New Tactics in the War on E. Coli
The U.S. Department of Agriculture’s Food Safety and Inspection Service has announced added policies to protect public health against the risk of E. coli O157:H7, including expanded testing and more rapid recalls.
“We want the American consumer to know that FSIS has taken a number of aggressive actions to respond to a recent increase in E. coli O157:H7 recalls and illnesses associated with this pathogen and we are further expanding these efforts,” says Dr. Richard A. Raymond, FSIS under secretary for food safety.
In June 2007, FSIS identified an increased number of E. coli O157:H7 positive tests in beef. This finding, along with a larger number of recalls and illnesses caused by this pathogen, prompted FSIS to increase the number of tests of ground beef for E. coli O157:H7 by more than 75 percent. “We are going through a very comprehensive review of our entire inspection and recall procedures at this time and taking lessons learned from a number of recalls, including the recent Topps recall,” said Raymond during an October 23 telephone press conference.
The agency also began planning for a new follow-up testing program for federally inspected beef plants that had positive tests for E. coli O157:H7. “FSIS will begin testing materials that are used as components in raw ground beef, in addition to the beef trim that is already tested, which is the primary component of ground beef,” says Raymond.
Currently, all U.S. beef plants are expected to verify to FSIS that they are effectively controlling E. coli O157:H7 during slaughter and processing. The agency provides industry- specific examples of minimum standards to enable a well- controlled process. By identifying which establishments achieve the base criterion, and which establishments do not, this process provides FSIS with critical information regarding areas of vulnerability.
FSIS is also requiring countries whose beef is imported to the U.S. to conduct the same kind of sampling or equivalent test measures.
Circle Foods LLC
- Nov. 8, 2007
- 3,750 lb
- frozen beef tamales
- may contain pieces of metal
Cargill Meat Solutions Corp.
- Nov. 3, 2007
- 1,084,384 lb
- ground beef products
- E. coli O157:H7
General Mills Operations
- Nov. 1, 2007
- 3.3 million lb
- frozen meat pizza
- E. coli O157:H7
Topps Meat Co.
- Sept. 29, 2007
- 21.7 million lb
- frozen ground beef products
- E. coli O157:H7
Richwood Meat Co. Inc.
- Apr. 20, 2007
- 107,943 lb
- frozen ground beef products
- E. coli O157:H7
For more information, visit www.fsis.usda.gov/Fsis_Recalls/index.asp.
|
A new, more sensitive test to detect E. coli O157:H7 contamination in products will begin in January 2008.
“I want to remind people that the outcome of this new test may be that we find more positive results than in years past,” says Dr. David Goldman, FSIS assistant administrator.
Along with improved testing, FSIS will begin targeted sampling for E. coli O157:H7 at slaughter and processing facilities. Presently, all plants have an equal chance of being tested. Under this new verification testing program, FSIS will more frequently test larger-volume operations, as well as those with a poor history or that do not meet the minimum standards.
Before implementing the new regulations, FSIS destroyed untested samples from ground beef producers that had verifiably destroyed or cooked the product in question. Under the new policy, says Raymond, “To try to improve our database, we [will] now pull that sample and send it to our laboratories for testing. And if it is positive, we hope that the company has held and will either destroy or cook the product. If they didn’t hold the product, we will recall it. And that [accounts for] about half our recalls.”
FSIS also determined that steps were needed to ensure that its inspection- program personnel and industry personnel fully understand the nature of the challenge presented by E. coli O157:H7. The agency is ensuring that suppliers, processors, and FSIS will be able to identify an emerging problem as early as possible.
FSIS will also target outreach and training sessions around the country for small and very small raw beef processors, other stakeholders, and FSIS inspection program personnel. This training will focus on new E. coli O157:H7 policies, as well as lessons learned from the recent recalls associated with E. coli O157:H7.
“By testing earlier in the production chain to identify contaminated beef trim intended for ground beef, FSIS prevents this source from contaminating the ground beef available to consumers,” says Dr. Daniel Engeljohn, FSIS deputy assistant administrator.
“We’ve created a new checklist for verifying these controls,” says Engeljohn. “FSIS will analyze the checklist data and adjust programs or policies as needed.”
For more information, visit www.fsis.usda.gov.
Do the Math
Last month we asked readers to find the error in the contest rules for a contest that offered a grand prize of your baby’s weight in gold. The error was in this line: “…based on price of gold …[$306.20/ounce] and a birth weight of 9.5 lbs = $46,542.40….”
The majority of readers recognized that the contest had used standard avoirdupois ounces and not troy ounces for the calculation (gold is measured in troy oz). There are 14.583 troy oz to a pound (not 16).
9.5 lbs = 138.54 troy oz.
Therefore: the example should have shown 138.54 x $306.20 = $42,420.95. This month’s lucky winner is Larry Golembiewski. A fantastic, possibly functioning, gift is on its way.
This month’s puzzle was already solved… by an eight-year-old boy. At a Charlotte, North Carolina, science museum, Parker Garrison came upon a pyramid full of jelly beans. Museum visitors were challenged to calculate the number of jelly beans in the pyramid given these instructions:
“A jelly bean has a volume of about 1 cubic cm. This container is half a pyramid:
Its base measures 46 cm by 23 cm and its height is 72 cm.
Here’s the formula to find the volume: 1/3 × base area × height.
Now divide your answer by 2 since this is half a pyramid.
Now multiply your answer by 0.9 to account for spaces between the jelly beans. The answer should be 22,853.”
Obviously the math doesn’t pan out. But where did the instructions go wrong and why? Be specific. Send us your answer by clicking the feedback link at the bottom of this page.
Send us your math error. If we use it, you win a prize.
Mind the [Engagement] Gap
Employees do not believe their organizations or their senior managers are doing enough to help them contribute to their companies’ success, according to a new global survey of 90,000 workers conducted by Towers Perrin, a professional services firm.
In the survey, just 21 percent of employees reported feeling “engaged” in their work, a term Towers Perrin defines as meaning that employees are willing to expend extra effort to help their companies meet goals. Fully 38 percent are partly to fully disengaged. The result is a gap--which Towers Perrin calls the “engagement gap”--between the discretionary effort companies need and people actually want to invest, and companies’ effectiveness in channeling this effort to enhance performance.
“It’s impossible to overstate the importance of an engaged workforce on a company’s bottom line,” said Julie Gebauer, managing director and leader of Towers Perrin’s workforce effectiveness consulting practice. “The global workforce study establishes a definitive link between levels of engagement and [a company’s] financial performance, and demonstrates that the workforce itself represents the largest reservoir of untapped potential.”
The survey also found that engagement has a direct correlation to retaining employees. Less than five percent of engaged employees said they were actively looking for another job compared with more than one in four of the disengaged employees.
“At the end of the day,” says Gebauer, “our study paints a picture of a workforce that is energetic, ambitious, and committed to working hard and giving its best. The challenge for senior management is to recognize the value of employees’ untapped potential and to channel it in ways that yield real improvements in business performance.”
For more information, visit www.towersperrin.com/gws.
New Shingo Book Translation
Enna Products Corp. and Norman Bodek have published a new hardcover book by Shigeo Shingo, Kaizen and the Art of Creative Thinking. Along with Taiichi Ohno, Dr. Shingo codeveloped the Toyota production system (TPS). Originally written in 1958–59, this new English translation reveals how Shingo taught Toyota and other Japanese companies the art of using creative thinking to identify and solve problems.
Dr. Shingo presents six models, the sum of which he calls the “scientific thinking mechanism.” These frameworks allow groups to deconstruct problems and rebuild them into powerful improvement ideas. This concept is central to TPS and provides the essential foundation for a successful lean initiative.
“The actual scientific model behind this book is as revolutionary as Dr. Shingo’s SMED [single minute exchange of dies] system,” says Collin McLoughlin, president of Enna Products.
Enna Products has also announced the founding of an annual $25,000 sweepstakes in honor of Dr. Shigeo Shingo. “At its core, the Shingo sweepstakes is about promoting the prestigious Shingo Prize for Manufacturing Excellence, as well as raising overall awareness of lean thinking,” says McLoughlin.
For more information about the Shingo Sweepstakes, visit www.shingosweepstakes.com.
Editorial by Carey Wilson
Auto Autos
How many of us have wished we could get into our car and tell it where we want to go, and have it take us there by the quickest, safest route possible while we sleep, read a book, or refine our notes for that upcoming presentation? And who wouldn’t like to see an armored truck with the ability to negotiate hostile territory and deliver supplies to soldiers in the field without risking the lives of drivers and guards?
Such are the goals of the DARPA Urban Challenge, which took place November 3, 2007, at the former George Air Force Base in Victorville, California, the third autonomous vehicle race sponsored by the Defense Advanced Research Projects Agency.
The Urban Challenge requires vehicles to maneuver in a mock city environment, executing simulated military supply missions while merging into moving traffic, navigating traffic circles, crossing busy intersections, and avoiding obstacles. The Carnegie Mellon University team that successfully completed the course in the fastest time won a $2 million prize.
“Vehicles competing in the Urban Challenge have to think like human drivers and continually make split-second decisions to avoid moving vehicles, including robotic vehicles without drivers, and operate safely on the course,” says Norman Whitaker, Ph.D., Urban Challenge program manager. “The urban setting adds considerable complexity to the challenge faced by the robotic vehicles, and replicates the environments where many of today’s military missions are conducted.”
The competing vehicles depended on onboard computers, a variety of sensors, and GPS systems that allowed them to see the environment; operate steering, throttle, braking, and transmission controls; and decide where to drive.
DARPA designed the course so that vehicles couldn’t compete merely by following GPS waypoints. Each vehicle was required to see the road ahead and to use its own judgment in determining where to drive.
Developing autonomous commercial vehicles is no doubt inevitable as the desire to get ourselves to our destinations while concentrating on other things, and the need to deliver essential supplies to soldiers besieged in urban environments, continue to evolve along parallel paths.
For more information, visit: www.darpa.mil/GrandChallenge.

Quality Digest publisher, Mike Richman speaks at WCBF Global Six Sigma Summit.
|
Six Sigma Summit Wrap-Up
The WCBF 2007 Global Six Sigma Summit and Industry Awards, held Oct. 23–26, in Las Vegas, featured a host of thought leaders, including author Jim Collins and Six Sigma architect Mikel Harry. The summit offered many chances to interact and exchange best practices. The awards ceremony honored the year’s best individual and organizational achievements in Six Sigma. Notable winners included CEO of the Year Tim Solso of Cummins Inc., Vice President of the Year Dr. Tomas Gonzalez of Valley Baptist Health System, and Valley Baptist Health System again, which won the Platinum Award for most outstanding organizational achievement.
Next year, WCBF will host three events: the 2008 Lean Six Sigma and Process Improvement in Healthcare Summit, in Las Vegas, Apr. 1–4; the 2008 Lean Six Sigma Summit, in Chicago, Apr. 29–May 2; and the 2008 Global Six Sigma Summit and Awards, in Las Vegas, Oct. 7-10, 2008.
For more information, visit online at www.wcbf.com/quality.
ISO Condom Standards Conference
Quality and international standards are never more important than when they affect human life. In places like Africa, where there is a high rate of HIV, condom standards are especially crucial--failure could mean the spread of deadly diseases.
To tackle the issue of updating condom standards, the 24th meeting of the International Organization for Standardization Technical Committee 157 on “mechanical contraceptives” was held October 8–14, at Seogwipo on South Korea’s Jeju Island.
ISO/TC 157 consists of 49 member countries and five international organizations. Participating organizations included the World Health Organization and the United Nations Population Fund.
During the conference, government officials and industry representatives examined condom manufacturing, specifications, and testing requirements. Manufacturers discussed proposals to reduce the quality-inspection time, along with new standards in the manufacture of polyurethane and female condoms.
The creation of a more unified international standard will allow more thorough testing. An ISO official told the Korea Times that the organization will “define condoms as daily necessaries and promote condom use to prevent AIDS.”
For more information visit: www.iso.org
Statistically Speaking
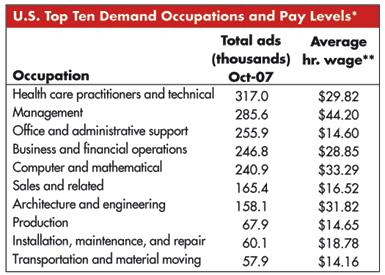
Source: The Conference Board -- All rights reserved.
*Demand refers to the number of classifieds placed in these occupations
**BLS Occupational Employment Statistics -- May 2006 estimates.
RFID at Sea
Shipping companies will soon be able to check the condition of their freight on the high seas in real time. In cooperation with an international consortium, Siemens has developed a surveillance system that tracks containers and can even check their condition.
When traveling from continent to continent, container ships are frequently underway for months. Until now, the shipping companies have only been able to track the position of the ships, but not the condition of the freight. As a result, it is not known whether refrigerated goods or costly objects have survived the trip undamaged until the cargo is unloaded at the destination. To address this problem, the new surveillance system combines a range of different communications technologies. Inside each container is a radio-frequency identification (RFID) chip that transmits information every two seconds on the freight’s current status to a special onboard global system for mobile communications (GSM) box.
The system transmits the current position and condition of the container to the ship’s captain and the shipping company or the freight’s owner. If any changes occur outside programmed values (e.g., high gas or temperature values, moisture, or suspicious vibrations), the RFID chip immediately sounds the alarm by sending out a text message.
The consortium of transport and shipping companies, technology suppliers, and security organizations recently tested the system on a route between Singapore, Thailand, and China. The containers’ RFID signals were evaluated by an independent institute in Singapore, which determined that all of the signals were accurately transmitted.
For more information, visit www.siemens.com.
|