by Dirk Dusharme
In 1895, Wilhelm Roentgen’s
discovery of X-rays proved to be one of the key findings
of the 19th century. Within months of his breakthrough,
this “new light” was put to use identifying
fractures and locating bullets in gunshot wounds. But although
X-rays were initially used for medical purposes, theories
about the new technology’s use in nondestructive testing
were also examined. Early X-rays of zinc plates, for instance,
hinted at the possibility for welding control--an idea that
bore fruit during the early 1900s, when X-rays were used
to examine boilers.
During the next half-century, X-ray technology--although
constantly refined--didn’t change drastically. X-rays
were emitted from a source, passed through an object and
detected either on film or a fluorescent screen. Contrast
and spatial resolutions improved, as did film speeds and
control over X-ray sources. Scintillation screens were also
used with film to achieve better images at lower dosage.
The next great advance occurred during the 1950s with
the advent of the image intensifier. For the first time,
clear images could be made available in real time. With
image intensifiers, X-rays are picked up on a phosphor screen,
focused down to another screen and then viewed either directly
or via a high-quality television image tube or CCD camera.
Despite image intensifiers’ great performance for
real-time imaging, film remained the only option for large
image size and good spatial resolution and contrast until
recently.
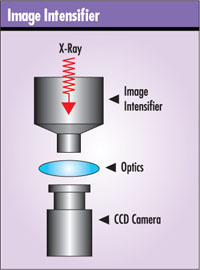
Each of these technologies has its own set of drawbacks,
however. X-ray film must be chemically processed, which
often means about 20 minutes of lag time between an image’s
capture and the technician’s inspection of it. If
the film isn’t properly exposed or the angle is wrong,
it’s a do-over, and another 20 minutes are lost. If
multiple pieces of film must be shot, the time required
to examine an object can run into several hours. Moreover,
a company must have methods in place and employees trained
to safely handle, store and dispose of film-processing chemicals.
Notwithstanding film’s very good spatial resolution,
it has a nonlinear and somewhat limited contrast range.
Add to this the human eye’s limitations to discern
no more than 100 or so contrast levels, and obtaining and
examining--on just one piece of film--an X-ray of an object
with a wide thickness or density range becomes nearly impossible.
For their part, image intensifiers have a limited field
of view, and their bulkiness prevents them from being used
in all applications. Distortion toward the edge of the image
means that only the center portion is useful in some applications.
Image intensifiers’ contrast and spatial resolutions
don’t compare well to other technologies, either.
Image sharing and archiving is an issue for both film
and image intensifiers. This problem is somewhat mitigated
with digitized still or video images, or by scanning X-ray
film, but archiving using these technologies is very space-
and time-intensive.
With the introduction of computed radiography during the
1980s, a giant step forward for X-ray imaging occurred.
Until this time, the technology’s analog nature prevented
any real automation. Inspection, defect recognition, sorting
and the like depended upon human interpretation of film
or image-intensifier images. Computed radiography offered
the benefits of computer-aided image enhancement and recognition,
the ability to store and transmit digital images, and the
elimination of film processing and all its associated costs.
Computed radiography works similarly to film-based X-rays,
but instead of X-ray film, a storage phosphor screen is
irradiated and the latent image stored within it. It’s
then taken to a reader, which uses a laser and detector
to scan the latent image from the screen. In most cases
this technology can be easily retrofitted into film-based
systems, eliminating the need for film, chemicals, processing
lab, equipment and storage.
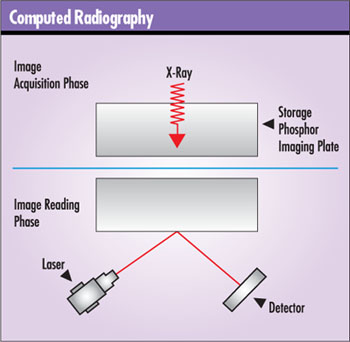
The reduced costs in those areas mean a quick return on
investment, says Fred Morro, Fuji Corp’s. director
of digital radiography products for NDT (www.fujimed.com/ndt/ndt_fcr.html).
“We do a cost analysis for each customer, looking
at film costs, chemical costs and the cost of chemical disposal,”
he says. “It depends on the application, but the ROI
can be less than one year.”
Envision Product Design, developer of the CMOS digital
flat panel (as illustrated below), estimates that recurring
costs such as film, processing and chemical disposal reach
about $6,000 per 1,000 X-ray exposures. This doesn’t
include costs for film storage or a processing lab.
In terms of performance, computed radiography’s
contrast resolution of 12 bits, or 4,096 contrast levels,
rivals film, says Morro. And although its spatial resolution
doesn’t yet surpass film, it’s more than enough
for most NDT applications, he adds. Computed radiography
readers for NDT can resolve 5 line pairs/mm (i.e., 100 µm).
Because of its high contrast range, computed radiography
has the ability, as do all digital radiography technologies,
to capture the entire density range of most objects in one
pass, something that’s impossible with film. Computer
manipulation then makes it possible to view just the density
ranges of interest.
Like film, computed radiography screens can be cut or
bent. Although the storage plates are more expensive than
film--a 14 X 17 in. plate costs about $700--it can be used
thousands of times, limited only by mechanical wear caused
by handling. This makes it cheaper than film. Also similar
to film, storage plates can be used--barring condensation
or other moisture issues--for field X-ray inspection under
extreme temperature conditions.
One advantage of computed radiography over other digital
radiography technologies is that, in most cases, only one
screen reader is needed to service an entire lab. The reader
is separate from the screen and therefore not an integral
part of the image-capture process. This could offer an advantage
over other digital technologies, where image acquisition
and the reader are integrated--requiring the purchase of
an entire system for each concurrent use.
A disadvantage of computed radiography is that, like film,
it isn’t real-time. Although faster than film processing,
the screen must still be removed from the X-ray station
and fed through the reader. Computed radiography represents
a huge step forward and is still the prevailing nonfilm
technology, but it can’t provide all the benefits
of digital X-ray products.
During the late 1990s, digital flat panels were introduced.
Unlike their film or computed radiography predecessors,
they provide digital readout of an X-ray image, making it
possible to automate X-ray NDT inspection. Except for the
fact that they can’t be cut or bent, digital flat
panels are used in much the same way as film or computed
radiography and can be left in place while robotic or conveyor
systems bring parts to them or reposition parts for multiple
views. The operator doesn’t have to change film or
storage phosphor plates between shots, and the X-ray image
is available seconds after it’s acquired, greatly
improving on the productivity offered by film or computed
radiography systems.
Currently, two digital flat-panel technologies are battling
head-to-head for the market: amorphous selenium (a-Se) and
amorphous silicon (a-Si). Outwardly, they both function
in the same manner: X-rays are picked up by the panel, which
converts them into a digital image that can be read from
the plate. Because the panels require no processing, images
can be obtained at rates of one image every few seconds
up to live video speeds of 30 images per second. Because
of their better resolution and increased field of view,
flat panel displays with 30 images-per-second speed are
ideal replacements for image intensifiers. However, depending
upon the manufacturer, the 30 image-per-second frame rate
may come at the cost of decreased resolution.
With amorphous selenium technology, X-rays strike an a-Se
layer, which converts them directly into an electric charge
that’s further converted to a digital value for each
pixel. This is called a direct-imaging method. Proponents
of a-Se say it offers better spatial resolution than a-Si.
With what are commonly called amorphous silicon panels
(a misnomer because even a-Se panels use amorphous silicon),
X-rays first strike a scintillation layer. This layer emits
photons in direct proportion to the energy of the X-rays
striking it. The photons are picked up by the underlying
a-Si photo-diode matrix, which converts them to an electric
charge. This charge is then converted to a digital value
for each pixel. Because of the intermediate step of converting
X-rays to light via the scintillation layer, this is called
an indirect-imaging method. The scintillation layer is commonly
composed of either cesium iodide or gadolinium oxysulfide,
with CsI being the preferred material. Proponents of a-Si
panels say they offer much faster frame rates, up to 30
images per second, than a-Se panels.
Both technologies offer near-film spatial resolution but
with contrast ranges far exceeding film.
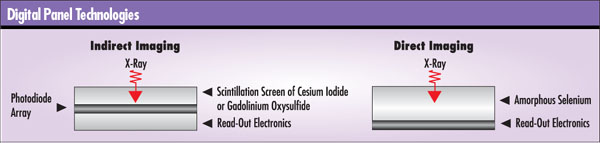
The battle between these two technologies--waged mostly
on a theoretical level with much talk of modular transfer
function, detective quantum efficiency and numerous Einsteinian-looking
equations--concerns which offers higher spatial resolution
with the best contrast and least noise. Bedford, Massachusetts-based
Hologic Inc., the main developer of a-Se flat panels, argues
that light generated by the scintillation layer of indirect
systems is somewhat scattered before reaching the photodetectors,
therefore degrading resolution. By contrast, with a-Se systems,
the electrons generated by X-rays striking these panels
are picked up directly by the electronics with very little
scatter, resulting in better image quality at a higher resolution.
“I would argue that it’s not just theoretical,”
says Ken Swartz of Hologic Inc. “There are now a number
of published studies that have compared the image quality
and productivity advantages of direct and indirect capture
detectors.” He points to an article by Ehsan Samei
and Michael Flynn in the April 2003 issue of Med. Phys.
“An Experimental Comparison of Detector Performance
for Direct and Indirect Digital Radiography Systems”
in which a Hologic direct-imaging panel was compared to
indirect-imaging panels from GE and Philips. The authors
conclude that when resolutions smaller than 200 µm
are required, a-Se performs better. For resolutions greater
than 200 µm, a-Si panels perform better. Swartz also
points out that Kodak, Siemens, Philips, Agfa and Instrumentarium
have chosen a-Se detectors for difficult medical applications
because of their higher-resolution image quality.
Flat
Panel Specifications What follows
are some simple specifications for a few digital flat
panels produced by some of the key vendors.
. This company’s
11 X 16 in. a-Si panel offers 12-bit (4,096 gray levels)
and 127 µm resolution. Agfa also repackages
the Hologic 14 X 17 in. a-Se panel. Both a-Si and
a-Se are available with a temperature controlled enclosure
for field work.
www.agfandt.com/bu/ndt/index.nsf/
EN/radviewdigitalsystems.htm
GE currently offers four a-Si digital detectors ranging
in size from 63 to 256 sq. in. They can operate in
static mode and/or up to 30 Hz image acquisition rates,
and all have 14 bit (16,000 gray level) contrast capability.
Spatial resolutions of up to 9 line pair/mm (55 µm)
without geometric magnification is available.
www.ge.com/ndt
The company’s
14 X 17 in. a-Se panel has a resolution of 3.6 line
pairs/mm (139 µm) and 14-bit (16,000 gray levels).
Hologic also sells a panel with 7.2 line pairs/mm
(70 µm).
www.hologic.com/prod-dr/sys-digi.shtml
The company’s
highest resolution panel is 16 X 16 in. with 200 µm
resolution. A smaller 8 X 8 in. panel has a resolution
of 400 µm, up to 7 frames-per-second
capture rate and can also be used in high-energy
applications up to 25 MeV. Contrast resolution for
all products is 16 bits or 65,000 gray levels.
optoelectronics.perkinelmer.com
(Select “Digital Imaging” from left menu.)
Varian Medical Systems
Security & Inspection Products. The company’s
12 X 16 in. a-Si panel has a resolution of 3.97 line
pairs/mm (126 µm). A high-speed mode will capture
30 frames per second at 1.29 line pair/mm (388 µm).
Varian also sells a high-energy option that allows
the flat panel to be used in applications up to 9
MeV. With this option it would be possible to examine
aluminum castings up to 27 in. thick, according to
the company. Varian’s products have a contrast
resolution of 12 bits or 4,096 shades of gray, but
a 16-bit version (65,000 gray levels) is available.
www.varian.com/sip/dig100.html
|
But the real test for NDT professionals is which of these
technologies will get the job done in an NDT application.
The answer is, “all of them,” according to
Scott Thams, president of X-R-I Testing (www.xritesting.com),
an independent testing lab that does work for aerospace
and automotive industries. “We find that amorphous
selenium, amorphous silicon and computed radiography are
good enough,” explains Thams. “They’re
film-equivalent.” Eighty to 90 percent of X-R-I’s
X-ray inspection is done on film--the company spends more
than $1 million on X-ray film per year--and Thams considers
himself a pretty good judge of how the various technologies
stack up against film and each other. “All of these
technologies have matured to the point that comparing them
is just splitting hairs,” he observes.
Specsmanship aside, manufacturers interviewed for this
article did acknowledge that no one technology is the silver
bullet; it all depends upon the application. For NDT, arguments
about which technology provides the highest-resolution images
might not really matter, says PerkinElmer’s Mario
Gauer, product leader for flat-panel detectors and image
tubes.
“You have to apply the technology to the respective
application,” he explains. “For automated defect
recognition or 3-D reconstruction, the use of detectors
with high dynamic range and excellent signal-to-noise characteristics
will reduce the number of required images and, thereby,
the cycle time.”
Whether a-Se or a-Si, both camps agree on digital panels’
productivity.
“Our thrust is not so much to replace film as to
automate a process,” says Greg Budner, technical account
representative for Varian Medical Systems Security &
Inspection Products. “We’ve taken a high-volume
film application and used the panel with a robot to do many
parts. The operator doesn’t have to take 20 minutes
to set up and look at a part.”
Budner points to the productivity gains that came about
after Varian installed a digital flat-panel X-ray to inspect
Ariane V satellite placement rockets. Before installation,
inspecting a cylindrical carbon composite part took more
than 350 pieces of X-ray film, roughly one shot per degree
as the part was incrementally rotated in front of the X-ray
machine. Using a digital flat panel, Varian could provide
X-ray inspections that greatly reduced inspection time.
As the part was rotated, the system captured and stored
an X-ray image in seconds before moving to the next position.
The system operated at 6 and 9 MeV energy levels and could
detect down to 300 µm occlusions with a 2 percent
contrast ratio through as much as 1,200 mm of carbon.
Although great for lab or production environments, Thams
and others familiar with all the X-ray technologies aren’t
convinced that digital flat-panel technologies will stand
up as well to field conditions as the more rugged film or
computed radiography. “The digital flat panels are
fragile, and they’re sensitive to temperature variations,”
says Thams. They also need power and cabling at the inspection
location where film and computed radiography do not, he
explains.
Varian and GE say that environmental concerns aren’t
an issue. GE has a thermal stabilization system and claims
its units are not sensitive to sunlight, and Varian says
its system works fine without thermal stabilization. Both
companies have a-Si flat-panel units in use in harsh desert
environments inspecting pipelines and unexploded ordnance.
On the other hand, a-Se panels were designed for medical
applications and normal room temperatures of 50° to
86° F. For temperatures outside this range, active heating
or cooling systems are required.
But the real issue for field work isn’t so much
environmental but rather the portability of computed radiography
and film vs. the data-collection capabilities of digital
flat panels, says Mike Bernstein of GE Inspection Technologies.
“For a one-off picture, computed radiography does
a nice job,” he says. “It’s portable in
terms of what you carry to the pipeline, for instance, and
it’s a bit more flexible. But if you’re taking
40 or 50 images, you have to think about the logistics of
processing those images.” Compare that to the ability
to capture and disposition images instantly and simply move
to the next location, and that versatility may offset the
portability advantages of film or computed radiography,
says Bernstein.
One disadvantage of digital panels, and perhaps a costly
one, is that, unlike film or computed radiography, where
several technicians can take X-ray images at one time and
process them in one film or computed radiography processor,
a complete system is required for each X-ray station--at
a cost of about $150,000 each--if more than one digital
flat-panel X-ray inspection is happening simultaneously.
This might be somewhat offset by productivity gains (e.g.,
fewer stations and lower labor expenses), but it’s
a consideration.
Another consideration in NDT applications is the issue
of dead pixels. Dead pixels or even dead lines (i.e., rows
of pixels) are inherent in this technology but can be replaced
artificially based on surrounding pixels (i.e., interpolation).
Nonetheless, in some industries, this might not be acceptable.
By analogy, consider that in aerospace, inspection codes
require that film be reshot if there’s an artifact
(scratch, pin hole, bubble, etc.) on the X-ray film itself
within the region of interest, says Thams. Bernstein doesn’t
see this as an issue and points out that with GE’s
flat panels a dead pixel is only 100 µm square, while
film artifacts are much larger.
This argument does point to one last consideration: industry
acceptance of nonfilm X-ray inspection. Currently, various
industry groups and standards organizations are looking
at how to change inspection specifications in order to accommodate
the digital X-ray technology, says Thams. He says that the
reason 80 to 90 percent of his X-ray work is still done
in film is because companies still specify testing requirements
in terms of it.
Although there currently is not a common industrial standard,
Bernstein indicates many companies have already defined
quality specifications for the implementation of nonfilm
X-ray. “GE Aircraft Engines has allowed the use of
both image intensifiers and digital detectors for years,”
he says. “In fact, at one of our manufacturing facilities,
digital detectors have been used to acquire and disposition
more than 30 million images since the mid-1980s.”
With
all the buzz over a-Si and a-Se flat panels, some other
flat-panel technologies might be overlooked but shouldn’t
be, such as the CMOS X-ray. This interesting new product
from Alaska-based Envision Product Design (www.cmosxray.com)
is a scanning flat panel. It consists of a linear X-ray
detector array and drive system housed within a flat panel
3 in. thick. The panels can measure up to 24 X 36 in. and
are used in the same fashion as the ones described earlier.
With this technology, as the scanner traverses the panel
(think document scanner), X-rays pass through a slot that
collimates them before they strike the scintillating material.
The material is deposited on the ends of a fiber optic bundle
that runs the length of the array (see illustration to the
right). In an arrangement that protects the X-ray-sensitive
CMOS detectors from X-ray damage, the fiber optic bundle
leaves the scan head at a right angle to the X-rays and
connects to the CMOS detectors, which are housed beneath
tungsten and lead shielding. The system can be built to
operate with high-energy X-ray systems up to 10 MeV.
Alternatively, Envision sells CMOS linear arrays up to
6 ft long that can be fixed in one place while parts are
moved past robotically or on a conveyor system. The image
on this issue’s cover (minus the rider) was taken
by moving the motorcycle in front of a 54 in. linear array.
The 54 X 84 in. image took 110 seconds to acquire.
Envision flat panels and linear arrays have spatial resolutions
of 80 µm and contrast resolution of 12 bits, or 4,096
gray levels.
Envision also sells a conventional 4 X 4 in. flat-panel
CMOS array capable of 50 µm resolution and 12 bits
of contrast.
As mentioned, one of the arguments against digital flat
panels for fieldwork is the necessity for power and cables.
Israel-based Vidisco Ltd. (www.vidisco.com)
has addressed this issue with its Flat FoX portable and
wireless a-Si systems. According to company literature,
the entire system, including a 150 kV pulsed X-ray source,
is contained in one case and can be used anywhere in the
field without an AC power supply. The equipment can also
be used with most existing heavy-duty industrial X-ray sources.
It captures a 12- to 16-bit image at 127 to 400 µm
resolution on an 11 X 16 in. a-Si panel. The system will
operate from a battery for two hours. A wireless option
allows the X-ray source to be triggered remotely and/or
image transmission delivered up to 200 m.
Although computed radiography is still the technology
of choice for film replacement, look for digital flat panels,
probably a-Si, to become the next key player in the NDT
X-ray market. The ability to capture images and store or
transmit them in real time opens up possibilities for NDT
professionals that don’t exist with film or computed
radiography. GE, Varian, Agfa, Siemens, PerkinElmer and
others will drive the technology to the next level. Though
most digital flat-panel manufacturers say they offer a productivity
tool rather than film-replacement technology, advances in
digital X-ray technology--such as improved contrast and
spatial resolutions, lower noise, improved ruggedness and
lower cost--could chip away at the film and computed radiography
market.
Dirk Dusharme is Quality Digest’s technology
editor. Letters to the editor regarding this article can
be e-mailed to letters@qualitydigest.com.
|