The
good news: You still have a year and a half to make the
transition to the new ISO 9001:2000 quality management system
standard. The bad news: There are only 18 months left in
which to do it. Depending on where you get your data, there
are anywhere from 40,000 to 55,000 companies in the United
States and Canada that still have to make the transition
and only about 80 registrars to do the auditing. Given that
one-quarter of the registrars handle 90 percent of the certificates,
best case, that's 1,800 audits per large registrar or roughly
100 audits per registrar per month. Although the larger
registrars believe this is completely doable, success hinges
on transitions being spread evenly over the remaining time
and not having a logjam in the last six months before deadline.
So, although 18 months may be more than enough time to plan
and implement the transition--many get the job done in three
to six months--registrars may find themselves in a crunch
if too many companies hold off for too long.
This observation and many more were revealed in this year's
ISO 9000-registered company survey, the largest such survey
performed on companies currently registered to ISO 9000
or QS-9000. The survey was sent to 29,000 registered companies
in the United States and Canada; about 2,600 responded.
According to this year's survey of ISO 9000-registered
companies, about 17 percent are currently registered to
ISO 9001:2000. Specifically, 17 percent of survey respondents
indicated they are registered to the new standard, with
73 percent planning to do so. The remaining 10 percent either
plan on letting their registration lapse, aren't sure about
their plans are or are changing to some other industry-specific
standard such as AS9100 or ISO/TS 16949.
Seventeen percent is high compared to Quality Digest's
Online Database of North American Registered Companies,
which shows 3.5 percent registered companies. A telephone
poll of some of the largest North American registrars (BSI,
DNV, Perry Johnson, QMI and TÜV America), representing
about one-third of all U.S. and Canadian registrations,
indicates that the actual figure is probably somewhere between
8 and 10 percent. That leaves a lot of companies left to
transition in a relatively short period of time. But is
this really a problem?
"Every registered company has one or two surveillance
audits a year to maintain registration," says Randy
Dougherty, director of registrar programs for the Registrar
Accreditation Board. "So, at this time, each and every
one of the 50,000 yet to transition will have one or two
audits before the deadline of Dec. 15, 2003--and the transition
audit can be accomplished by an extra one to two days added
to the surveillance audit. So completing all the transition
audits isn't impossible."
Jack West, chair of the U.S. TAG TC 176, the committee
responsible for the ISO 9000 standards, also isn't that
concerned. "I'm not at the point of saying that it's
impossible," he says, pointing out that many currently
registered companies probably won't seek certification to
the new standard. "We know that some organizations
in the auto industry won't worry about it yet. And we know
that some companies are just going to walk away from registration
because they don't see any value in it. We'll get some fallout."
The survey supports West's comments regarding QS-9000-registered
companies. Roughly one-seventh of all ISO 9000-registered
companies in North America hold a QS-9000 or ISO/TS 16949
certificate, meaning their main customers are probably automakers.
About 15 percent of the survey respondents currently holding
QS-9000 certificates indicated that they won't bother with
ISO 9001:2000. Because automakers are requiring that suppliers
switch to the ISO/TS 16949:2002 standard by the end of 2006,
some clients have told their consultants and registrars
that they'll simply keep the QS-9000 certificate and transition
to ISO/TS 16949:2002 sometime before the 2006 deadline.
Although this idea may temporarily postpone having to transition,
it's not what the Big Three would prefer (see "Some
Automotive Suppliers Hold Off On Transition" on page
32).
Both West and Dougherty speculate that transitions will
be distributed fairly evenly over the remaining 18 months
as surveillance audits come due or certificates expire and
have to be renewed.
Registrars aren't so sure. Both DNV Certification and
Perry Johnson Registrars, both in the top 10 in certificates
issued, are concerned that an influx of latecomers will
cause audit congestion. "The transition rate won't
be linear," explains Bill Sullivan, DNV's marketing
manager. "And the ability of any registrar to accommodate
the rush is clearly a function of how big the rush is and
the available audit resources to perform the transition
audits. There's a point at which the demand will exceed
the available audit resources. This is true for all registrars."
While optimistic about handling their projected workload,
registrars do have contingency plans. "We're monitoring
this situation carefully," says Terry Boboige, president
of Perry Johnson Registrars. "We run regular reports
to determine where to concentrate our endeavors. PJR is
currently training more auditors to prepare for the anticipated
increase in transition audits, and in the event that the
schedule appears to be too concentrated near the deadline,
we may increase our auditor staff to accommodate."
Some registrars may subcontract audits in order to meet
the demand, something that DNV has considered, says Sullivan.
The survey asked several questions on whether recipients
had read the standard, understood it, and had access to
enough information to aid in understanding and implementing
the standard within their organization.
Although people may not stop to read the manual on how
to program their VCR, they do take the time to read the
ISO 9001:2000 standard, a moderately more interesting read.
Of the respondents who have already transitioned or plan
to do so, nearly 90 percent had read the standard. Of those
who read it, about 58 percent report that they definitely
understand the standard well enough to implement it, 37
percent aren't so sure and 4 percent were definitely not
sure they understand the standard well enough to implement
it.
While 58 percent is a reasonable amount, it still means
that there are tens of thousands of companies whose ISO
9000 coordinators or managers aren't confident about implementing
ISO 9001:2000. West and others attribute this to ISO 9001:2000's
process approach to a quality management system compared
to the old standard.
"The new standard is different and disquieting to
people who are steeped in this stuff," says West. "We've
traded the procedural approach for one that manages a series
of processes that meets a particular outcome. The whole
standard has a different focus."
Dougherty agrees that this may be the main issue. "Less-sophisticated
organizations may find ISO 9001:2000 harder to understand
and implement than ISO 9001:1994," explains Dougherty
"Actually, ISO 9001:2000 is less prescriptive and more
flexible, so it should be easier to implement. It's enigmatic
that the less prescriptive and more flexible a requirements
document is, the more challenging it is to apply because
there are many options and choices. It's easier to be told
specifically what to do."
In addition, West and others believe that because ISO
9001:2000 has broadened its language it may be speaking
in a tongue unfamiliar to some users. The consensus among
those we interviewed is that the language is much easier
to understand for those coming from a service or other non-manufacturing
company where a more holistic quality approach to meeting
the company's objectives is the norm rather than the exception.
Of course, the ability to understand the standard is directly
related to the amount and quality of information available
on the subject. Of those who gave an opinion on whether
they're satisfied with the amount of information on the
standard provided by their registrar, 60 percent reported
that they are satisfied, 15 percent are dissatisfied, 6
percent don't expect their registrar to provide information
and 18 percent are neutral. When the same question was asked
about consultants, 73 percent said they're satisfied with
the information provided by their consultants, 8 percent
are dissatisfied, 4 percent said they don't expect their
consultant to supply information and 14 percent are neutral.
All the registrars we talked to have been proactive in
providing information to their clients. Many provide guideline
documents and have a lot of useful information on their
Web sites. "It makes good business sense for registrars
to help their clients understand their options with respect
to the new standard and the importance of having a transition
plan in place," says Sullivan, whose company provides
an interpretive guideline document and a forum for asking
questions. "The objective is to avoid a situation where
the client may find itself without a valid certificate after
December 2003."
Although providing useful information is obviously a wise
business decision, the registrars have to walk a fine line
between sharing information and consulting. "It's my
impression that registrars are doing quite a bit of information
sharing," says Mark Alpert, senior vice president of
TÜV America Inc. "But companies are looking for
consulting, and the registrars who are playing by the rules
aren't providing it. That causes the [negative] feedback
you're seeing."
To help facilitate the flow of information ANSI-RAB has
relaxed a bit on how much registrars can assist clients,
says Dougherty. "ANSI-RAB withdrew Advisory 5, which
prohibited on-site training by a registrar, in order to
make it easier for registrars to provide training,"
explains Dougherty. "However, there are critics who
think on-site training by a registrar is too close to consulting."
Despite the high satisfaction scores for information coming
from registrars and consultants, 25 percent of respondents
indicated that overall they don't feel they have enough
information on ISO 9001:2000.
To help our readers along, Quality Digest has provided
a list of resources that survey respondents submitted as
being useful for learning about and keeping up-to-date on
the standard. As well as several hot books on the topic,
there are registrars' Web sites, ASQ courses and courses
provided by consultants. Web forums are also a great source
of information because they allow the user to communicate
directly with hundreds of other forum users who share information
and experiences. The two most popular forums reported by
survey respondents are the Cayman Cove Forums and InsideQuality's
ISO 9001:2000 forum. The entire
list of sources can be download by clicking here.
We asked a number of questions related to the new standard's
usability, understandability and usefulness. The results
in the table on page 24 are presented in two ways. The first
is a numeric score based on the 1 to 5 scale used for responses:
1 is the lowest, most negative perception, 5 is the highest,
most positive perception and 3 is neutral. The other format
shows the actual number of positive, above neutral answers
and the number of negative, below neutral answers.
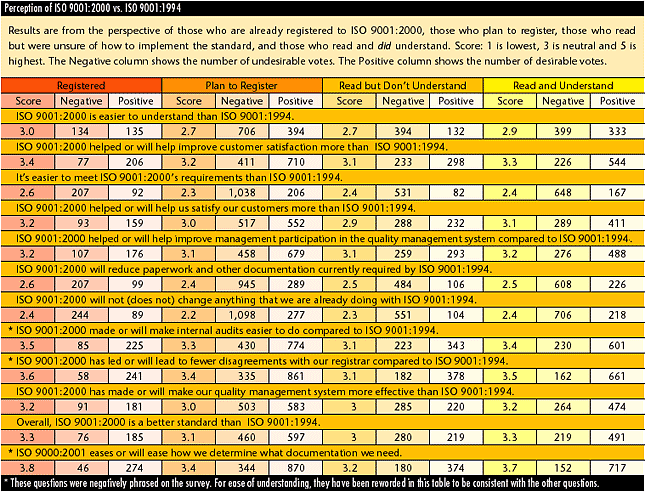
The scores are generally low, indicating mostly negative
perceptions of the standard. One of the lowest-scored statements,
even among those who had completed the transition, was "It's
easier to meet ISO 9001:2000's requirements than ISO 9001:1994."
"The old standard was very light on talking about
an integrated system, offers West. "Individual processes
were treated in isolation. Under the new ISO 9001 you need
to look at the overall processes. And that, for some companies,
is a major change, almost profound."
The statistics requirements could be another issue, says
Mark Lutz, an ISO 9000 consultant. "The main problem
area I've seen with my clients has been coming up with measurable
objectives and following through on measuring and analyzing
to those objectives," he explains. "Section 8
of the new standard talks about measuring processes using
statistical analyses. The old standard was much lighter--only
requiring statistical analyses where the company identified
the need. The new standard is much more prescriptive in
this area, saying you need to measure, analyze and improve
processes. . . and here's where you need to do it."
On the positive side, most felt that auditing was easier
and less prone to disagreement with the registrar compared
to the old standard. From those who have already transitioned,
both registrars and internal auditors got high scores for
understanding how to audit to the new standard.
In general, the response to the standard was mediocre.
Much of this could be attributable to a reluctance to change
or, as several registrars pointed out, discomfort with a
completely different way of viewing a quality management
system. It will take a couple of years to assess the real
benefits of the new standard. In the meantime, West likens
it to an old Philip Crosby lesson: "The first of Crosby's
lessons was to do it over again," recalls West. "The
system becomes stale unless you refocus it. That's one of
the objections to formal systems; they become a bureaucracy.
I encourage people to look at this change as an opportunity
to make their system better. This is a great opportunity.
Take it."
Our survey indicates that 15 percent of currently registered
QS-9000 companies are not going to pursue ISO 9001:2000
registration. Most of these companies will instead simply
wait until they transition to ISO/TS 16949:2002, which includes
ISO 9001:2000. The perceived advantage is that companies
have until the end of 2006 to make that transition. Here
is what the Automotive Supplier Quality Requirements Task
Force has to say about that option, according to Russ Hopkins,
Ford Motor Co.'s representative to the task force:
n The task force strongly
recommends to all QS-9000-registered suppliers that they
upgrade to ISO/TS 16949:2002.
n Suppliers can migrate from
QS-9000 to ISO/TS 16949:1999 and then migrate to ISO/TS
16949:2002 next year--or in 2004, if the customer agrees.
This is a business decision for the supplier.
n The task force recommends
that suppliers upgrade to ISO/TS 16949:2002 at the end of
their current QS-9000 or ISO/TS 16949:1999 certifications
rather than wait until the last minute to avoid impacting
the registrars. This is also a business decision for the
supplier.
n All suppliers must upgrade
to ISO/TS 16949:2002 by the end of 2006.
n Individual OEMs may specify
particular dates for certification earlier than 2006.
This year's survey was faxed to 34,424 fax numbers pulled
from the U.S. and Canadian listings in Quality Digest's
Online Database of North American Registered Companies.
Of those, 28,913 faxes were successfully sent. Of those,
2,690 surveys were either completed online or faxed back,
a response rate of 9.3 percent.
The survey was designed using Survey Select Expert from
SurveyConnect Inc. The software allowed us to create both
an online and print version of the survey. The online survey
allowed conditional branching based on question response.
SurveyConnect hosted the online survey and e-mailed the
response database to Quality Digest at the survey's end.
Faxed responses were manually entered into the response
database.
Data analysis was done by Quality Digest. The choice of
data to extract was based on conversations with registrars
and our knowledge of topics that interest our readers.
Dirk Dusharme is Quality Digest's technology editor. Letters
to the editor regarding this piece can be e-mailed to letters@qualitydigest.com.
|