by Leo Cote
Manufacturers are severely
challenged by a double-edged sword: They must make products
at the highest quality while being extremely adaptable to
customer demand. These two requirements do not easily co-exist.
Manufacturing to quality typically means lower yield and
higher cost, while being adaptable can create chaos in operations
management, resulting in reduced efficiency and quality.
Can manufacturers address both requirements and still maintain
market momentum?
A significant contribution to manufacturing has been the
development of software solutions that address all aspects
of the product lifecycle--from product inception to aftermarket
service. Forward-looking businesses are beginning to realize
the benefits of manufacturing software and are extending
advanced technology and solutions to their processes, resources
and partners. In doing so, these businesses are capable
of maintaining both operational flexibility and highest
quality, helping them meet business goals of growth, efficiency,
cost containment and customer satisfaction, even through
rocky economic times.
This article focuses on one such company, Network Engines,
which stayed ahead of the dotcom crash and was able to reinvent
its business with the help of its intelligent manufacturing
system built on multiple software solutions.
Network Engines was founded in 1997 and went public in
mid-2000, raising $117 million just before the Internet
bubble burst. Previously focused on providing make-to-stock
servers designed to quickly implement Web-based businesses,
the company reconstructed its business to reflect what its
customers needed in the changing economy: enterprise appliance
solutions for the storage and security software industries.
An enterprise appliance is a network-enabled device designed
to provide a single dedicated service or a suite of services.
Installation and maintenance is greatly simplified because
of its stand-alone nature. An appliance allows IT staffs
to rapidly deploy new applications.
Network Engines partners with software companies, licenses
their software, installs it on hardware and sells the resulting
appliance. This provides customers with ready-installed
software on a plug-in appliance, reducing the complexities
typical in the support and maintenance of multivendor software-hardware
bundles.
Network Engines’ business is focused on quality
“out the door” through its appliances and integration
services to software companies. Network Engines takes a
best-of-breed business approach in delivering the highest
quality of products and services to its appliance partners.
Using specific business processes to ensure the quality
of the manufacturing process, and to better monitor and
control the delivery of orders, Network Engines employed
the use of an intelligent manufacturing system that has
ensured the efficient fulfillment and delivery of product
to partners’ sales channels or end-users throughout
the company’s change in focus and product direction.
The system’s flexibility enables Network Engines to
successfully drive a highly mixed line of products and still
maintain consistently high levels of quality and yield.
Network Engines relies on a manufacturing system built
on a solid, integrated information infrastructure that provides
the flexibility to address market shifts. In the interconnected
system, engineers use Agile Software to create products,
the manufacturing department uses Datasweep solutions to
build and test products, and business administrators use
Microsoft Great Plains software to input sales orders and
procure supplies. Web tools on the front end convert the
data into actionable business information for analytics
and reporting. The system provides an open database scheme
and the ability to activate manufacturing plant lines as
needed.
Here’s a closer look at the three applications:
Agile Software. Agile Software provides the tools to create
product designs and release them to manufacturing. It maintains
critical product data such as manufacturing instructions,
product requirements, bills of material and engineering
change orders.
Microsoft Great Plains. Among other things, this application
provides sales order and procurement information that allows
the user to view material requirements by day, week or month,
or in a bucketless format. Great Plains collaborates with
finance on order approvals and then controls the submission
of the work order to manufacturing. It also processes orders
to suppliers, as well as finished goods inventory.
Datasweep. Datasweep’s solutions provide the manufacturing
system and process control in order to build customized
units correctly and on-time while retaining visibility into
production status and key performance indicators throughout
the process and across the supply chain.
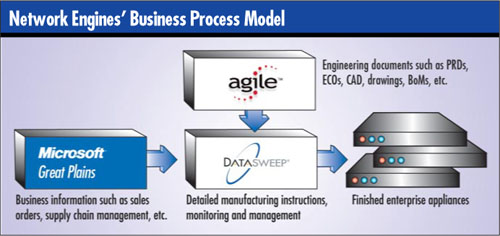
One of the main reasons for Network Engines’ success
is a flexible information technology infrastructure that
has integrated these different applications. The Datasweep
solutions are integrated with Microsoft Great Plains to
seamlessly share and update business information on sales
orders, suppliers, work orders and just-in-time inventory
management. Datasweep is also a solution partner of Agile
Software Corp., which achieved certification to the Datasweep
Advantage suite for its Agile Interface product. With this
end-to-end solution, Network Engines is able to design,
build and track customized products across the entire product
lifecycle.
A product order is created from manufacturing instructions,
product requirements documents, bills of material and engineering
change orders. Network Engines uses Agile Software solutions
to record this important information, maintaining document
history and revision control. When an engineering change
order is created, all the necessary information including
date, the reason for the order, the affected items and the
“class” of the order is logged. The engineering
change order is then classified (e.g., critical, rework,
documents only or procedural). Based on the class of the
order, Agile Software applications will alert, notify or
request approvals from the appropriate decision makers.
The engineering change order process also alerts the manufacturing
floor, putting a hold on units in process and preventing
new units from being manufactured--when necessary. Once
all appropriate parties have been notified and approvals
have been received, the engineering change order is executed.
Microsoft Great Plains is Network Engines’ ERP/MRP
package. This package is used to manage inventory, sales
orders and supplier relationships. Great Plains provides
a database of current in-stock inventory that’s cross-indexed
with a parts list for each appliance product manufactured.
This allows Network Engines to make accurate projections
on requirements while effectively managing supplier orders
and incoming quality management. Customer expectations on
timing--across both manufacturing and delivery--are better
managed through visibility into parts availability and ordering.
One important benefit to partners is the powerful set of
Great Plains forecasting tools, which allow the company
to rapidly address and respond to unexpected orders from
partners.
The Datasweep system guides the manufacturing process
beginning with pulling parts from inventory through final
test and packaging. It’s important to note that the
Datasweep system is tightly integrated with a comprehensive
bar-coding system, providing an automated quality check
system. Bar codes can be associated with detailed information
about the component such as vendor, version number and revision
number. Bar-coding eliminates many manual processes, avoiding
opportunities for human error and ensuring the highest levels
of quality and manufacturing control. The Datasweep system
is initiated when it receives a work order from Great Plains.
This work order includes a “pick list” of components
required to manufacture the appliance. By this time all
incoming components have been inspected and individually
bar-coded. Any unacceptable components have been segregated
in a locked cage to prevent contaminating the inventory.
At the technician’s workstation on the manufacturing
line, detailed work instructions are brought up for each
process that will be performed at that station. These work
instructions may be unique to each appliance. These work
instructions are under engineering-change order control
in the Agile system to update them to any last-minute instructions
or changes.
As the technician assembles the appliance, the bar code
of each component is scanned as it’s installed in
the appliance. The component is checked against the bill
of materials to ensure that the correct parts are being
used in the appliance. If an incorrect component is used,
the Datasweep system will alert the technician. Finally,
the Datasweep system ensures that all components are consumed
before the unit can proceed to the next workstation.
After assembly, each appliance is run through a series
of hardware tests. Throughout this automated test process,
data is collected and appended to the unit’s manufacturing
history. Any out-of-tolerance readings trigger the system
to e-mail technicians and managers with details regarding
the problem. This approach enables a small number of employees
to manage a high volume of units under test.
Once the unit has passed all hardware tests and a final
visual inspection, it moves to the disk-imaging area, where
the partner’s application is loaded. Agile Software
controls the disk image and ensures that the appliance receives
the most recent code revision. Depending on the requirements
of an appliance partner, the system may specify a “smoke
test” to confirm a good load of the disk image, or
it may require that license keys are entered.
The unit is then automatically directed to the pack-out
station, where it’s boxed with the appropriate manuals,
warning labels, instruction cards and backup CDs. All inserts
are scanned and checked against the protocol. Finally, Datasweep
informs Great Plains that the completed unit is ready, and
Great Plains supplies the ship-to information and schedules
invoicing.
The system is linked with all returns into the manufacturing
process for rework, repair or replacement. Any information
captured along this trail through the servicing of a product
is centralized in the Datasweep system and available for
root-cause analysis. Having repair and rework information
linked to unit-level parts and supplier detail helps Network
Appliances quickly and accurately provide customer responses
and determine the appropriate disposition and financial
effect of returned products.
All of the product and process information is stored in
a centralized collection of Oracle and SQL databases, with
Web tools providing online access and control over this
information. This enables Network Engines to see the status
of a pending order online. By accessing centralized information,
the company can obtain a real-time snapshot of how many
units are in assembly, how many units are in test, and how
many units are completed.
Business processes also provide a substantial benefit
to customer service. Once an appliance serial number is
entered, users immediately receive a detailed list of the
components used to manufacture that particular appliance.
This tool is a tremendous customer service advantage, providing
an immediate, detailed and complete summary of the hardware
and code level of each system. In a troubleshooting situation,
customer service technicians will know the manufacture date
of the appliance, as well as the exact configuration of
the unit down to the revision level of processors, memory,
chipset and lot number of each component.
Visibility and control along each step of the process--with
checks and enforcements--help improve product quality and
reliability. Using a system that automates quality processes
and best-in-class traceability helps the company reduce
costs inherent in error-prone manual systems. Integration
across product design, manufacturing and ERP helps improve
order accuracy and build detailed product genealogy for
faster tracking. The Web-based system provides speed of
production and real-time visibility into manufacturing activities,
supporting just-in-time inventory management. Product accountability
is ensured through detailed reporting, access and thorough
tracking of information from design to aftermarket service.
The flexibility of the system gives Network Engines the
ability to quickly adapt to changing customer demands--without
sacrificing quality.
Leo Cote is director of quality and manufacturing
operations at Network Engines. He has spent his career in
quality and manufacturing. Letters to the editor regarding
this article can be sent to letters@qualitydigest.com.
|