newsdigest
by Dirk Dusharme and Cecelia Reeves
President Announces 1996 Baldrige Winners
Motivational Posters-Back With a Vengeance
RAB Tightens Auditor Requirements
IRS: Labor-Management Teams That Work
ASQC Launches ISO 14000 Quarterly
Swept Away!
National Science Foundation Funds Quality Research
ANSI-RAB Evaluates ISO 14000 Trainers
Eight Steps to Change
Entela Founder Dies
Making TPM Work
President Announces 1996 Baldrige Winners
On October 16, President Clinton and Commerce Secretary Mickey Kantor announced
the winners of the 1996 Malcolm Baldrige National Quality Award. There were
winners in each of the award categories-manufacturing, service and small
business-the first time that has happened since 1992.
There were 29 applicants for this year's award, the lowest since the award's
creation in 1988. Although fewer companies are applying for the award, the
award criteria are accepted widely as the standard for performance and business
excellence. The criteria are used by thousands of organizations of all kinds
for self-assessment, planning, training and other purposes. More than a
million copies have been distributed since the first edition in 1988.
http://www.quality.nist.gov/
ADAC Laboratories, Milpitas, California
Baldrige category: Manufacturing Employees: 710
ADAC designs, manufactures, markets and supports products for health care
customers in nuclear medicine, radiation therapy planning and health care
information systems.
All executives are expected to spend 25 percent of their time with customers,
personally take customer calls and invite customers to attend weekly quality
meetings. Since 1990, customer satisfaction for post-sales technical support
has increased 10 percent and customer retention has grown from 70 percent
to 90 percent. In addition, the length of time it takes to get customers
up and running once a problem has occurred has decreased from 56 to 17 hours.
Dana Commercial Credit Corp., Toledo, Ohio
Baldrige category: Service Employees: 547
Dana Commercial Credit provides leasing and financing services to a broad
range of business customers in selected market niches.
DCC consistently meets or exceeds key customer requirements, including completing
transactions that competitors cannot, closing transactions on time, getting
transactions done as agreed and providing customized lease products before
the competition. Customers of DCC's Capital Markets Group have ranked them
between four and five on a five-point scale (five is highest). DCC's Dealer
Products Group U.S. ranks between eight and nine on a 10-point scale (10
is highest).
Custom Research Inc., Minneapolis
Baldrige category: Small business Employees: 105
CRI is a full-service national marketing research firm with clients in consumer,
business-to-business, service and medical markets. The company works with
large multinational companies to design and conduct projects that provide
information to help make better business decisions.
CRI meets or exceeds clients' expectations on 97 percent of its projects.
Seventy percent of CRI's clients say the company exceeds expectations. CRI's
"technology-driven processes" have allowed the company to reduce
cycle time for data tabulation from two weeks to one day.
Trident Precision Manufacturing Inc., Webster, New York
Baldrige category: Small business Employees: 167
Trident Precision Manufacturing is a contract manufacturer of precision
sheet metal components, electromechanical assemblies and custom products
for the office equipment, medical supply, banking, computer and defense
industries.
Trident monitors custom product reliability through defects per 100 machines.
For the past two years, Trident's custom products have had zero defects.
Quality rating for its major customers shows performance results consistent
over time and above 99.8 percent. Since 1990, on-time delivery has risen
from 87 percent to 99.9 percent, and direct labor hours spent on rework
declined from 8.7 percent to 1.1 percent
Motivational Posters-
Back With a Vengeance
Do you miss those beautiful inspirational posters of soaring eagles, sunsets,
joggers and the American flag waving in the breeze? Don't worry. They're
back-with a vengeance.
But while sales are booming for companies that sell motivational missives,
others question the motivation of managers who use them, according to a
recent Conference Board report.
"These are gimmicky attempts to fill the void where effective management
doesn't exist," says Alfie Kohn, author of Punished by Rewards. "Companies
buy them because they're cheap compared to what it takes to remake a workplace.
One of W. Edwards Deming's 14 points was to eliminate slogans. That whirring
you hear in the background is Deming spinning in his grave."
"[Managers] actually believe that these pump-up toys work," says
Charles Garfield, author of Peak Performers: The New Heroes of American
Business. "If the poster says 'Risk and Experiment,' but the company's
message is 'Don't lose a dime of the company's money,' which do you think
you're going to follow?"
Then again, Southwest Airlines, renowned for its fun, participatory work
environment, recently bought $38,000 worth of motivational posters.
RAB Tightens Auditor Requirements
Beginning Jan. 1, 1998, all certified auditors must document at least 15
hours of continuing quality-related professional development activities
each year, the Registrar Accreditation Board recently announced. The requirement
is part of RAB's update to its quality management system certification program.
The program also requires that candidates applying for QMS auditor certification
after Jan. 1, 1997, have completed an approved training course within the
previous three years and removes the three-year limit for provisional auditors.
For certified auditors, acceptable continuing quality-related professional
development activities include but are not limited to attending training
classes, seminars, conferences or workshops; teaching courses; or publishing
articles.
IRS: Labor-ManagementTeams That Work
By consenting to implement a total quality partnership agreement, the National
Treasury Employees Union and the North Texas District of the Internal Revenue
Service have significantly improved labor-management relations, enhanced
customer service and saved the taxpayers money.
In 1993, labor-management relations at NTD reached an all-time low when
the union, with a bargaining unit of 1,893 employees, filed 132 grievances
and 20 unfair labor practices. Strained labor-management relations based
on we-they positional bargaining slowed or prohibited process improvements,
says Bobby Scott, NTD's director. "We had a standoff on a lot of routine
issues," he notes.
With the signing of the Total Quality Partnership agreement in July 1994,
the union gained a more active role in decision making, says Scott. NTEU
members attend executive staff meetings, off-site planning meetings and
budget meetings; NTEU representatives and nonbargaining employees participate
in process analysis teams; and labor and management discuss workplace changes
and other issues earlier in the process.
The transition has not been easy, says Scott. There is distrust on both
sides and accusations of "sleeping with the enemy," he says. But
the real test of whether the partnership has worked is in the results. "We
have improved productivity and we have saved the taxpayer a lot of money,"
Scott points out.
Joint labor-management teams working on a variety of projects have saved
taxpayers nearly half a million dollars, according to the IRS. Grievances
dropped from 132 in 1994 to 123 in 1994, and no unfair labor practices were
filed-resulting in a savings of $57,000. Union negotiations, which have
taken as long as four weeks, were reduced to just three days at the last
negotiations.
This year, the IRS, the North Texas District and the NTEU were winners of
the federal National Partnership Award, which honors federal labor-management
teams that improve the delivery of customer service.
ASQC Launches ISO 14000 Quarterly
New on the ISO 14000 horizon from ASQC is Focus on 14000, a new environmental
management standards quarterly. The report will provide executive summaries
of significant developments and trends in ISO 14000, as well as substantive
and actionable information for those who need continuous updates on ISO
14000 developments.
Editor Cornelius "Bud" Smith Jr. is a leader of the U.S. Technical
Advisory Group to ISO Technical Committee 207, the international body charged
with developing ISO 14000. He will serve as the editor of Focus 14000. Smith
will be assisted by a group of contributing editors, including SubTAG chairs
of the U.S. TAG to ISO/TC-207. The advisory board will include Joe Cascio
of Global Environment and Technology Foundation, U.S. TAG chair; Joseph
Dunbeck, CEO of the Registrar Accreditation Board; Mary McKeil, director
of the Volunteer Standards Network, Environmental Protection Agency; and
various other contributors.
For subscription information, contact the ASQC at (800) 248-1946 or (414)
272-8575.
Swept Away!
Internet surfing may be sweeping employees away in a tide of unnecessary
information and inefficiency. One problem is Internet privilege abuse, according
to a survey developed by Robert Half International Inc. One-hundred-and-fifty
executives from the nation's 1,000 largest companies were asked, "Is
employee time spent accessing the Internet for nonbusiness purposes considered
a threat to productivity today?" Fifty-five percent of them said yes.
Another problem is information overload. A British survey found that faxes,
voice-mail, e-mail and, yes, the Internet actually increased stress levels
and, to some degree, inefficiency. Four out of 10 managers call their working
environment extremely stressful on a daily basis, and 94 percent do not
believe the situation will improve.
National Science Foundation Funds Quality
Research
One of the problems with the quality movement is the lack of good empirical
research to back it up, according to University of Cincinnati quality expert
James W. Dean Jr., program director of the Transformation to Quality Organizations
research program at the National Science Foundation. To encourage research
on quality, TQO, along with the ASQC and leading corporations and universities,
has committed a total of $9 million in grants over a three-year period to
fund research in quality management and engineering.
"We hope that the TQO will provide a firm foundation of well-executed
research to give companies some assurance that what they are doing will
make a difference," says Dean.
The purpose of the research is to develop or improve concepts, theories
and methodologies for transforming to quality organizations and to encourage
the development of new tools or processes that lead to quality improvements.
Research supported by the program is done by university faculty and must
be based on partnerships between researchers and organizations, says Dean.
Research must also be interdisciplinary. NSF uses nine of 11 Malcolm Baldrige
National Quality Award core concepts to suggest the research domain.
A few of the 25 research projects currently funded by TQO include "Leadership
of Technical Professional Teams"-University of North Texas, Department
of Psychology; "The Role of Employee Performance Evaluations in Quality
Improvement Initiatives"-Boston University School of Public Health;
and "Saturn: The GM/UAW Quality Partnership"-Massachusetts Institute
of Technology, Sloan School of Management.
For more information or grant application guidelines, call the TQO at (703)
306-1757.
http://www.asqc.org/alliance/nsf.html
ANSI-RAB Evaluates ISO 14000 Trainers
Five companies will participate in a pilot accreditation program for ISO
14000 auditor training course providers. The pilot is part of the National
Accreditation Program, a joint ISO 9000 and ISO 14000 accreditation program
run by the American National Standards Institute and the Registrar Accreditation
Board.
The course providers selected for the pilot are: Applied Quality Systems
Inc., Excel Partnership Inc., International Quality & Environmental
Services, Quality Systems Development and Stat-A-Matrix. RAB auditors will
perform detailed evaluations of each provider's complete course materials.
These evaluations involve course administration system documentation, course
examinations, and instructor and student materials. Each course must pass
the detailed evaluation in order to move onto the the on-site evaluation.
On-site reviews will involve an RAB audit team observation of each candidate
course's entire offerings. Once any nonconformances are corrected, a report
is issued by the audit team to the environmental management systems' council.
The council will then vote on the accreditation status of the pilot candidates.
Eight Steps to Change
How can change be instituted so that it strengthens rather than depletes
our companies, our society, our people? John P. Kotter, professor of leadership
at Harvard Business School, outlines an eight-step action plan in his book
Leading Change (Harvard Business School Press):
Establish a sense of urgency: Examine market
and competition realities. Identify crises and opportunities quickly.
Create a guiding coalition: Emphasize teamwork.
Develop a vision and strategy: Focus on giving
efforts direction and on motivating people.
Communicate the change vision.
Empower broad-based action: Change those systems
or structures that seriously undermine the vision.
Generate short-term wins: Plan visible performance
improvements and recognize the people who achieve them.
Consolidate gains and produce more change:
Use increased credibility to change any systems that don't fit the vision.
Anchor new approaches in the corporate culture:
Ensure that employees recognize the link between customer satisfaction and
improved results.
Entela Founder Dies
Kenneth Sweers, one of the founders of Entela Inc., died on October 15th
of an extended illness. He was 68 years old.
Entela provides testing, inspection and quality assurance services to manufacturers
from automotive, furniture, metal and plastic industries. Sweers built the
business around the philosophy that employees were valued as contributing
individuals in the firm's success and that they were an integral part of
the corporate family.
Making TPM Work
The good news is: Total productive maintenance works. The bad news is: It
doesn't work if you don't stick with it. That's the lesson learned by Fiberweb
North America's Simp-sonville, South Carolina, plant, a producer of nonwoven
fabrics.
Since implementing total productive maintenance one-and-a-half years ago,
the Simpsonville plant has seen total uptime grow from less than 60 percent
to more than 90 percent.
The system worked so well, in fact, that in June, with equipment uptime
nearing 99 percent, the plant decided to skip scheduled maintenance for
six weeks in order to accommodate increased production-a big mistake, says
Plant Engineer Dennis Edwards.
"Very quickly, we saw the effects," he recalls. "In July,
our overall uptime dropped below 80 percent." In August, when the plant
resumed its regular maintenance schedule, uptime again increased into the
mid-90s-nearing world-class levels, says Edwards.
Besides keeping on track with scheduled maintenance, the key to successful
TPM for Simpsonville has been to view maintenance and production as a single
process, says Edwards.
"We don't consider ourselves production or maintenance," he explains.
"We're manufacturing; we're all in the same boat. That's why when we
talk about uptime, we don't worry about equipment uptime vs. process uptime.
We talk about total uptime."
At Simpsonville, maintenance technicians work closely with production to
schedule maintenance during routine machine downtimes, such as during a
changeover. Moreover, the plant tries to maintain a one- to two-week planned
maintenance interval on equipment. Machine operators perform their own low-level
maintenance, such as lubrication, leaving higher-level maintenance to maintenance
technicians.
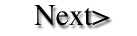