Wydler Technology Innovation Act, which is the law that originally established the Baldrige Award. It was passed by the House of Representatives in March and by the Senate in September. ASQ led a large coalition of Baldrige supporters to rally support for the bill. It was also successful in 1998, when ASQ’s lobbying efforts helped convince legislators to expand the Baldrige Award into the health care and education sectors.
There are currently five Baldrige Award categories: manufacturing, service, small business, education and health care. The Foundation for the Malcolm Baldrige National Quality Award has raised an endowment of more than $18 million to support the program and will raise additional funds to support the new category. Federal funding for the Baldrige Award program in 2004 totaled $5 million.
The program may begin accepting Baldrige applications from nonprofit organizations in spring 2006.
For more information, visit www.baldrige.nist.gov.
ASQ to Expand Health Care Faculty
The American Society for Quality is seeking quality professionals to expand its faculty base.
Candidates should have at least five years of experience in the following areas:
Quality tools and problem solving
Statistical process control
Continuous improvement methodologies
Change management
Six Sigma/Master Black Belt
Failure mode and effects analysis
Human factors
ISO 9001
Lean
Patient safety plan development
Patient flow
Teamwork
Leadership development
Cultural change
Integrating technology and quality management systems
For more information, visit www.asq.org.
It’s a REALLY Small World
Nikon Instruments Inc. recently presented several innovative scientist/photographers with awards in the company’s annual Small World Competition.
Photomicrographers submitted more than 1,200 images of some of the tiniest things on earth. Nikon judges picked 20 to include in its Small World exhibit, which will begin touring the country in January 2005. Seth Coe-Sullivan of the Massachusetts Institute of Technology’s engineering and computer sciences department won first place in the competition for his depiction of quantum dot nanocrystals deposited on a silicon substrate. Shirley Owens of Michigan State University won second place and Torsten Wittman of The Scripps Research Institute won third place.
“This year’s (exhibit) recognizes the world’s best photomicrographers who make critically important scientific contributions to life sciences, bioresearch and materials science,” says Lee Shuett, Nikon Instruments executive vice president. “We are all beneficiaries of their scientific insights and artistic perceptions.”
The exhibit of the winning images will begin a cross-country tour starting on Jan. 1, 2005 in Times Square in New York City.
View the exhibit’s electronic galley at www.nikonsmallworld.com.
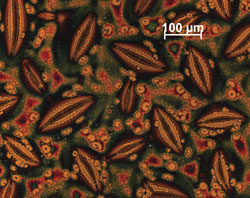
First Place-Seth Coe-Sullivan. Quantum dot crystals on silicon substrate
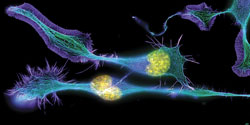
Third Place-Torsten Wittman. Differentiating neuronal cells.
|
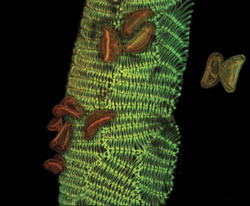
Second Place-Shirley Owens. Spiderwort flower and immature pollen. |
Canada Awards for Excellence Announced
Three Canadian small businesses have been recognized with the National Quality Institute’s Canada Awards for Excellence, that country’s equivalent to the Malcolm Baldrige National Quality Award.
Winners in the CAE’s small business category were M & M Meat Shops Ltd. (head office), Print Audit and Strus & Associates Inc.
“As a core part of Canada’s economic engine, these smaller businesses are to be applauded for such outstanding performance,” says Cameron Hyde, NQI chairman as well as senior vice president and general manager for Xerox Corp.’s North American agent operations. “For these winners, excellence is a way of life and central to the way their operations are managed.”
M & M Meat Shops’ head office services the largest retail chain of specialty frozen foods in Canada: 378 franchised stores in 10 provinces and the Yukon. The company provides extensive training, marketing resources and communications programs that help them nurture an effective two-way partnership with franchisees. A formal wellness program helps keep employee turnover and absenteeism to a minimum and promotes professionalism, productivity and teamwork.
Print Audit provides print tracking and copy auditing services to help clients analyze and recover their printing and photocopying costs. The company focuses on product quality and a close collaboration between developers and technical support staff. Despite thousands of customers, Print Audit averages only about five support calls per day and has doubled its sales since its inception in 1998.
Strus & Associates has more than 50 specialist resources and is Canada’s only full-service consulting and training firm. The company is customer-focused and provides consulting on NQI and Baldrige standards. It has a stringent operating standard and is respected for exceeding client expectations.
NQI recognized Delta Hotels, DaimlerChrysler Canada and the Canadian Auto Workers, and Polywheels Manufacturing Ltd. as Gold Trophy recipients. In addition, Formation Construction Engineering Maritime Forces Atlantic, The Region of Peel, Calian Technology, Henry Hudson Sr. Public School and R.H. King Academy all received Silver-level performance awards.
The awards were formally presented at the Canada Awards for Excellence gala on Oct. 19 in Toronto. For more information, visit www.nqi.com.
Health Care Quality Improves… For a Few
The U.S. health care system has huge quality gaps that contribute to 42,000-79,000 avoidable deaths every year, according to a recent survey released by the National Committee for Quality Assurance.
“State of Health Care Quality 2004,” released this fall, found that the quality of care delivered by health plans improved markedly from last year. But it also indicates that, because those improvements were applied to only one-quarter of the system, health care is deeply polarized and delivers excellent care to some people and generally poor care to others.
A total of 563 health plans, covering 69 million people, are included in the survey. The quality gap refers to the difference between the national average in a given clinical measure and the performance of the top 10 percent of health plans. The latter is used as a benchmark because it represents a realistic, achievable goal for the entire system. For instance, only about 34 percent of Americans with high blood pressure have their condition adequately controlled. But 71 percent of high blood pressure patients covered by the top 10 percent of health care plans have their blood pressure controlled, resulting in a 37 percentage point quality gap.
“It would never be acceptable to say, ‘I’m sorry we didn’t save your loved one--we knew how, we just didn’t do it,’” says Ellen Stovall, National Coalition for Cancer Survivorship president and CEO. “But these quality gaps show us that that actually happens thousands of times every year. And every time it happens it represents a failure to put health care knowledge into practice. Surely we can do better.”
This year’s report also highlights various efforts aimed at improving health care quality, including several physician and hospital pay-for-performance projects, which are seen by many experts as a key part of the solution to the country’s health care problems.
“Measuring performance allows us to do three very important things: inform consumer choice, reward quality and identify opportunities for improvement,” says Mark McClellan, M.D., administrator of the Centers for Medicare and Medicaid Services. “There is enormous potential in these activities to drive improvement, and without measurement you can’t do any of them. Medicare is 100-percent committed to pay-for-performance.”
To see the report, visit www.ncqa.org. |