Commerce Department Aims to Ease International Trade Woes
The U.S. Department of Commerce
has released an eight-point standards initiative in an effort
to alleviate some challenges of international trade. The
initiative is in response to industry concerns that foreign
standards and technical regulation issues are becoming among
the greatest challenges to expanding exports.
"The Bush Administration remains committed to promoting
competition and opening new markets for U.S. goods,"
says Commerce Secretary Don Evans. "Standards and testing
are key to our international competitiveness. More and more
we're hearing that foreign standards and testing requirements
are keeping our products out of foreign markets. This is
the wrong approach that reduces efficiencies, limits competition
and increases prices for consumer goods. This initiative
is an effort to create a more level playing field around
the world."
The eight points are:
Developing a commerce global standards activity assessment.
The Technology Administration, through the National Institute
of Standards and Technology, will conduct a standards activity
assessment of existing Commerce Department programs and
efforts to reduce standards-related barriers in foreign
markets. Following consultations with industry and other
stakeholders, recommendations will be made to the Commerce
Secretary for future action.
Reinforcing expertise in key markets. NIST and
the International Trade Administration have developed a
newly redesigned intensive training program for standards
liaisons posted abroad.
Devising an effective training and outreach program.
NIST and ITA, in cooperation with U.S. standards development
organizations, will develop a standards training program
for all Commerce Department foreign commercial service officers.
Creating a "best practices" database.
The Commerce Department will develop a database of best
practices in addressing standards issues in foreign markets.
Expanding the early warning system. The Commerce
Department will strengthen and expand Export Alert!, a free
Web-based service to disseminate market intelligence and
information on standards developments in key priority foreign
markets in Europe, Asia and Latin America.
Partnering with the President's Export Council on Standards
Leadership. The Commerce Department will support the
development of a dialogue on standards within the proposed
President's Export Council subcommittee on technology and
competitiveness.
Reaching out to U.S. industry. The Commerce Department
will host a series of industry-specific roundtable discussions
to gather input from U.S. industry on the most pressing
standards issues and priority foreign markets.
Appointing a liaison at the International Trade Administration.
A senior official will act as ITA's standards liaison with
U.S. industry to ensure that priorities on standards are
promoted through the Commerce Department's international
policies and programs, and will also work with other U.S.
government agencies.
The Commerce Department is currently actively engaged
in standards-related activities, including ensuring recognition
and use of globally relevant and internationally recognized
standards domestically and in the global marketplace, promoting
worldwide acceptance of U.S. test and calibration data to
facilitate the marketing of U.S. products, and providing
assistance to other government agencies, industry, trade
associations, exporters, and standards development organizations.
To view a full copy of the initiative, visit www.commerce.gov.
Insiders Consider E-Based Management and
Auditing
Representatives of accreditation
bodies and certification providers recently convened to
explore the advantages and challenges that accompany e-based
management systems.
An internal report from the International Accreditation
Forum states: "The subject of e-based management systems
is complex, broad in scope and evolving at an extremely
fast pace. It is clear that organizations are implementing
these systems because they bring value benefits in terms
of increased productivity, process control and cycle time
enhancement."
During the March meeting, the group identified four areas
that must be recognized and accommodated in order for an
e-based management system to be sound: guidance, audit competence,
recommendations for assessment mechanics and potential certification/registration
body models. The learning session wasn't intended to develop
guidance or direction in these areas but rather to identify
areas in which guidance is needed.
NetAudit, an e-based auditing system, was discussed and
led the learning team to conclude that remote auditing is
possible using readily available technology. However, several
considerations must first be taken into account, including
security of access to the client's system. The report states:
"The real question is the confidence of the client
in the certification/registration body. The certification/registration
body may have to execute a binding nondisclosure agreement
with the client to obtain access."
The group also concluded that assessors should require
specialized training to work within an e-based assessment
environment, including a basic understanding of software
development and a high level of business process knowledge.
The meeting included representatives from ANSI-RAB, SCC,
RvA, SINCERT, JAB, UKAS, JAS-ANZ, TGA, IAAR, IqNET and ITIC.
Application providers and consultants from Vintara, EtQ
Inc. and BQPM LLC were also present.
Quality Digest will report more detailed findings from
the knowledge-sharing session in next month's issue.
Manufacturers Need to Improve Selling
and Ordering Practices
Fifty-seven percent of manufacturers
have problems generating error-free customer quotes, proposals
and orders, according to a recent comprehensive study conducted
by KRC Research and released by Blue Martini Software Inc.
The study focuses on manufacturers across dozens of segments
in the United States, the United Kingdom, France and Germany.
It highlights some of the challenges manufacturers face
in their sales and order processes.
Many manufacturers have adopted lean manufacturing and
production principles but haven't applied those principles
to their sales and order processes, a practice that Blue
Martini calls Lean Selling. Blue Martini asserts that Lean
Selling streamlines the sales process beginning with needs
analysis and continuing through proposal generation, configuration,
pricing, quoting and ordering.
Conducted during February and March, the study finds that
manufacturers' sales and order processes are typically inefficient,
complex and full of errors. This is especially the case
for industrial and high-technology companies with complex
products and selling practices.
Some key results of the study follow:
Seventy-nine percent of manufacturers surveyed have products
that are highly configurable or difficult to specify. The
result is an increasingly complicated selling process involving
multiple selling stages, multiple people involved in generating
and reviewing each proposal, and an increasing number of
product permutations.
Thirty-nine percent of survey respondents have consistently
error-ridden orders, even after the orders move from sales
to manufacturing.
Almost 70 percent of those surveyed face situations in which
customer requirements constantly change, requiring rework
of several proposals.
Thirty-six percent of those surveyed said that 51 to 75
percent of content in each proposal requires modification
or complete redrafting.
Although 73 percent of manufacturers claim to have tools
in place to automate the needs analysis process for products
and services and proposal generation, only 38 percent have
improved the accuracy, quality and consistency of proposals.
A smaller percentage (21%) say that they have reduced costs.
However, more than half of the manufacturers surveyed (60%)
expect to evaluate better software tools over the next year
to help improve their sales processes, including needs analysis
and delivery of highly accurate proposals.
KRC Research, a strategic opinion and market research
firm, was commissioned by Blue Martini Software to conduct
the survey. The majority of companies cited at least $75
million in revenue. Survey results are based on 213 interviews.
To learn more, visit www.bluemartini.com.
Is Your Organization Suffering From Brain
Drain?
There are several reasons a
company would suffer from the loss of knowledgeable employees:
Baby boomers are reaching retirement age, and the corporate
tide is flowing toward rapid growth, turnover, mergers,
acquisitions and internal redeployment.
In an effort help management retain knowledge in their
organizations, the American Productivity and Quality Center
embarked on a project to learn how the principles, tools
and practices of knowledge management can be applied to
retain valuable knowledge. The result of APQC's undertaking
was a best-practice report based on information from more
than 30 benchmarked companies.
"Retaining Valuable Knowledge: Proactive Strategies
to Deal With a Shifting Work Force" summarizes the
findings of the five-month study that involved site visits
to leading organizations such as Best Buy, Corning Inc.,
Northrop Grumman, Siemens, The World Bank and Xerox Connect.
These organizations, among others, identified best practices
in retaining key knowledge and information despite increasing
attrition.
"We identified practical methods to capture, transfer
and access knowledge," says Carla O'Dell, APQC's president
and special adviser for the consortium study. "This
report will help organizations that want to build a knowledge-sharing
culture, capture valuable information before employees walk
out the door, and decrease the time to competency of new
hires by giving them access to lessons learned and communities
of knowledgeable people from whom they can learn."
The study is intended to assist organizations in designing
and implementing appropriate systems, determining support
structures and roles, estimating costs, identifying enablers
and barriers to success, and assessing and measuring the
effectiveness of knowledge retention strategies. It includes
five case studies.
Bill Baker, knowledge management and benchmarking champion
at Raytheon Co., explained the benefits his organization
reaped from sponsoring the study. "We used the study
to understand what others were doing and to help craft our
own knowledge management strategy, including a valuable
training session for our knowledge management champions,"
he explains.
To view an executive summary or to purchase the report,
visit APQC's online bookstore at www.apqc.org/pubs.
Canadian Consumers Assess the State of
Service Quality
When asked to provide their general views on the quality
of service they're receiving, about 75 percent of Canadians
rated their overall perception as either good or excellent,
according to a recent survey conducted by the National Quality
Institute.
The NQI survey on service quality in Canada took a look
at Canadians' impressions of service quality in several
sectors, a few of which dropped in satisfaction since 1997,
when NQI conducted a similar survey. Telephone companies
and airlines showed the largest decline in popularity, which
have gone through significant changes in recent years. "What
is intriguing in this sector is that the prime reason for
taking a deregulated approach was to open the industry to
competition and to benefit consumers," comments Dan
Corbett, president and CEO of NQI. Large retailers and postal/courier
service companies showed the highest improvement.
The survey also revealed that Canadian consumers are happier
with their country's services than they are with those of
the United States by a ratio of five to one. "The higher
the income, the more positive perception there was for U.S.
organizations," Corbett notes. "However, Canadians
gave a strong response to Canadian organizations. This should
be good news in terms of competitive advantage on a service
basis."
Although Canadian consumers are generally satisfied with
their service quality, more than half of the respondents
stated that they've had a negative service experience. The
most commonly cited negative experience (43%) was that a
service representative had displayed a surly or hostile
attitude.
To see the survey and read Corbett's commentary on the
results, visit www.nqi.ca.
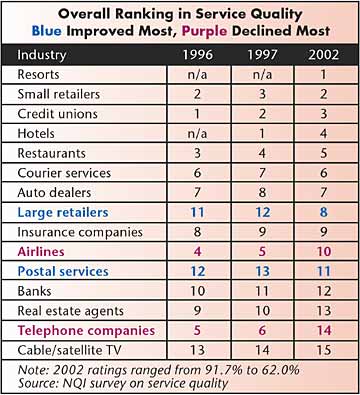
ISO Seeks to Standardize Personnel Certification
Personnel certification programs
exist in professions ranging from health care to financial
planning to nondestructive testing as a means of verifying
professional ability. However, these certification programs
frequently vary from country to country, and in some cases,
facility to facility.
In an effort to facilitate the global mobility of personnel,
the International Organization for Standardization has developed
ISO/IEC 17024, Conformity assessment--General requirements
for bodies operating certification of persons.
The standard provides guidelines for managing the qualifications
and certification of people, including procedures for the
development and maintenance of a certification scheme. It's
designed to help certification bodies conduct structured
evaluations of personnel using objective criteria for competence
and grading, and to ensure impartiality of operations and
reduce conflicts of interest.
"To be able to choose a person with the competence
needed, or for a person to be able to demonstrate specific
competencies, a defined certification scheme is particularly
useful," notes Thomas Facklam, chairman of the International
Accreditation Forum and convener of the working group that
developed the standard.
ISO/IEC 17024 addresses the structure and governance of
the certifying body, the characteristics of the certification
program, the information required to be available to applicants,
and the recertification initiatives of the certifying body.
"Only the harmonization of the system for developing
and maintaining certification schemes for ersons can establish
the environment for mutual recognition and the global exchange
of personnel," continued Facklam.
ISO's committee on conformity assessment working group
17, "Certification of persons," and the International
Electrotechnical Commission developed the standard. It's
available through ISO national member institutes, a list
of which can be found at www.iso.org.
ROMER CimCore and FARO Settle Patent Suit
ROMER Inc. and CimCore Corp.
have reached a final settlement with FARO Technologies Inc.
in the patent- infringement lawsuit pending in the Federal
District Court for the Middle District of Florida.
FARO brought about a lawsuit in January asserting that
ROMER CimCore's seven-axis 3000iSC scanning arm technology
infringed on FARO's patent of its seven-axis arm technology.
Under the terms of the settlement, FARO cannot reassert
the patents-in-suit against any of ROMER and CimCore's current
products, nor can FARO bring a suit against ROMER and CimCore's
3000iSC seven-axis scanning arm on any patent currently
held or obtained by FARO in the future.
FARO has reserved its right to sue ROMER CimCore if it
introduces any seven-axis articulated CMM products which
have other than insubstantial differences from FARO's current
products. FARO's seven-axis patents continue to be valid.
The court dismissed ROMER and CimCore's counterclaim that
FARO's patents for its seven-axis CMM were invalid.
ASQ
Koalaty Kid Conference Breaks Attendance Records
"Different Journeys, Same
Destination," was the theme of this year's three-day
Koalaty Kid Conference, held earlier this year in Ottawa.
For the third consecutive year, the conference set an attendance
record with 505 attendees, 103 more than last year.
Sandra Cokeley-Pedersen spoke of her experience with Pearl
River School District in Pearl River, New York. The district
was one of the recipients of the 2001 Baldrige Award. Conference
sessions discussed various classroom tools and the plan-do-study-act
cycle.
American Society for Quality Koalaty Kid Alliance President
Connie Faylor addressed conference attendees on ASQ's expanding
role in education. ASQ plans to widen its quality in education
outreach, namely by co-sponsoring the National Quality in
Education Conference, slated for next year.
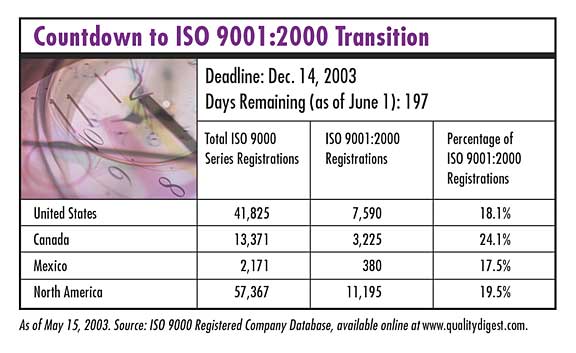
INDUSTRY NEWS
Cyber
Optics Corp. has transferred its patented digital range
sensor technology and license to Quality Vision International.
Through Optical Gaging Products, a QVI company, design teams
will utilize the technology to expand and improve upon existing
laser measurement capabilities. Manufacturing has been transferred
to OGP's facility in Rochester, New York. An existing clean
room will be transformed into the laser technology and manufacturing
center. To learn more, visit www.ogpnet.com.
Factory Logic Inc. and KAIZEN Institute of America have
agreed to jointly offer a combination of lean manufacturing
software solutions and consulting services. Factory Logic
offers the Streamline lean factory management system, and
KIA provides consulting services to both manufacturing and
service industries. For more information, visit www.factorylogic.com
or www.kaizen.com.
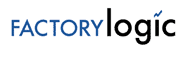 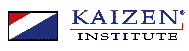
Perceptron
will provide 3-D scanning technology to Carl Zeiss Co. for
use in its EagleEye Navigator system. The Zeiss system integrates
a Perceptron laser sensor and 3-D scanning software with
a horizontal-arm coordinate measurement machine to perform
data collection and inspection applications. Perceptron's
ScanWorks Toolkit software provides mathematical algorithms
that extract dimensional features from a cloud of scan data,
such as the location and diameter of holes and slots. To
learn more about Perceptron, visit the company online at
www.perceptron.com.
CogniTens
Ltd. and QMC LLC have reached a mutual agreement for integration
and distribution of OptiCell, an automated 3-D noncontact
robotic cell for online repetitive part measurement.
CogniTens developed the noncontact 3-D measurement solution
for the robotic cell, which is based on its Optigo series.
QMC provides quality solutions and performs the integration
of flexible measurement systems to deliver an integrated
turnkey noncontact measurement station. For more information
about CogniTens, visit www.cognitens.com.
Corning
Tropel Corp. has been named worldwide distributor for Optical
Dimensions LLC's Lasercheck application, a noncontact surface
roughness measurement gage. As stipulated in the agreement,
the product will be marketed as the Tropel Lasercheck. The
Tropel Lasercheck measures the average roughness of materials
including metals, magnetic media, plastics and ceramics.
Product specifications for the Tropel Lasercheck are available
at www.corning.com/semiconductormaterials.
The
American Productivity and Quality Center has launched a
consortium benchmarking project to study how process improvement
leaders incorporate knowledge management into their Six
Sigma and lean processes.
The consortium, "Replicating the Gains from Six Sigma
and Lean: Capturing and Transferring Knowledge and Best
Practices," offers participants an opportunity to explore
how collaboration, as well as knowledge-capture and transfer
of processes, can be integrated into performance improvement
methodologies to bolster the replication of meaningful results.
The benchmarking project will commence June 24 in Houston.
For more information, call (800) 776-9676.
Hexagon's
Swiss subsidiary TESA S.A. has acquired Sud Mesure S.A.
Through TESA, Hexagon will expand the business into the
noncontact arena and continue to develop manual 3-D vision
machines.
In the last year, Hexagon has acquired Brazilian metrology
distributor and agent Quality Ltd. and CEJohansson, the
metrology company of Newport Corp. For more information,
visit www.hexagon.se.
Metrolog
software will run on all DEA and DEA Brown & Sharpe
machines. Under the software interface development collaboration,
both companies agree to supply each other with the necessary
support, electronics, mechanical parts and software without
limitations.
"Customers will have the ability to equip all existing
and new DEA Brown & Sharpe measuring machines (touch-trigger
probes or scanning heads) with Metrolog software,"
says Ettore Bandieri, managing directory of DEA.
Visit Metrologic Group at www.metrologic.fr
and DEA at www.dea.it.
|