NOTE: A correction was made to "D'oh the Math." Originally the equation read (y-x/x) x 100.
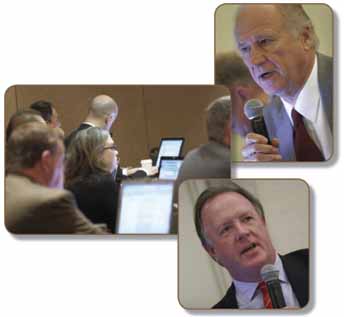
Above, Joe Bransky; below, Nigel Croft
|
Improving Certification
Output matters. That was the overriding message at the March meetings of the International Accreditation Forum's technical and executive committees. Finding ways to improve accreditation body (AB) and certification body (CB) accountability was a major topic of discussion at the event, and measuring AB and CB effectiveness through an examination of their registered clients' product output is a way of verifying this effectiveness, reported several meeting participants.
A paper produced by the IAF technical committee's (TC) Reengineering Accreditation Task Group calls for better assessment of the competency of AB assessors, the improved verification of AB impartiality, improved criteria for audit preparation and reports, and more complete AB surveillance audits of certification bodies. The paper will be discussed at the IAF's next meeting in Sydney, Australia, planned for October.
Several TC members acknowledged that shoddy products shipped by certified companies have the potential to erode the value of accredited certification. The problem lies with unaccredited certification companies and inexperienced auditors who are driven more by money than by the quest for quality improvement.
"The ultimate accreditation is from the client's customers," says Nigel Croft, convener of ISO/TC 176, the technical committee responsible for developing the ISO 9000 series of standards and guidance documents. "Those clients are the ones paying the bills for the good and the bad, and they are the ones we need to pay attention to."
The discussion is part of an ongoing effort by the IAF to increase the value of accredited certification to management system standards. Long-term action items planned by the organization include:
• Developing methods to measure the quality of certified organizations' product output
• Collecting and processing information from second-party audits, regulator audits and media accounts of certified organizations
• Pushing for the evolution of the relationship between ABs and CBs into stricter cooperation and partnership
• Substantially tightening the requirements for obtaining and maintaining accreditation, especially with regard to the verification of the implementation of improved rules
• Strongly regulating price competition
"A substantial redesign of the accreditation and certification processes… cannot be based only on defining better rules, but implies a major cultural and political change," says Lorenzo Thione, convener of the Reengineering Accreditation committee. "This cannot be achieved without the consciousness and cooperation of all the interested parties."
The larger IAF meeting, held March 24-30 in San Francisco, included daylong breakout sessions for several other of the TC's work groups, including the ISO 20000 work group, which continued its work on revising and reviewing the service-sector standard; the ISO 14065 work group, which is developing an international standard for greenhouse gas measurement and reduction; and the ISO 9000 advisory group, which discussed the ongoing revisions of ISO 9001 and ISO 9004.
The TC agreed to form several new work groups, as requested by industry representatives. The new work groups will explore accreditation and standardization in the product-certification sector, and a global accreditation program for ISO 13485 (which relates to medical devices), among others.
The weeklong conference--hosted by the ANSI-ASQ National Accreditation Board (ANAB)--also featured ANAB's first Industry Day. The event featured presentations from industry sector representatives who discussed ways in which accreditation and certification can be improved to benefit them. Joe Bransky, General Motors' representative to the International Automotive Oversight Bureau, gave a particularly pointed address, urging the IAF to require more accountability from accreditation bodies, and automotive suppliers to be more transparent with their supply chain challenges. He also noted that certification bodies haven't sufficiently developed auditor competencies, and reported the need for more effective witness auditing.
"There should be no secrets," Bransky says. "If we are serious about improvement, we need to put all the cards on the table and say where we really are."
Also at Industry Day, the technical committee agreed to form an end-user advisory group, which will provide information to the TC about how IAF decisions affect certification among end-users. A representative from the advisory group will also be a member of the TC.
D'Oh the Math!
I'm not sure if the onslaught of e-mail responses to last month's "Do the Math" was because the error was so ridiculously easy to spot or because the subject of the article was about controversial MSNBC commentator Keith Olbermann's salary demands. Along with correct answers to the puzzle, we got plenty of opinions about Olbermann. But back to math.
According to the Dec. 19, 2006, New York Post article, "The obnoxious MSNBC gabber is trying to squeeze a whopping 400-percent raise out of his cash-strapped network. Broadcasting & Cable reports [Olbermann] wants to increase his annual $1 million salary to 'north of $4 million.'"
Actually, an increase from $1 million to $4 million is a 300-percent raise, not 400 percent. This is a pretty common error; we see it a lot in press releases.
In case you have forgotten the equation, to calculate percent increase or decrease from x to y: (y- x)/x × 100.
This month's "Do the Math" winner, randomly selected from all correct answers, is Dean Whitehead. Congratulations Dean, you win a (most likely useless) prize from woot.com .
The first part of the puzzle will be getting there: www.sfgate.com/cgi-bin/article.cgi?f=/c/a/2005/10/15/BAGOEF8UPS1.DTL&hw=simpsons+rubenstein&sn=002&sc=350. If you see the headline, "Cal math lecture to feature binge-eating cartoon dad," you're at the right spot. Now find the error. I'll save you a little time: It's not the "pi to 40,000 places" reference.
Send your entry by clicking the feedback link at the bottom of this page. If we choose your entry, you win a prize.
Send us an example of any math murder you spot in newspaper, radio or television. If we use your entry, you get a prize.
Hexagon, FARO Settle Patent Lawsuit
Hexagon subsidiary ROMER Inc. and FARO Technologies Inc. recently agreed to settle a lawsuit that alleged that FARO breached ROMER's patent of unlimited movement in an articulated-arm measuring device.
Under the terms of the settlement, patent suits pending in California and Florida and a lawsuit involving claims of false advertising will be dismissed. The patent dispute involved a key feature of articulated-arm coordinate measuring machines--the ability to rotate the primary axis indefinitely without encountering a hard stop. The measurement devices are used by engineers to design and inspect a variety of manufactured products.
"We are pleased to see these lawsuits come to an end. We feel that the mutual understanding between us and FARO will work in both parties' favor. We will now again focus exclusively on doing what we do best--making metrology products--and compete with each other in the marketplace and not in the courtroom," says Ola Rollén, CEO and president of Hexagon AB.
The War Over Health
Americans are more worried about paying for their health insurance than the war in Iraq, according to research sponsored by the American Society for Quality.
The rising cost of health care was the No. 1 concern for survey respondents, with 85 percent naming it as their top concern. In contrast, 80 percent cited the rising cost of fuel as their main worry and 79 percent reported the war in Iraq as their top concern. The threat of global warming was cited by 61 percent of respondents.
Universal health coverage got very strong approval ratings in the survey, with 79 percent of respondents saying that they believe it would improve health care quality. Nearly nine in 10 adults (88%) said that being able choose their physician would also improve the quality of their health care.
"It's clear that Americans are getting hit hard by our current health care crisis, and they are looking for change," says Jim Levett, ASQ health care division officer. "This survey shows the increasing importance for both the U.S. administration and health care organizations across the country to look for new solutions to improve the quality of health care while still managing escalating costs."
The survey also found that women are more likely than men to believe that universal health care would improve health care quality, and that women are more likely than men to delay medical procedures because of the cost. In addition, 68 percent of respondents said they thought that health care quality would improve if people were less dependent on health insurance companies for the cost of their health care.
Thirty-nine percent of respondents said that they would be concerned or very concerned about medical errors if they were hospitalized.
The survey was commissioned by ASQ and conducted by Harris Interactive.
For more information, visit www.asq.org.
Day in the Life
Andy Joswiak, Linetec VP of operations
|
Linetec is one of the largest paint and anodize finishers in the United States, and the country's largest independent architectural finisher. It operates a national trucking network and maintains 500,000 square feet for finishing products such as aluminum windows, wall systems, doors, hardware and other metal components.
The company received the 2006 Wisconsin Manufacturer of the Year Grand Award recently, and has adopted Six Sigma as its continuous improvement methodology. More than 50 Linetec employees have completed advanced Six Sigma training and now lead internal projects, which have included waste and lead time reduction, cost savings and collaborative projects with customers.
Linetec was also recognized for its customer focus, community involvement, environmental leadership, safety and sales growth, and its use of technology to enhance employee and customer communication. Here, Andy Joswiak, Linetec's vice president of operations, discusses how the company maintains its focus on quality.
Quality Digest: What were some of the problems Linetec was having when it began its Six Sigma effort?
Andy Joswiak: Linetec was the premier aluminum finisher in the architectural industry but knew it could improve its operational efficiency. We had some great equipment, but we couldn't optimize it with the tools we had. For example, we had the best paint application equipment money could buy, but it only improved our process slightly when compared to our old equipment. Our people were working hard with some successful days, and then failure would occur without any apparent reason. Defects were up, and on-time delivery was down. We were working Saturdays and still delivering late. We needed something more, a toolset to target the root-cause issue behind the problems and a way to eliminate or at least minimize their negative effects. That toolset was Six Sigma.
QD: How did Linetec train employees?
AJ: Linetec began training senior staff on the tools, using a consultant organization. Soon afterward we trained several individuals to the Black Belt level, which included four full weeks of training. Eventually, every person in our leadership group--including all managers, supervisors and engineers--were trained to the Green Belt level. Currently we have 12 Black Belts and nearly 50 Green Belts trained, with five more currently in training. Several hourly associates were or are currently being trained to the Green Belt level as well.
QD: What other quality improvement methods has Linetec used?
AJ: Prior to Six Sigma, Linetec was heavily involved in theory of constraints (TOC), statistical process control (SPC) and a few other improvement initiatives. They worked OK but didn't always solve the problems we were facing. TOC and SPC told us where the bottlenecks were and ensured our process was running consistently, but that wasn't enough.
QD: What kind of projects did the company undertake?
AJ: We started with what we thought were our largest issues: Paint rework, paint throughput, paint consumption reduction, anodize rework, anodize throughput and material damage. We thought that if we could fix or improve these problems, we would have all of our problems solved. Those projects were completed, and we found more opportunities for improvement. We are now in our sixth year and have more than 100 projects behind us. We have done several operational improvement projects, some joint projects with customers as well as suppliers, and recently some very successful transactional projects, such as scheduling accuracy and order-entry error reduction. We currently target nearly $1 million in improvement opportunities per year.
QD: How has Six Sigma changed Linetec?
AJ: Six Sigma gave Linetec a methodology that allows us to have a systematic approach to solving nearly any problem or opportunity that presents itself. We now have methodology and training programs that ensure the knowledge learned is passed on to those who need to know it. Through Six Sigma, we have improved our product and services to our customers, including reduced defects and increased on-time delivery, and have made Linetec a great company to work for through increased profits, growth, enhanced safety, reduced stress and more opportunity for those who want it. Since starting the Six Sigma journey six years ago, Linetec has eliminated more than $4 million dollars in operational cost. This enables Linetec to be more reliable, consistent and dependable to our customers, associates and shareholders. This is a great process improvement toolset and one that will be with Linetec for many years to come.
WCBF Knows Six Sigma
Two upcoming conferences from WCBF will include practical information on the use of the Six Sigma methodology.
The third Annual Design for Six Sigma Conference will feature speakers from varied industries, including Kevin Cluff, Abbott Pharmaceuticals business excellence manager; Rick Hefner, Northrop Grumman senior manager of process initiatives; and Mark Wilen, Boston Scientific director of DFSS and corporate innovation. The conference will be held June 20-21 at The Congress Plaza in Chicago. For more information, visit www.wcbf.com/quality/5075.
WCBF's second annual Global Six Sigma Summit and Awards will be held at the Rio All-Suite Hotel & Casino in Las Vegas Oct. 23-26, and will include speakers such as Jim Collins and Mikel Harry. The call for entries for the awards is now underway. To find out more or make an award nomination, visit online at www.tgssa.com . To register for the summit, visit www.wcbf.com/quality/5081.
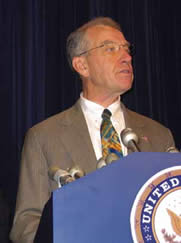
Senator Chuck Grassley (R-Iowa)
|
Leaders Recognized for Advancing Health Care Quality
The National Committee for Quality Assurance recently presented NCQA Quality Awards to a senator, a governor, a physician-advocate, and a collaboration between nonprofit health organizations and a children's television network.
The recipients are:
• Senator Chuck Grassley (R-Iowa), for leading the fight to pass the Medicare Modernization Act of 2003, which gave a prescription drug benefit to millions of senior citizens.
• Governor Kathleen Sebelius of Kansas, who has made improving the health of her state's citizens one of her top priorities. She has raised childhood immunization rates and launched the Healthy Kansas campaign to inspire her constituents to adopt healthier lives.
• Edward H. Wagner, M.D., whose Improving Chronic Illness Care initiative is dedicated to helping the 133 million Americans who suffer from chronic pain to lead healthier lives. Wagner is the director of the MacColl Institute for Healthcare Innovation at Group Health Cooperative in Seattle, and his care model has been adopted by health plans and medical practices nationwide.
• The Let's Just Play Go Healthy Challenge, which is a collaboration between the William J. Clinton Foundation and Nickelodeon that is designed to combat obesity in young children. The challenge follows four kids on their quest to eat better, play harder and feel better; a highlight of the program was the third annual World Day of Play, when the network went off the air and urged kids to go outside and play.
"Each of our winners is being recognized for turning their commitment and dedication into action that has helped health care achieve its fundamental purpose--to improve health," says Margaret E. O'Kane, NCQA president.
For more information on the NCQA Quality Awards, visit www.ncqa.org.
A Hard Look at 'Soft' Issues
Executives are more concerned than ever about "soft" issues such as corporate culture, environmental protection and knowledge management, according to new research.
Nine out of 10 respondents to Bain & Co.'s annual Management Tools & Trends study said that they believe corporate culture is as important as strategy for business success. Knowledge management, for the first time, ranked among the top 10 "most used" business tools, and seven out of 10 respondents said that they consider environmentally friendly products and practices to be important parts of their mission. This environmental focus is even more important to executives in emerging-market countries than those in established-market countries, with 77 percent and 59 percent, respectively, reporting its prioritization.
"Executives are actively addressing higher-order needs, changing the rules and tools of management," says Darrell Rigby, study author. "Organizational culture and so-called softer issues are now top of mind. Executives are clearly looking beyond cost cutting for success."
Increasing dissatisfaction with offshoring was also a major trend in the survey; it fell from seventh to 16th place in satisfaction this year. Offshoring showed the sixth-highest defection rate in terms of the number of companies that have abandoned its use.
The top 10 most-used management tools, according to the study, are: strategic planning (first); customer relationship management; customer segmentation; benchmarking; core competencies, and mission and vision statements (tied for fifth); and outsourcing. Business process reengineering, knowledge management, and scenario and contingency planning, collectively, tied for eighth place.
Other study highlights include:
• Chinese economic pessimism. 45 percent of Chinese executives reported that they are preparing for an economic slowdown, as compared to 27 percent in North America, 18 percent in other Asia-Pacific countries, 15 percent in Europe and 10 percent in Latin America.
• Continued globalization. 42 percent agree that cross-border acquisitions will be critical to achieving growth objectives in the next five years; 53 percent said that working with China and India will be vital to success over the same time period. Nearly two-thirds said that innovation could be increased by collaborating with outsiders, even competitors.
• Emerging vs. established markets. Executives in emerging markets tended to use total quality management, supply chain management and Six Sigma more than their counterparts in established markets. Executives in established markets were more apt to use mergers and acquisitions, offshoring, benchmarking, and scenario and contingency planning.
• Public vs. private ownership. 43 percent of respondents agree that their companies would work better if privately owned in the long term; 25 percent disagreed. Thirty-nine percent said that they would rather work for a privately owned company, and 27 percent said that they would not.
For more information, visit www.bain.com/management_tools/Management_Tools_and_Trends_2007.pdf.

John Dew |
Mr. Dew Goes to
Washington
The chair of the American Society for Quality's Education Division was recently appointed to serve on a U.S. Department of Education committee.
John Dew will be one of 18 committee members representing education and nonprofit institutions in the United States. He has a Ph.D. in education and was a quality professional at Lockheed Martin for 23 years before joining the University of Alabama, where he currently serves as the director of quality improvement and planning. He has written five books.
"The future of quality in higher education has never been more critical than it is today," says Dew. "For that reason I am pleased that I've been selected to represent ASQ among this group of influential educators."
Dew will serve on the Department of Education's Rulemaking Committee, which establishes rules for accreditation in higher education.
For more information, visit www.asq.org/education/why-quality/overview.html.
Statistically Speaking
There are between 15,000 and 17,000 components in the average automobile made in the United States. In North America alone, 70,000 cars are delivered every business day.
Source: International Automotive
Oversight Bureau
|