Managers Disagree on Quality’s
Definition
A survey sponsored by the American
Society for Quality reveals that the majority of U.S. executives
believe quality contributes to the bottom line, but the
way they define quality varies.
More than 600 executives from four industry segments--manufacturing,
services (including government), health care and education--provided
their perspectives on the value that quality brings to their
organizations. Of those asked, 99 percent said they believe
quality contributes to the bottom line, and 92 percent believe
that an organizationwide effort to use quality techniques
provides a positive return.
However, defining quality didn’t elicit such a uniform
agreement. Sixty-four percent of respondents believe that
quality is a management tool, and 36 percent believe quality
is built into a product or service but isn’t necessarily
a management tool. When asked to define quality, the majority
of respondents equated quality to customer satisfaction.
“It’s encouraging to know that most executives,
no matter in what industry, believe in the practice of quality
and the value that it can bring to their business--not just
in terms of economic return but also in the form of customer
satisfaction,” notes ASQ President Ken Case. “However,
it’s a bit disconcerting that many executives don’t
view quality as a business management tool when many of
the continuous improvement efforts practiced in business
today grew out of the quality discipline and the work of
quality professionals.”
The survey also indicates that there’s a gap between
executives’ awareness of quality improvement processes
and implementation. When asked about their awareness and
usage of benchmarking, total quality management, quality
circles, ISO 9001, Six Sigma and the Baldrige Award criteria,
respondents from all four industry segments reported high
awareness and usage of TQM and benchmarking.
Manufacturing executives report greater awareness of ISO
9001, quality circles, Six Sigma and the Baldrige criteria
than leaders in the services, health care and education
sectors.
Actual use of all six techniques across all industries
was considerably lower than was reported awareness, as illustrated
below.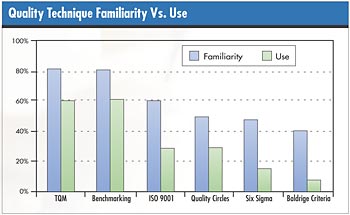
“The sizeable gap between usage and awareness leads
me to believe that businesses and organizations either don’t
use quality methodologies to improve their operations or
they just don’t realize that the processes they have
in place are attributable directly to the quality discipline,”
adds Case.
The survey was conducted by Market Probe, a global marketing
research company. A full report of the findings, including
industry-specific breakdowns of responses and demographics,
can be found at www.asq.org/survey.
The site redirects to a PowerPoint presentation.
ISO 9001 Users Go Online for Assistance
The ISO survey includes questions covering four topics:
Details about the nature and size of your organization
Users’ experience with the ISO 9000 series,
both the 2000 version and previous versions
Difficulties users may have encountered with ISO 9001:2000,
with the opportunity to explain the nature of the
difficulty and suggest alternative text to address
the problems, along with a call for general comments
about any clause without suggesting alternative text
Any suggestions on how to improve ISO 9004:2000
|
The International Organization
for Standardization is providing users of its ISO 9000:2000
series of quality management system standards with two online
initiatives: a user feedback survey to identify points for
improvement and an interpretation service to clarify the
intent of requirements.
“This support of users mirrors the evolution taking
place in the industrial and business sectors that our organization
serves,” says ISO Secretary-General Alan Bryden. “In
today’s competitive markets, a company cannot afford
to develop a product and just throw it over the wall to
customers. Many successful products are part of a total
package that includes support, maintenance and enhancement
services.”
The online feedback survey for users of ISO 9001:2000
and ISO 9004:2000 aims to improve the standards or develop
support documents to help users understand and implement
the standards. Any person with knowledge of or experience
with the standards may participate, and there’s no
limit to the number of participants from any organization.
The survey takes about 15 minutes to complete.
“Customer focus is one of the quality management
principles on which the ISO 9000:2000 series is based,”
continues Bryden. “Therefore, before launching the
development of the standards, ISO surveyed users for their
requirements and gave them the opportunity to ‘trial’
the standards during the development process. The recently
launched user feedback survey and interpretations service
demonstrates that ISO is continuing to put the customer
focus principle into practice.”
The survey is available at http://isotc.iso.ch/webquest/tc176/.
The interpretations service is intended to prevent ambiguous
and vague interpretations of the requirements of ISO 9001
and to develop a database of interpretations. It provides
interpretations related to what to do and not how to do
it, without changing any requirements of the standard or
its original intent. Requests for interpretations must be
submitted via ISO national member institutes.
The database, guidance on submitting a new request and
the official request form can be accessed at www.tc176.org/Interpre.asp.
ASQ Co-Hosts China Quality Conference
The American Society for Quality’s
Customer-Supplier Division and the China Association for
Quality will present the Third China-America Conference
on Quality Tools and Technologies Sept. 6-9 in Shanghai.
“We need to know the strengths as well as the weaknesses
of our trading partners,” states Dennis Arter, an
ASQ organizer. “Having been to China three times,
I’m beginning to understand the culture and the work
structures. Managing for quality is different in our two
countries. Trade with China offers a significant opportunity
as well as a challenge.”
The Shanghai event will be geared toward:
Learning about existing and future business relationships
in the People’s Republic of China
Exchanging ideas with professional colleagues in the world’s
fastest growing economy
Learning about the government-industry structure in China’s
new market economy
Introducing company products and services to China’s
market
Gaining better understanding of ASQ and CAQ
The fee of $3,600 for the full week includes airfare,
hotel accommodations, ground transportation and most meals.
Also included are cultural events in Shanghai and nearby
cities.
The CAQ serves quality professionals in the People’s
Republic of China. With headquarters in Beijing, CAQ offers
training, publications and support in the field of quality.
ASQ’s Customer-Supplier Division is a special interest
group aimed at exploring, expanding and communicating practices
that lead to effective supplier performance and increased
customer satisfaction. To learn more, visit www.asqcsd.org.
MetricStream Merges With Zaplet
MetricStream Inc., a developer
of enterprisewide quality software, has merged with Zaplet,
a provider of business process management solutions for
corporate compliance.
Shellye Archambeau, past CEO of Zaplet, has been named
CEO of MetricStream. Gunjan Sinha, former Chairman of MetricStream
will act as MetricStream’s executive chairman.
“Serving individual organizations separate solutions
for each of its compliance initiatives is a time-consuming
process,” explains Anil Gupta, vice president of marketing
for MetricStream. “It made sense to combine MetricStream’s
solutions with Zaplet in order to bring separately organized
compliance initiatives into one cohesive platform.”
For more information, visit www.metricstream.com.
Customer Satisfaction Can Equal
Failure
Philip Crosby Associates, a
consultancy touting the late quality guru Philip B. Crosby’s
Absolutes of Quality Management, has added another absolute
to the four originally coined by Crosby in his book Quality
Is Free (Mentor Books, 1992).
The new mantra comes two years after Crosby’s death.
It states, “The purpose of quality is to ensure customer
success, not customer satisfaction.”
“We are having a quality crisis in this country
because companies are narrowly focused on customer satisfaction,”
says Wayne Kost, president of PCA. “It has become
imminently clear that pursuing customer satisfaction can
be a surefire, direct route to corporate failure.”
The fifth absolute is designed to drive a stake through
the “customer satisfaction myth,” according
to PCA. “People can be satisfied with almost anything--happy
customers are not necessarily successful customers,”
explains Kost. “If you focus on satisfaction, you
will have short-term gains, but there’s a loss to
the customer. Fanatically focusing on customer success is
the only way to ensure corporate success. Building an organization
that knows how to focus on customer success and make it
a repeatable, continuous process is the next decade’s
primary challenge.”
A new book based on Crosby’s Quality Is Free
will cover this new absolute.
“No one is against quality, yet very few achieve
it,” adds Kost. “We took a hard look at the
original absolutes because we realized that a company could
live by them and still fail.”
Crosby defined the four absolutes as:
Quality has to be defined as conformance to requirements,
not as “goodness.”
The system for causing quality is prevention, not appraisal.
The performance standard must be zero defects, not “that’s
close enough.”
The measurement of quality is the price of nonconformance,
not indices.
Learn more about Philip Crosby Associates at www.philipcrosby.com.
Best-Practice Lean Manufacturers
Recognized
The largest missile manufacturing
facility in the world, an appliance manufacturer and 10
automotive suppliers are recipients of the 2004 Shingo Prize
for Excellence in Manufacturing. Dubbed the “Nobel
Prize of manufacturing” by Business Week, the Shingo
Prize is the premier manufacturing award and recognition
program in North America.
Notable achievements of the 2004 recipients include:
Seven of the 12 winners achieved product quality of fewer
than 10 returned parts per million opportunities.
Seven of the 12 recipients have inventory turnover rates
greater than 25 per year, compared to a U.S. average of
eight.
Premium freight as a percent of production costs averaged
0.12 percent.
“Once again, the recipients of the Shingo Prize
demonstrate that they are prepared to weather economic uncertainty
by not wasting precious manufacturing and business resources,”
notes Ross Robson, Shingo Prize executive director. “Shingo
Prize recipients and lean manufacturers clearly stand out
among North American manufacturers in terms of quality,
cost, delivery and business results.”
This year’s recipients are:
ArvinMeritor Light Vehicle Systems-- Gladstone plant, of
Columbus, Indiana
Delphi Corp.--Delphi Electronics and Safety, Delnosa 5 and
6 Operations, of Reynosa, Mexico
Delphi Electronics and Safety--Kokomo Operations, Plants
7 and 9, of Kokomo, Indiana
Delphi Corp.--Energy and Chassis Systems, of Empresas Ca-Le
de Tlaxcala, Mexico
Delphi Corp.--Packard Electric Systems, Plant 50, of Del
Parral, Chihuahua Mexico
Delphi Sistemas de Energia S.A. de C.V., Plant 57, of Chihuahua,
Mexico
Delphi Corp.--Packard Electric Systems, Plant 58, of Meoqui,
Chihuahua, Mexico
Delphi Packard--Centro Tecnico Herramental S.A. de C.V.,
Plant 98, of Ramos Arizpe, Coahuila
Delphi Packard, Plant 51, of Nuevo Casas Grandes, Chihuahua,
Mexico
Maytag Jackson Dishwashing Products of Jackson, Tennessee
Raytheon Missile Systems--Tucson Operations, of Tucson,
Arizona
TI Automotive of Cartersville, Georgia
The Shingo Prize is administered by the Utah State University
College of Business. Awards will be presented at the 16th
annual Shingo Prize Conference and Awards Ceremony, May
20 in Lexington, Kentucky. To learn more, visit www.shingoprize.org.
Overseeing Unfamiliar Projects
Common Among Managers
Learning by leading is a popular
concept in many offices, a new survey suggests. About 40
percent of executives polled in the recent survey said it’s
common for managers to oversee projects for which they have
limited experience.
Executives were asked, “How common or rare is it
for managers at your firm to oversee projects for which
they have limited experience?” Forty-seven percent
said it’s somewhat rare; 33 percent said it is somewhat
common.
The poll includes responses from 150 senior executives--including
those from human resources, finance and marketing departments--with
the nation’s 1,000 largest companies. It was conducted
by an independent research firm and developed by Accountemps,
a specialized staffing service for temporary accounting,
finance and bookkeeping professionals.
“Many leadership skills--such as the ability to
motivate people and inspire motivation--are transferable,
and companies frequently ask experienced managers to oversee
a range of initiatives, including those outside their immediate
expertise,” explains Max Messmer, chairman of Accountemps.
“This is especially common as firms strive to maintain
productivity despite leaner staffing levels.”
Messmer notes that managers who take on assignments outside
of their scope often work harder to win employee trust.
“Staff members may initially be skeptical of leaders
who come from outside the ranks,” he says. “Managers
in this situation must show that they value their team’s
expertise and encourage everyone working on the project
to share ideas and information.”
Messmer offers four tips for reducing the learning curve
on new projects:
Let the experts be the experts. Rely on your team
for its knowledge and tactical skills, and focus your efforts
on motivating employees and keeping projects on track.
Don’t rush to judgment. Avoid making quick
decisions. Instead, consider the situation from several
different angles and gather feedback before establishing
a plan.
Take all perspectives into account. Solicit various
viewpoints but don’t be unduly influenced by one or
two team members.
Give credit where it’s due. Thank employees
and co-workers who share insights and give them credit for
their ideas.
|