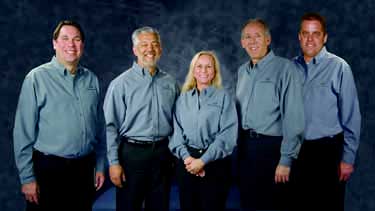
Boeing Co.'s Gold-Award-winning C17 Stuffed Tailcone Team
(left to right): Matt Correa, Daniel Munoz, Teri Garten, Mark Adams, Matt Swan |
The Triumph of Teamwork
One of the most eagerly anticipated events at the annual American Society for Quality World Conference on Quality and Improvement is the International Team Excellence Competition. This year's competition, held during the May conference in Orlando, Florida, was extremely spirited and close, and included the first three-way tie (for second place) in the 22-year history of the event.
The Gold Award was presented to the Boeing Co.'s C17 Stuffed Tailcone Team. Responding to safety concerns raised by factory personnel, the Stuffed Tailcone Team used problem-solving tools to generate solutions that eradicated unsafe conditions during installation, and initiated process improvements with positive results in the areas of quality, cost and scheduling, with a direct effect on organizational goals.
The unprecedented three-way tie for the Silver Award allowed three teams to be recognized for their quality improvement efforts. The Boeing Co.'s C17 on-board inert gas generating system II (OBIGGS II) project replaced the existing system that protects the fuel tanks from explosion by filling the volume above the fuel with nitrogen-enriched air. The OBIGGS II team greatly enhanced reliability of the inerting system through outstanding teamwork, innovation and dedication. Another Boeing group, the C17 World Class Safety Team, embarked on a journey to become world-class in safety. By benchmarking best-in-industry companies, employing expert safety consultation and using root cause analyses, the team saw dramatic improvements from the development of an integrated safety management system. The Department of Children and Families, Suncoast Region, Team Scanit, developed, piloted and implemented an electronic imaging system for receipt, storage and retrieval of all paperwork associated with the region's 190,000 public assistance cases, saving $269,816 the first year and $310,126 annually thereafter.
The Bronze Award went to the CSX's Locomotive Fuel Process Improvement Team, which increased shutdown time of idling locomotives, reducing fuel consumption across CSX. The project used CSX's accountability model and Six Sigma's define, measure, analyze, improve and control process. The team generated savings of more than 14 million gallons of fuel worth $28 million.
Congratulations to all the winners, as well as everyone who participated. For more information about ASQ or next year's World Conference on Quality and Improvement, scheduled for May 5–May 7, 2008, at the George R. Brown Convention Center in Houston, visit online at http://wcqi.asq.org .
Global Six Sigma Awards Call for Entries
WCBF is launching its Global Six Sigma Awards 2007 program by issuing a call for entries from organizations across the globe that employ Six Sigma to secure business improvement. The focus of this unique awards program is not on the process of Six Sigma itself, but on the organizational success achieved through the adoption of Six Sigma.
Entries are invited for the following nine organizational categories:
• Best achievement of Six Sigma in manufacturing
• Best achievement of Six Sigma in service and transactional environments
• Best achievement of integrating lean and Six Sigma
• Best achievement of design for Six Sigma and innovation
• Best achievement of Six Sigma in health care
• Best achievement of Six Sigma in financial services
• Best achievement of Six Sigma in government and defense
• Best achievement of Six Sigma in sales and marketing
• Best achievement of Six Sigma in outsourcing
There will be two additional awards, selected from all category entries: the Platinum Award, for outstanding global organization achievement through Six Sigma (sponsored by Genpact), and the best use of Six Sigma by a small organization.
The first deadline for entries is 11:59 p.m. (PST) on Friday, June 8. The late deadline for entries is 11:59 p.m. (PST) on Friday, June 22.
The awards will be presented at the Global Six Sigma Awards Gala Dinner on Wednesday, October 24, 2007, at The Rio All-Suite Hotel & Casino in Las Vegas. The Gala Dinner coincides with WCBF's Global Six Sigma Summit, the largest gathering of CEOs and senior executives passionate about Six Sigma.
For more information, visit www.tgssa.com.
Do the Math
Last month's "Do the Math" sent you to an Oct. 15, 2005, San Francisco Chronicle column by Steve Rubenstein entitled "Cal math lecture to feature binge-eating cartoon dad." The article was reporting on an upcoming lecture at University of California, Berkeley, by Ken Keeler, one of three writers for "The Simpsons." Keeler and the other writers, all mathematicians, often work math jokes into Simpson episodes. Rubenstein writes, "Homer, in a dream, wrote that 1,782 to the 12th power plus 1,841 to the 12th power equals 1,922 to the 12th power. (It does.)"
Rubenstein's parenthetical remark is what got him trouble with math nerds across the galaxy. Because, in fact, the equation is wrong.
You can solve this empirically:
1,78212 + 1,84112 =
1.025397835622633634 e+39 +
1.515812422991955541 e+39 =
2.5412102586145891762 e+39
1,92212 = 2.541210259314801410 e+39
As you can see, they are only equal up to the ninth digit after the decimal.
Or, you could have solved this instantly if you had been familiar with Fermat's Last Theorem: "It is impossible to separate… any power higher than the second into two like powers." Put another way, for n > 2, there is no solution for an + bn = cn.
Congratulations to Carl Toering for correctly answering this month's puzzle. Your Woot.com prize is on its way.
This month's puzzle is not so much a math error as a reporting error. Go to www.qualitydigest.com/april07/columnists/jharrington.shtml, spot the error and send us your answer by clicking the feedback link at the bottom of this page. And for Pete's sake, send us some puzzles.
Quality Management for Education
The International Organization for Standardization has published specific guidelines for organizations in the education sector wishing to benefit from the implementation of ISO 9001.
ISO/IWA 2—"Quality management systems—Guidelines for the application of ISO 9001:2000 in education," contains the full text of ISO 9001, followed by specific text making the standard easier to understand and implement in the education sector.
Although ISO 9001 users already include educational establishments, the guidelines are intended for organizations at all levels, providing all types of education, from elementary schools to higher education, as well as special and adult education, distance and e-learning.
For more information, visit www.iso.org.
Lean For Dummies Released
With Lean For Dummies (Wiley, 2007), those looking to gain basic information about the lean process now have a place to turn. The principles and techniques of lean began more than 50 years ago at Toyota Motor Corp. Since then, lean has become a watchword among industry people as the most consistently successful approach to organizing and operating a business or institution. However, many people still have never heard the term lean and have no idea how the concept applies to business practices.
The newly published first edition of Lean For Dummies , by Natalie J. Sayer and Bruce Williams, thoroughly explains how lean helps organizations improve business results by reducing and even eliminating the waste that occurs naturally. This includes wasted time, energy, materials, money, space, employees, supplies and even opportunities.
Written for people at all levels of business, Lean For Dummies reveals not just how to recognize waste, but also how to reduce or eliminate it to increase efficiency and profit. In plain English and an easy-to-use format, the book teaches readers how to:
• Understand what lean is and how it's implemented
• Speak the language of lean
• Identify and eliminate the seven forms of waste
• Construct and use value-stream maps and other lean tools
• Improve business with kaizen —the basis for continuous improvement
• Engage people in a lean transformation
Like all books in the For Dummies series, Lean For Dummies concludes with the "Part of Tens," including "Ten Best Practices of Lean," "Ten Pitfalls to Avoid" and "Ten Places to Go For Help." The handy, tear-out "Cheat Sheet" includes lists of lean fundamentals, lean Japanese terms, the "5S of the Workplace" (sort, straighten, shine, standardize and sustain), and more.
For more information, visit www.wiley.com/WileyCDA/WileyTitle/product Cd-0470099313.html.
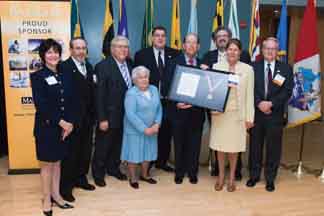
Terry Collard (second from right) and Chimes International leaders with their Maryland Senate Productivity Award |
Day in the Life
Chimes International Ltd., based in Baltimore, offers education, services, support and employment to more than 12,000 people with disabilities throughout the Mid-Atlantic region of the United States and in Israel. Basic to Chimes' system of service is the active involvement of the people served, their families and advocates. Equally important is a well-trained, dedicated staff and board of directors who are committed to excellence. Fundamental to all of Chimes' activities is the maintenance of the highest quality and integrity.
Following, Terry Collard, vice president and chief strategic officer of Chimes International, discusses Chimes' work to achieve optimum quality in all of its operations.
Quality Digest: What quality methodology (or methodologies) has Chimes implemented?
Terry Collard: Chimes uses the Baldrige criteria as a template for assessing and improving organizational performance. In addition, process improvement (PI) teams with representation from departments involved in the process have been used for the past two years to address areas where performance or outcomes are problematic.
The PI team begins with the team charter to outline the work, the milestones and the outcomes that they wish to achieve. They document the process using flowcharts, identify measures and key requirements, and develop a communication plan. Each PI team selects the most appropriate quality tools for the particular process at hand. Root cause analysis has consistently provided insight for many PI teams.
One of the most important byproducts of the PI teams is improved communication across departments and more insight into the challenges each department must address internally.
QD: How many people are in your quality department?
TC: Each subsidiary within the Chimes family of services has a director who is responsible for quality. Each director of quality has one to three people reporting to him or her. Every employee is responsible for assuring that quality services are delivered and that desired outcomes for people receiving services are achieved.
QD: How has Chimes trained its employees in quality techniques?
TC: Chimes trains employees during new-employee orientation, through policies and procedures, and through consultants from the American Society for Quality. Chimes hosts an annual best practices conference that focuses on quality techniques and provides a forum for each subsidiary to share its successes.
QD: What are some quality challenges that Chimes has encountered?
TC: Our biggest challenge was in changing the culture of our human service organization. Human service organizations have historically measured quality intuitively (i.e., "I know it when I see it"), or as measured by regulators through compliance with regulations during surveys.
QD: Specifically, how has the company dealt with this situation?
TC: Segmenting our customers, identifying key requirements for each segment and defining metrics to measure the progress toward delivering key requirements resulted in a metrics system being developed that captured data on a site level and rolled it up to a department, subsidiary and corporate level. The measurement system has provided managers the ability to monitor processes and outcomes, and provide consistent feedback to the workforce.
Terry Allen Perl, Chimes' CEO and president, provided leadership and support through meetings with key staff, roundtables, articles in internal and external organizational publications, and conducting quarterly performance reviews with each subsidiary based on the measurement system. The final piece of the puzzle, a new employee evaluation system that ties each employee's performance to the major drivers of the organization, is being piloted this fall.
QD: What is a quality tool that your quality department couldn't live without?
TC: The most important single quality tool is flowcharts. The work of the PI teams has been vital to improving quality throughout the organization, and the flowcharts allow everyone to see where breakdowns and problems occur.
Got Crises?
If you're dealing with a crisis in your manufacturing system, a guide from the Automotive Industry Action Group could help.
The guide, called "Business Continuity Planning Toolkit for the Automotive Supply Chain," was updated to help automotive companies of all sizes and structures identify and develop a plan to ensure the safety and security of their employees, as well as recognize key processes and equipment that are most vital and time-sensitive to operations. New elements include advice about establishing emergency communications, business resumption planning and information technology disaster-recovery planning.
The guide was created in response to a widespread lack of long-term emergency plans among automotive suppliers. In the event of a disaster or crisis, companies that lack tested and well-conceived plans face the possibility of employee endangerment and stalled operations that could create a domino effect throughout the supply chain.
For more information, visit www.aiag.org.
AB to CB: Don't Tread On Me
Noting an increasing number of complaints about accredited certification bodies (CB) issuing certificates for accreditation-based standards such as ISO/IEC 17025, the International Accreditation Forum's technical committee is currently voting on a proposal that would allow the accreditation of offenders to be revoked. Put simply, certification bodies are supposed to certify and accreditation bodies (AB) accredit.
The IAF technical committee first discussed the issue at its November 2006 meeting in Cancun, Mexico, where it noted that certification bodies that issue certificates for standards used by accreditation bodies to accredit certification bodies (such as ISO/IEC 17025) are essentially competing with accreditation bodies themselves. This is prohibited by ISO/IEC 17011.
According to Randy Dougherty, director of accreditation at ANSI-ASQ National Accreditation Board (ANAB), the proposal—as it is now written—would allow offenders to earn their accreditation back by taking corrective action.
After the technical committee's March meeting in San Francisco, the subcommittee that is spearheading this effort drafted the following proposal, which was sent to technical committee members for a vote that ends on June 29:
"The IAF and ILAC GAs [general authorities] resolve jointly that, when a CAB [conformity assessment body] accredited by an AB [accreditation body] is issuing attestations of conformity (whatever named) to any standard used by such AB as a basis for accrediting CABs (e.g., ISO/IEC 17025 or ISO 15189), the accreditation of such CAB shall be withdrawn in full, as this behaviour of the CAB will put the AB, against its will, in the condition of providing the same service that the CAB performs, in violation of subclause 4.3.6 of ISO/IEC 17011."
If the proposal is approved by the technical committee, it will be forwarded to the IAF's General Assembly for its consideration.
For more information, visit www.iaf.nu.
Statistically Speaking
A total of 12,765 robots valued at $904.2 million were sold to North American companies in 2006, a decline of 30 percent in units and 22 percent in revenue from 2005. When sales to companies outside North America are added in, North American robotics companies' sales were 13,791 robots valued at $958.4 million, down 29 percent in units and 22 percent in revenue.
Source: Robotic Industries Association
Protecting the Protectors
The Canadian Standards Association, in cooperation with the Canadian General Standards Board and other stakeholders, has announced its intent to develop a national standard for protective equipment for fire, police and paramedic services in the event of a chemical, biological, radiological or nuclear (CBRN) incident.
"Canada's fire, police and EMS services are the first on the scene in 90 percent of emergencies and not all have the minimal level of protective equipment necessary in the event of a deliberate or accidental CBRN incident," says John Walter, CSA vice president for standards development. "This is why CSA, Canadian General Standards Board and other stakeholders are working to develop a national CBRN standard that will help improve the protection of first-responders across jurisdictions from coast to coast."
Currently, there are limited protective equipment standards specific to CBRN incidents. Most first responders in Canada have hazardous material or dangerous-goods standards to guide them in responding to a CBRN incident. With this project, first responders will have, for the first time, a national standard recognized across jurisdictions to protect them in their vital work.
"Assuring Canadians that those they rely upon in the event of an emergency are adequately prepared to deal with a CBRN event, and strengthening Canada's capabilities to respond to CBRN incidents, are continuing priorities for all levels of government," says Dr. James G. Young, special advisor to the deputy minister, Public Safety Canada. "First responders are on the front line in times of crisis, so we must continue to develop and implement appropriate preparedness, and response programs and standards to help improve their capabilities and their safety."
The new national standard will have a significant effect in assisting first responder organizations in the selection, use, capabilities and limitations of CBRN personal protective equipment, enabling them to do their jobs more safely, with greater protection and functionality. The standard will identify requirements for protective CBRN equipment, such as respiratory protection and whole-body protection. The standard will also address and provide valuable guidance on key issues such as interchanging and interoperating equipment to enhance the capacity of first responders to work effectively across jurisdictions.
The new standard will also address the differences between a conventional hazardous-material incident and a deliberate CBRN incident to understand how equipment guidelines may differ.
For more information, visit www.csa.ca.
|