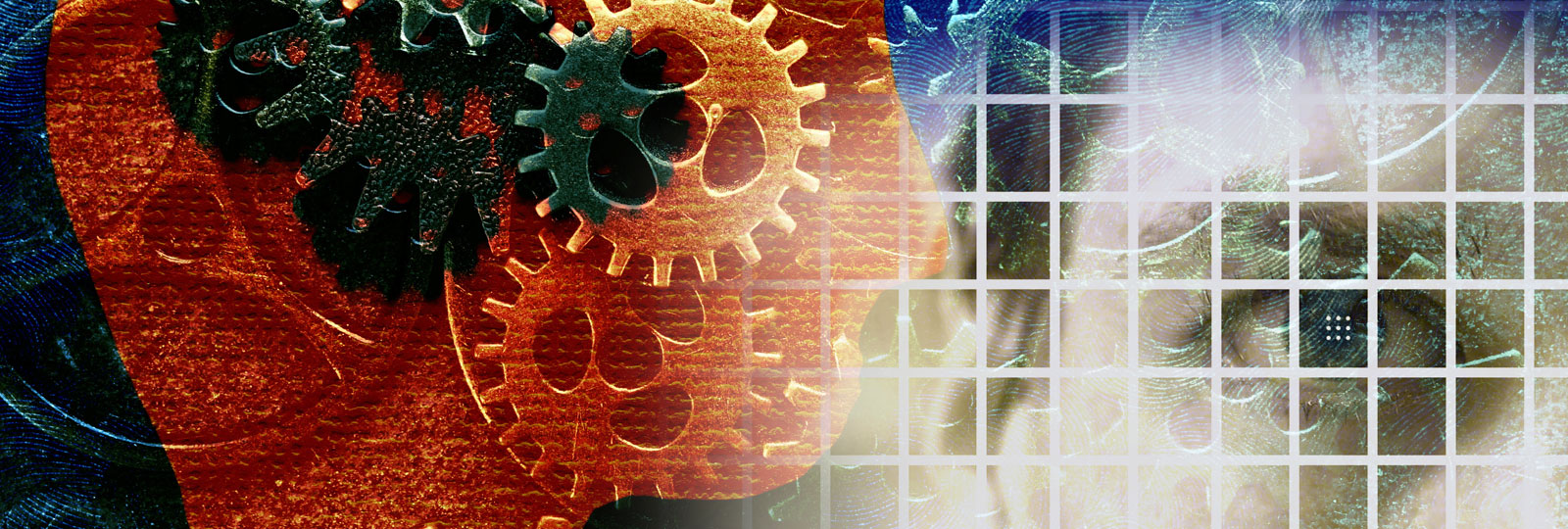
Every company wants to succeed, but not all can say they meet the current requirements to do that. More than a focus on capital, business plans, or staff, a successful business in 2022 must operate digitally. Yet for the 45 percent of small and medium-sized businesses (SMBs) that still rely on paper to function, the digital transformation is easier said than done.
For these companies, the issue isn’t complacency. Many might not have the manpower or financial resources to take on digital transformation and all it entails. Their data may be scattered among a mishmash of paper, Excel and Word files, or even legacy enterprise resource planning (ERP) systems. Most likely, they have no idea how to begin a paperless initiative while still using those critical documents daily. Even on a good day, the path toward a digital solution seems overwhelming. On a bad day, it’s impossible.
And that doesn’t even begin to address digital’s big brother: AI. Unfortunately, oversaturation of artificial intelligence (AI) in media and advertising has numbed the average manager to the very real impact AI can have on almost every aspect of industry, from real-time interpreting of shop-floor data to customer service interactions. AI promises to reduce a lot of the analysis lag imposed by the huge amount of data that businesses collect today and turn those data into information to help us improve our processes. This includes using AI within an electronic quality management system (EQMS).
Where are you now?
Most major EQMS software developers have integrated AI into their software. However, talking about AI within an EQMS is putting the cart before the horse for most companies, the majority of which still handle their quality management system (QMS) documents and procedures using paper, Excel, or home-brew QMS solutions. According to a recent survey conducted by Dot Compliance, only 22 percent of businesses use a cloud-based QMS solution. More than half use either Excel (27%) or paper-based systems (26%). The first step for these companies is to digitize their QMS, before considering AI.
A quick look at two of the most-used in-house QMS solutions shows why a move to an EQMS is critical.
First there’s paper. The downside of paper-based systems is obvious to those who use them:
• Manual data entry
• Data entry errors
• Entering exactly the same information into multiple documents
• Routing documents for signatures
• Storage requirements that consider security, environment, and space
• Misfiled or destroyed documents
Next there’s Excel. While it’s true that Excel is better than paper—almost everyone has it—it isn’t ideal. Using Excel for quality management is a laborious process. It requires manually downloading or importing raw data from your system, cutting and pasting data into the right format across different files, updating formulas and links, and so forth. Forget about multiple users trying to edit spreadsheets at the same time.
All of these issues can lead to delays in the reporting that’s critical to properly maintaining a QMS. And of course, you still have human error due to manual data entry, which leads to inaccurate data analysis, which in turn hinders your ability to make effective decisions.
The biggest problem with Excel, or any general-purpose data-handling application, is that they simply aren’t designed with a QMS in mind.
Advantages of EQMS software
According to marketing research firm Wakefield Research and data analysts Elastic, more than half of office professionals spend more time searching for documents than they do working—a fact that quality professionals can confirm.
QMS documentation, corrective action reports, training records, procedures, and audit findings are likely scattered among paper and electronic filing systems throughout the company. However, any major EQMS software is designed to deal with QMS requirements, including maintaining all the required records in an easy-to-access application. This allows third-party auditors to confirm that you are meeting those requirements.
The following are just a few of the many advantages of a cloud-based EQMS:
Access to data: Particularly with a cloud-based EQMS, data are accessible to anyone, including auditors, at any time from anywhere. Coupled with access control, data can be filtered so that only data relevant to an employee or supplier can be viewed by them. Most EQMS software will run on mobile devices, further improving data access. This accessibility speeds reporting and, ultimately, issue resolution.
Track improvement: Metrics at your fingertips let you quickly see if your improvement initiatives are working. For FDA-regulated industries, this might include lot acceptance rates, product-quality complaint rates, or invalidated out-of-specification rates.
Data integrity: This refers to data accuracy, completeness, consistency, and validity. Anyone who has ever worked with paper or other free-form data collection knows that maintaining data integrity can be a huge problem. A lack of data integrity makes it difficult to track problems or identify trends. Along those lines, a couple of good articles worth reading are “Citical Data Elements and Data Quality” and “Is Data Quality the Same As Data Accuracy?” To address these issues, EQMS systems use standard forms, standard terminology, and prefilled dropdown fields to increase the accuracy and speed of data entry.
Better workflows: Along with consistency comes better workflows. Clear and efficient workflows that include alerts and reminders, electronic signatures from any device, direct connection to training along with read-and-understand (R&U) approvals, and an efficient reporting system can save users between 30 and 40 percent more time than in-house on-paper solutions. Workflows also include signature routing. Even the most basic EQMS requires that corrective and preventive actions, for instance, be logged and routed to appropriate personnel for review. EQMS software can be configured to handle this automatically by following predefined routing rules.
Employee motivation: Although employee motivation is hard to quantify, none of us like spending our time on unnecessary tasks. Duplicating work, running around to get signatures, and searching for documents is not only wasteful but also demotivating. Quality personnel would rather spend their time addressing the root causes of quality issues.
Regulatory compliance: An EQMS makes it easier to meet regulatory requirements. Within the life sciences or medical device industry, this would include government regulations on electronic records and electronic signatures, such as the FDA’s 21 CFR Part 11 and the EU’s analogous Annex 11. The same holds true for those who need to show compliance to medical-device QMS standards such as ISO 13485.
Data security, extensibility, and maintenance: A cloud-based EQMS frees your IT department (assuming you have one) from having to constantly apply security patches, updates, and other maintenance-oriented tasks. This includes adding new functions and rolling those out to multiple sites. A cloud-based EQMS vendor handles all of that for you. Patches and updates are pushed out to the cloud servers and are immediately available to all users.
A tedious but necessary step
The move from your current system to an EQMS doesn’t have to be overwhelming. But you do need to take some steps for it to be successful.
If you are using a paper-based system, the migration to an EQMS is going to be tedious and yes, even painful. It means manual data entry. But don’t let this stop you; The benefits of all that data entry will be immediately obvious once finished, so grit your teeth and get it done. In today’s digital business environment, paper-based systems are slowing you down compared to your digitalized competitors. Quick access to data means quicker decision making.
For those of you using Excel or some other form of electronic data management, take heart. One advantage is that you have already gone through the process of putting some structure to your data—something that is missing in many paper-based systems. You have likely identified all of your QMS master data, such as all the data associated with customers, products, sites, and suppliers. In Excel, you probably created a separate column for each of these.
As long as you can export your data from Excel or another spreadsheet/database program, it is relatively straightforward for an EQMS software vendor to then import those data into the EQMS system. Master data, once imported into an EQMS, give you a platform on which you can now build a proper EQMS system and gain all the benefits.
There are some basic steps needed before migrating your data to an EQMS, regardless of which vendor you choose.
• Create a master document list. This includes all paper and electronic versions.
• Define workflows that are critical to your business. These workflows would include how you handle controlled documents, CAPAs, deviations, investigations, complaints, and supplier issues.
• Identify system users and user roles as well as your system administrator.
• Determine how employee training will be handled.
If you operate within an FDA-regulated industry, you will also need to consider how a vendor’s EQMS software will be validated. Does it come fully validated or will you need to conduct the validation yourself?
Next stop: AI
Once you have implemented your EQMS, you are ready for the next step, if you want to take it: implementing AI.
But first, what is AI and what does it do?
Simply put, AI systems examine large amounts data, looking for patterns that would be impossible for humans to spot in a timely manner—or at all, in some cases.
For example, a production camera connected to an AI processor looking at a pill-packaging station can be taught what constitutes a flaw or doesn’t. The AI doesn’t need to be trained on every type of flaw that exists. After a certain number of training images, the AI recognizes patterns in the flaw examples and can extrapolate to find flaws it was never trained to catch. In human terms, it can deduce from previous examples what humans consider to be a flaw.
A subset of AI is natural language processing (NLP). With NLP, a computer is able to examine the contents of text or even spoken language, including their contextual nuances. Then, in much the same way as the image-recognition example above, it can look for patterns and extract useful information to help with identifying issues that previously would have been hidden.
This idea extends to any kind of data. In the case of a QMS system, imagine that an AI with NLP could scan through text descriptions of failures, complaints, corrective actions, and audit results, and find relevant trends and patterns. An AI-powered QMS can look at textual or spoken complaints and, using NLP, quickly see correlations that a human might miss and flag administrators if an unusual trend occurs.
For example, think of how many ways people might describe a complex problem when talking to a customer service representative: “It’s broken,” “It doesn’t work,” “Tab A didn’t fit into slot B.” Do those different descriptions point to the same problem, or even the same cause? AI could help identify commonalities.
Historically, life sciences have faced significant challenges, from mountains of data and inefficient, complex processes to rigorous compliance expectations. AI offers important benefits to that sector. Some of these benefits will be discussed in the upcoming webinar “The Digital Quality Transformation Journey: From Paper to AI” on Oct. 12, 2022, at 11:00 a.m. Pacific. Benefits include proactive and predictive quality and using NLP to identify risks buried in communications between a complainant and a manufacturer. Much of AI’s value will result from its integration with Industry 4.0 technology: access to IoT sensors, machine and software outputs, and even live camera data.
In today’s increasing digital workspace, with quality systems collecting more and more data, industry needs AI. Without it, too many opportunities for improvement are left on the table, and worse, potential risks will be overlooked.
If you haven’t converted from a paper or Excel-based QMS to an EQMS, you need to get started. Paper-based systems, and software that isn’t designed with QMS in mind are holding you back. Efficiencies in handling all aspects of your QMS (and any associated audits) will quickly pay for the cost of data-migration. Once you have implemented an EQMS, AI is the next option, and a logical one. The benefits of AI are more than hype and can revolutionize many manufacturing and customer-service processes. If you already have a cloud-based EQMS, now might be the time to contact your vendor and see if AI capabilities are available. If you don’t have an EQMS, you should move quickly and establish one.
For a deeper dive in transtioning into an EQMS and AI register for the upcoming webinar “The Digital Quality Transformation Journey: From Paper to AI” on Oct. 12, 2022, at 11:00 a.m. Pacific.
Add new comment