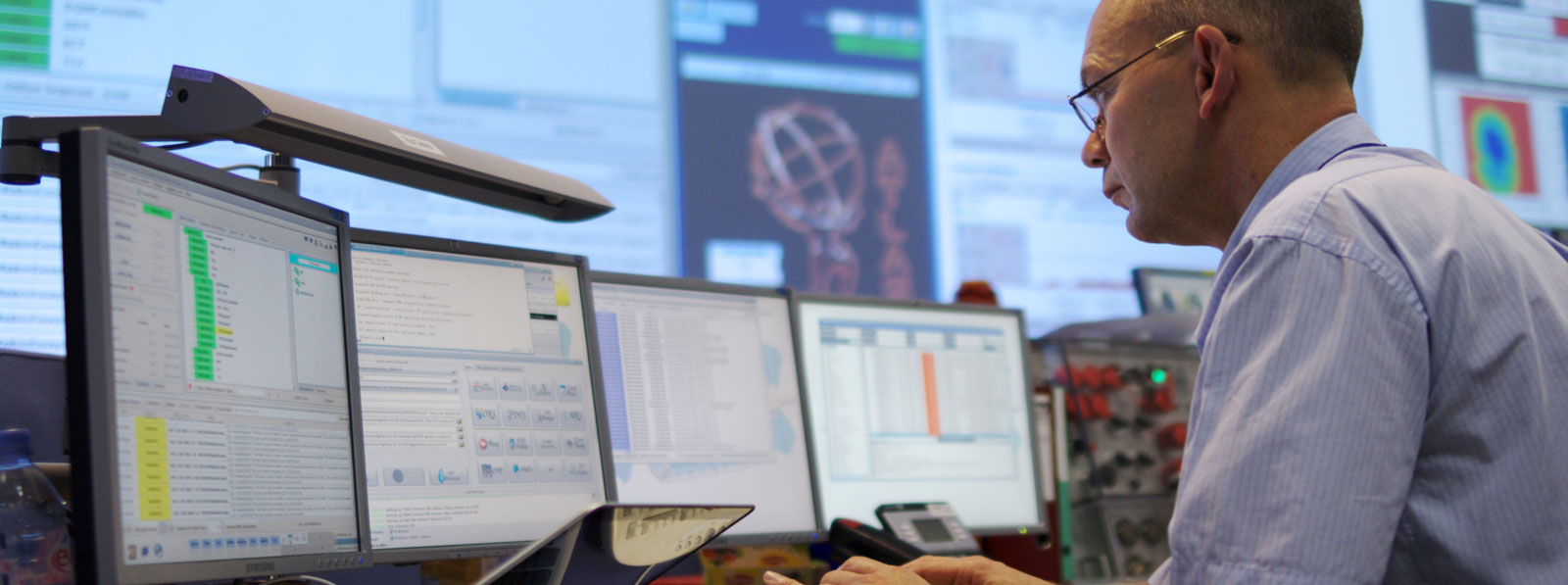
Even in the midst of the pandemic, product safety and quality remain critical. For many manufacturers, complex quality management systems and procedures stand in the way of agile responses and effective operational optimization. Cloud technology provides the means to dramatically simplify quality management.
If you’re like many quality pros and manufacturing leaders right now, you’re working crazy hours, possibly on a different schedule or from a remote location. You’re struggling to find new ways to get the data that operators are collecting on the plant floor and support workers as they adapt to rapidly changing demands. You’re also likely scrambling to coordinate with your plant managers and create custom reports for your executive teams.
It’s a challenging time, and if you’re lucky, you’re keeping on top of the unique demands this time has put on you. But even in the middle of this sprint, product safety and quality remain paramount.
During the current crisis, you may be intensely aware of how complex quality management can be, especially when you’re:
• Collecting much of your data manually
• Storing quality data in multiple systems and locations
• Analyzing information and compiling reports from hundreds of sources
• Needing access to critical operational and quality data when not on the plant floor—or off site
With too much information in too many formats, it’s hard to know where to focus your attention.
Fortunately, modern data analytics solutions are available to help you. Let’s take a look at some ways that technology can help—right now—and make your life easier going forward.
Reduce the complexity of quality management
Quality and operational data are at the heart of all your operations, and making that information accessible, understandable, and actionable is essential for optimizing every level of your manufacturing organization.
Legacy quality management systems and procedures that rely heavily on manual data collection and spreadsheet-based data manipulation create deep layers of complexity across the manufacturing plants. Modern, cloud-based quality management software platforms starts by standardizing all your quality data and putting them into one centralized database. With centralized data access, you suddenly have the ability to see and analyze data in real time and take meaningful action—quickly.
Here are five ways that a cloud-based, centralized quality management solution can reduce complexity in your organization.
Automate data collection
Handwritten, paper-based records can be inaccurate and are time-consuming to record and analyze. By implementing automated or semiautomated data collection, you can improve data accuracy and increase the efficiency of plant-floor operators. Automating notifications for timed data collections helps operators ensure that checks happen on time. And automated alerts provide timely reminders, allowing operators to maintain their focus on critically important tasks.
Make data actionable on the plant floor
Role-based dashboards are one of the most useful tools in modern software. Dashboards can be easily configured for each role and even each user on the plant floor. A dashboard can then present information and actionable insights that are directly relevant to that user—empowering operators to take proactive steps to stay on top of quality at a granular level.
Streamline analytics
Analyzing data that reside in multiple sources is time-consuming and complicated, if at all viable. In many organizations, quality professionals and plant managers are spending up to one-third of their week just collating and preparing data to discover what’s happening. If that’s you, you know how painful it can be to discover a truly significant issue hours, days, or weeks after it’s happened.
Modern data analytics software still leverages the proven power of statistical process control (SPC), and it does so behind the scenes, automatically and instantly. Instead of spending time making charts, you can open a dashboard and see the important information that those charts reveal—right now, when you actually need it.
Standardize operations and best practices
Siloed operations create inconsistent data and procedures across lines and plants, and make it impossible to ensure best practices are being applied the same way at every location. A single source for data also becomes a single source of truth, enabling plant managers and executive leaders to discover issues and dive in to find the root causes.
Even better, you can see which lines and plants are excelling at quality and why. Then you can use your dashboards to standardize those best practices for every line and every plant across the enterprise.
Prioritize quality improvement initiatives
One of the greatest areas of complexity lies in not just maintaining quality but also ensuring continuous improvement over time. Often, quality, process, and product improvement initiatives take a back seat to daily operations simply because such projects are complex or time-consuming. Out of all the possible improvements you can make, how do you decide which are most important? And how do you know an initiative will deliver a solid ROI?
This is where cloud-based analytics really shine. With easy-to-interpret visual reporting, a quality intelligence platform helps you go from “just managing quality” to optimizing your entire manufacturing business.
Reduce complexity to achieve manufacturing agility
For most manufacturers, legacy quality management systems have grown increasingly complex over time. That complexity has grown incrementally so that to a great degree, organizations just accept it because it’s “the way we do it.”
Complexity doesn’t have to be a cost of doing business anymore. When you leverage modern software solutions in a platform that is purpose-built for manufacturing quality and operational optimization, the improvements are dramatic—even transformational.
To get started, begin with a focused proof of concept. Implement the solution on a single line, with a single goal. The exercise can happen very quickly and will give your teams the chance to understand the software, see it work, and embrace the change. It will also establish the configuration elements you need to rapidly roll out the solution across lines and plants throughout your organization.
When you simplify quality management, you simplify all of your operations. That makes you more agile—and more resilient now and in the future.
At InfinityQS, we understand that we all face some challenging and tumultuous times ahead. But we face them together. For the days and weeks to come, we wish all our manufacturing colleagues the very best. Feel free to visit our website to learn more about how our software solutions can help your organization in immediate and practical ways. Stay safe—and let us know how we can help you.
Add new comment