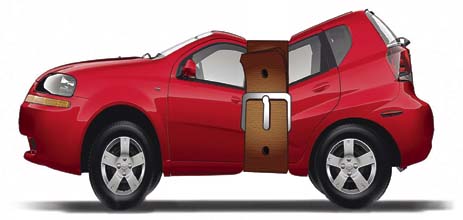
Can Lean Save the Automotive Industry?
An unsettling 38 percent of U.S. automotive suppliers are in fiscal danger, according to a recently released report.
The findings are derived from AlixPartners' "Automotive Vehicle Industry Review and Outlook" study, which also found that another 24 percent of worldwide automotive suppliers face the same fiscal danger, unless they take "urgent, counteractive measures." This observation comes on the heels of $60 billion in major supplier bankruptcies in the United States alone since 2001.
The study examined 104 automotive suppliers, 22 automakers, 18 heavy-vehicle producers and 32 automotive conglomerates worldwide, and measured and compared them across a wide range of financial and operating metrics. Among the more startling findings in the survey are indications of a pronounced divergence between top-performing OEMs and suppliers, and those in the lowest-performing quartile.
Furthermore, the $72 billion Chinese components market--which has been considered a cash cow for years--has fragmented to such a degree that, according to the study, "a big shake-up is most likely brewing [in China]."
Although this poses a potential opportunity for Western suppliers, market conditions indicate an oversupply of Chinese goods. For the first time, China was a net exporter of vehicles in 2005. Overinvestment has led to lower profitability and massive price cutting for most OEMs.
"The gold rush in China is officially over, as least as far as easy profits goes," says John Hoffecker, AlixPartners managing director. "Even though we forecast that 34 percent of the global auto industry's growth by 2010 will come from China, our analysis tells us that the many automakers there are headed toward a major reckoning, as we predict that capacity utilization will level off at the current low levels, in the neighborhood of just 50 percent, and that today's price-cutting trend will continue. And, of course, that's a double-whammy for Western suppliers and OEMs alike, as that overcapacity will put even more pressure on China to export. That's certainly not good news at a time when the inflation-adjusted price of a new car in the United States over the last decade is on the same downward curve as the price of apparel."
The study also notes that many of the disconcerting trends in the worldwide automotive industry are regional in nature. Fully 21 of the top 25 suppliers as measured by total value creation in the past two years are Asian, while 15 of the 25 suppliers at the bottom of that list are North American. Additionally, U.S. suppliers are trailing far behind their Asian and European counterparts in investment in research and development, a critical element in developing innovative products for future returns. All this points to a need for automakers and automotive suppliers to do better.
"Increasing globalization is the number-one key driver forcing the need for increased efficiencies in auto markets all around the world," says Hoffecker. "But, compared with other industries, not to mention compared to where they certainly are going to have to be long term, suppliers and automakers alike are mostly just in the beginning to middle stages of this race. Some suppliers and OEMs have turned in very impressive performances so far, but the performance of many companies remains spotty in terms of organization, process and, especially, execution."
Citing the research, Pelion Systems, a company that provides manufacturing process optimization solutions, will host an executive roundtable event titled "Lean Forward: Exploring a New Operational Performance Standard for the Automotive Industry," to be held Sept. 28 at the Lean Learning Center in Novi, Michigan. The event will conclude with a debate on whether standards should be established to accelerate the adoption of lean principles by automotive suppliers. The outcomes of the discussion may form the basis of a business case to be submitted to the Automotive Industry Action Group.
Jamie Flinchbaugh, founder of the Lean Learning Center and co-author of The Hitchhikers Guide to Lean (Society of Manufacturing Engineers, 2005), and Bob Djuvoric, DNV Certification director of North American automotive services, will lead the day's discussions.
For more information, visit www.pelionsystems.com/resources/reg_ seminar.html or www.alixpartners.com.
Do the Math!
Have you ever been reading the paper, watching television or listening to the radio and suddenly been stopped in your tracks by improbable statistics, outrageous numbers or equations that just don't add up? Here's the place to tell us about it.
We want to hear all about math murders and arithmetic arrhythmia. The rules: Your example must be a reasonably obvious error, misuse or misunderstanding. Please, no disputed interpretations of statistical analyses. Just provide a copy of the newspaper or magazine article via fax, (530) 893-0395, or e-mail, comments@qualitydigest.com . If it was something you heard on broadcast media, we must have a link to the show, or the date, time and name of the broadcast to verify your number abuse.
We'll start you off with a mild example of what we mean.
This comes from National Public Radio's Talk of the Nation , Science Friday, July 21, 2006, "Controversy Over Wind Power." The discussion is about the use of wind power as a source of alternative energy. During the call-in section, a retired utility worker makes the point that while wind energy may be nonpolluting, it isn't as cost-effective as traditional sources (18:20 into the podcast).
He says, "In a typical coal-fired power plant, it costs about $25 a megawatt to produce power, but the quoted figures for wind energy is closer to $75 a megawatt…. To the rate payers as a whole, wind power is a relatively expensive situation."
The following response to this comment comes from Laurie Jodziewicz, communications and policy specialist for the American Wind Energy Association in Washington, D.C.:
"Wind energy is actually competitive with other sources of… fossil fuel sorts of electricity…. It's in a competitive range. It depends on the site, but it's about [laughter in background] three to seven cents per kilowatt hour, which I don't think is quite what the gentleman mentioned."
Really?
Do the math!
Lean, Mean Military Machine
Several U.S. Army divisions stationed in Korea recently graduated their first class of lean Six Sigma Black Belts, and more training is underway.
The U.S. military has made process improvement through lean, Six Sigma and theory of constraints (TOC) a major focus in recent years. The Navy has initiated an extensive lean Six Sigma effort, run by a centralized office called NAVAIR, that is charged with improving everything from aircraft maintenance to the delivery of food and supplies to deployed divisions. The Army's Headquarters Materiel Command leads its lean Six Sigma effort and has, so far, trained hundreds of uniformed and civilian employees in the methodology. In June, it established a formal "school" to centralize its training programs and currently has 213 Green Belt candidates and 105 Black Belt candidates. Once trained, they will be charged with improving the organization in such critical areas as reset, repair, manufacturing and administration.
"Lean Six Sigma empowers people and helps them see the possibilities," says Francis J. Harvey, secretary of the Army. "People learn they can document processes that haven't been documented, quantify work activities that haven't been quantified and measure results that haven't been measured. They also learn it's OK to challenge assumptions and think creatively about how to get work done more efficiently."
The U.S. Navy was the first branch of the military to implement widespread lean and quality improvement programs. It launched Task Force Lean in 2004, which supports the NAVSEA command structure, and established a lean office, which is staffed full time. Earlier this year, the Navy teamed with the American Society for Quality to develop its Lean Six Sigma Black Belt certification. Forty-four Navy officers and employees recently earned the new certification, and 750-800 more Navy personnel are working toward certification. Navy leaders in Washington, D.C., recently announced a new requirement that its commanding officers, executive officers, department heads, command master chiefs and senior enlisted advisors must complete lean Six Sigma and TOC training, noting that it will probably extend the requirement to other personnel as well.
This year, according to military newspaper Stars and Stripes , the Army reports it has spent about $300,000 on a four-month training session for its soldiers and civilian employees in an effort to revamp various procedures, including tank maintenance, accounting and waste reduction. One of its South Korean units reduced the time it takes to overhaul an M-1 tank from 105 days to just 30. In addition, the Army estimates that it will save $11.9 million in Patriot missile maintenance, and that it reduced the length of the mechanics line needed to work on Humvees from 1,100 ft to 500 ft.
The Army will soon apply lean Six Sigma concepts to its Installation Management Agency, which currently has a budgetary shortfall of $500 million.
For more information, visit www.amc.army.mil/lean/page.aspx?id=0.
No Harm, No Foul
ISO 9001 registration is a cutthroat business. Taking advantage of a mixup, an unnamed registrar turned in a competitor for using the ANSI-ASQ National Accreditation Board (ANAB) logo on several of the ISO 9001 certificates it recently issued to clients. Rick Breden, president of Verisys Registrars, says the mistake was inadvertent, and stemmed from a staff member's confusion over the relationship between ANAB and RABQSA. The use of the logo on the certificates was intended to demonstrate the issuing auditor's certification, instead of implying Verisys' accreditation, says Breden. Verisys is accredited by the International Accreditation Board.
ANAB took over accreditation duties from the former Registrar Accreditation Board about 18 months ago, when RAB merged with QSA International to become RABQSA. RABQSA performs auditor certifications, while ANAB issues certification-body accreditations. ANAB and RABQSA are not affiliated in any way.
"It was completely inadvertent," says Breden. "We had someone on staff who was a little more confused about the relationship between RABQSA and ANAB than they should have been, and this is what happened. We reissued the certificates, and the problem is solved."
Bob King, ANAB president, reports that it was notified of the issue by another registrar in July. ANAB gets several complaints about unauthorized uses of its logo per year, and most of them are honest mistakes.
"I don't think this was malicious in any way," King says. "Sometimes we get complaints where the registrar is trying to get away with something, but that's mostly the exception to the rule. This appears to be an honest error, and they corrected it right away."
For more information, visit www.verisysregistrars.com or www.anab.org.
Six Sigma Cures Hospital's Error Problems
The implementation of Six Sigma at an Illinois hospital has saved it millions of dollars--and simultaneously dramatically improved patient satisfaction.
Decatur Memorial Hospital reports that 10 months after it installed patient-safety technology from Omnicell Inc., it was more than $2 million under budget in its drug department and $750,000 under budget for pharmacy labor.
Decatur's team used a Six Sigma approach to analyze the hospital's medication-use process, and then looked for automation approaches to help streamline the process. The team identified 132 steps in the hospital's patient drug-delivery system; 42 were eliminated through subsequent automation projects. In addition, the hospital reduced the time it takes to dispense and administer drugs to patients from 186 minutes to 104 minutes.
"Medication errors have dropped 70 percent, with very few of the more serious med errors," says Ron Wolschlag, director of the hospital's pharmacy. "Our nurses are much happier with the new system because it makes them much more efficient and gives them more time for patient care."
Decatur Memorial Hospital is located in central Illinois and has 350 beds. For more information, visit www.dmhcares.com.
Help Us Celebrate Our Anniversary
We at Quality Digest are preparing to celebrate our 25th anniversary in the November issue. This special edition will include a retrospective on the last quarter-century of quality.
We're asking for your help in compiling this issue. In your opinion, what methodologies and/or systems have had the greatest effect on the quality industry since the early 1980s? What "next big thing" flopped? Who are the visionaries who have emerged? Whose vision turned out to be less than 20/20? What's made your job easier? Harder?
Your thoughts on how we've done over the years would be appreciated as well. What articles or columns from our history really stand out in your mind? Where did we hit the mark? Where did we fall short?
Finally, whip out your crystal ball and tell us what you predict for the next 25 years. Who knows, in 2031 we might be digging up your comments and marveling at your prescience!
Send your comments to comments@qualitydigest.com. Thanks for 25 years of support.
ISO Survey Finds Dramatic Registration Increases
The International Organization for Standardization reports an 18-percent increase in the number of international registrations issued for ISO 9001 in the annual "ISO Survey of Certifications."
The survey is ISO's main barometer for measuring international use and compliance with its standards. It reports that as of December 2005, there were 776,608 organizations in 161 countries registered to ISO 9001, an 18-percent increase over 2004. ISO 14001 has also seen tremendous growth. The survey reports a 24-percent increase in the number of registered organizations--111,162 in 138 countries. In 2004, there were 89,937 registered organizations in 127 countries.
The largest gains in the survey were for organizations registered to ISO/TS 16949 and ISO 13485. ISO reports that as of the end of 2005, there were 17,047 organizations registered to ISO/TS 16949, an increase of 70 percent over 2004. Even more striking is the growth of ISO 13485; the survey found 5,065 ISO 13485-registered organizations in 67 countries, a 111-percent increase over 2004, when there were 2,403 registered organizations in 55 countries.
ISO surmises that increased registrations in China and India are largely responsible for the trends. Additionally, the survey indicates the increasing popularity of ISO 9001 and ISO 14001 with service organizations. Nearly 33 percent of ISO 9001 and 31 percent of ISO 14001 registrations went to organizations in the service sector.
For more information, visit www.iso.org.
Quality New Mexico to Host Baldrige Conference
The Baldrige National Quality Program recently announced that Quality New Mexico will host the Western Baldrige Regional Conference this fall.
The conference and preconference workshops will be held Oct. 4-5 at the Hotel Albuquerque Old Town. The conference will feature speakers and workshop presentations from the 2005 Baldrige Award recipients: Sunny Fresh Foods Inc., DynMcDermott Petroleum Operations, Park Place Lexus, Jenks Public Schools, Richland College and Bronson Methodist Hospital. It will also feature former Baldrige Award recipients.
A preconference workshop, scheduled for Oct. 4, will focus on the basics of the Baldrige program for those who are new to it. The workshop is not a prerequisite to the conference, and is available with or without a full conference registration.
Quality New Mexico is the administrator of the New Mexico Quality Awards program. For more information, visit www.qualitynewmexico.org.
Quality Profile
Vicky Wachendorf, quality assurance manager for Metaldyne Inc. of Ply-mouth, Michigan, won an iPod from Quality Digest for her participation in our annual reader survey. Metaldyne is a designer and supplier of engines, drivelines and chassis, and employs nearly 7,500 people in 45 facilities in 14 countries.
What's the first thing you do when you get to the office in the morning?
Vicky Wachendorf: Check e-mail to see if there are any issues or questions from our Japanese office and customers. Then I walk the floor prior to attending the production meeting to get an idea of how things are running and to look for any issues that I need to bring up.
With all the portable inspection gadgets on the market these days, how important is first-person shop-floor inspection to you?
VW: We depend on technology and also do a little old-style auditing in the plant. The operator who runs the part is responsible for the quality of the part, and most take this seriously.
How often do you walk the shop floor?
VW: Depending on the day, there are times I am on the floor all day, especially if we are having issues or launching a new product. Other days, I may only make it out at the start and end of the day. I walk the floor right before I leave to verify that everything is running smoothly.
How important is continuing education to your job?
VW: It is critical to the job. Our company runs an online "university" with classes offered continuously. |