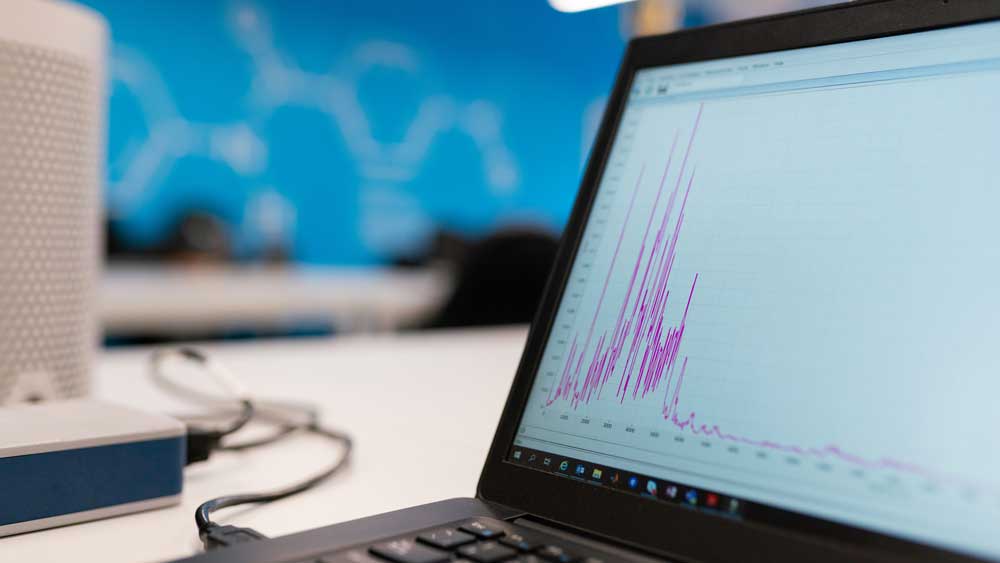
Photo by ThisisEngineering on Unsplash
In regulated industries like pharmaceuticals, medical devices, and food manufacturing, compliance is crucial for operational excellence. A validated quality management system (QMS) is key to maintaining this compliance. Let’s explore how QMS software streamlines validation and ensures regulatory compliance.
ADVERTISEMENT |
Understanding compliance validation in QMS
Compliance validation is a key process in quality assurance that checks whether your QMS software works as it should and meets necessary regulatory standards. In highly regulated industries, such as those overseen by organizations like the FDA, ISO, and EU MDR, validation ensures that products are safe, effective, and of high quality. This article covers what compliance validation is, why it’s done, and why it matters.
Regulatory requirements for QMS software validation
Navigating regulatory requirements can be complex, but understanding them is crucial for compliance.
…
Add new comment