American Red Cross Undergoes Quality Transfusion
The American Red Cross has
launched a multiyear, multimillion- dollar quality effort
to enhance organizational effectiveness and improve its
process of collecting, manufacturing, testing and distributing
blood.
The Red Cross' Biomedical Services sector derives three
end products from whole-blood donations: red blood cells,
platelets and plasma. The intention of this quality initiative
is to improve the ways in which the Red Cross manufactures
these three products.
"Our quality effort is focused on ensuring safe,
pure and effective blood," explains Jack Prause, senior
director of quality business operations at Red Cross Biomedical
Services. "Like many organizations, over time we've
reacted to problems by applying a Band-Aid, a manual work-around,
an additional inspection or something else to ensure that
we get a quality end product. This has resulted in increased
complexity in our operating processes and systems. Our focus
is to build key control points within those processes to
make them less complex and as flexible as possible."
The Red Cross began planning this effort in May 2001,
but the events of Sept. 11 significantly transformed the
initiative. "Sept. 11 caused a massive change because
of the huge amount of donations we were receiving,"
explains Prause. "It put a severe strain on the organization.
Everything was working at absolute capacity, and this helped
us identify some of the systems that weren't quite as robust
as we would absolutely like."
Red Cross Biomedical Services is a separate entity from
the rest of the organization, so it wasn't involved in the
issues surrounding the diversion of post-Sept. 11 charitable
donations.
This isn't the first quality overhaul the Red Cross has
undertaken. In 1993, the organization launched Transformation,
a comprehensive program designed to centralize and systemize
its operations. Prior to Transformation, each of the Red
Cross' 50 regions had considerable autonomy. There were
11 different computer systems being used, and each region
used its own testing labs. Transformation centralized the
Red Cross' system to one computer system and one set of
procedures, thus ensuring national control and improving
the safety of distributed blood.
As a result, the organization decreased the number of
Form 483 Observations, or areas that the Food and Drug Administration
views as needing improvement, by more than 80 percent in
the last decade. In fiscal year 2002, 27 of the 38 regional
sites and laboratories inspected by the FDA had zero observations.
In the facilities where observations were written, seven
of the 11 facilities had no more than three observations.
"This quality initiative involves reengineering and
redesigning the procedures that are now common," Prause
explains. "Now we can make a change and roll it out
everywhere in the nation and know that it happened nationwide.
Now we're looking to drive down any variability, deviation
or error down to the zero level."
This quality effort is a comprehensive and integrated
holistic approach to organizational improvement. The effort
consists of more than 30 initiatives, including:
Using new technologies to reduce the potential for human
error
Restructuring and increasing the level of quality assurance
staff by 50 percent, with 175 new positions being added
throughout the field units and headquarters
Creating a more streamlined training system and implementing
a comprehensive training program
Reengineering the core manufacturing processes to provide
more efficient and simplified processes that will reduce
and prevent errors.
Investing in facilities to address short-term infrastructure
needs and enable more efficient and effective adoption of
new technology
Prause is confident that the quality effort will be a
success, and he attributes it to four factors:
Absolute executive support and involvement. Top Red Cross
executives have given the quality team the resources it
needs to implement a successful initiative.
A focus on operating excellence rather than FDA compliance.
The Red Cross believes that by reengineering its processes
to be effective, streamlined and efficient, compliance with
any regulations will follow.
Comprehensiveness. Rather than focusing on FDA hot-button
issues, the Red Cross is redesigning its entire system.
This involves training staff, bringing in new technology
and ensuring that each facility has resources to manufacture
a safe product.
End-user involvement. The Red Cross has enlisted end-users
and field unit operators to help design the quality initiative.
"They play a large part in designing a process that
allows for compliance but is also user-friendly and flexible,"
says Prause.
The Red Cross provides nearly half of the nation's blood
supply to patients in 3,000 hospitals nationwide. Learn
more at www.redcross.org.
Calibration Trends Indicate Growth
The calibration services industry
will keep growing until at least 2007, according to a new
research report available from The Signal Group.
"The Market for Calibration of Test and Measurement
Equipment: Strategies, Trends and Forecasts 2003–2007"
forecasts calibration services growth driven by increasing
adoption of quality management systems and the increased
use of measurement and sensing technology.
"The calibration services industry has seen growth
rates in excess of 15 percent per year in many countries,"
says Greg Powell, Signal Group partner and principal author
of the report. "The commercial sector will benefit
heavily from a continuing trend to outsource calibration
services."
The study also analyzes the situations faced by different
providers of calibration services, including test equipment
manufacturers, commercial vendors and in-house laboratories.
The report can be used as a sourcebook of current conditions,
practices, trends and developments, including an analysis
of eight key industry segments. The report also analyzes
fundamental background issues and provides five-year forecasts
accompanied by practical strategic advice.
The 103-page report is available for $850. To review the
report's table of contents, or to place an order, visit
www.thesignalgroup.net/research.
Microsoft to Launch Six Sigma Software
Microsoft Corp. has developed
Accelerator for Six Sigma, which the company plans to launch
within the next few months.
Microsoft Accelerator for Six Sigma is an integrated set
of products and services that leverages existing software,
such as Microsoft Project and Visio, and is customized for
Six Sigma practitioners. It includes interactive project
guides to lead organizations through the define, measure,
analyze, improve and control model, assisting in tracking
financial information, utilizing human resources, managing
Six Sigma tools and electronically sharing knowledge gathered
across the enterprise.
"We're looking hard at how we can develop offerings
that improve productivity in all aspects of a company that
enable customers to take greater advantage of the functionality
in their software to address specific business problems,"
says Ted Johnson, corporate vice president of the Business
Tools Division at Microsoft. "The Microsoft Accelerator
for Six Sigma is a great example of an offering that can
affect the operations function in a company. Not only can
it help improve efficiencies, but it's also based on Microsoft
software that many customers already have in place."
Microsoft
has been practicing Six Sigma internally. The company developed
Accelerator using the design for Six Sigma methodology.
"By calling it an 'accelerator,' we mean that Microsoft
isn't creating a whole end-to-end solution, but rather facilitating
a whole solution by adding additional functionality to our
existing Information Worker software," says Ingo Heel,
senior product manager of Microsoft's Information Worker
Enterprise Solutions Group. "Think of it as an application
layer."
The software leverages the company's existing products,
including Office XP Professional, Project Server 2002, Project
Professional 2002, Visio 2002, Windows 2000 Server, SQL
Server 2000 and SharePoint Team Services, as well as third-party
products, services and deployment partners.
Microsoft worked with Apriso Corp., a provider of collaborative
execution solutions, to create enterprise performance solutions
for manufacturing and health care companies. Additionally,
Microsoft is teaming with SigmaPro Inc., a supplier of integrated
Six Sigma, design for Six Sigma, and lean consulting and
training services.
Visit Microsoft's Web site at www.microsoft.com.
Check Your Calendar
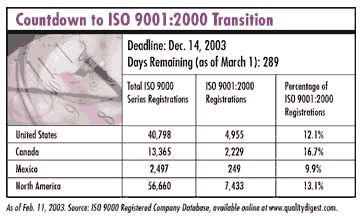
Introduce Lean to Your Organization
Lean
is one of the most popular buzzwords in quality-minded organizations
today, but--much like a fat-trimming diet--getting lean
is easier said than done. More and more, a lean transformation
isn't just a quality choice but a quality must.
The Lean Learning Center in Novi, Michigan, teaches a
set of lean workshops that provide a foundation for lean
transformation. Participants learn how to translate lean
into a set of rules and principles, practice implementation
through factory simulation, and develop a plan for introducing
lean to their organizations.
"Few companies today can escape the challenge of
delivering reduced prices and better quality to their customers,"
says Jamie Flinchbaugh, one of the founders of the Lean
Learning Center. "We help companies understand lean
as a sustainable enterprisewide system, not just as a collection
of tools."
The Lean Learning Center's 2003 workshop schedule includes
four sets of lean-focused curriculum:
The Lean Experience--geared toward operations managers and
their teams that want to begin a lean initiative at their
organization. The five-day course includes lean concepts
and principles, factory simulation, case studies, and various
lean implementation methods.
Lean Leadership--focuses on creating leadership within an
organization. This two-day course includes a look at notable
business leaders, lean leadership models, and leadership
characteristics and styles, among other topics.
Lean Kaizen Workshop Boot Camp--a five-day course for individuals
interested in leading large-scale lean projects. The boot
camp teaches facilitators how to identify a project, plan
a team workshop, use process tools to understand the organization's
current state, establish an ideal state, and plan and execute
an action plan.
Lean Value Stream--provides insight into how to identify
opportunities for gains in cost, quality, delivery and flexibility.
Value stream mapping methods are also taught.
"Everyone learns better when they're enjoying themselves,
so we try and make the experience fun," comments Flinchbaugh.
"Our goal is to create champions of lean ready to convey
and execute the lean philosophy to their companies."
A schedule of the workshops can be found at The Learning
Center's Web site, www.leanlearningcenter.com
.
Baldrige Challenges CEOs to Become Chief
Ethical Officers
In
the wake of some major corporations' immoral actions and
their legal consequences, it comes as no surprise that the
National Institute of Standards and Technology is challenging
CEOs to prove that their organizations' practices are just.
Organizations vying for the 2003 Baldrige Award will find
extra emphasis on ethical activities throughout all seven
of the 2003 Baldrige Criteria for Performance Excellence's
categories: leadership, strategic planning, customer and
market focus, information and analysis, human resource focus,
process management, and business results.
According to NIST, these criteria will help organizations
form the foundation for sound management and ethical business
practices.
"For America to have a strong economy, we need sound
businesses with ethical, responsible leaders," says
U.S. Commerce Secretary Don Evans. "Great authority
is vested in the men and women who run our public corporations,
and with such power comes responsibility. Corporate leaders
aren't simply stewards of their individual companies. They're
stewards of American capitalism itself."
The criteria state: "Senior leaders should serve
as role models through their ethical behavior… Senior
leaders should be responsible to your organization's governance
body for its actions and performance. The governance body
should be responsible ultimately to all stakeholders for
the ethics, vision, actions and performance of your organization
and its senior leaders."
This emphasis on ethical practices is most prevalent in
the criteria's leadership category, which asks how the organization's
governance system ensures management and fiscal accountability
and independence in audits while protecting stockholder
and stakeholder interests.
Additionally, the results category asks organizations
to provide evidence of fiscal accountability, ethical behavior,
legal compliance and organizational citizenship.
Other areas receiving greater attention in this year's
criteria include the need to capitalize on knowledge assets,
the need to create value for customers and the organization,
and the alignment of all aspects of an organization's performance
management system with the results measurements.
To download a copy of the 2003 Baldrige Criteria for Performance
Excellence, visit www.baldrige.nist.gov.
INDUSTRY NEWS
Oliver R. Smoot of the United
States has taken office as president of the International
Organization for Standardization for a two-year term. Smoot
succeeds Mario Cortopassi of Brazil.
Smoot will work on involving developing countries in standardization
processes, identifying new areas for standardization and
developing ways of communicating the benefits of conforming
to ISO standards.
Smoot has experience in standardization, law, intellectual
property and information technology. Visit www.iso.org
to learn more.
Xspect Solutions Inc. has begun
business as a nationwide total metrology outsourcing partner.
The company is a business partner with Wenzel GmbH as an
exclusive distributor of Wenzel CMMs in North America.
The company is headed by Keith Mills, former president
of DEA and International Metrology Systems. "The continued
fragmentation of the CMM industry creates an opportunity
for change management in both CMM distribution and support
activities," says Mills. To learn more, visit www.xspectsolutions.com.
The National Committee for
Quality Assurance has launched qualityprofiles.org, which
catalogs 65 quality improvement efforts from NCQA-accredited
health plans.
The site allows users to download quality improvement
tools, such as action plans, guidelines, member and provider
letters, log sheets, and surveys. It also features advice
on implementing an improvement effort, summary descriptions
of specific challenges and a list of required resources.
Each study includes staffing requirements, timelines, required
resources and specific activities that improve performance.
The Web site is based on NCQA's print version of Quality
Profiles.
NVision Inc., a provider of
laser-scanning solutions and consulting services, has expanded
its North American technical center to increase its consulting
services in the laser-scanning field.
"This expansion positions us to provide a fuller
range of consulting services to companies that want to take
advantage of laser scanning without having to invest in
equipment and train people in its use," comments Bill
Bonner, NVision's director of sales and consulting. Learn
more at www.nvision3d.com.
Xerox Corp.'s Acoustical Engineering
Laboratory now provides consulting services in the areas
of design for low noise and sound quality, industrial noise
and vibration control, in-process quality control, predictive
maintenance and condition monitoring, noise measurement
to ISO and ANSI standards, and hearing conservation.
The
Webster, New York-based laboratory houses an ISO 3745-conforming
precision hemi-anechoic chamber, noise control engineering
facilities and model shop, and noise-control equipment from
several leading metrology companies. To learn more, visit
www.xrx-acousticenglab.com.
Newport Corp. has opened a
new 42,000-square-foot optics manufacturing facility near
its headquarters in Irvine, California.
During the last three years, Newport has expanded its
optical manufacturing capability to provide collimators,
beam expanders, spatial filters and optical components to
the semiconductor, medical, aerospace and scientific markets.
"The facility includes controlled environments to
ensure particulate, temperature and humidity levels consistent
with manufacturing high-precision optical components and
thin-film coatings," says Robert J. Phillippy, vice
president and general manager of Newport's Industrial and
Scientific Technologies Division. For more information,
visit www.newport.com.
Hertzler Systems Inc. now offers
the GainSeeker OPC Connectivity Pack, a solution that captures
data from any OPC server and provides automated enterprisewide
process control.
OPC, or OLE for Process Control, is an industry standard
created through the collaboration of automation hardware
and software suppliers in cooperation with Microsoft.
Hertzler Systems, which developed the GainSeeker suite,
provides software and services that help collect, manage,
analyze and report quality information. For more information,
visit www.hertzler.com.
|