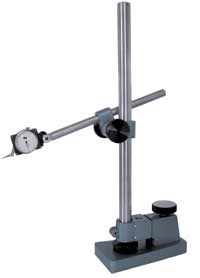
Dorsey's S4 Height Gage Stand
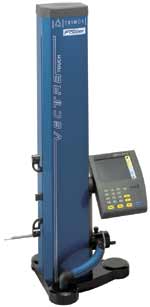
Fowler's Trimos Series Electronic
Height Gage
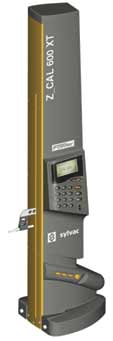
Fowler's Z-Cal Motorized Height
Gage
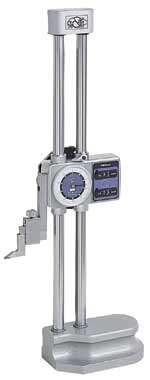
Mitytoyo's Digital Counter
Type Height Gage |
One of the most
common and widely used benchtop tools is the height gage.
You may think that their name says it all: Height gages
measure height, of course. But after a century of improvement,
height gages have emerged as highly versatile tools, able
to measure a great deal more than their name might suggest.
If you’re looking for something more capable than
calipers but not quite as complex as a coordinate measuring
machine, a height gage could be the perfect solution.
Height gages have been in existence since the turn of the
20th century, says Scott Robinson, from the technology services
department at The L.S. Starrett Co. Vernier-type calipers
were standard tools at that point. "It didn’t
take long before people said, ‘If we’ve got
a device to measure horizontally, maybe we ought to put
a base on it and stand it vertically to measure height,’"
Robinson explains.
The subsequent evolution of the height gage has remained
steady. In the years that followed their inception, Vernier
height gages became common tools. The trouble with Vernier
height gages, however, is that they rely on users’
skill. For many years, a typical accessory for a Vernier
height gage was a magnifying glass to assist the user in
determining which lines truly matched up.
During the 1970s, dial calipers began to emerge as "easier
to read" tools. Dial height gages quickly followed.
The dial height gage features a round-faced dial with an
arrow pointed toward graduations that indicate height. "It
was much faster and as accurate as the Vernier height gage,"
notes Robinson.
The mid-1980s were a time of technological growth, during
which the first electronic height gages emerged. Instead
of manually operating the gage and reading a dial indicator,
electronic reading tools, like touch-trigger probes, can
capture the exact measurement of a material and translate
it onto an LCD screen.
Although more advanced versions of height gages are repeatedly
being introduced to market, there’s still enough of
a need for the old-fashioned, straightforward Vernier and
dial height gages that they remain popular items in gage
manufacturers’ catalogs.
All height gages, whether manufactured in 1902 or 2002,
carry basically the same features. They all have a vertical
column, anywhere from 6 to 36 inches long (custom-made height
gages can extend even higher), attached to which is a unit
that slides up and down. An arm protrudes from the gage,
coming into direct contact with the material being measured.
Each height gage features a solid base, giving the vertical
column enough stability that it remains at a right angle
to the table’s surface. What separates one height
gage from another depends on the technology you add to these
basic features. Here are some different types of height
gages available:
• Vernier height gage. A height gage
with graduated scales featuring marks of measurement both
on the vertical column and on the arm. The graduations line
up to indicate the most accurate height. Adjustments are
made manually using a knob for precise positioning.
• Dial height gage. An analog-reading
height gage featuring a round dial attached to the slide.
The dial reads graduations of measurement, and the user
adjusts position manually.
• Digital dial height gage. Like
a dial height gage, but with a counter for more precise
measurement. For example, the counter will read to tenths
of an inch, and the dial will read to one-thousandths of
an inch.
• Electronic digital height gage.
A height gage featuring a digital display of measurements.
These units can also include features such as instant inch-to-millimeter
conversion, a hold option that temporarily saves your measurements
and the ability to set any position to zero.
In addition to the several types of height gages available,
there’s a wide variety of height gage accessories.
These include:
• Riser blocks. Precisely measured
blocks that increase the range of a height gage
• Scribers. Instruments attached
to the arm of the height gage that mark the material for
later machining
• Probes. Parts attached to the arm
that come into direct contact with the part being measured.
Measurement is triggered when the probe touches the part.
Probes of various shapes and sizes measure grooves, diameters,
bore centerlines and such.
• Granite surface plate. A primary
reference surface. Measurement with a height gage is typically
performed atop a granite surface plate. When purchasing
a height gage, it’s important to consider this additional
cost.
• Height gage software. If the height
gage is capable of direct output, consider purchasing accompanying
software to help track measurements.
According to industry experts, there’s no such thing
as a good height gage or a bad height gage. In fact, the
only way you could end up with a "bad" height
gage is if you choose the wrong one for your particular
need. Height gages can be used for the simplest of measurements,
from basic go/no-go applications to advanced mapping of
complex parts.
"Applications for height gages are numerous, from simple
step and height measurements to sophisticated 2-D applications
like diameters and bolt-hole patterns," notes Dennis
Traynor, vice president of sales and product support services
for Mitutoyo America Corp. "They’re ideal for
parts that have single or 2-D tolerancing and accuracy requirements."
A basic use for a height gage would be taking sample measurements
of manufactured parts to make sure they’re within
tolerances. For example, a maker of beverage containers
must make sure its cans are exactly 5 inches tall. If they’re
too tall or too short, they could jam in the chute of a
vending machine.
A step up from this simple use of a height gage would be
scribing material for later machining. For example, a machinist
needs to cut a 1-inch groove exactly 4 inches from the base
of a piece of steel. The machinist would take that piece
of steel to the height gage, measure exactly 4 inches from
the base, lock the mechanism in place and scratch a 1-inch
groove into the steel using a scriber. The material would
then be marked for later work.
An even more sophisticated use for a height gage is mapping
the parameters of a piece of equipment. For example, an
engine block manufacturer needs to know that its part is
accurate according to its blueprint. Once the engine block
is in position on the granite surface plate, an engineer
would use a height gage to determine the location, high
points and low points of bores, shafts, bearings and other
part features. This is often accomplished by performing
two-axis measurement with the height gage.
In order for a height gage to perform two-axis measurement,
the operator must measure a part in one axis and then rotate
the part 90 degrees and perform a second set of measurements
in the same sequence. Software programs have emerged that
enable an operator to input a part’s dimensions; the
software then calculates those dimensions and displays them
in 2-D.
With so many different types of height gages and even more
applications for them, a potential height gage buyer may
feel overwhelmed, not knowing where to start. Most experts
agree, however, that the most important consideration is
to determine exactly what you’ll be using your new
tool for. "There’s a number of things buyers
need to establish," says George Schuetz, director of
precision gages at Mahr Federal Inc. "How big is the
part? How skilled are the operators? Where in their facility
will the height gage be housed? How many different parts
do they want to measure? Once they’ve defined their
criteria for taking measurements and determined their budget,
buyers can then seek a height gage that matches those criteria."
• What accuracy can I expect?
• What is the repeatability of the
readings?
• How easy is this to use? How much
instruction will the operators need?
• Can the batteries be recharged,
or do I have to replace them? How often?
• How far away do I have to send
the height gage for repairs?
• How will the shop floor environment
affect the height gage’s readings?
• How adaptable is the height gage
to upgrades?
• What customer support does the
company offer?
Fred V. Fowler III, vice president of sales and marketing
at Fred V. Fowler Co., urges buyers to keep the operator
in mind when purchasing a new piece of equipment. "When
you have a height gage with more functions than you need,
people are going to gravitate away from it," he says.
"You’re going to be stuck with a $6,000 instrument
that nobody uses because everyone’s afraid to turn
it on." Instead, Fowler suggests the height gage should
contain four or five basic functions. "You can get
90 percent of what you need done with just the basic features
of a height gage," he says. "If you need more,
then that’s when you can start purchasing add-ons."
Schuetz stresses that the best height gages will have as
little operator influence as possible. "They should
have the capability of being motorized so that they always
test the part with the same force," he says. "Part
programming for repetitive operations is a must."
There are so many different types and sizes of height gages
that prices vary greatly. The simplest Vernier height gage
starts at about $50, but highly sophisticated models can
cost more than $10,000.
Custom-made height gages can carry even heftier price tags.
Don’t forget that purchasing a height gage may also
mean purchasing a granite surface plate, extra batteries,
gage blocks, special probes and software.
During an economic crunch, a height gage can serve as a
suitable alternative to a CMM. "As long as you have
time, modern height gages can measure just about any part
feature," notes Traynor. However, if you’re trying
to measure a part with full 3-D orientation, height gages’
limitations will become apparent. They aren’t capable
of measuring cylindrical or spherical objects, or anything
else within the 3-D range of measurement.
Still, buyers may want to weigh the pros and cons of using
a height gage as a temporary solution to their measuring
needs until the company’s economic future looks a
little brighter.
What’s next in the world of height gages? Customers
can expect better resolution in the scale and more features
built into the gaging processor or display portion, but
most believe its unlikely height gages will ever be replaced
by noncontact vision measurement equipment, says Schuetz.
"There will probably be some innovation in the way
they’re sealed against harsh environments, like dust
and moisture," adds Drew Koppelmann, product manager
of precision gages at Mahr Federal.
Fowler’s newer gages will feature direct Internet
connection capabilities. "By equipping the height gage
with a network interface chip, it can connect directly to
the shop floor network," explains Fowler. "It
looks just like a computer on your network, and you can
upload and download information from it, or you can update
software."
As for a more distant future, Fowler has a very different
take on where height gages are headed. "I think the
height gage will meet its end in years to come," he
says. "The entire field of dimensional measuring will
change significantly as far as what people expect from systems."
Fowler predicts that an all-in-one noncontact vision measuring
system will someday be developed, eliminating the need for
height gages altogether. However, he does note that this
innovation will only replace other measuring systems when
the price is right. "It comes down to an issue of getting
rid of all the hard gaging at a company and replacing it
with one fabulous machine," he says. "More than
likely, people will plug on like always until they can’t
afford not to switch."
Fowler’s sentiments aren’t shared by all, however.
"Height gages have definitely found a place in the
measurement field," argues Ted Luty, CEO of Dorsey
Metrology. "They’ve worked their way up the technology
tree, and I would guess that they’ll continue to thrive
well into the future."
Kennedy Smith is Quality Digest’s assistant editor.
Letters to the editor regarding this article can be sent
to letters@qualitydigest.com.
|