The
picture of the perfect factory is one that utilizes real-time
manufacturing intelligence to achieve optimized performance
and minimal unscheduled downtime. As market leaders, these
model plants are highly efficient, productive and profitable.
By implementing new technology strategies that yield real-time
manufacturing intelligence, manufacturers can achieve high
levels of optimization and overall equipment effectiveness.
A direct connection to machine controls is used to continuously
monitor, track, compare and analyze production parameters.
This enables manufacturers to uncover opportunities for
improvement and ensure that machines are operating within
defined specifications. Being able to view and analyze monitored
production parameters from anywhere, at any time, is what
provides real-time manufacturing intelligence.
Continuous control-system monitoring can save manufacturers
millions of dollars. The ability to monitor dozens of process
line parameters, such as temperature and line speed, and
alert plant staff to changing conditions can significantly
decrease downtime. Continuous monitoring gives remote engineers
a direct line of sight into process line activity, enabling
them to solve production problems quickly and perform predictive
and preventive maintenance. Real-time manufacturing intelligence
also enables manufacturers to focus on making process improvements
during scheduled downtime.
Although many organizations understand the theory of OEE
as a tool to maximize capacity, few have actually put it
into practice. Continuous control-system monitoring provides
an Internet-enabled OEE tool to monitor the efficiency and
manufacturing consistency of each piece of equipment. A
continuous control system monitoring service that facilitates
constant running of equipment at steady speeds ensures quality
and consistency of products.
Continuous control-system monitoring and data analysis improve
OEE over time through:
• Proactive 24/7/365 technical support and immediate
notification of process deviations
• Reductions in unplanned downtime
• Preventive maintenance
• Continuous process improvement and optimization
of machine speeds and material yield Most important, by
making accurate OEE numbers readily available, manufacturers
can better control machine performance.
Real-time manufacturing intelligence is aimed at turning
raw machine data into valuable information. This information
serves to optimize production and, ultimately, create a
more strategic business.
Data from the factory floor are vital to making informed
business decisions. With a remote monitoring and diagnostics
system, off-site support specialists can proactively support
plant operations and quickly identify potential problems
in the production process. Remote-engineering specialists
deliver this information to the manufacturer in the form
of detailed reports to facilitate ongoing process improvements.
This empowers the manufacturer or specialists with the knowledge
and means to gain a competitive advantage.
Once a problem is detected, it can often be corrected remotely
before a machine or process fails. This proactive approach
can significantly increase plant uptime, help focus internal
resources on business growth initiatives and provide a cost-savings
advantage over traditional reactive support programs that
address problems after they occur.
An "always on" connection over a high-speed data
communications network allows plant personnel, business
managers and off-site technical support specialists to monitor
production data around the clock to gain real-time manufacturing
intelligence.
The monitoring system and networks are also designed to
meet all of the corporate security requirements to prevent
intruders from disrupting operations on the factory floor.
Just as the information age fueled worldwide business growth,
real-time manufacturing intelligence is poised to transform
the way manufacturers do business.
Web-enabling process line functions using continuous monitoring
and data analysis services are highly effective in increasing
productivity and OEE. These services enable plant personnel,
business managers and off-site technical support specialists
to view and manage data directly from any Web-enabled PC.
This provides them with a comprehensive view of process
line activity that is unprecedented in scope, detail and
accessibility.
Outsourced manufacturing services utilize the expertise
and technology of a service provider to deliver a cost-effective
productivity solution to manufacturers. Given the right
combination of industry expertise, talent and technology,
a manufacturing service provider can significantly enhance
operational performance—often at a fraction of the
cost it would take to accomplish the same goals using in-house
technology and resources.
By establishing a direct connection to the manufacturer’s
machine controls, the service provider can deliver real-time
technical support and data analysis services to predict,
prevent and accelerate the resolution of equipment problems
from a remote location. In this way, the service provider
becomes an extension of the manufacturing organization.
Utilizing the expertise and resources of off-site engineering
specialists eliminates a significant capital investment
in the hardware, software and administrative staff needed
to support an internal solution.
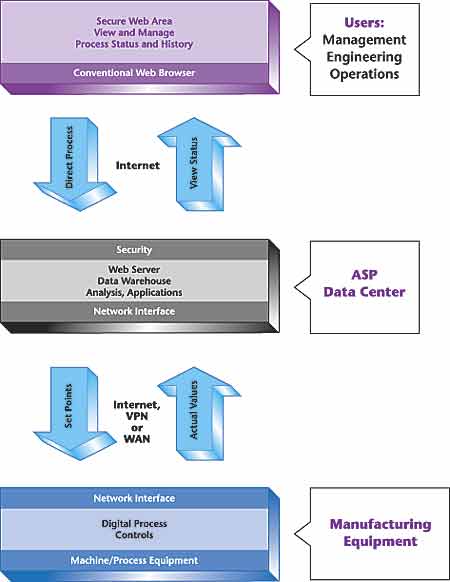
Outsourced services ensure the highest levels of security,
high-speed networking and fault-tolerant server capacity
to store and process data. Internally hosted software applications,
which provide fragmented and incomplete functionality—in
comparison to outsourced services, are only as reliable
as the manufacturer’s networking and computer systems.
As such, internal software applications are likely to go
down when other systems fail. This is the time when the
latest control system settings, current product recipes
and process line status are most vital to manufacturers.
By storing the manufacturer’s machine settings and
control programs at an off-site location, the service provider
can ensure software recovery in the event of a disaster,
system failure or drive replacement. This enables the manufacturer
to resume operations quickly and without any loss of data.
The outsourced service model is especially practical in
a harsh manufacturing environment, where delicate computer
equipment is at greater risk for damage.
Outsourcing control system monitoring and analysis is simply
more cost-effective, faster and easier to deploy than in-house
investments in technology and personnel.
Because downtime is one of the most costly conditions a
manufacturer can experience, a proactive technical support
program can generate significant cost savings. In order
to effectively diagnose problems and make process improvements,
it’s vital that remote engineers have a deep understanding
of the manufacturing industries in which their customers
specialize.
I
By leveraging real-time manufacturing intelligence acquired
through continuous control-system monitoring, remote-engineering
specialists have the insight to solve process line problems
more quickly, efficiently and effectively than traditional
technical support centers. Remote-engineering services are
designed to complement a manufacturer’s in-house capabilities,
or assist them with 24/7 technical support to help reduce
internal labor costs.
Continuous-monitoring services can also generate cost savings
by protecting existing investments. The direct high-speed
connection used for online monitoring provides a conduit
for regular backup of system software and machine settings.
This protects manufacturers against information loss due
to electrical failure, disaster or system lockup. Regular
backup of machine data also provides version control to
ensure that equipment is operating with the latest settings.
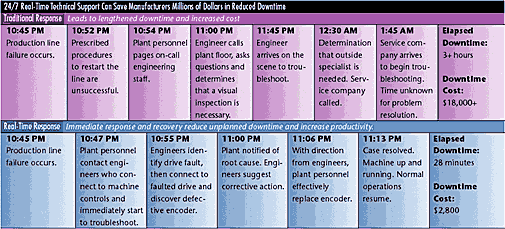
• Analysis tools. Process line monitoring and data
analysis are also used to identify optimum production benchmarks
and set thresholds for process variables. When any metric
that affects output quality falls outside "best case"
standards, plant staff are alerted.
Outsourced technical support staff also leverage monitored
parameters by providing insightful reports on how to reduce
costs, improve quality and enhance productivity.
• Historical database. By storing monitored machine
parameters and reporting support cases to a central database,
plant managers and remote engineers can cross-reference
current process line data with past activity to more quickly
identify and solve problems.
• Automating traditional manual processes. Continuous
monitoring and data analysis services can also be used to
incorporate traditional manual processes, such as quality
assurance testing, into an Internet-enabled centralized
data repository. This augments process line problem resolution
and maximizes production uptime.
Every manufacturing company is different. Some are big.
Some are small. Some have process experts on staff. Some
don’t. Some need help in a few specific areas of production.
Others need help in many areas of production. Fortunately,
because outsourced services are cost-effective and flexible,
they provide the best solution for any manufacturer.
Continuous monitoring and data analysis of process line
activity, coupled with remote 24/7 engineering support,
can help manufacturers realize optimized production. These
services bring manufacturing operations in closer alignment
with corporate headquarters, to ensure that business plans
are in step with the needs and goals of the plant, and vice
versa. They also pave the way for the future integration
of enterprise applications that synchronize manufacturing
operations with customers and suppliers. This holds great
potential to accelerate and enhance the entire manufacturing
process from raw material to finished product.
Brett Smith is co-founder ei3 Corp., which specializes in
using the Internet as a vehicle to help manufacturers improve
productivity. Prior to the launch of ei3, Smith served on
the restructuring team for Delta V Technologies, an industrial
engineering subsidiary of Presstek Inc. Letters to the editor
regarding this article can be e-mailed to letters@qualitydigest.com.
Copyright 2002 ISA—The Instrumentation, Systems and
Automation Society. All rights reserved. Used with permission
of ISA. This paper will be presented at the ISA 2002 Emerging
Technology Conference, Oct. 21–24, 2002, in Chicago.
|