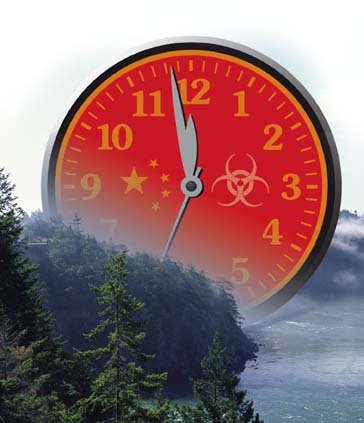
Thorny RoHS
Think Europe’s Restriction of Hazardous Substances (RoHS) was tough? Meet China RoHS.
Phase One of China RoHS took effect on March 1, and while its intent is similar to the European Union’s RoHS, the approach is different. Like RoHS in Europe, China RoHS (officially known as Management Methods for Controlling Pollution by Electronic Information Products) restricts six hazardous substances (lead, mercury, cadmium, chromium VI compounds, polybrominated biphenyls and polybrominated diphenyl ethers) from all electronics and electrical products entering the country. This includes products that were exempt from the EU’s RoHS, such as automotive electronics, radar equipment, semiconductors and other manufacturing equipment, components, packaging materials and some raw materials.
Geoffery Bock, manager of WEEE/RoHS
services for TÜV Rheinland of North America, estimates that China RoHS will affect nearly 6,000 types of equipment and thousands of manufacturers around the world. Before, many of them were exempted from the EU’s RoHS directive, so there is considerable concern about the looming compliance deadline.
“I’d say there’s some pretty serious panicking happening because there’s still a lot we don’t know about China RoHS,” Bock says. “The worst problems are for companies that were exempted from Europe’s RoHS but will be seriously affected by China RoHS.”
The two laws are similar, but there are some key differences. Europe’s RoHS prohibits the presence of the stated hazardous substances in all electronics products (with some exceptions) imported into the European Union; China’s RoHS doesn’t prohibit them—yet. Phase One of China’s RoHS only requires the identification and marking of all offending materials, including packaging materials, coming into the country.
There are three marking requirements: A label must state if the product contains one of the six hazardous substances and, if it does, the environment-friendly use period. Whether or not the packaging material contains hazardous materials must also be labeled. The marks must be displayed on the outside of shipping materials, and the accompanying documentation is required to be translated into simplified Chinese. Additionally, China’s initiative requires noting concentration limits of hazardous substances and the disclosure of the date of manufacture for all affected items.
China RoHS also includes a standard on testing procedures and a catalog of products subject to substance restrictions and mandatory certification, though these requirements won’t take effect until Phase Two, which is expected to become effective later this year or early in 2008. Noncompliance—even early in the law’s enforcement period—can block a manufacturer or supplier from distributing in China.
“Companies are faced with a choice—either meet the RoHS requirement or eliminate China from the sales plan,” says Bock. “Some may choose to distribute to other countries instead, but eventually they will turn to China. China is the world’s fastest-growing economy, and they want to sell their products there.”
Phase Two of China’s RoHS will likely be more severe than Phase One. It’s still being developed and the specifics are a little vague, but China’s Ministry of Information Industry has already announced that it won’t allow manufacturers of some prohibited materials to self-declare their products’ materials; instead, it will require them to be tested for compliance at one of 18 Chinese labs. The catalog of prohibited materials is also likely to grow.
“Phase Two is going to be tough,” Bock observes. “They’re not just going to take manufacturers’ words that there are no prohibited materials in their products; they’re going to require independent testing in China. That’s going to take some getting used to for a lot of people.”
For more information, visit online at www.chinarohs.comor www.us.tuv.com.
MSC Measures Up
Unless you’re deeply interested in metrology or measurement science, you may be unaware of the Measurement Science Conference held each year in Southern California. This conference, while containing a lot of information largely of interest to metrology scientists, has plenty to offer for anyone involved in measurement technology, including manufacturers who use NIST-traceable test and measurement equipment and standards as part of their daily quality control.
The 37th annual conference, held this past January in Long Beach, California, drew more than a thousand attendees and 115 vendors . Although several of the tracks dealt with standards development or technical issues largely of interest to scientists or calibration labs , it also offered a broad range of workshop topics of universal interest to manufacturers, such as measurement uncertainty, upcoming measurement standards, calibration issues in FDA-regulated environments, lean manufacturing and statistics. There was also a wide array of informational classes on test and measurement techniques for all types of measurement, including vibration, dimensional, frequency, flow, radio frequency and microwave, temperature and so forth.
The MSC is the only venue where representatives from the National Institute of Standards and Technology provide two full days of technical seminars .
“This conference is unique because it is held annually on the West Coast,” says Doug Sugg, former president of MSC and deputy technical operations manager for the Naval Surface Warfare Center, Corona Division. “It’s a way for all people interested in measurement science to get together and share ideas.” Education is a key aspect of the show. Sugg points out that companies are finding it harder to locate knowledgeable and seasoned metrologists, so shows such as the MSC, which developed from academia, have made education a key part of their charters.
The conference is held the first quarter of every year in Southern California. For more information on the MSC, visit its Web site at www.msc-conf.com .
Harrington Receives Award
Management guru (and Quality Digest columnist) H. James Harrington received the Howard Jones Award from the American Society for Quality’s Quality Management Division earlier this month.
The award, presented to Harrington on March 1 at the division’s annual Quality Management Conference in Dallas, recognizes his long contributions to the science of quality management. The award is the latest in Harrington’s extensive collection; he’s received most of the industry’s top awards in his more than 55-year career in quality. The Quality Management Division is ASQ’s largest division, with more than 22,000 members. Grace Duffy, ASQ vice president and recipient of the award in 2005, says Harrington’s accolades are well deserved.
“If anyone exemplifies the attributes of someone who has contributed to the quality profession, it’s Dr. Jim,” Duffy says. “He most certainly deserves this.”
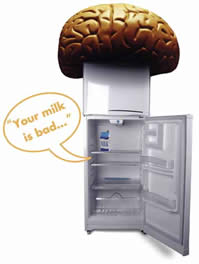
Brainy Freezer
Think radio frequency identification’s (RFID) usefulness ends at warehouse inventory tracking? Think again.
A South Korean company is developing a new refrigerator that will use RFID to alert owners when items inside are running low or approaching their expiration dates. The Korea Times newspaper reports that in addition to automatic inventory monitoring, Samsung Electronics’ fridge could even send a shopping list to its owners’ cell phones, or an order to the supermarket. Other cool capabilities include recipe generation using the items in the refrigerator. This smarty-pants fridge should be available for consumers in 2008 or 2009.
Order one with your new iPhone.
Quality Enlists
If there’s a new look to the 21st-century U.S. military, Nicholas Kunesh defines it. Kunesh works in the Pentagon and reports directly to Don Winters, the Secretary of the Navy. Kunesh enjoyed a long and successful career working for corporate giants Motorola and Panasonic before enlisting as a civilian executive in the Navy. In his senior executive role at Motorola, he was charged with operating the company’s Japanese supply chain and was the only foreigner—among 5,000 employees—working in its Yokohama factory.
Almost four years ago, the Pentagon asked Kunesh to join its ranks. An appointee of President Bush, he is now the deputy assistant secretary of the Navy, logistics department. He’s one of the few political appointees in the Navy to come from a commercial background. As the department’s lean Six Sigma champion, Kunesh has to find ways to save the Navy money and time. He’s been very successful at doing both.
While he couldn’t say exactly how much the Navy’s process improvement efforts have cost (that information is considered sensitive), he did say that it has obtained a four-to-one return on its investment.
“It’s been incredibly successful at finding waste and helping us to identify places that need improvement,” Kunesh says. “Six Sigma and lean have been exactly what this organization needed to transform.”
The military’s use of process improvement techniques has been well documented, but the evolution of the phenomenon hasn’t been as fully explored. After almost six years and nearly 4,000 lean and Six Sigma projects, it’s clear that the methodologies and, more important, the mindset have infiltrated the military. What’s most notable is the shifting awareness of process improvement techniques among the rank-and-file.
“We’re seeing people working in maintenance operations, for example, who are considering how each step they take could be done better,” says Kunesh. “They make suggestions for improvements, they’re implemented and we’ve just taken another step toward maximum efficiency. Everyone is getting that message.”
As the military has developed a process improvement mindset, the need for outside consultants to lead projects and train leaders has started to dip. Kunesh estimates that the Navy and Marines have used approximately 15 consultants to kick off various lean, Six Sigma and theory of constraints projects, and to train officers and other leaders. The goal is to train military employees to take over from the consultants, and that goal is well under way. The Navy and Marines have approximately 1,000 in-house Black Belts, and Six Sigma training classes are regularly full. The American Society for Quality recently developed a Black Belt certification exam for the military, and 81 of the 100 people taking the exam passed it.
“We work for the taxpayers, and we know who our stakeholders are,” says Kunesh. “We know that what’s good now can be better tomorrow.”
Happy Birthday
Joseph M. Juran, the legendary “father” of quality, celebrated his 102nd birthday on December 24.
Born in Romania, Juran’s life is a study of the American Dream in microcosm. After immigrating to the United States, Juran’s family settled in Minneapolis. He overcame poverty and a fractured family to conceptualize the Pareto Principle, which millions of modern-day managers use to separate the “vital few” from the “useful many.” His books are must-reads for any quality professional.
Juran is now retired and lives in Connecticut, where his Juran Institute is located.
Do the Math
In last month’s “Do the Math,” we directed readers to a December 15, 2006, Associated Press story about race car driver Marco Andretti’s F1 debut. The story contained the following sentence:
“Andretti posted a time of 1 minute, 21.873 seconds through 62 laps of the 2.748-mile circuit in a Honda 2006 RA106 car.”
Regarding the results of his run, Andretti said, “It took me a little while to get used to the traction control and the brakes.”
Well, yeah. As many of our readers noticed, traction and braking are an issue when you’re traveling at Mach 10.
As this month’s “Do the Math” winner, Patrick T. O’Connell, pointed out: “To complete 62 laps of a track that is 2.748 miles long in the time listed, he had to have been driving a little over 7,491.5 miles per hour. If this is his first appearance I know who to put my money on this year.”
Do the math:
62 laps × 2.748 miles = 170.376 miles
170.376 miles/81.873 seconds =
170.376 miles/0.0227425 hours =
7,491.5 miles/hours
Patrick wins a terrific prize for his speedy entry.
Since our readers have been so astute in identifying outright math errors, we’re going to change gears a bit. The following New York Times article has no math errors; however, it does have a misleading definition. Visit online at http://travel.nytimes.com/2006/12/13/dining/13calo.html to see what we’re talking about. Tell us what definition we’re referring to and why, without further explanation in the article, it gives the reader misleading information. Send your answer to Quality Digest by clicking the feedback link below and be entered for one of our great prizes.
Challenging Compliance
Food and Drug Administration compliance and traceability requirements involve a great deal of documentation, and finding ways to integrate document management with process management is among the top challenges for FDA-regulated companies.
Research performed by the Aberdeen Group suggests that aligning these two functions with one another as well as a quality management system makes organizations more competitive. How do they do it? Most manufacturers (64%) reported that implementing automated document management systems that also integrate quality, compliance and traceability data has helped solve the problem. More than half (54%) build compliance and traceability into their production processes.
The findings are part of the Aberdeen Group’s “Compliance and Traceability in Regulated Industries Benchmark Report,” which analyzed survey results from more than 340 companies in various regulated industries. The research also found that best-in-class manufacturers are more than twice as likely as other manufacturers to integrate their software solutions; they are also 75 percent more likely to have process visibility and automated traceability than other manufacturers. Moreover, best-in-class manufacturers spend far less time preparing for audits—an average of 36 hours. Average and below-average competitors spent an average of 89 hours and 210 hours, respectively.
For more information, visit www.aberdeen.com.
Kahane Keynotes ASQ’s 2007 WCQI
Adam Kahane, one of the world’s leading problem solvers, will deliver the opening keynote address at the American Society for Quality’s 2007 World Conference on Quality and Improvement.
Kahane has helped numerous business, government and spiritual leaders solve contentious conflicts and is the author of Solving Tough Problems: An Open Way of Talking, Listening and Creating New Realities (Berrett-Koehler Publishers, 2004). Nelson Mandela endorsed the book, observing that it “addresses the central challenge of our time: finding a way to work together to solve the problems we have created.”
Kahane, founding partner of Generon Consulting, served as the head of social, political, economic and technological scenarios for Royal Dutch/Shell in London. He was named as one of 16 outstanding individuals on Fast Company magazine’s “Who’s Fast” list. Kahane will share his perspective on global business and social responsibility on the first day of the conference. Other keynote speakers include Donna Shalala, former U.S. Secretary of Health and Human Services; and Jim Carroll, futurist and innovation expert.
The World Conference on Quality and Improvement will be held April 30–May 2 at the Orange County Convention Center in Orlando. For more information, visit http://wcqi.asq.org.
Errata
In the January 2007 issue (our Quality Sourcebook), we inadvertently left out the following two companies. Their information and the directories in which they should have been listed are provided below. Quality Digest regrets these omissions.
For the Calibration Service Directory:
- 6015 N.E. 80th Ave., Ste. 400
- Portland, OR 97218
- Phone: 800-247-1927
- Fax: 503-231-4012
- www.theppigroup.com
For the ISO Consulting Directory, the Quality Consultants Directory and the Training Directory:
|