by William M. Gascoigne
Like a fashion model who's also a member of Mensa, 3-D computer-aided design (CAD) lends support to the argument that first impressions never tell the whole story. Frequently people are so enamored with the 3-D visuals that they forget to look deeper for the real value of this approach.
3-D technology has played a major role in the revolutionary developments that have taken place across design and manufacturing during the last decade. Rather than limiting a 3-D design discussion to visual capabilities and the input of ideas into the design process, this article will go further and examine what happens after the input of product ideas is completed and strategic opportunities occur, particularly in the area of product quality.
We must look beyond the surface of 3-D.
Fuji Electric Retail Systems
Nowhere is the art and science of vending machines more advanced than in Japan, where limited land for stores have made these unmanned merchants a popular alternative. About half of these distinctively designed machines, called jidoohanbaiki , handle beverages. The rest dispense other everyday staples, including food--everything from snacks to entire meals--fresh flowers, literature, CDs and clothes.
Not only has fierce competition spurred a diversity of artful exteriors, it's also created demand for more sophisticated functionality in jidoohanbaiki , which now cater to personal preferences. For example, coffee vending machines grind beans and brew fresh coffee for each customer. They then add toppings, offer a choice of hot or frozen drinks, and automatically place a lid on the cup.
"Simply inserting money to get the product is nothing special anymore," says Tetsuo Suzuki of Fuji Electric Retail Systems. "A company couldn't survive in this competitive market by providing functionality that simple."
In developing its product line, the company looks at each new vending machine as a platform, a master design that may require modification for each individual customer and that customer's merchandising needs.
At one time, Fuji Electric Retail Systems tried to produce product drawings automatically by creating a database of parameters for each new product. However, designs often were completed before the database rules could be defined, and the database failed to keep up with the development cycle.
For highly innovative companies with constantly adapting products, the time required to "automate" a design process must be evaluated against the product's life cycle. In some cases, the time to automate actually introduces waste into the development process.
Instead, Fuji Electric Retail Systems turned to concurrent engineering and 3-D design, using CoCreate Software Inc.'s OneSpace Designer Modeling, which enabled the company to achieve faster development times and lower development costs through 3-D virtual prototyping. Additionally, the time to design sheet-metal components to match customer merchandise configurations was cut by 30 percent, while product quality increased by leveraging the 3-D model to simulate plastic mold flow and stress analysis for plastic components.
"To stay competitive, we need to adapt quickly to changing industry needs," says Suzuki. "Designer Modeling best suits our model for success."
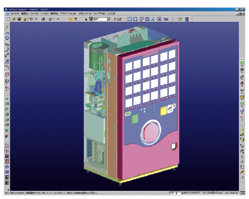
|
Whether products are drawn, drafted or modeled, much of a product's quality is determined during design. Although any good development department constantly works to identify and resolve design-centered quality issues, sometimes issues remain hidden, surfacing only during late-stage prototyping or, worse, during manufacturing ramp-up. Even more regrettable are when issues emerge later, in the field, where the costs to service departments and to the company's reputation can be astronomical. 3-D product development's strength lies in eliminating this risk and waste.
Companies that see the end result of 3-D design as only automatically generated 2-D drawings are missing the point. Rather than considering a 3-D model as a step above a 2-D drawing, view it as a different--and better--world. A 3-D computer model is so lifelike that companies can apply quality control measures to the virtual model more effectively than they used to do with a physical model. These test applications in the virtual world are not only easier, faster and cheaper to execute, but the tests themselves are more comprehensive and better able to identify problematic design aspects.
One example is prototyping. A perfect prototype is often the final milestone before a product moves from design into production. It ensures that all subassemblies fit together without conflict, moving parts function correctly and manufacturing engineers have a mockup to work from to create assembly sequences.
However, the path to a perfect prototype is inherently iterative. Traditionally, a series of imperfect prototypes might be created to work out problems before the design is finalized. In designing a product in 3-D, the expense and time formerly associated with multiple physical prototypes are eliminated by storing iterations inside the computer. Because 3-D models can be assembled and animated, an entire product can be perfected for proper clearances, tolerances and interference before the physical product is built. Motion can also be simulated to evaluate the working behavior of moving parts.
Another example is testing for real-world conditions. A product's casing, for example, must be durable enough to protect the device from stress or strain. Fabricators build a physical prototype, and product testers place the case under the physical conditions the product might expect to experience. If the prototype breaks, it's back to the drawing board to find a more suitable material or thickness. With 3-D design, however, products can be tested under the same working conditions, including stress, displacement and heat. Also, a much broader range of materials can be tested without ever leaving the computer desktop.
There seems to be no limit to the kind of simulation that can be applied to 3-D data, whose mathematical attributes can comport with even highly specialized simulation programs developed by researchers. More common needs of computerized product testing are now satisfied with software modules that plug into the solid modeler itself. For sheet-metal fabrication, a bend deformation module will affect the shape of the 3-D model the same way fabrication tools affect the material. If a punch is planned too close to an edge, the metal buckles on the screen. A designer can then immediately change the location of the punch in the 3-D model--no time or materials are wasted. Similarly, mold analysis will predict flaws in molded plastic as it hardens, thus enabling the cost-effective manufacture of designs with more complex curves.
Due to the development of 3-D simulation applications, many companies can eliminate iterative physical prototyping and spend those precious dollars only one time--during the final prototype. The ability to archive dozens of design cycles within the computer saves an immense amount of money, considering that a physical prototype might cost as much as $10,000. The timeline spanning idea conception to factory reproduction has also shortened to what was previously considered impossible. 3-D design and simulation can replace much of the work that used to be done through physical test batteries. In this way, 3-D CAD ensures a higher quality of product.
Some companies consider the various 3-D systems to be essentially the same. In reality, there are two distinctly different approaches to 3-D product development: history-based (sometimes known as feature-based modelers) and the history-free method of dynamic modeling. Each approach is applicable to different types of companies.
In time-pressured industries, a design issue might be noticed at the last minute before production starts, a small suggestion to improve the quality of the product might be proposed or a feature might be added based on a competitor's actions in the market. For a complex part, it might take days or weeks for someone to research how a part was made in a feature-based modeler, and then reconstruct the model to incorporate the change. All the while, factory equipment sits idle, and product revenues are delayed. With a dynamic modeler, the change can be made directly within minutes or hours.
Product development that demands real-time response to new and changing information is particularly well-suited for dynamic modeling. These fluctuating conditions can quickly tangle a history tree because they represent change that wasn't planned during design.
A dynamic-modeling approach excels for companies confronted with frequent or unpredictable change, or for products with short development cycles. Dynamic modeling is history-free and creates a free-form design environment that rapidly creates products with all the precision and power expected of a 3-D system. Dynamic modeling's strengths are also well aligned to companies that leverage lean principles in their development process.
Take, for example, waste reduction. Design-data management systems directly support the principle of design reuse by not redesigning a product or part that's been created before. This eliminates the waste of duplicative effort. But design reuse isn't just about finding what already exists. It's also about repurposing what already exists into the next generation of product.
This is an area where dynamic modeling dominates. History trees are similar to software programs in that they don't work if you cut the instruction code in half. Dynamic modeling, however, lives in a world of geometry, which allows an existing product to be cut in half any way the engineer desires, and then easily morphed into the next-generation product. Because engineers won't have to start from scratch on new product development, companies gain a significant head start on development and can shave weeks or months off of projects.
Sharing without limitations is another benefit of dynamic modeling. Interoperability problems can create a lot of waste during the development phase, when models must be re-created rather than carried forward. Geometry is the only common element across all 3-D systems. Because dynamic modeling thrives in a geometry-based world, it can import data from any other 3-D system and work with it, eliminating the waste normally associated with a lack of interoperability.
Equally important is that any member of the design team can pick up a design and make changes without having to know the history behind the series of steps taken to create the model. With dynamic modeling, a shape is a shape is a shape, and the user can focus on the end result of design in form, fit and function. It's not uncommon in companies that standardize designs with dynamic modeling for engineers to pass models around the team for each other to work on during development. This is the difference between a design team and true "team design." The latter eliminates resource bottlenecks, brings different perspectives to bear on problems, and fosters innovation and creativity through collaboration.
These are just some of the reasons why dynamic modeling is described as a forward-looking design process.
A quality product--or quality in anything--depends upon the quality of processes that go into its creation. Even well-conceived ideas require the right execution before they become successful products. This is where the business process of developing products comes into play, sometimes known as product life cycle management (PLM). Although the PLM process spans the entire company, the quality gains typically start with the interactions of the design team and how it works together to develop products.
Design-data management systems have grown around 3-D modeling, creating vital design collaboration when working with mechanical assemblies. These products allow a design project to unfold naturally with more room for creative solutions. Like a network file server, design-data management systems allow multiple designers access to all 3-D files on a project. Unlike a network file server, design-data management updates the changes to the design as they happen, and all designers can view the entire master assembly simultaneously.
To take an example of how this affects business process quality, let's say that I'm collaborating with a colleague in writing an article. I save my work in progress on a network file server. My colleague and I can read the same document at the same time, but one of us has a read-only copy. Only one of us can save our edits to the document; the other might lose the modifications if saved under the same name. If the file is under a different file name, two versions of the same article could circulate. A design-data management system, on the other hand, allows us both to make changes at the same time, see each other's changes as they happen, and save the file without accidentally losing information.
This would seem a bit chaotic for the task of writing, but in the geometry of physical design, this chaos is desirable because it accelerates the workflow and enables the creation of design solutions without impediment. Without an integrated model-management system, there would be a lot of waiting around for files to become accessible for viewing and editing, plenty of redundant modeling and a great deal of lost data.
Managing design data between multiple users also extends to the transition from design to manufacturing. By organizing and tracking the various stages of a design, data-management systems provide assurance that released designs contain the most current parts and subassemblies. This eliminates rounding up renegade designs from hard drives, manually comparing different versions of the same part or finding versioning errors during prototyping.
It's essential that collaboration is built into the entire process to connect both people and data. Working across a typical organization takes more effort than going to the elevator and finding the right floor to meet with someone. The average team is made up of people both internal and external to the company.
Collaboration takes many different forms and can use various tools and technologies for stimulating dialogue between people. These are used to support a business process that fosters teamwork, the free flow of ideas and continuous communication. As a result, companies have a tremendous opportunity to lower the total lifetime costs of a product. These costs fall under the different stages of a product's life cycle, such as design, manufacturing, service and warranty.
For example, manufacturing and quality teams in direct communication with designers and engineers can exchange ideas for simple part modifications, resulting in lower manufacturing costs and increased quality. Similarly, input from maintenance and warranty departments give designers guidance in terms of access for servicing and replacing parts. A part that takes less time to manufacture, or an assembly that takes less time to service, adds greater quality to the business process. These measures reduce a product's total lifetime costs for the company.
When thinking about the role that 3-D design and software applications supporting the PLM process play in your overall quality program, consider one last thought. Quality takes many forms within the company. Although the physical measure of product quality is often related to customer satisfaction, the management measure of business process quality is often related to a company's profitability. Obviously, both are very important.
William M. Gascoigne is CEO of CoCreate Software Inc. and has more than 30 years of experience in information technology. He served as executive vice president of worldwide operations for Structural Dynamics Research Corp. and as vice president of worldwide marketing at Applicon Inc.
|