RFID Survey Results
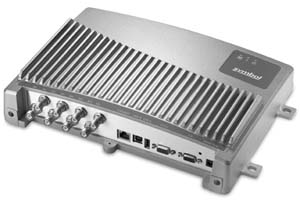
Symbol's XR400 RFID reader
|
Radio-frequency identification (RFID) is all the rage in the retail sector, but there's been little independent research done to examine the best product choices for organizations interested in implementing the technology. Until now, that is.
Noting customer demand for independent analysis of RFID devices, ODIN Technologies--a consultancy that focuses on RFID deployment and electronic product code (EPC) compliance--started a research project on the topic two years ago. The results reveal that there is a significant variance in the performance of various RFID products.
"That there were such major differences in the performance of these products proves the need for research such as ours," says Bret Kinsella, ODIN chief financial officer. "It's a very valuable tool for the many organizations that are being required to implement RFID technologies. The timing couldn't be better for getting this kind of information."
The survey analyzed the performance of RFID readers from seven manufacturers: Alien Technology Corp. (the ALR 9800 model), Impinj Inc. (the Speedway model), Intermec Technologies Corp. (the IF5 model), OMRON Corp. (the V740 model), SAMSys Technologies Inc. (the MP 9320 model), Symbol (the XR400 model) and ThingMagic (the Mercury 4 model). All of the models included in the survey are ultra high frequency (UHF), passive RFID systems that are EPC-compliant--appropriate for use in such major retailers as Wal-Mart, Target and Best Buy.
Based on performance and risk factors, Symbol's XR400 and Alien Technology's ALR 9800 were the top performers. The readers were evaluated on their performance related to distance, power output, receive sensitivity, interference rejection and dense reader mode, and time-to-read tag population.
"Overall, were very clearly the two top performers," says Kinsella. "We are starting to see clear differences in the Gen 2 devices, as they have evolved from Gen 1. The Gen 2 devices are getting much better at user response and read rates."
RFID technology is a hot topic right now, especially in the retail sector. The use of RFID chips and readers greatly simplifies inventory control and supply chain management, and major retailers and government organizations--including Wal-Mart and the Department of Defense--are starting to require that their suppliers use the technology. The sheer size of these organizations means that their requirements affect thousands of smaller suppliers. The cost of RFID systems--Forrester Research estimates that it costs about $9 million for a large retailer to set up a complete RFID system--means that selecting the right one is an important choice for companies.
"If you choose the wrong reader, you have little chance of getting high read rates," observes Patrick J. Sweeney II, ODIN president and CEO. "Without high read rates your accuracy will be low and the data will be of little use."
In the retail sector, RFID readers work by decoding information stored in chips or tiny ribbons that are embedded in cartons and other inventory. The reader transmits the data to a computer system, which updates the location of the product. The system provides reliable, electronic, automatic inventory management, which greatly improves overall supply-chain efficiencies.
The Gen 2 Reader Benchmark was sponsored by Unisys, a technology services and solutions company that has a longstanding partnership with ODIN Technologies.
For more information, visit www.odintechnologies.com.
Improving Medicare Drug Quality
Providing prescription drugs for the nation's senior citizens is a noble pursuit that demands strict attention to quality measurement.
So says a recently released study commissioned by the National Committee for Quality Assurance and the Academy of Managed Care Pharmacy. Using data that suggest the danger of quality lapses in the complicated Part D drug benefits, the organizations urged the Centers for Medicare and Medicaid (CMS) to use pharmacy claims to measure the quality and efficiency of Part D plans. They have also requested that the CMS use the results to improve the quality of all health care provided to Medicare beneficiaries.
For more information, visit www.ncqa.org.
PQ Systems Reissues Classic Film
PQ Systems Inc. has reissued Right First Time on DVD to celebrate the movie's 50th anniversary.
The film was produced by London Television and released by the British Productivity Council in 1956, when the manufacturing world--especially in Europe--was focused on post-war recovery through quality improvement and production. Fifty years later, the black-and-white film, with its quaint speech and vintage dress, has assumed an almost timeless appeal.
In the story, after a customer announces that his company will accept shipments only from suppliers whose products have been manufactured strictly to specification, one of his suppliers struggles to conform to the new requirements. Company representatives visit Marks & Spencer, a retailer known for the high quality of its products, and then estimate that their company loses 15-20 percent of its costs due to poor quality. Subsequent improvements allow the supplier to overcome its quality challenges.
"While the film reinforces concepts of teamwork, continuous improvement, statistical process control and the concepts of quality leaders like W. Edwards Deming and Joseph Juran, it also gives a sense of progress," says Beth Savage, PQ Systems' marketing manager. "Characters in the film, unlike modern quality managers, seem shocked at the notion of quality improvement. We've come a long way since then."
Limited quantities of the video are available. For more information, visit www.pqsystems.com.
Outsourcing 101
A new book delves into the global offshoring movement to examine best practices and provide advice for organizations.
In Get It Done! A Blueprint for Business Execution ( Wiley & Sons, 2006) , authors Ralph Welborn and Vince Kasten provide a first-hand look at the problems many outsourcing organizations face. The statistics they include are startling: Only 19 percent of U.S. businesses have outsourcing strategies; the percentage skyrockets to 95 percent if only Fortune 1,000 companies are considered. The authors forecast that by 2008, the outsourcing market will grow to more than $500 billion, of which nearly $380 billion will be information-technology-related. In 2005, the outsourcing market was worth $335 billion.
To ease the organizational tensions outsourcing can cause, Welborn and Kasten offer some pithy tips and insights designed to demonstrate how the outsourcing phenomenon has changed the way business is done. In a word, say the authors, it's usually not the cost-saving nirvana companies hope for.
Welborn's and Kasten's insights about outsourcing include:
• If it looks too good to be true, it probably is.
• Too many outsourcing companies underestimate the work required to meet their client's needs.
• The prevalent "core vs. context" approach is becoming outdated.
• Often-contentious contract negotiations strain business relationships more than expected.
• What you don 't know will bite you.
• Outsourcing companies don't always do exactly what they say they are doing, and their day-to-day operations are virtually invisible to their clients.
• Companies are starting to reject long-term contracts.
To read more about the book, visit www.qualitydigest.com/qualityinsider and click the "Outsourcing 101" headline.
Quality News From China
SAQM Partners With Shanghai Mobile
The Shanghai Association for Quality Management and Shanghai Mobile Communication Corp. recently formed a new partnership.
The formation of the Scientific Research Base of Quality marks the first time the SAQM has partnered with a large private enterprise. Shanghai Mobile received the 2005 China National Quality Award and the 2005 Asian and Pacific Quality Award.
The Scientific Research Base of Quality will lead the Shanghai Mobile Performance Excellence Management project, which will help Shanghai Mobile improve its competitiveness through the use of quality management principles. The project will last for five years and be implemented in three phases.
Chinese Publish Book on Competitiveness
A three-year study into quality's role in China's competitiveness resulted in the recent publication of a book on the subject.
Quality Competition is the product of a research project called "A Study on the Quality Competitiveness of Chinese National Enterprises Under the World Trade Organization." The research was performed by the Shanghai Academy for Quality Management, which surveyed such major Chinese businesses as Shanghai Bao Steel, Shanghai General Motors, Shanghai Electric Power Station Group, Lianhua Supermarket, China Eastern Airlines and Shanghai Metro. Based on data from the organizations, SAQM compiled a quality index that can be used as a benchmark for other Chinese organizations.
Manufacturing Group Honored By NIST
The Corporation for Manufacturing Excellence (Manex) recently received the Newcomer of the Year award from the National Institute of Standards and Technology for its contributions to the manufacturing sector's effort to enhance competitiveness.
Selected from more than 1,500 applicants, Manex was honored at the 2006 NIST Manufacturing Extension Partnership Conference, which was held in Orlando in May. Manex provides advisory and implementation solutions such as lean and Six Sigma to small manufacturers, distributors and their supply chains, with the goal of increasing growth, productivity, quality and profitability. The Manufacturing Extension Partnership is a department of NIST that provides advisory services to manufacturers to stimulate and stabilize the U.S. manufacturing sector.
"Over the past year, we have strengthened our organization with an experienced management team and staff, and an expanded service portfolio," says Brent Meyers, Manex president and CEO. "By combining our capabilities with the MEP national network, we are able to help our clients implement business solutions that drive innovation and significantly improve bottom-line results."
Several other people and organizations also received MEP awards at the Orlando conference. Other winners include:
• MEP Practitioner of the Year--Petra Mitchell, Catalyst Connections vice president of operations; and Craig Cochran, regional manager of the Georgia MEP
• MEP Champion of the Year--Bill Donohue, A.L. Philpot MEP (Virginia); and Tom Palisin, Pennsylvania Department of Community and Economic Development manufacturing ombudsman
• MEP Innovator of the Year--Roxanne Baumann, Mike Hablewitz and Mike Klonsinski of the Wisconsin MEP
• MEP Unsung Hero of the Year--Deb Perkins, of the Ohio MEP; and C.J. Smith, director of business development for the Louisiana MEP
Changing Times
Bob Dylan was right. The times, they are a-changin'.
A recently released study found that most U.S. multinational companies have undergone--and are currently undergoing-- great changes. The typical company is using an average of five change-management strategies. Quality management techniques have become an important part of managing change, with 56 percent and 41 percent of respondents reporting that Six Sigma and total quality management (TQM), respectively, were their preferred methodologies.
Predictably, the vast majority of respondents reported that growth and cost reduction are the major reasons for their organizations' changes. Growth was the most-cited reason for change, with 88 percent reporting it as an "important" source, and 42 percent citing it as an "extremely important" source of change. Cost reduction was second on the list, with 76 percent reporting it as an "important" reason for change, and 35 percent citing it as "extremely important."
"Not surprisingly, companies that see change as necessary for growth are the faster growers," notes Karen Vander Linde, leader of change-management practice at PricewaterhouseCoopers, which performed the research. "Implementing change for cost reduction ensures that their growth will be profitable."
Other often-cited reasons for organizational change were domestic competition, new regulations, risk-management programs, energy costs and quality improvement programs.
PricewaterhouseCoopers interviewed 133 top executives from major U.S.-based companies. Almost all respondents--98 percent--reported that senior management's support of change activities is essential to success. Other critical success factors included employee involvement (95%), training programs (82%) and team-building exercises (77%).
For more information, visit www.pwc.com and view "U.S. Multinationals Have Much at Stake in Change Management, PricewaterhouseCoopers Finds."
Interoperability Standard Could Save Big Bucks
A metrology standard now under development has the potential to save millions of dollars for any organization that shares quality management data with its suppliers or original equipment manufacturers. The standard is being developed by a technical committee organized by the Automotive Industry Action Group. Attendees at June's Quality Expo Detroit got a sneak peek at how it will work.
The standard enables a truly seamless exchange of quality measurement information between disparate and proprietary gages and reporting tools. Currently, manufacturers--especially automotive manufacturers--lose millions of dollars and significant product development time because of a lack of interoperability with proprietary quality data collection systems. As a result, many companies are forced to integrate data from as many as 1,500 different data formats.
The open, nonproprietary standard is based on XML and aims to help companies recover the costs and resources associated with manual data integration. The standard eliminates waste and complexity from the supply chain, reducing 1,500 data formats to a single open-reporting format. Additionally, gages will be able to exchange variable, attribute and binary data used in statistical process control (SPC) and measurement system analysis (MSA) studies to different reporting tools.
A draft of the standard will be released during the third quarter of this year. For more information, visit www.aiag.org.
Developing Social Responsibility
File this under the "Not Easy But Worth It" category.
The International Organization for Standardization working group that's developing ISO 26000, which relates to corporate social responsibility, has close to 2,100 comments to examine before writing a second draft of the standard. The working group's 320 members met in Lisbon, Portugal, in May, where they discussed the first draft.
ISO 26000 is being developed for use in the public and private sectors, and by developed and developing nations. As an advisory standard, it will contain guidelines, not requirements. It's being developed by representatives from industry, government, labor, consumers, nongovernmental organizations, and service, support and research groups. It is expected to be published in the first quarter of 2009.
The committee will next meet in Australia in January or February 2007, where a second draft of the standard will be available.
For more information, visit www.iso.org. |